FSW APPLICATION
Stiffened Panels Welded by FSW
Enhanced technical characteristics of aluminium stiffened panels through Friction Stir Welding.
Why Choose Friction Stir Welding for Your Stiffened Panels Assembly?
Aluminium stiffened panels comprising a “skin” sheet and stiffeners, are widely utilized in industries like aeronautics, automotive, railways, naval and bridge construction. Formerly assembled primarily through riveting or MIG welding, these panels are increasingly being joined using FSW welding due to its superior technical benefits in the assembled components.

Longer Panels
With FSW, aluminium profiles, which must be less than 400 mm wide, can be butt welded to overcome this limitation.

Lighter & Enhanced Rigidity
Profile optimization with FSW eliminates unnecessary shapes, resulting in more rigid and lighter panels.

Permanent Joining
This irreversible method requires no drilling or addition of external elements, offering excellent corrosion resistance.
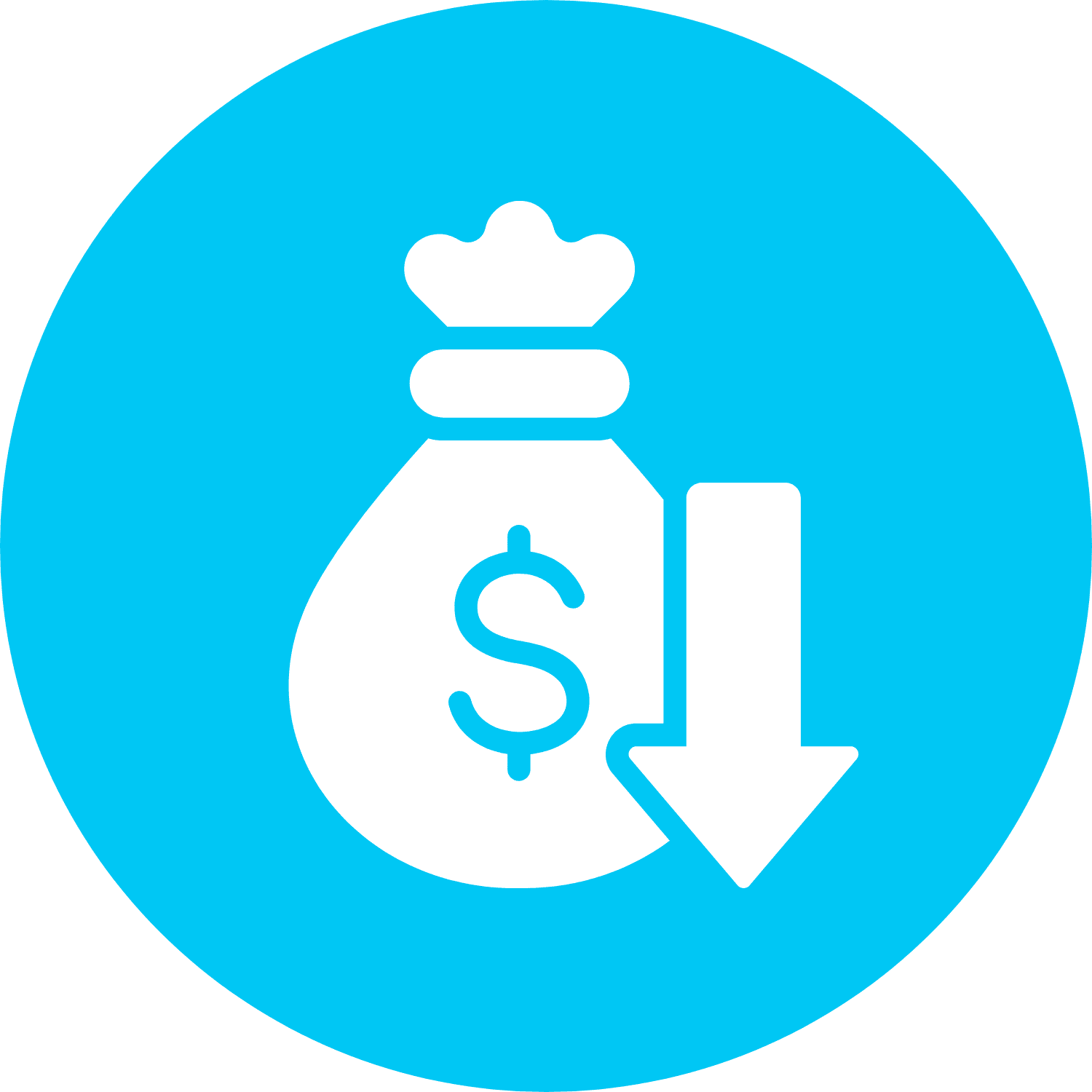
Cost-effective Production
When compared to riveting, MIG or laser welding, FSW offers a more economical solution.
Technical Specifications of FSW-Welded Stiffened Panels

Stiffened panels crafted from high-strength aluminium are essential in industrial sectors with stringent technical and mechanical demands, such as aeronautics and space. These sectors often require the use of 2000 or 7000 series aluminium alloys due to their superior mechanical properties and performance under demanding conditions, making them ideal for applications that require both strength and durability.
The length of stiffened panels can extend up to 12 metres, making the size of the part a crucial determinant in selecting the appropriate assembly technique. The substantial length necessitates a careful consideration of the assembly method to ensure optimal performance and integrity of the panels.
The length of stiffened panels can extend up to 12 metres, making the size of the part a crucial determinant in selecting the appropriate assembly technique. The substantial length necessitates a careful consideration of the assembly method to ensure optimal performance and integrity of the panels.
Stiffened panel geometry can vary, incorporating “T”, rectangular, triangular or omega stiffeners. Due to the complexity of these parts, the welding process demands meticulous force control to successfully execute the operation. This requirement ensures not only the precision in assembling the parts but also the integrity and performance of the resulting stiffened panels.


FSW tool: Choosing the right FSW tool is crucial for weld quality. Consider four key parameters for selection: weld length, weld depth, tool geometry and part material. These factors significantly influence the tool’s effectiveness and the resulting weld quality.
Design of the clamping jig: Secure clamping of stiffeners is vital when welding aluminium stiffened panels to avoid lifting or part separation. A specialized local clamping tool, used with global clamps, is necessary to track the weld seam, ensuring defect-free welds. Our expert team is available to assist in designing a clamping device suited to your specific applications.
Welding parameters: Weld quality is influenced by parameters like rotation speed, feed rate and Z-force. Conducting prototyping tests on coupons is essential to identify optimal welding parameters, ensuring the resulting welds are strong and intact. These tests are crucial for achieving the desired weld quality and integrity.
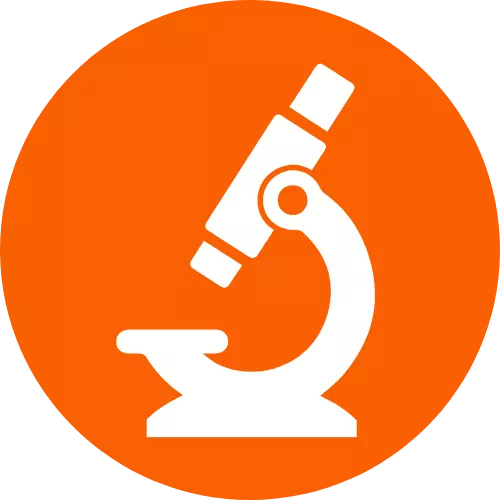
Metallographic cross-section
To verify the absence of porosity and lack of penetration in welds, as well as to ensure good contact between the FSW tool and the part surface, two metallographic cross sections are required.
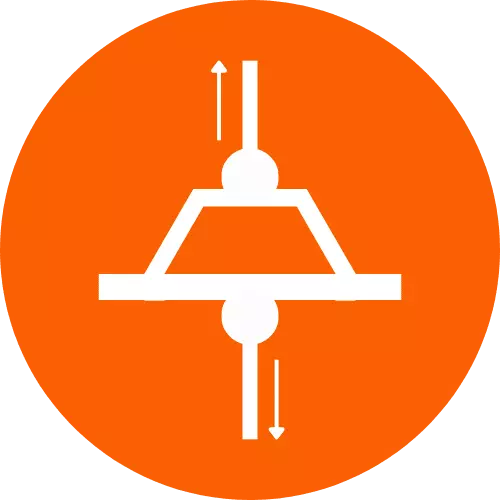
Tensile test
Conducted to assess the tensile strength of FSW welded panels in compliance with ISO25239. During these tests, the stiffener welded to the skin is subjected to pulling forces in a static test.

S-bending test
The S-bending test involves bending the weld to evaluate the strength of the aluminum stiffened panel that has been welded using FSW.

Visual test
The visual test identifies excessive flash and verifies correct shoulder force. Anomalies may suggest weld weaknesses.
See Friction Stir Welding Applied to Stiffened Panels in Real-Time
Comparing FSW to Traditional Stiffened Panels Assembly Techniques
Friction Stir Welding vs. Riveting
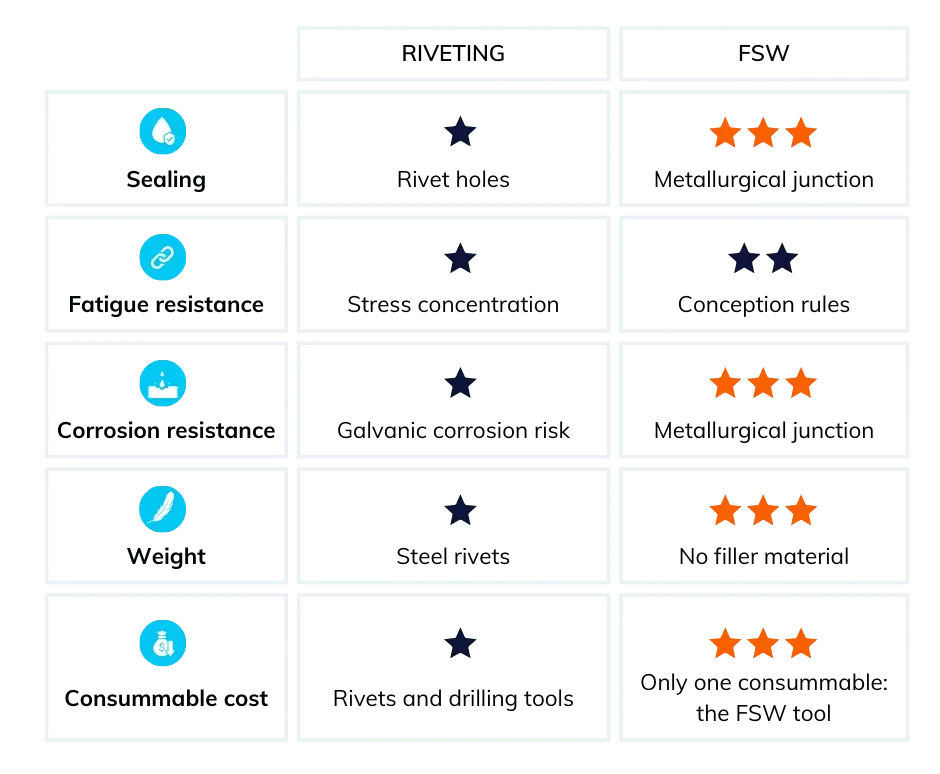
Friction Stir Welding vs. TIG and MIG
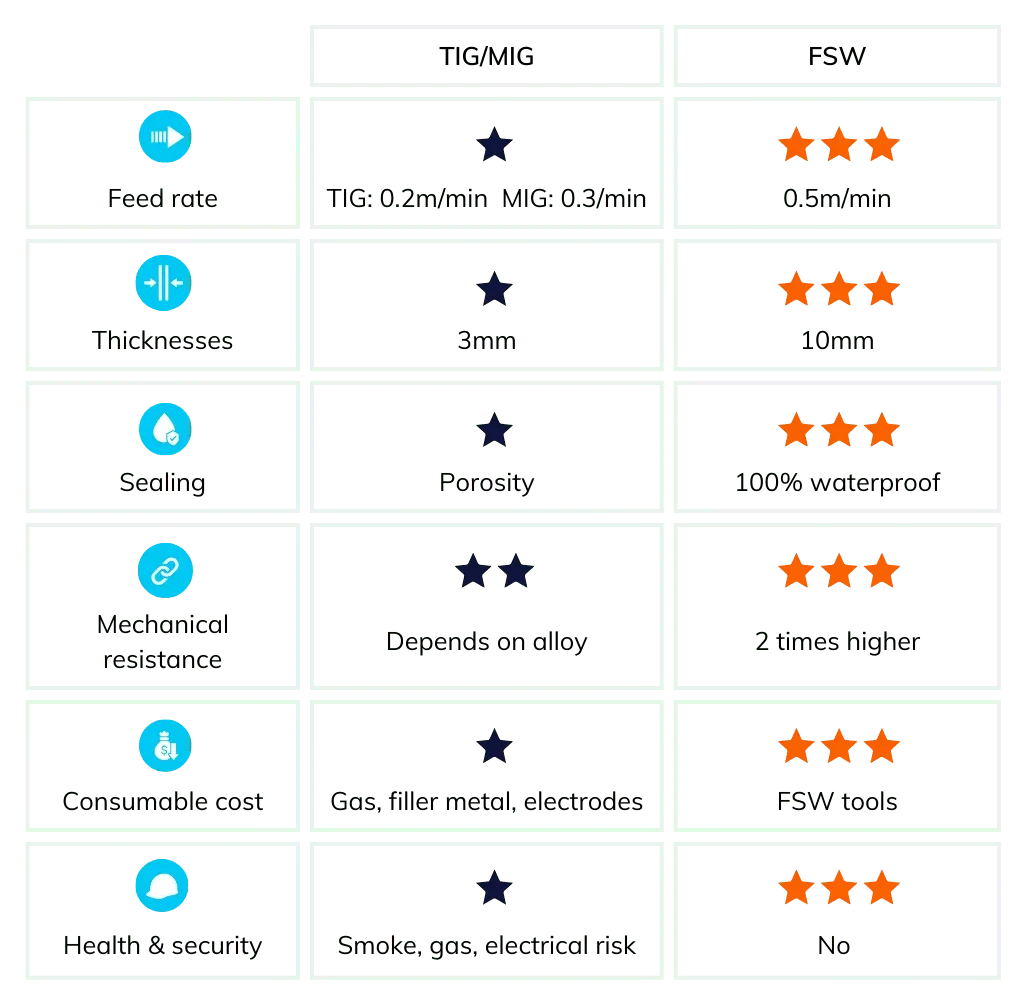
Aluminium Stiffened Panels: Key Concerns for Critical Sectors
In the realm of advanced manufacturing, the emergence of Friction Stir Welding as a reliable technique has transformed how industries approach assembly and design. FSW-welded stiffened panels stand out, not just for their robustness but also for their adaptability and efficiency in construction. These panels are renowned for their mechanical stability, lightweight attributes and resistance to environmental challenges, qualities that are sought after in high-demand sectors. Industries ranging from automotive to aerospace, from shipbuilding to railway, have witnessed the transformative benefits of these welded panels
Stiffened panels play a pivotal role in various sectors where high mechanical resistance is imperative:
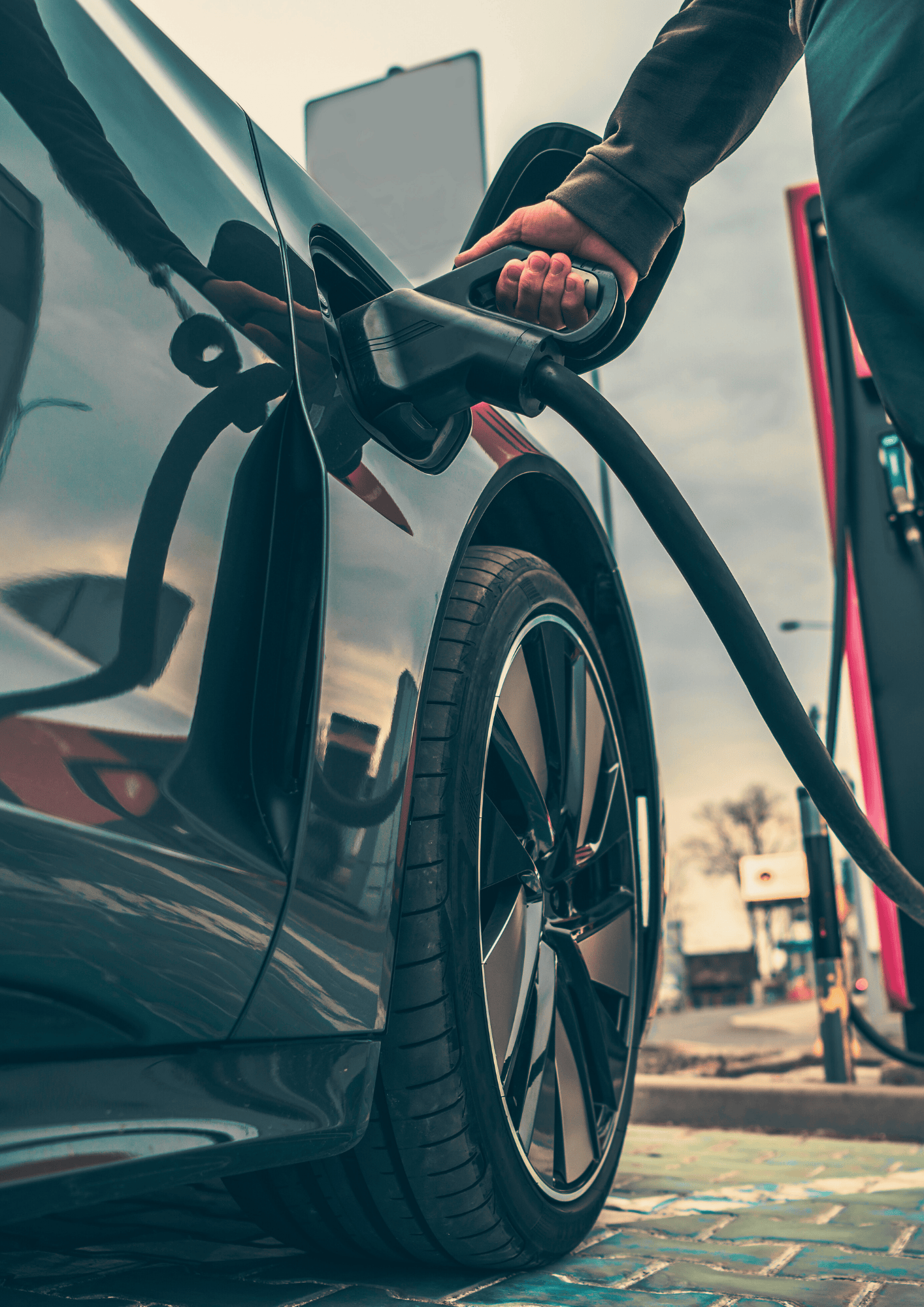



They Trust Us




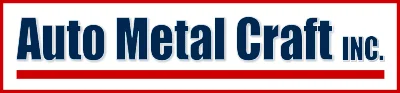
“At Calip, we use Friction Stir Welding technology for three main reasons. First, for sealing purposes. Our clients often come to us with sealing challenges for their components and we find that FSW provides the only reliable solution. Second, we value the mechanical strength that FSW offers. As we work with very large profiles that sometimes require reassembly, the mechanical strength of the weld is crucial. The third advantage is repeatability, which ensures consistent quality across multiple welds.”
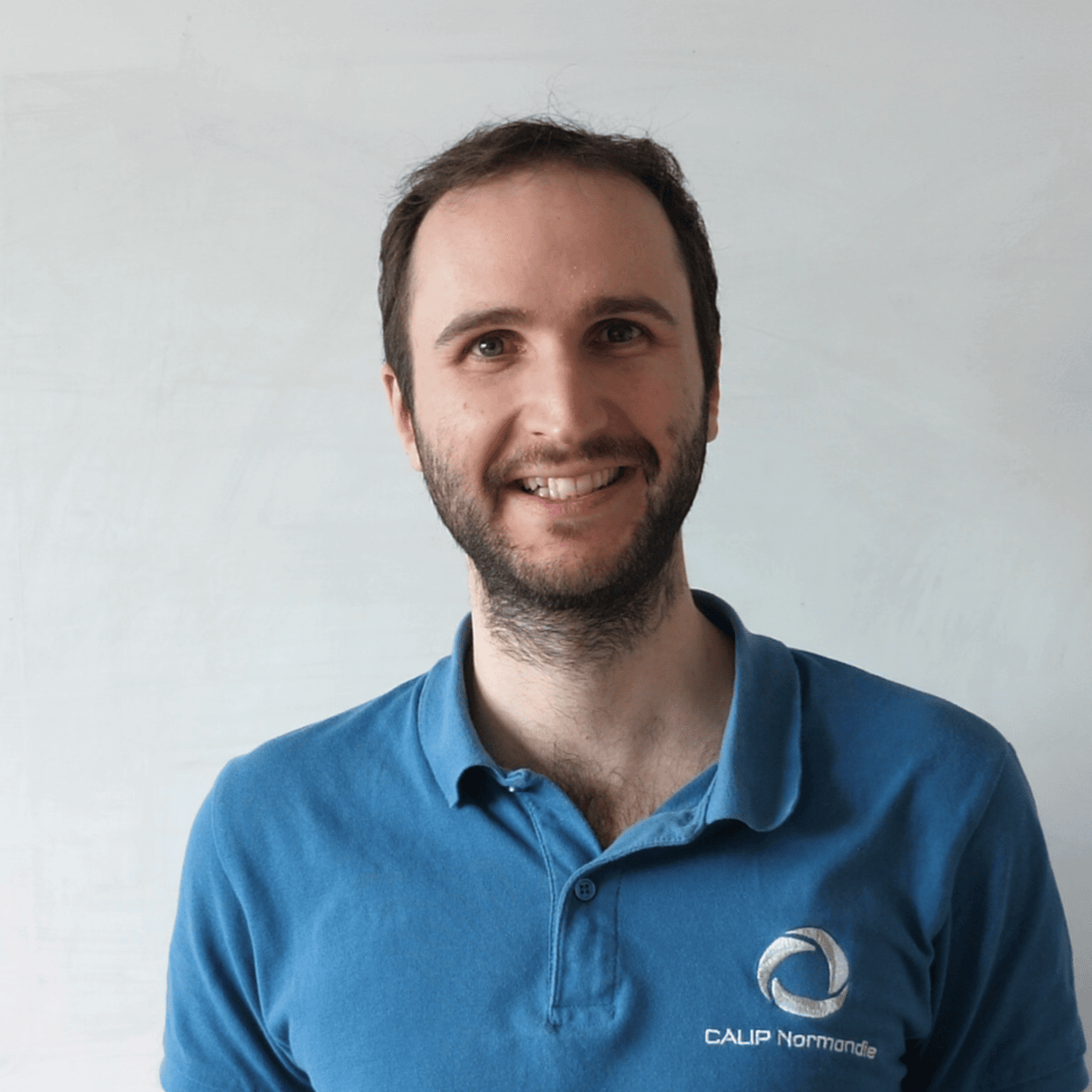
Gabriel Venet
Doctor of mechanical engineering

“FSW technology has the possibility that, when you weld, you don’t degrade the material as other process or other joining technologies. The main advantage that we see at Stirweld is the intercompability and the flexibility that the head provides us compared with a dedicated machine.”

Mario Alberto Solís Alvarez
R&D Innovation Engineer

Dive Deeper: Comprehensive FSW Stiffened Panels Resources
Are you curious to learn more about stiffened panels welded by FSW? We provide everything you need, including webinars, blog articles and whitepapers.
Webinar – 45 min
Stiffened panels welded by FSW
Explore innovative friction stir welding technique for joining stiffened panels. The special qualities of 6xxx alloys and the intricacies of the high strength 2xxx and 7xxx aluminum alloys are clarified in this session. Take advantage of the knowledge that top industry players have to offer.
Blog articles – 5 min
Stiffened panels welded by FSW
4 essential elements for high quality FSW
White paper – 20 min
Aluminium stiffened panels welded by FSW
Explore in-depth the precise manufacturing of stiffened aluminum panels using FSW in this white paper. Overcome assembly challenges by using a process that prioritize robustness and endurance.

White paper – 20 min
Friction Stir Welding: principles & trends
Explore the nuances of FSW with our white paper. Learn about its operational benefits, distinctive product strengths, economic benefits, range of equipment and current market trends.
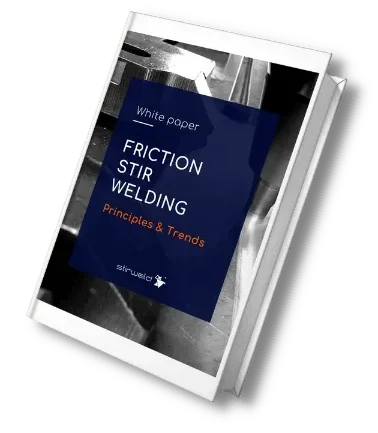
Ready to Revolutionize your Stiffened Panels Assembly?
With our state-of-the-art FSW technology, experience greater cost-effectiveness and performance. To discuss specific solutions for your stiffened panel manufacturing needs, please contact our specialists.