Stiffened panels welded by FSW
The use of stiffened panels has been widely developed in the industry. These aluminium panels consist of a sheet, the so-called skin, and stiffeners. These stiffeners have the advantage of considerably increasing the bending or buckling stiffness of these aluminium sheets. Due to the mechanical characteristics of these panels, riveting or MIG welding were for a long time the only processes available to the industry for assembling these parts. Today, FSW welding of stiffened panels is becoming increasingly popular in high-tech industries. Friction stir welding technology allows the production of lighter and stronger stiffened panels.

Definition & technical special features of stiffened panels
Definition & technical special features of stiffened panels
A stiffened panel is an aluminium part made up of 2 parts :
These stiffeners consist in longitudinal members integral with the skin over their entire length. There are 2 types of stiffeners:
Special features of stiffened panels
Stiffened panels have special technical characteristics that make them difficult to weld with conventional welding techniques.
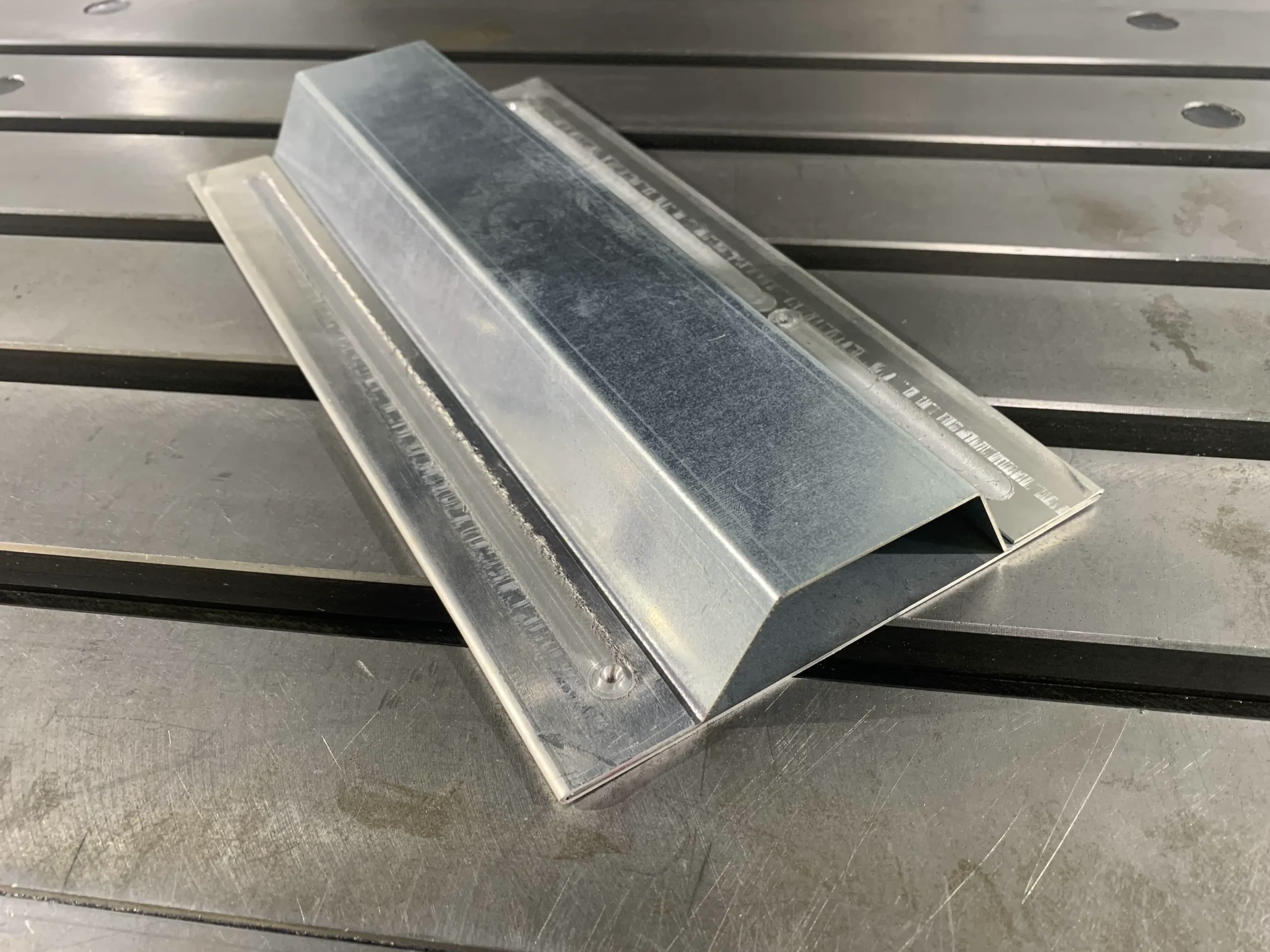
High-strength aluminium stiffened panels
Stiffened panels are made from aluminium alloys. In the aerospace industry, parts are mainly made of aluminium 2000 or 7000. The 2000 series is characterised by high strength and heat resistance. The 7000 family of aluminium is valued for its high mechanical strength. These alloys have excellent technical characteristics, however theyare susceptible to corrosion. These grades are also known to be difficult to weld, except by FSW.
In shipbuilding, stiffened panels are made from aluminium 5000, which is known for its good deformability and corrosion resistance.
Longitudinal stiffened panels
Stiffened panels are very long metal parts of up to 12 metres in length. The size of the part is an important consideration in the choice of joining technique. In addition, during the welding process, local clamping is required to hold these large panels. Special clamping systems are used to hold the parts during the joining process.


Longitudinal stiffened panels : decks for fast ferries – Marine Aluminium Norway
Geometry of stiffened panels
Stiffened aluminium panels have a particular geometry (T-shaped, rectangular, triangular, omega). This geometric feature makes them difficult to weld with traditional processes.
In addition, the stiffeners are made using a manufacturing process called “extrusion”. This mechanical manufacturing process consists in compressing a material into a given shape under pressure. The resulting parts can vary in geometry, thickness and flatness. It is therefore essential to perform the welding operation with the FSW head by force control and not by position control.
Examples of stiffened panel applications in industrial sectors
Stiffened panels are commonly used in several industrial and civil sectors: aerospace, civil engineering, automotive, aeronautical and marine. Indeed, the stiffener offers several advantages for advanced industries. Their main advantage is to significantly increase the bending or buckling stiffness of the panel while ensuring a minimum volume of additional material. Stirweld works with customers in the aerospace and naval fields to manufacture these stiffened structures.
Stiffened panels for aerospace
Aerospace is a sector where stiffened panels have many applications. These stiffened panels are used to replace long flat structures. By FSW welding these stiffened panels, it becomes possible to improve the specific performance of the part. Friction stir welding avoids the need for drilling during riveting and the inherent reduction in strength (especially in fatigue due to the stress concentration created by the rivet hole).
Self-stiffened panels are found in aircraft and aeroplane floors. The Eclipse 500, classified as a light jet aircraft, was equipped with aluminium stiffened panels.
The stiffened panels are also used in the manufacture of aluminium tanks. These smaller, lighter structures replace large tanks, freeing up space and reducing the weight of the equipment.


Manufacturing of low cost aircraft panels by FSW of T profiles and bending
As part of the energy transition, the use of aluminium panels is becoming standard in European shipbuilding. Aluminium has the advantage of being a light, non-corrosive and recyclable metal. The welding of stiffened panels by FSW is thus developing in the maritime sector.
Stiffened panels are used in particular in the design of bridges for a longer durability.

400 000m of weld without welding defect for European ship building
Conventional joining processes for stiffened panels: mechanical joints
The skin and stiffener, which make up the stiffened panel, are mostly joined by mechanical joining processes. The most common joining techniques are riveting or screwing.
Metal bonding is a recent and growing joining process. Bonding is used in particular in the aeronautical industry. However, this technique provides less strength than other existing mechanical processes. Moreover, aluminium bonding requires extreme cleanliness of the surfaces to be bonded, which necessitates polluting and expensive chemical etching.
Finally, it is very difficult to weld stiffened panels using conventional arc welding processes such as TIG or MIG: presence of porosity or sticking in the weld, hot cracking of certain non-weldable aluminium alloys (6000, 2000 and 7000). Indeed, the aluminium alloys used (6000, 2000 and 7000) and the geometry of the parts require a more advanced welding technique such as FSW. Why is this so? Because with FSW, we do not reach the melting point so there is no risk of porosity, sticking or hot cracking.
Riveting of stiffened panels
Riveting is a process for joining two or more parts together permanently. The parts to be joined are drilled in order to place the rivet. Developed at the same time as the intensive use of steel, riveting is the best known and most renowned method of permanent joining. The main advantages of riveting are the durability of the fastener and its precision. Unlike screwing, riveting has the advantage that no thread need to be introduced.
However, vibration and fatigue cycling of the structures on which the stiffened panels are installed can lead to cracking in the rivet hole. Regular inspection of the rivets is therefore necessary to ensure the long-term reliability of the structure. The drilling of the components to be joined also makes the part susceptible to corrosion.
Screwing together stiffened panels
Screwing consists of joining two or more parts by compression using a fixing screw.
As with riveting, drilling for rigid panel assembly results in weakness in the final structure. Indeed, this fastening technique involves drilling which makes the assembled part vulnerable to corrosion and cyclic fatigue.
FSW advantages for the assembly of stiffened panels
FSW process: definition
FSW refers to the friction stir welding process invented by The Welding Institute in 1991. This technique consists in assembling, in a solid state, two or more parts by bringing them to a pasty state using a rotating pin.
This breakthrough technology has made it possible to weld aluminium alloys that were considered un-weldable. Friction Stir Welding also facilitates the welding of parts that are dissimilar in material, geometry or thickness.
Friction Stir Welding for joining stiffened panels
The two main configurations for friction stir welding are lap welding and butt welding.
In the context of joining the skin and stiffeners for a rigid panel, lap welding is most frequently used. To make a lap weld, the parts to be joined are placed on top of each other.
Butt welding can more occasionally be used depending on the geometry of the stiffened panel. For example, this welding configuration is used to join several stiffened panels together, one next to the other.
Regardless of the welding configuration adopted, Stirweld standard tools provide a high strength weld for rigid panels. You can find our FSW tools in our tools catalogue.

Local clamping jig for defect-free FSWed stiffened panels
Advantages of Friction Stir Welding of stiffened panels
FSW offers several advantages for the manufacture of stiffened panels. This breakthrough technology has many applications in the industry. The main advantages of FSW welding of stiffened panels are durability, mechanical resistance, economy and environmental friendliness.
Friction stir welding is a permanent and irreversible joining method. It has the additional advantage that no drilling or fitting of external elements is required. This assembly technique therefore allows the non-corrosive appearance of the aluminium panel to be maintained. Once welded and installed, the stiffened panel does not need to be inspected afterwards to ensure that the fasteners are secure.
In addition, FSW welding of the skin and stiffeners can be carried out much faster than mechanical joining methods. The time saved is even more noticeable on very large panels.
The time saving is due to the fact that FSW does not require any preparation and degreasing of the parts before welding. It is also not necessary to rework the parts after welding. All these advantages make FSW an environmentally friendly process.
The use of friction stir welding also saves money in terms of purchase and production. Indeed, Stirweld FSW welding head can be installed on existing CNC machine, which represents a much lower investment cost than a special machine.
In terms of mechanical strength, friction stir welding results in stiffened, sealed and high strength panels. This innovative welding technique preserves the mechanical properties of the welded metals. Indeed, during an FSW operation, the melting point of the materials is not reached.
FSW also makes it possible to produce wider and thinner stiffened panels. The width of an extrusion profile is usually limited to 300 mm, the maximum width of an extrusion die. Friction stir welding makes it possible to overcome this limit by joining several aluminium parts together. In addition, profile optimisation coupled with FSW limits unnecessary shapes and thus ensures lighter and stronger panels.
Qualifitacion of FSW welding of stiffened panels
In order to ensure the strength of the FSW weld, quality controls are carried out on representative coupons for each project. This involves making a 600 mm long weld on a simplified prototype part. This sample is representative in terms of aluminium grades and thickness compared to the final rigid panel.
These tests are necessary to define the 4 FSW welding parameters: FSW tool, feed rate, rotation speed and forging force.
Quality controls are then carried out to examine the quality of the FSW weld in accordance with the FSW standard ISO 25239, which requires two macrographic cross sections and two bending tests. The macrographic examination of the welded joint ensures that the panel is free of porosity. The bending test consists in twisting the weld to check its strength. These tests are carried out twice along the weld seam to ensure its quality along its entire length.

In parallel to these welding tests, Stirweld can carry out a prototyping study for the assembly of the stiffened panels. This study phase allows us to support the client in the integration of the FSW into its industrial process. The Stirweld team then remains in support during the industrialization phase at the customer site.
The assembly of stiffened panels requires a process that must combine strength and the ability to join large sheets while ensuring the strength and lightness of the structures.
FSW is a mature assembly technology that has already been democratised in the automotive (battery tray), railway (car side panels), aeronautical and naval (floor) industries. This friction welding technique is now a relevant solution for the manufacture of stiffened panels. Stirweld has worked with customers such as Ariane for the FSW welding of stiffened panels for the Ariane 6 rocket launchers.
Want to know more?
Contact our team of experts in FSW technology.