FSW APPLICATION
Aluminium Tank Welded by FSW
Elevating Aluminum Tank Manufacturing: Achieving Efficiency and Strength through FSW.
Why Choose Friction Stir Welding for Your Aluminium Tank Assembly?
Aluminum tanks, used in various applications such as liquid hydrogen storage for airplanes, cryogenic hydrogen storage and space launchers, greatly benefit from FSW technique. This method effectively preserves the inherent mechanical properties of the material. Additionally, it ensures complete hermetic sealing of the tanks, thereby significantly extending their lifespan.

100% leak proof
No risk of leak (from vacuum to any liquid). Solid state process > No porosity
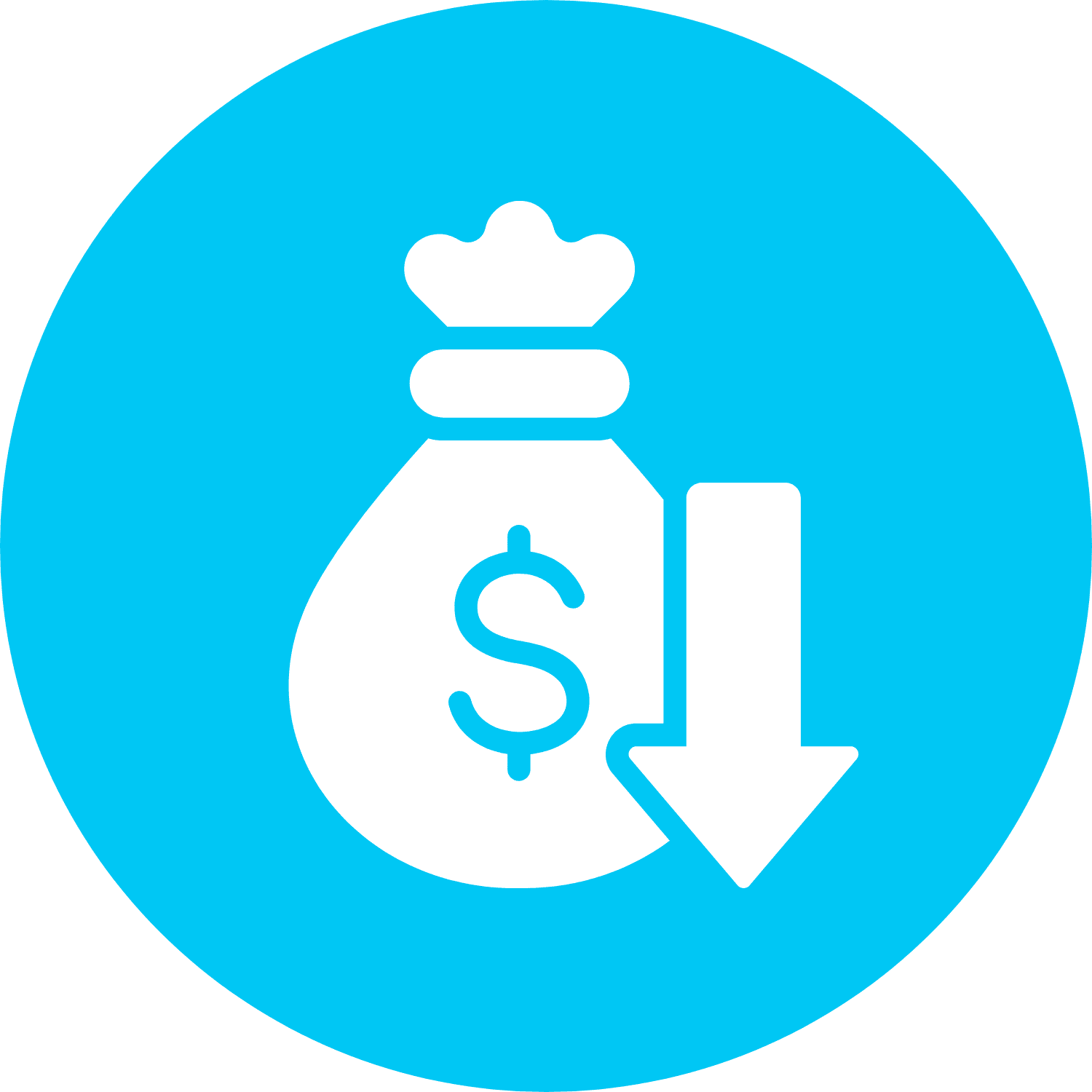
Cost divided by 2
Up to 2 times less expensive than arc or laser welding.

High resistance
Up to 280 bar (4000 psi) without post heat treatment.

Weight reduction up to 2
Replaced stainless steel by high strength aluminium (2000 or 7000).
Technical Specifications of FSW-Welded Tanks
Tanks under Ø 300 mm
The manufacturing of 300-mm tanks is revolutionized by incorporating extrusion and Friction Stir Welding, which offer unparalleled versatility as the extrusions can be seamlessly integrated with any aluminum alloy, thus facilitating the assembly process. The extrusion method streamlines the entire manufacturing workflow by eliminating the necessity for longitudinal welding, thereby simplifying the complexity of the production process. Moreover, the adoption of aluminum extrusions is not only a strategic move for improving efficiency but also serves as a cost-effective measure, significantly reducing the overall manufacturing expenses.
Tanks exceeding Ø 300 mm
A tank with a diameter exceeding 300mm typically consists of multiple components: the body (half-collet) and two end caps.
Consequently, assembling this type of aluminum tank requires four FSW welds:


Friction Stir Welding is a sophisticated welding technique renowned for meticulously preserving the mechanical properties of aluminum, exhibiting a joint efficiency coefficient ranging between 70 and 100%. Furthermore, FSW assures minimized post-weld defect rates, immaculate repeatability and the capability to adeptly weld high-performance aluminum alloys, inclusive of AA2024-T3 and AA2219-T8. Once subjected to this superior welding process, a cryogenic hydrogen tank not only attains 100% waterproof integrity but also meets the stringent quality demands requisite for such applications.
Furthermore, the application of Friction Stir Welding plays a pivotal role in advancing towards zero-emission aviation by enabling the secure and efficient storage of liquid hydrogen. This approach not only ensures the structural integrity required to withstand the extreme conditions associated with low-temperature hydrogen storage but also aligns with the aerospace industry’s goals for sustainable and environmentally friendly fuel alternatives.
Friction Stir Welding is deployed for circumferential welding of launch vehicle panels as well as dome butt-welding, effectively halving the associated process costs. This technique facilitates the welding of high-performance aluminum alloys in the 2xxx and 7xxx series. These alloys, integral to the fabrication of space launchers, were either non-weldable or posed considerable welding challenges in the past.
Moreover, FSW contributes to the reduction of space launcher weight by enabling the welding of lighter, stiffened panels. These panels can accommodate weldable stiffeners of diverse shapes—including cross, triangular, axial and circumferential configurations. Stiffeners, which can be crafted through machining or extrusion processes, offer additional versatility and options in launcher construction.
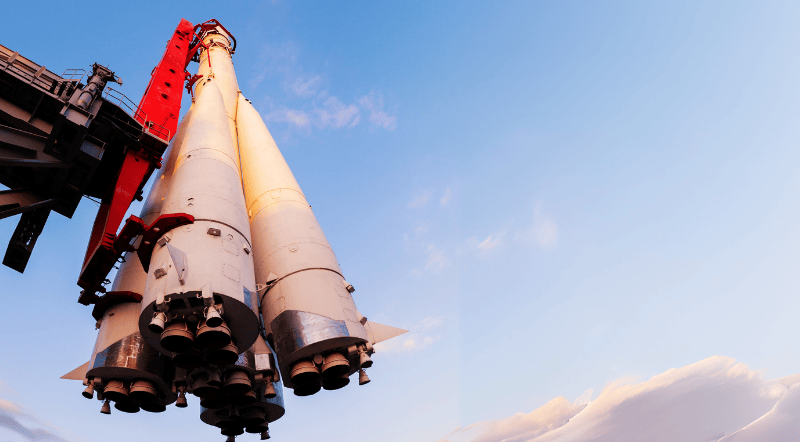

The utilization of Friction Stir Welding in the assembly of liquid oxygen tanks brings forth a multitude of advantages tailored to meet the unique demands of this specific application:
See Friction Stir Welding Applied to Aluminium Tanks in Real-Time
Zoom on Friction Stir Welding with Retractable Pin: the Solution to Fill the Exit Hole
A common issue in the space and aeronautics sectors, the exit hole resulting from FSW, can be effectively filled with a retractable pin system. The accompanying image illustrates a circumferential FSW weld on a 100mm diameter aluminium tank made of 2024-T3 grade aluminum with a thickness of 2.4 mm. Notably, the exit hole at the weld’s end is seamlessly filled, applying the retractable pin technique.
For additional insights on the retractable pin principle, explore our Friction Stir Welding Head equipped with a Retractable Pin feature.

Aluminium Tanks: Key Concerns for Critical Sectors
Aluminum emerges as the top choice in mobility sectors for tank construction due to its lightweight nature, corrosion resistance and ideal balance of strength and flexibility. Exceptional thermal conductivity plays a pivotal role in the management of extreme cryogenic temperatures. Customization drives innovative tank designs while aligning with budget constraints, making aluminum a cost-effective solution.
In critical sectors where precision and performance are paramount, the combination of aluminum and FSW offers unmatched advantages for mission success.
They Trust Us





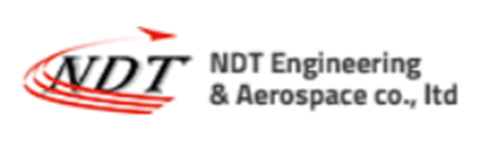
Dive Deeper: Comprehensive FSW Tanks Resources
Curious to delve deeper into the world of FSW-welded aluminum tanks? Explore a wealth of knowledge through our webinars, articles and whitepapers. Click below to access a treasure trove of resources designed to expand your understanding and expertise.
Conference – 25 min
Friction Stir Welding: a cost-killer in the aeronautics industry
Discover a conference replay that delves into the transformative impact of FSW on various sectors, including tank manufacturing, hydrogen storage, space launchers, riveting alternatives, material efficiency and busbar applications.
Blog articles – 5 min
Hydrogen cryogenic tank: a forward-looking concept for aeronautics
Friction Stir Welding: a revolution in aluminium welding
White paper – 20 min
Friction Stir Welding: principles & trends
Delve into the intricacies of FSW through our white paper. Gain insights into its operational advantages, unique product attributes, economic merits and the latest market insights.
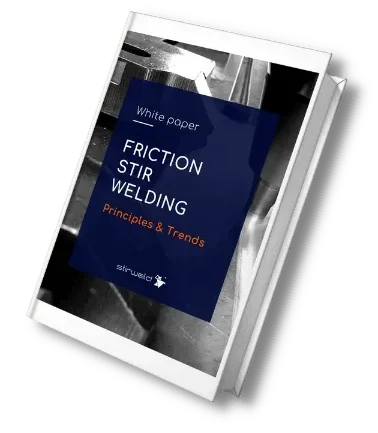
White paper – 20 min
Friction Stir Welding: applications
Uncover your comprehensive FSW application guide. In this white paper, we explore a variety of applications where friction stir welding offers numerous benefits, including aluminium tanks.
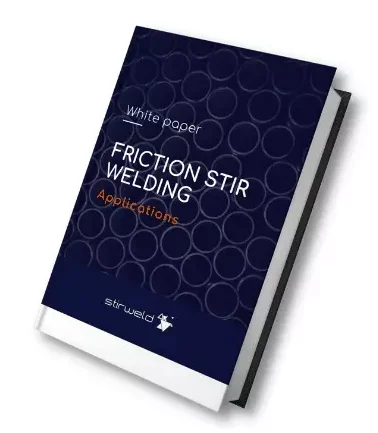
Ready to Elevate Your Tank Solution?
Discover how FSW transforms tank construction. Contact us to discuss your specific needs and explore the advantages of FSW technology. Your journey to enhanced tank solutions starts now.