STIRWELD FSW SERVICE
Friction Stir Welding Protyping
Codesign, clamping jig, quality control, support and optimization.
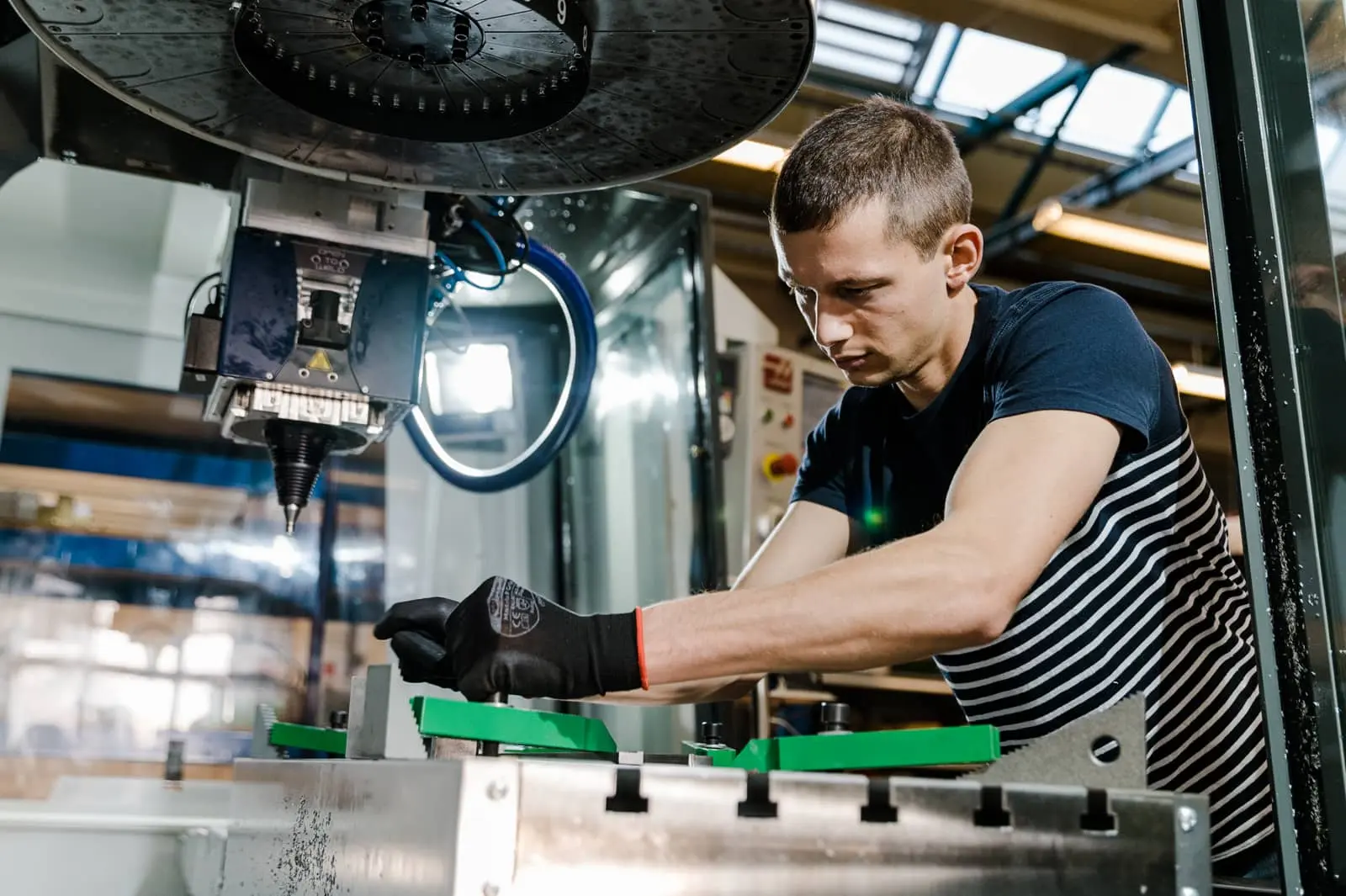
Why Choose Stirweld for Prototyping Your FSW-welded Parts?
Discover the Stirweld difference: a blend of unrivaled FSW expertise, industry acumen and advanced friction stir welding prototyping techniques awaits you.

Adaptive Industry Excellence
Specializing in complex projects across various sectors such as aerospace, automotive and naval, we offer expertise in intricate welding needs and adapt swiftly to your requirements. Keeping pace with the latest technological advances, we maintain a proactive and cutting-edge approach.
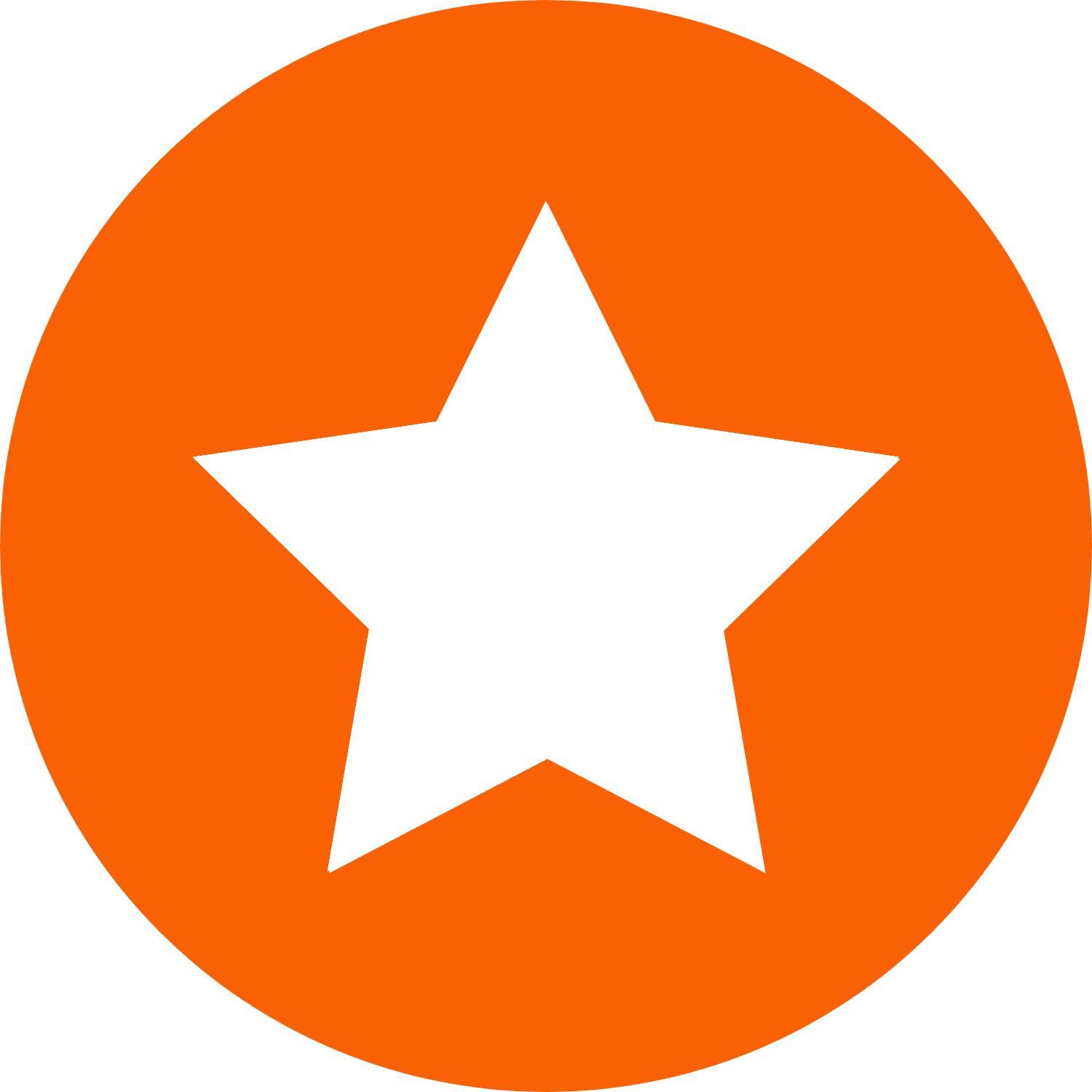
FSW Expertise Unmatched
Our team, comprised of 6 friction stir welding specialists, including 2 IWEs and 1 one worldwide FSW expert with 18 years of FSW experience, is here to assist you from the design of your part to the qualification of the weld, including setting the welding parameters.
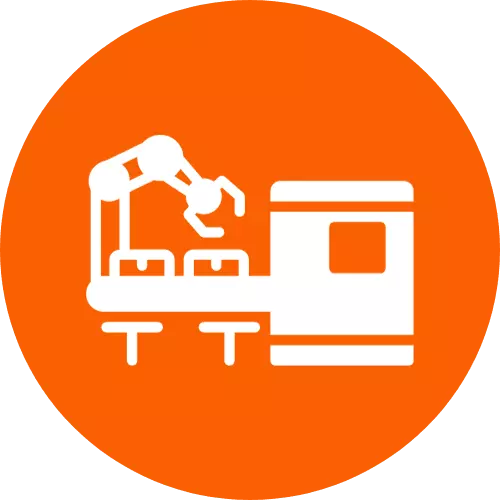
Advanced Prototyping Arsenal
Our prototyping workshop is equipped with 4 CNC machines and an industrial robot. Each of these machines is fitted with an FSW head tailored for machining centers, as well as an FSW robot spindle. We can accommodate parts of any size and shape, whether they require orbital welding or not.
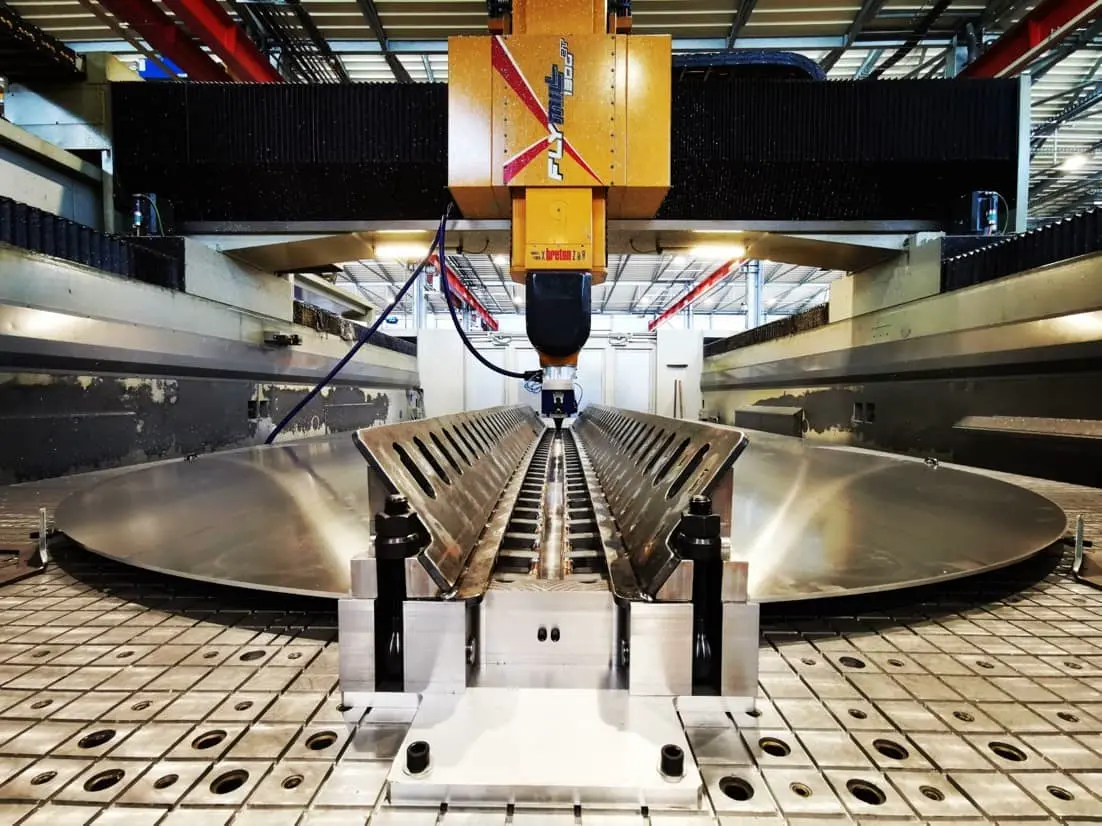
BRETON FLYMILL
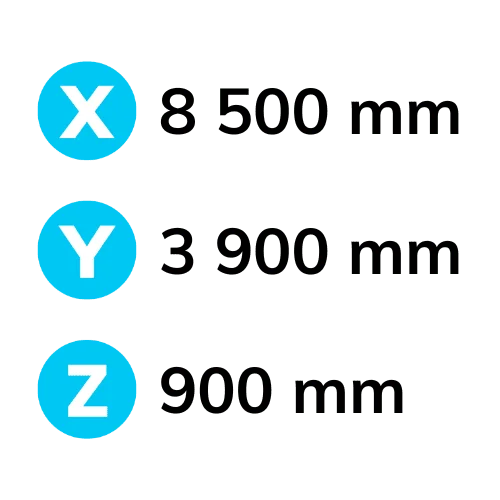
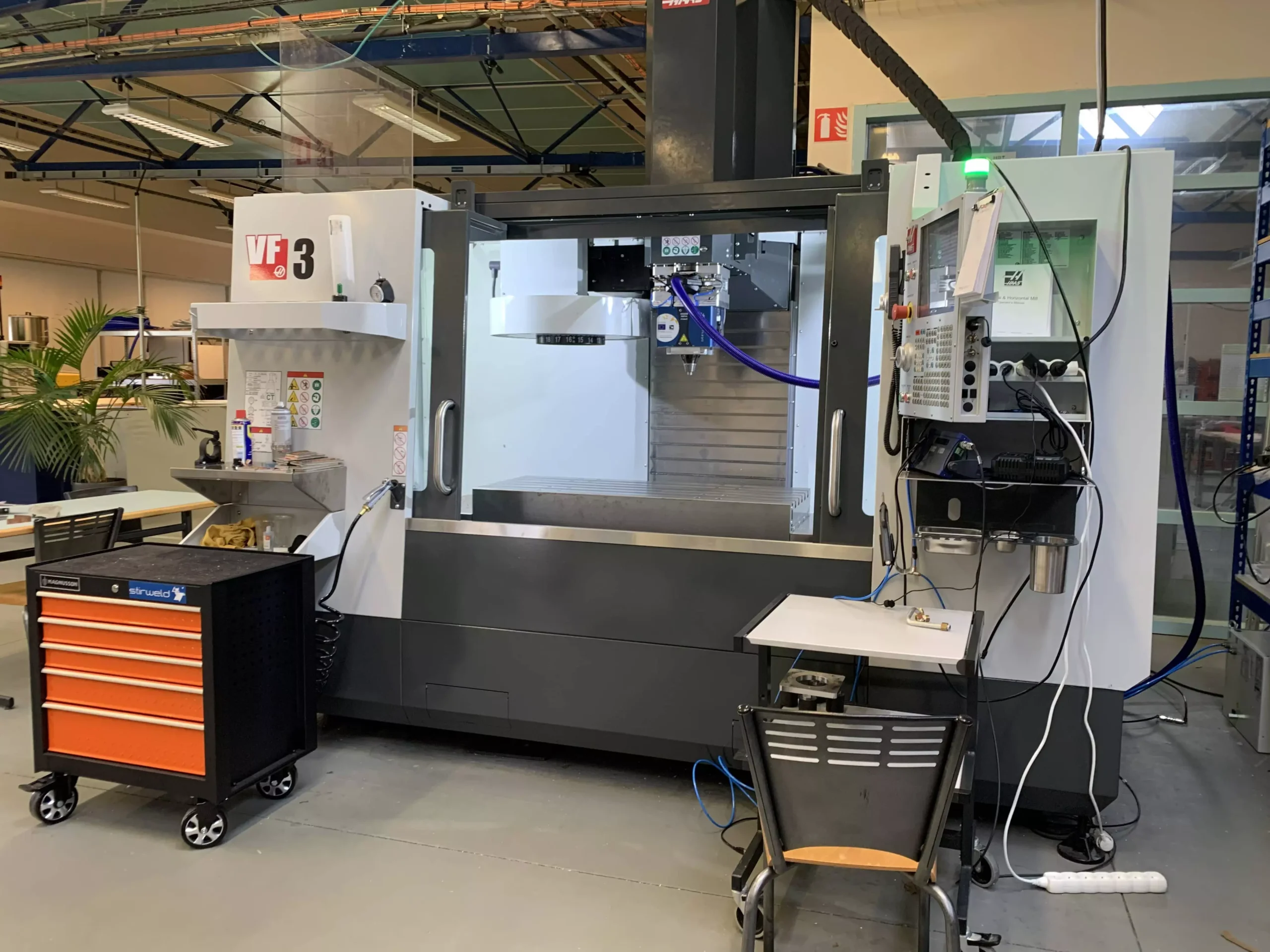
HAAS VF-3
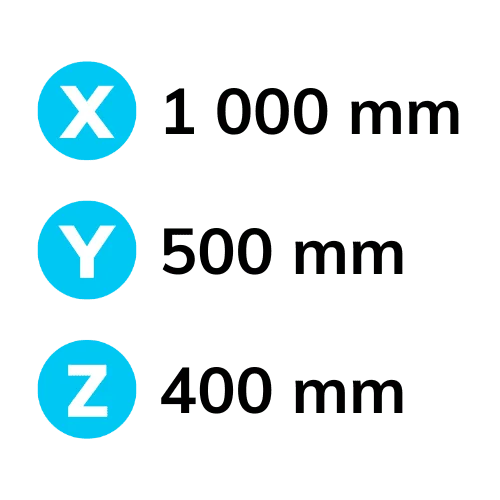
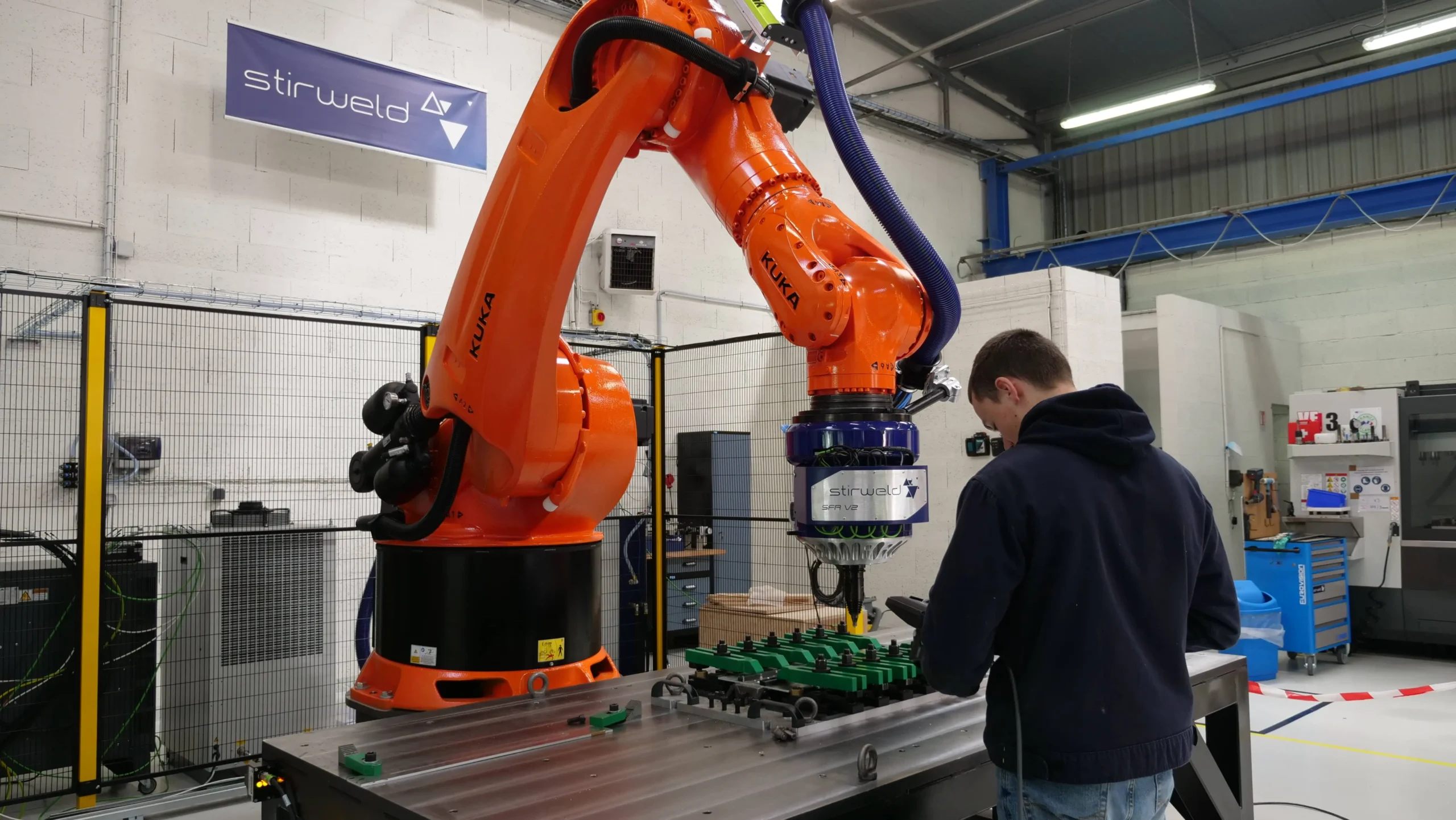
KUKA

DOOSAN MYNX
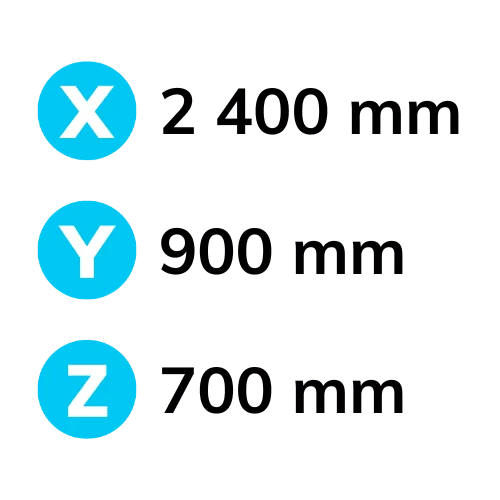

DAEWOO
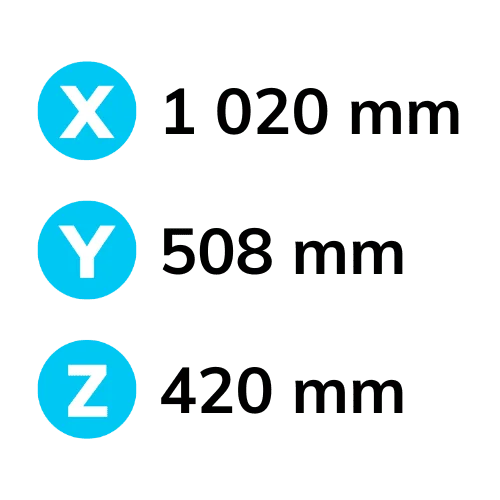
Friction Stir Welding Prototyping: Your Journey from Concept to Creation
Friction Stir Welding is a groundbreaking technique that has reshaped the way we approach welding projects. At Stirweld, we not only master this craft, but we also guide you through every stage of the prototyping process. From the initial feasibility assessment to the production of initial batches, our aim is to ensure your project benefits from the precision, efficiency, and quality that only FSW can offer.
What follows is a detailed walkthrough of the four key stages of our FSW prototyping service:
Step 1
FSW feasibility study and design recommendations
There are two potential scenarios when working with us. Firstly, you might have a part that was already produced using an alternative process, such as screwing, conventional welding, EB welding or brazing. Alternatively, we can embark on a fresh journey, starting the project entirely from scratch. Regardless of the starting point, our approach remains consistent. We commence with an FSW feasibility study that can lead to insightful design suggestions or even the conceptualization of a completely new part tailored to your FSW needs. Furthermore, our commitment extends to optimizing the Friction Stir Welding process, ensuring both cost-effectiveness and the highest standard of weld quality.

Step 2
Design and manufacturing of a friction stir welding prototype clamping jig

Efficient Friction Stir Welding depends on clamping system. At Stirweld, understanding the specifics of each project is crucial to us, and we strive to create a clamping solution that meets individual requirements. The journey starts with a thorough examination of component geometry to pinpoint essential support areas and determine the necessary clamping force. The route of the FSW tool is also taken into account, aiming for smooth movement and the best welding conditions. Such a careful method enables the creation of a prototype clamping jig that not only holds the component securely but also optimizes the FSW procedure.
Step 3
Determination of your FSW parameters by our experts (WPS/PQR)
We guide you in refining your welding parameters, encompassing the selection of the ideal FSW tool, defining the welding force and determining tool rotation and advance speeds. Our aim is to fine-tune these settings, ensuring consistently high-quality welds. Tool positioning, specifically identifying its leading and trailing sides, is also vital. Every welding detail is documented in our WPS (Welding Procedure Specification). If needed, we offer ISO 25239 / AWS D17.3 qualification at our facility, including macrography and various tests. Findings are then consolidated in our PQR (Procedure Qualification Request).
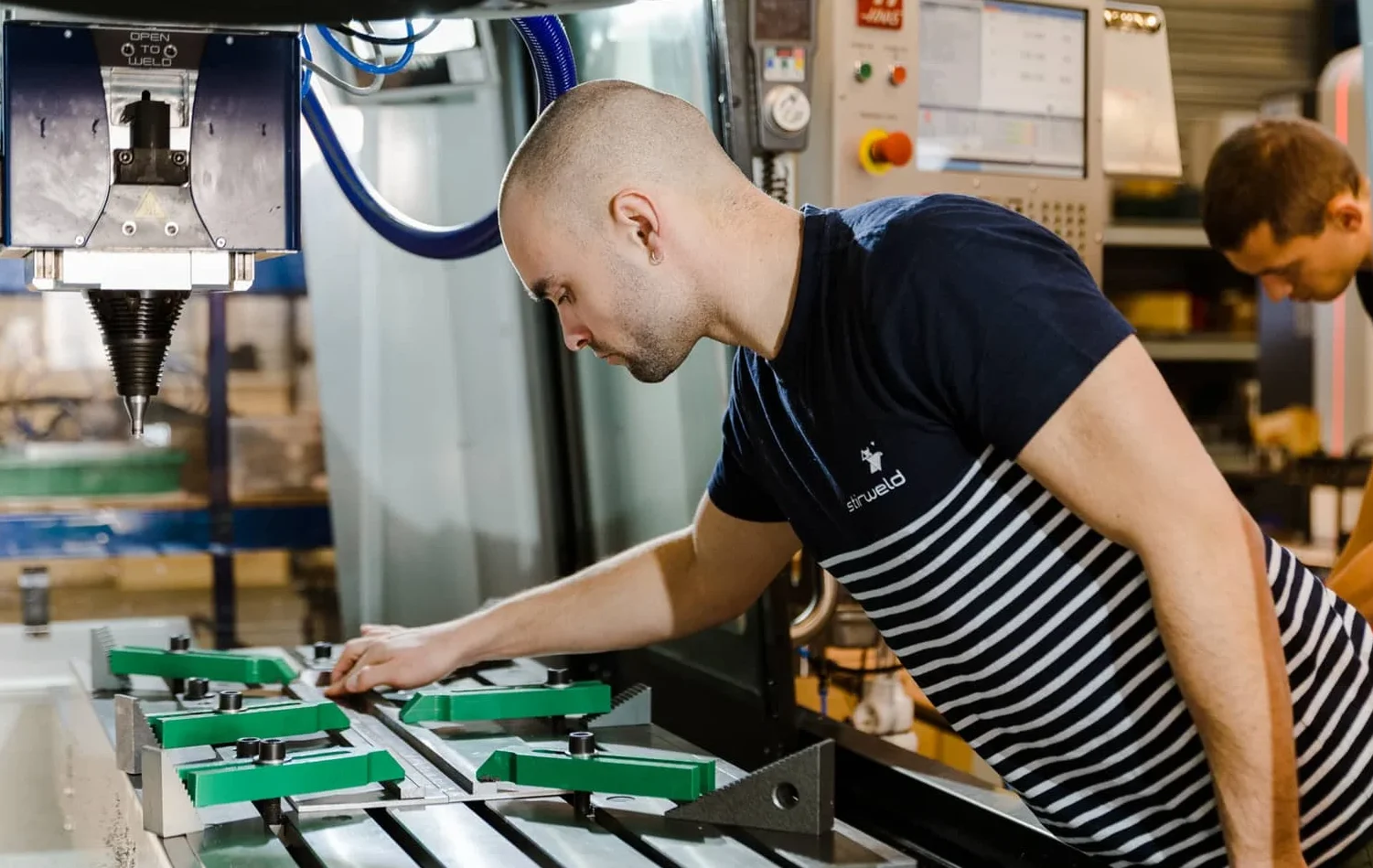
Step 4
Friction Stir Welding of your prototype

Once welding parameters are set and refined, we’re prepared to weld your prototypes. Upon request, quality checks can be conducted on the welded prototype:
Stirweld can also handle initial batch productions, ranging from 10 to 500 units depending on their intricacy. After welding and quality checks, parts are shipped to your specified location.
They Trust Us




Dive Deeper: Exploring Stirweld FSW Equipment
Stirweld stands at the forefront of Friction Stir Welding innovation, underpinned by a suite of advanced equipment. Each piece embodies years of research, dedication and a passion for engineering excellence. Dive into the essence of what makes our FSW technique unmatched:

FSW heads for CNC
Stirweld FSW range of heads showcases the fusion of precision engineering and innovative design. Our Standard FSW head offers versatility across multiple machinery axes, ensuring impeccable welding results. Complementing this is our FSW head with a retractable pin, uniquely designed to eliminate exit holes.
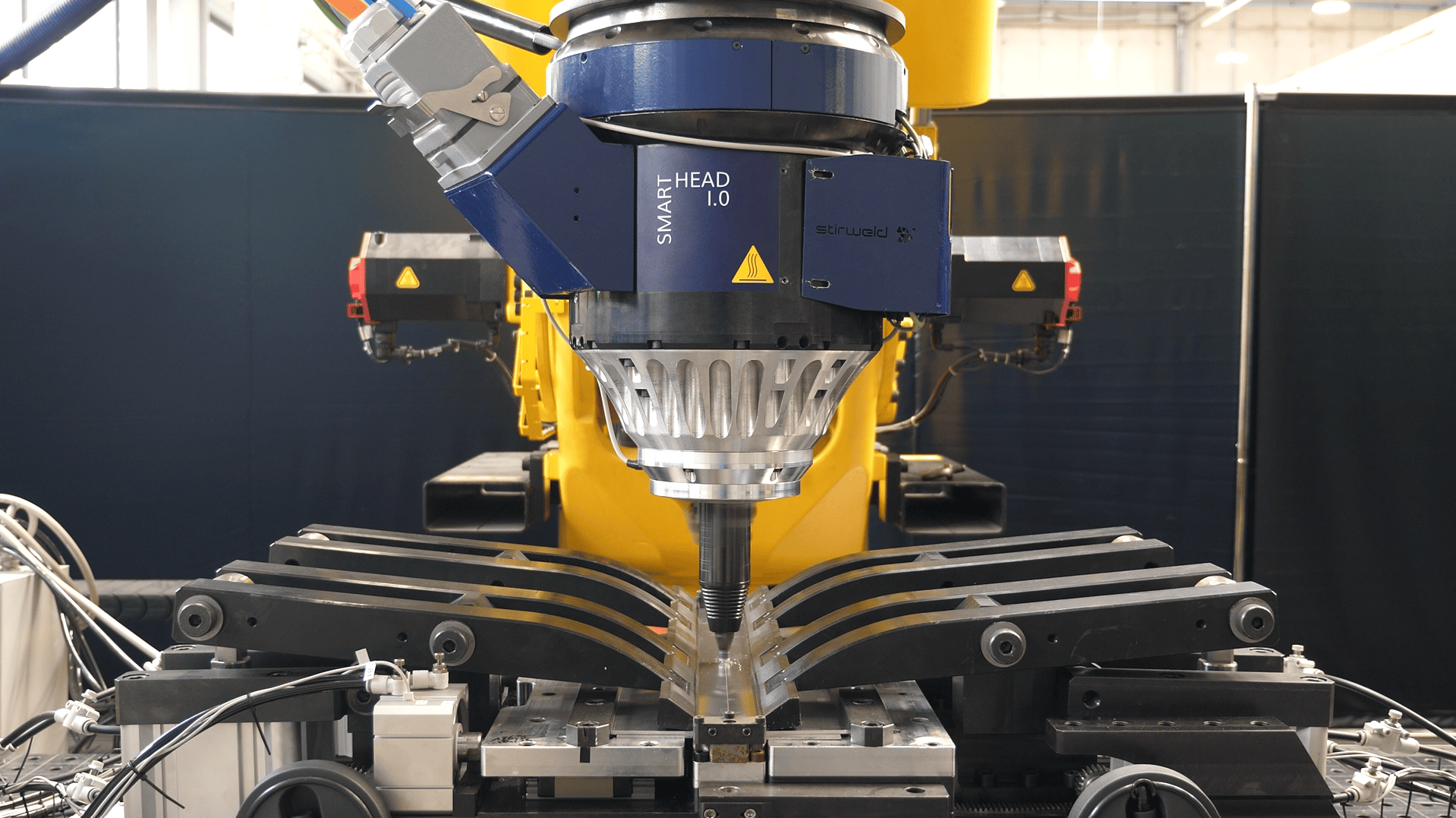
FSW spindle for robot
Engineered for robust robots, our FSW spindle evolves standard industrial robots into versatile powerhouses. This robotic FSW strategy marries Friction Stir Welding with both welding and machining operations, amplified with automated tool interchange capabilities.
From Idea to Prototype: Let’s Innovate Together!
Entrust us with your vision and we’ll shape it into a piece 100% weldable by FSW with unparalleled quality. Dive into the future with Stirweld’s expertise.