STIRWELD FSW SERVICE
Friction Stir Welding Clamping System
Design of your Friction Stir Welding clamping system by our experts.

Why choose Stirweld for your FSW clamping system?

FSW Expertise
Leverage our deep-rooted experience and specialized expertise in Friction Stir Welding to customize your clamping tools for the perfect fit with your components.

Superior Quality
Elevate the standard of your welding processes and the components produced by using our meticulously crafted clamping tools, created exclusively for optimal FSW performance.
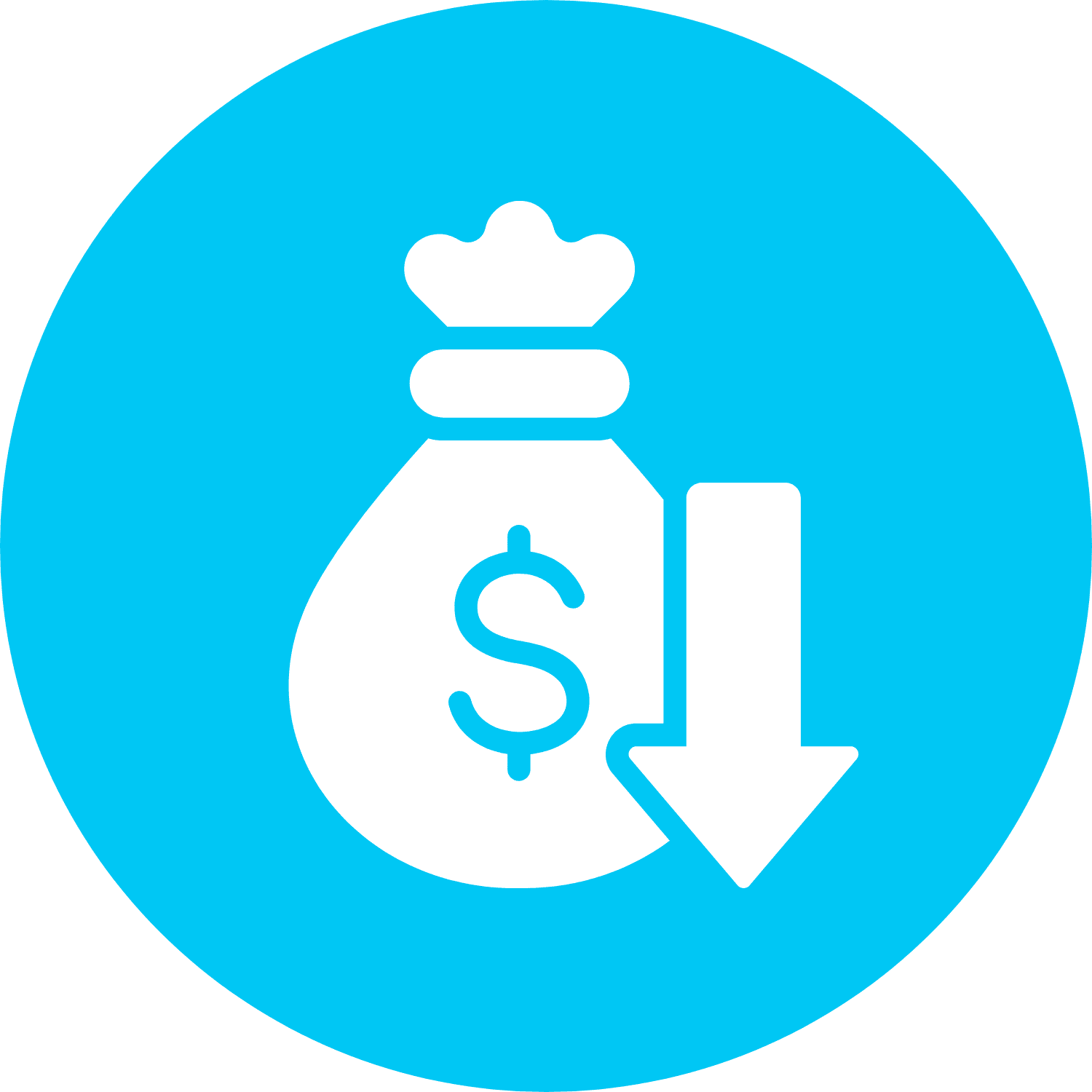
Cost Reduction
Lower your production expenses with our efficient and bespoke tooling solutions, designed to reduce the incidence of quality-related costs.
Unlocking Friction Stir Welding: Key Features of Stirweld FSW Clamping System
Stirweld’s clamping systems are designed to adapt to every stage of your FSW project, providing the right solution for prototyping, serial production and complex welding requirements. Each type of clamping jig is engineered to meet specific needs, ensuring optimal performance, cost-effectiveness and precision for different production phases.



Stirweld Clamping Systems: Industry-Specific Examples
At Stirweld, we have implemented clamping solutions across a diverse range of industries. Below, we present a selection of our most notable examples, each designed to meet the specific needs of applications such as small and large foundry parts, tanks, mounting brackets and large-scale tooling systems.
While these examples highlight our capabilities, the majority of our work is confidential. To protect the proprietary processes and designs of our clients, we are only able to show a limited number of examples. These cases, however, reflect the precision and innovation of Stirweld’s custom FSW clamping systems.
Application: Tanks
Application: Cast parts
Application: Bus bars

This lightweight, manually operated clamping system is designed specifically for demonstration purposes, showcasing the welding of bimetallic materials (copper and aluminum) in bus bar applications. It enables overlap welding of an aluminum bar onto a copper bar, along with additional welds for a copper rod on an aluminum bar and an aluminum rod on a copper bar.
Application: Large-Scale Tailor Welded Blanks
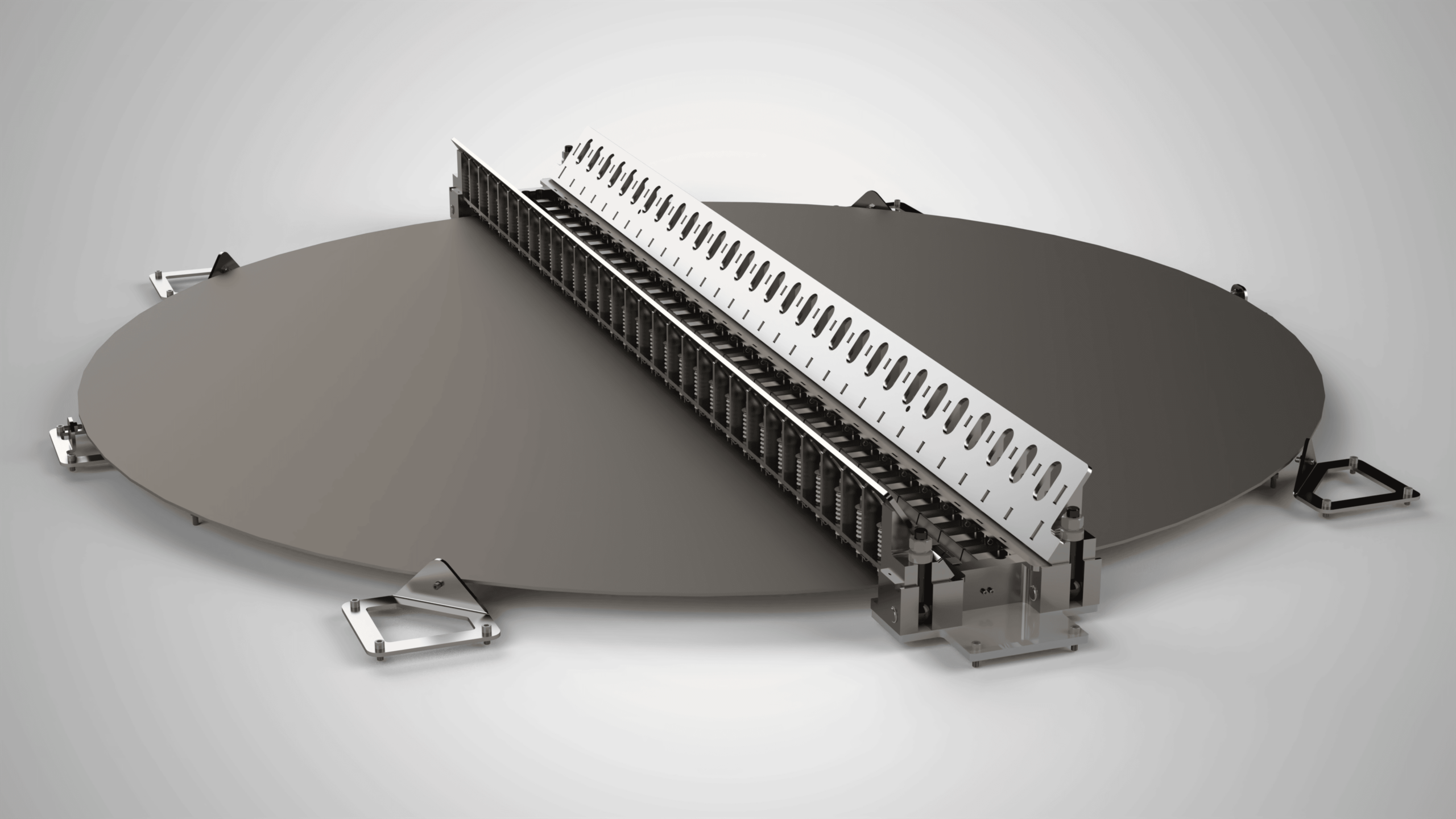
For the assembly of two half-discs, each with a radius of 1.5 meters, this complex clamping system is engineered to deliver precision in butt welding across the full thickness of the laser-cut parts. The fixture is assembled directly on the machine table, ensuring stability and alignment throughout the welding process.
Application: Stiffened Panels
Application: Mounting Brackets
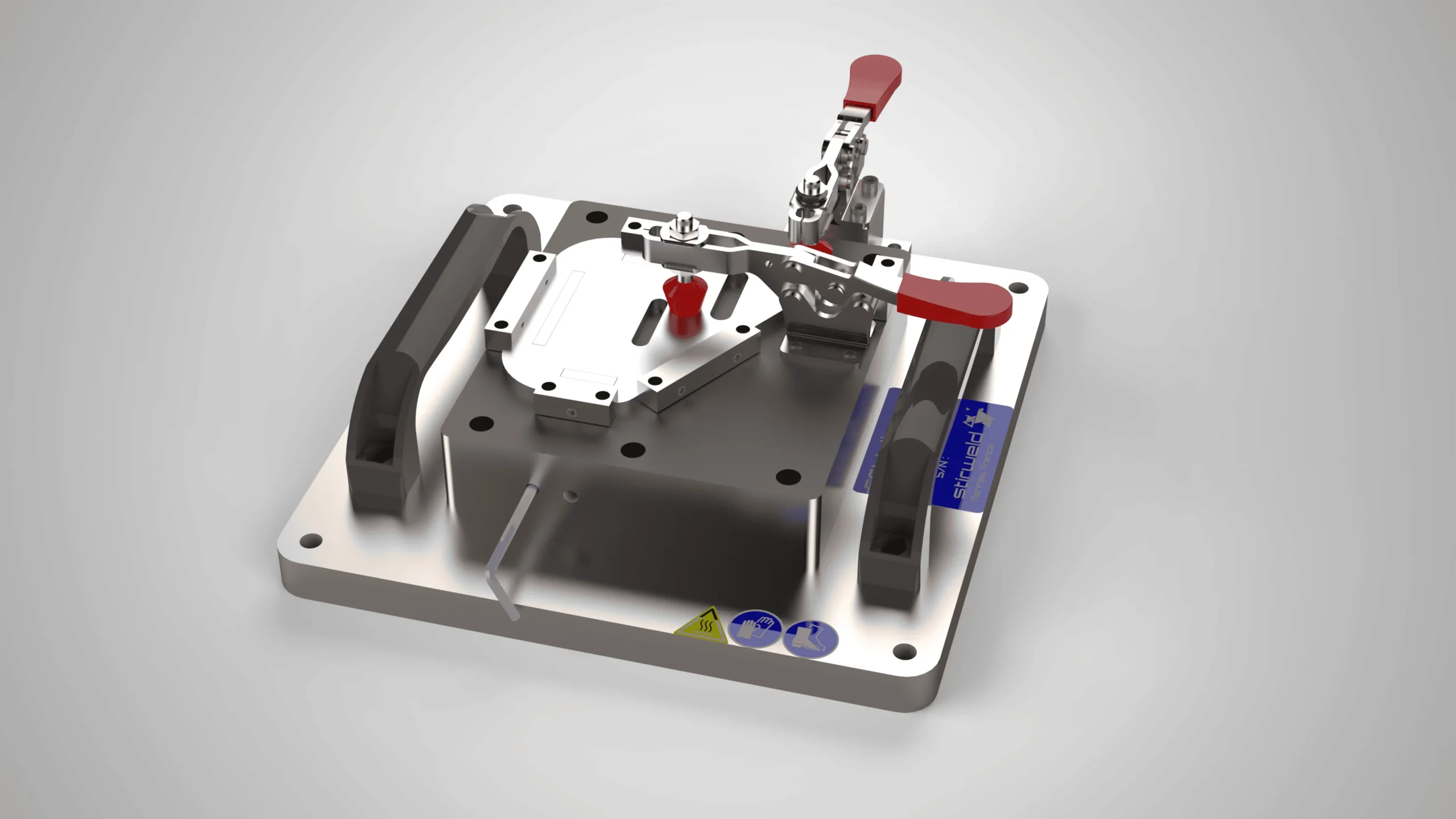
This clamping system is used for the assembly of two laser-cut sheet metal parts: one flat and the other bent at a 90° angle. The process involves butt welding along the full thickness of the flat part, using a tenon mortaise joint to ensure a secure and precise fit.
Application: Cold plates
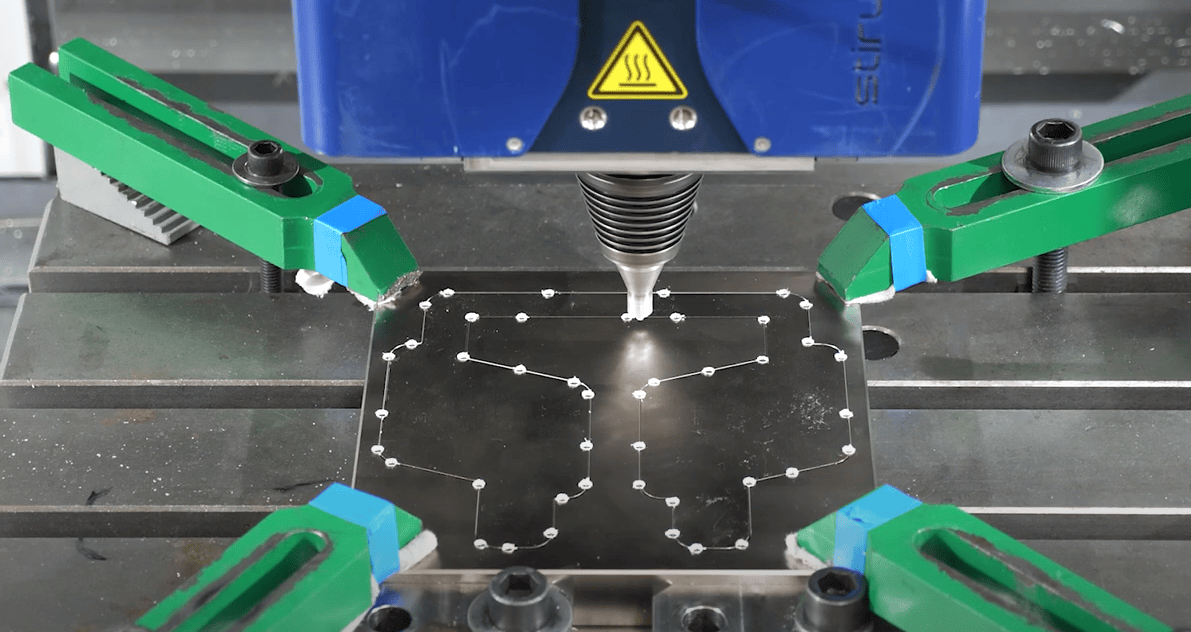
Liquid cold plates generally have a simple shape, where the body is milled and the cover can be laser-cut, allowing standard milling clamping elements to securely hold the part on the CNC table. Depending on the size of the production series, the cover can either be vertically clamped onto the body or tack-welded prior to the continuous weld. However, if the tack welding operation extends the cycle time too much, a dedicated automatic jig may need to be designed to improve efficiency.
Automated Clamping System
At Stirweld, we excel in designing and producing complex, automated clamping systems tailored to meet a variety of mechanical constraints. With an experienced team of automation specialists, we develop advanced tooling solutions that optimize efficiency, precision and adaptability in FSW applications. Our expertise covers a wide range of clamping configurations, from semi-automatic systems to fully automated solutions, each engineered to enhance production speed, repeatability and welding quality.
Each clamping system is customized to the specific requirements of each project, ensuring dependable performance and optimized processes across diverse production environments.
The Clamping System Development Process by Stirweld
At Stirweld, we follow a structured process to design and deliver custom clamping systems that meet the specific needs of Friction Stir Welding applications. Throughout each stage, we maintain full transparency with our clients, providing clear communication on technical details and project timelines. Our approach ensures a seamless transition from the initial concept to the final product, guaranteeing high quality and precision at every step.
Kick-off
We begin with a kick-off meeting to establish the project schedule, welding requirements, automation goals and mechanical specifications.
Detailed 3D Then 2D
We finalize detailed 3D models followed by 2D drawings, incorporating feedback for internal and customer validation.
Assembly
The clamping system is mounted and tested. We perform clamping checks, quality inspections and prepare the system for release.
Preliminary 3D Project
Our team creates initial mechanical concepts, automation designs and functional specifications.
Manufacturing and Supply
We execute the manufacturing processes, ensuring the quality and precision of each component.
Delivery
Finally, the clamping system is delivered to your facilities, ready for integration into your production line.
They Trust Us



Customize Your Perfect Clamping Solution
Ensure the precision and efficiency of your welding operations with a Stirweld-designed Friction Stir Welding clamping system. Get in touch to start customizing a solution tailored to your needs.