
WHERE FSW TECHNOLOGY MAKES A DIFFERENCE
Friction Stir Welding in Aerospace
FSW technology transforms aerospace with stronger, lighter and more reliable components.
Unlocking Aerospace Potential with Advanced FSW Techniques
The aerospace sector faces a myriad of challenges and stakes, owing to the inherent complexity involved in the designing, manufacturing and operating of aircraft and rockets. Friction Stir Welding (FSW) provides a set of unique advantages, making it an invaluable technique for aerospace applications. By meeting the industry’s strict demands for durable, lightweight and reliable components, FSW is setting new standards in aerospace manufacturing excellence.
Exploring FSW Applications in the Aerospace Sector
The ability of FSW to deliver strong and uniform joints in materials that are challenging to weld using other methods makes it an appealing technology for a wide array of aerospace applications:

Stiffened panels
Stiffened Panels provide crucial structural support in aerospace, enhancing rigidity while maintaining a lightweight profile for optimal aircraft performance.
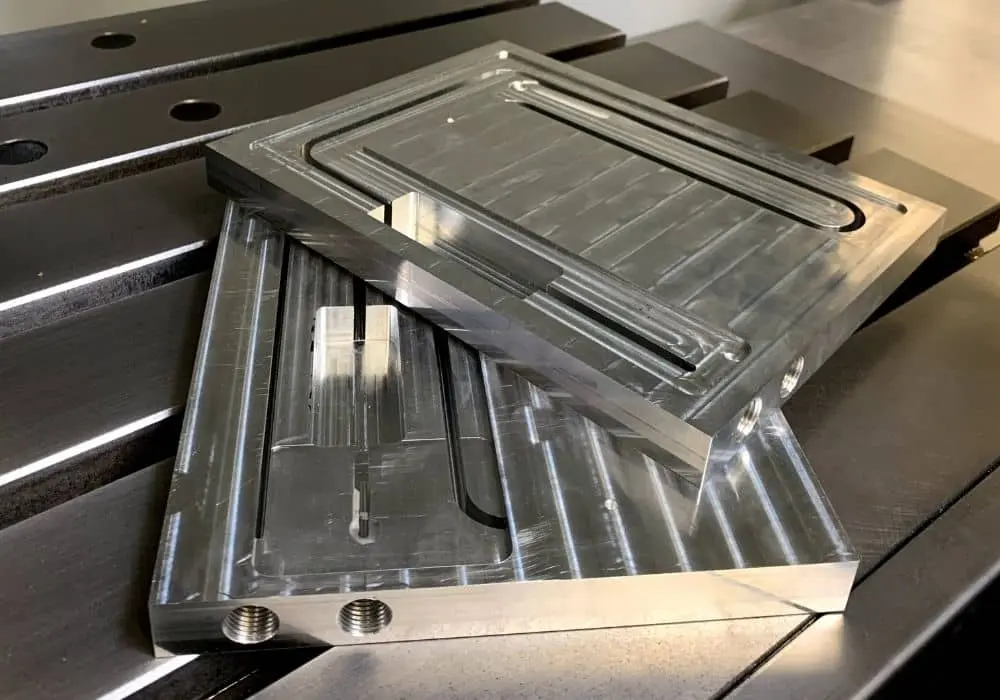
Cold plates
Cold plates are essential for thermal management of aerospace electronics, ensuring optimal functionality and longevity of high-performance systems.

Tanks
Aerospace tanks are vital for storing fuels and other fluids securely, requiring welding solutions that guarantee a leak-proof and durable structure.
Recommended FSW Equipment for Aerospace Applications
Our FSW equipment delivers numerous benefits in terms of quality, efficiency, cost and environmental impact, meeting the stringent requirements of the aerospace sector.
Discover the equipment pieces our experts highly recommend for your needs:

Standard FSW head for CNC
Designed for universal compatibility, the FSW Standard Head effortlessly integrates with existing 3, 4, or 5-axis machines, instantly offering precise force control, real-time force monitoring, effective tool cooling and optimal protection against mechanical stress and vibrations for high-quality FSW welding.

FSW head for CNC with retractable pin
Featuring the advanced functions of our FSW Standard Head, the FSW Head with Retractable Pin stands out with its retractable pin feature, eliminating exit holes, a significant advantage in aerospace applications. Its user-friendly interface ensures perfect control and impeccable quality for each weld.
They Trust Us






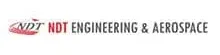

“Two essential reasons led us to choose Friction Stir Welding. First, it provides an excellent opportunity to secure the assembly operations between the sole and the cover, which together make up the heat sink. Second, we were looking for a technology that is not only simpler but also more reliable. FSW not only simplifies the industrial process, it’s also safer and can lead to significant cost reductions.”

X.A.
Supplier Development
Dive Deeper: Comprehensive FSW Aerospace Applications Resources
Looking to explore further into FSW Aerospace Applications? From insightful webinars and articles to in-depth whitepapers, we have a variety of resources available. Click below to access a wealth of information we’ve prepared for your convenience.
Conference – 25 min
Friction Stir Welding: a cost-killer in the aeronautics industry
Explore a conference replay where we delve into how FSW revolutionizes tank manufacturing, hydrogen storage, space launchers, riveting replacement, raw materials reduction, and busbar applications.
Blog articles – 5 min
Hydrogen cryogenic tank: a forward-looking concept for aeronautics
FSW machine: choose the best option
White paper – 20 min
Overcoming cold plate manufacturing challenges
Unveil the capabilities of FSW in crafting liquid cold plates through our insightful white paper. Efficiently turn manufacturing challenges into opportunities by addressing critical issues with this resource.

White paper – 20 min
Aluminium stiffened panels welded by FSW
Explore the unmatched ease of assembling stiffened aluminium panels with FSW in our concise white paper. Transform assembly challenges with techniques ensuring durability and resistance.

Got FSW Questions or Projects?
Wheter you have a part to weld, a project underway, or simply questions about Friction Stir Welding, we are here to assist you. Don’t hesitate to reach out!