Friction Stir Welding: butt & lap comparison
Friction Stir Welding can be performed in two ways: butt and lap welding. In this article we review these types of FSW welds, digging in depth the differences between both of them. Keep reading and put all your doubts to rest!

First of all, do you know what butt and lap welding are? If not, don’t worry, and follow the guide !
Butt welding
To carry out the butt welding, we place the pieces to be welded alongside each other.
Within the butt-welding category, there are 3 ways to place the pieces to be welded during the FSW process: square butt joint, edge butt joint, and T-butt joint.

Square butt joint

Edge butt joint

T butt joint
In the following cross section, we can see how the butt weld is produced internally, in a 2-mm thick weld:

Cross sections of a butt FSW weld
A good example of an application where a butt weld is performed is in the manufacture of heat sinks:


FSW-welded water heat sink for e-mobility
For example, in this water heat sink for e-mobility, a cover is placed over the housing through which cold water circulates. It is welded to the heat sink using FSW, specifically butt welding.
Another example of butt welding can be seen in these two welded rheocasted parts (FSW of more complex components previously not castable):
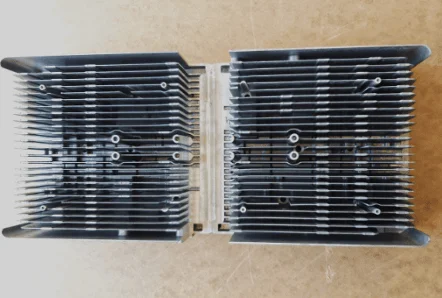

FSW of two rheocasted parts
Lap welding
Alternatively, to carry out lap welding, the parts are placed one over the other.
Again, there are three positions that can be adopted to carry out lap welding through Friction Stir Welding: lap joint, multiple lap joint & T-lap joint.

Lap joint

Multiple lap joint

T lap joint
This type of welding, internally, looks like this (welding thickness of 5 mm):

Cross sections of a lap FSW weld
The lap weld is used, for example, to replace riveting, to carry out the welding of copper brackets or even with the replacement of copper with aluminium:

Replacement riveting by FSW welding for the mixed application 2024-T3 and 7075-T6.

FSW copper welding on aluminum.
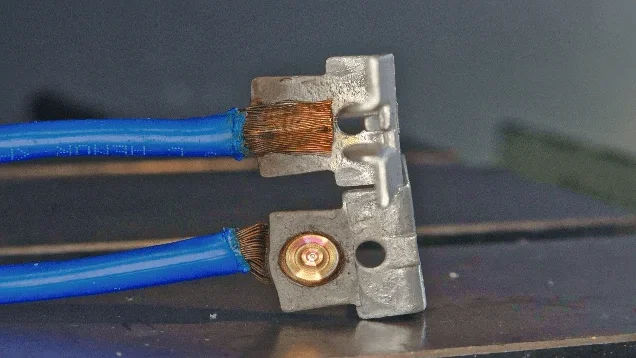
FSW spot welding of a tinned copper connector on a copper cable.
Butt and lap welding
In addition, it is possible to use both types of welding in the same application, as it is the case of rigid panel manufacturing.

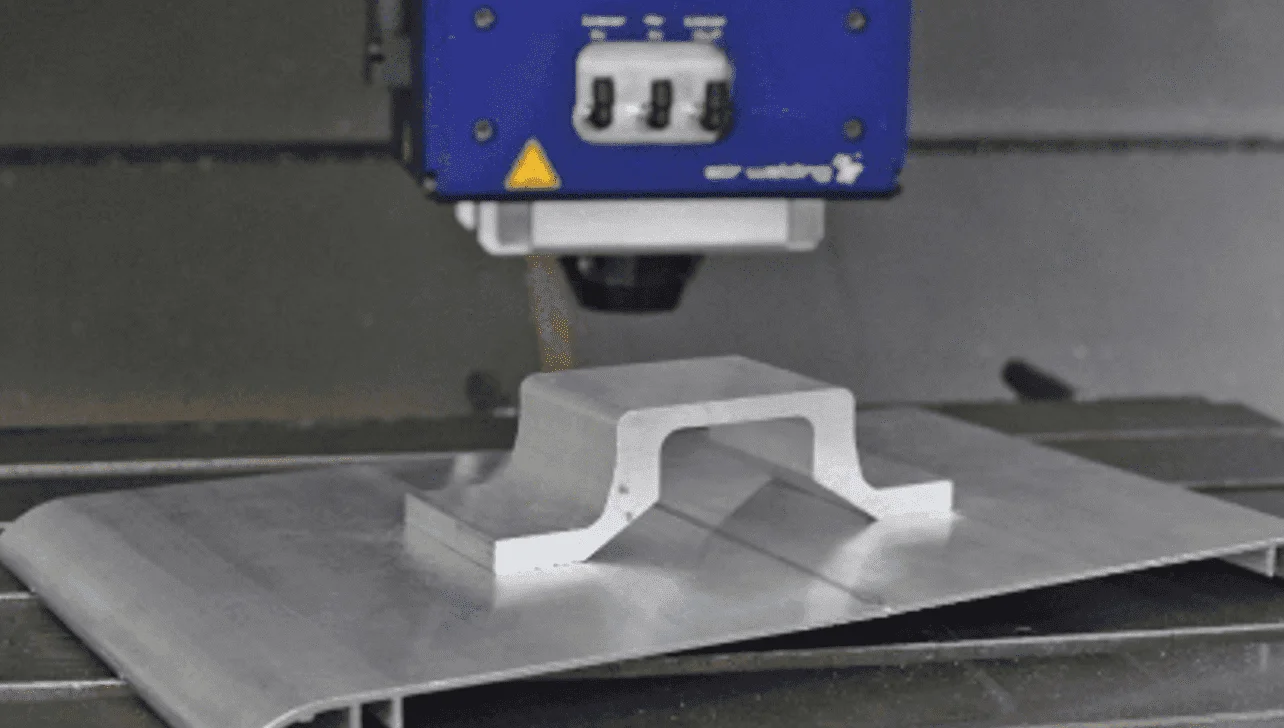
The decision to select either butt or lap as the type of welding to be performed depends on the application for which the Friction Stir Welding is meant. However, the choice of the welding type has an impact on 5 points:
It is important to be aware of these differences in order to select, in the most efficient way, our type of welding. Therefore, we explain each of them step by step below.
Commun FSW defects to butt and lap welding
When the process of Friction Stir Welding is carried out, defects can occur. Special attention must be paid to avoid them in order to achieve a high quality of the weld. Some of them can occur independently of the position of the parts when welding, that is, they can occur regardless of whether it is butt or lap welding.
For example, types of defects that can appear regardless of whether it is a butt or lap weld are flash and wormhole (both of which can be seen with the naked eye):

Flash

Wormhole
However, there are other types of FSW defects that are specifically associated with butt or lap welding.
Frequent FSW defects in butt welding
In the case of a butt weld, we must be very aware of whether the lack of penetration occurs.
This defect arises when the FSW tool does not go completely through the parts, leaving a part of them unwelded. This defect cannot be seen with the naked eye, as it is an internal defect.
When we look at the defect internally, we can see that the parts not been welded, however simply stuck together. In the following images, we can see the line that separates both parts and shows that they are not welded (since the parts have not been removed creating a single piece):

Lack of penetration

However, we should not be overly concerned about this defect since it is easily avoidable. Therefore, carrying out butt welding is easier to do than lap welding if we focus on this point.
Frequent FSW defects in lap welding
When talking about the defects that can occur when performing a lap weld, we must consider hooking and kissing-bond:
On one hand, kissing bond occurs when the interface between the two joining metals is insufficiently heated and stirred, which results in a remnant oxide layer. At the interface, there could be little or no bond, raising the local stress in the weld during mechanical solicitation. In the case of lap welding, the oxide disruption at the sheet interface is more difficult than for butt welding due to the orientation of the joint interface with respect to the FSW tool.
On the other hand, hooking defect is formed when the interface between the two joining sheets is stirred up into the top sheet, which effectively reduces the cross sectional area of the top sheet. The hooking defect occurs on the TMAZ of the AS (TMAZ = Thermal Mechanical Affected Zone). Moreover, the form and the vertical direction of the notch can reduce the mechanical properties by acting as crack initiation site during transverse loading. Lastly, top sheet thinning is observed on both sides. As the hooking defect, this thinning is due to the pulling up of the interface into the top sheet thereby reducing its cross section.

Hooking
In the following image, we can see how both defects have been produced in the same lap weld:

Unlike the lack of penetration, it is more difficult to prevent hooking and kissing-bond defects from occurring. For this, it is necessary to rely on experts who perform adequate welding parameters and use the correct FSW tool. But don’t worry, at Stirweld we can help you.
Friction Stir Welding resistance according to lap/butt weld
The previously announced defects have a massive impact on the mechanical resistance when performing Friction Stir Welding.
Hooking defect creates a crack initiation and therefore reduces the fatigue resistance. This defect does not produce a direct breakage of the welded piece but, with time, as the two parts are not completely welded but simply hooked together, both parts could end up separating:

Visualization of the hooking in cross section

Very bad defect by the forces applied to the upper plate in the direction we see above.
Moving on to talk specifically about kissing-bond defect, as it is a non-stirring zone, we reduce the weld section. That is, we reduce the mechanical resistance of the weld due to the fact that the weld is smaller.
These defects (hooking and kissing-bond) are those that directly affect the resistance of the weld, and both can be found in lap welding. Therefore, lap welds generally have a lower resistance than butt welds.

FSW welding speed
As mentioned before, hooking and kissing-bond are due to poor stirring phenomenon. Therefore, to prevent these defects from occurring, we must increase the effect of stirring, which is achieved by reducing the FSW welding speed.
Thus, when comparing butt and lap welds, we must take into account that the lap weld (being the one that has the possibility of creating hooking and kissing-bond) is the one that must be carried out at a lower speed. Specifically, lap welding is usually carried out at a speed of 2.5 meter per minute, while butt welding is performed at a speed of 3.0 meter per minute.

FSW surface preparation
During Friction Stir Welding, we do not feed any material into the weld. Then, FSW can’t support an important gap between the two components that are going to be welded. In the case of butt welding, the maximum allowed gap is 10% of the thickness (up to 10 millimeters). If the gap is higher than this percentage, a hole defect occurs into the weld. This is why before carrying out a butt weld, it is important to perform an accurate edge preparation. There are several ways in which this process can be executed: laser cutting, water cutting or machining. However, it cannot be carried out by shearing.
No edge preparation is required for FSW lap welding, as the parts to be welded are placed on top of each other. In addition, no further surface preparation is needed (no degreasing, no brushing).

Friction Stir Welding: clamping system
The same principle applies to the clamping system. Since it is not possible to have a gap of more than 10% of the thickness of the parts to be welded when performing a butt weld, it is of utmost importance to have a correct clamping system. This must be accurate enough to prevent a larger gap from occurring.
This process facilitated by Friction Stir Welding of the lap type. Why? The tool pushes one part over the other one with a force that limits the gap between the components.
In addition, when performing a butt weld, it is imperative that the tool follows the joint pass. The reason for this is that if the FSW tool is away from this joint line, we could have defects such as lack of penetration. It is therefore important that the clamping system ensures that the tool is in the correct position at all times while Friction Stir Welding is performed. However, when carrying out a FSW lap weld it is not necessary to follow any joint line, so the clamping system can be less accurate.
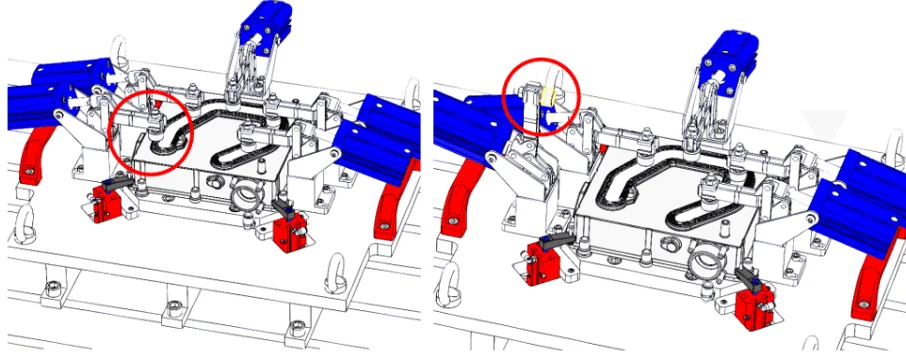
Automatic jig for a butt weld

FSW sealing quality
Finally, it should be noted that in both cases (butt and lap welding), we get waterproof and airtight welds. Thus, it is not possible to find differences between the two types of FSW welding as far as this characteristic is concerned.

Throughout this article we have delved nto the different types of FSW welding: butt and lap. Below you can see a summary infographic that will help you clarify all the information:

If you still have doubts about what type of FSW welding suits your application best, don’t worry: we can help you solve them! At Stirweld we count on a team of qualified professionals who will guide you through your first steps in Friction Stir Welding thanks to our design office.
Do not hesitate to contact us without any commitment
We are here to help you!