Mounting Bracket and FSW: Friction Stir Welding performance in response to the welder shortage
Mounting brackets are applications to support various loads and mechanical elements in many industrial sectors. Mounting brackets welded by Arc (TIG or MIG) present various technical performance problems (such as lack of mechanical strength or sealing problems), as well as a lack of qualified welders. Thanks to the different FSW products of the Stirweld range, we address these technical and human deficits by offering easy to use and low-cost solutions for the assembly of mounting brackets.

Mounting bracket and friction stir welding: technical specifications
Friction stir welding is a solid-state welding technique. The melting point is not reached as the deformation of the material is done by the rotation of the FSW tool in the material. FSW offers many advantages regarding the assembly of aluminium brackets, both in terms of economic and mechanical performance. Many industries have therefore adopted this new joining process to weld their mounting brackets at lower cost and without defects.
FSW applications adapted to the mobility sectors
Mounting brackets are used to support various mechanical elements such as cables, tubes or other mechanical equipment. These mounting brackets can be found in industrial equipment, military equipment and mobile machines.
In the mobility sector, certain criteria such as the weight of components are crucial. This is the case for trains, trucks, airplanes, helicopters, agricultural machinery, tanks, submarines and many others. To meet this weight requirement, applications such as mounting brackets are made of aluminium, which is one of the strongest and lightest metals. The lighter the components of a vehicle, the lower the energy and fuel consumption.
Concerning ships and submarines, aluminium is also preferred to limit the risk of corrosion. Aluminium has the ability to become passivated (chemical reaction on metals). This is due to the reaction of aluminium and oxygen, which forms a thin, amorphous oxide layer that protects the metal from corrosion.
A high strength double friction stir weld (FSW) joint
With welding processes such as arc welding (TIG/MIG) used to assemble mounting brackets, weld defects frequently occur. These defects have a direct impact on the mechanical strength of the applications. Thanks to a double assembly – mechanical assembly and FSW – FSW welded aluminium mounting brackets benefit from a high mechanical strength.
The steps of a double mounting bracket assembly in friction stir welding :
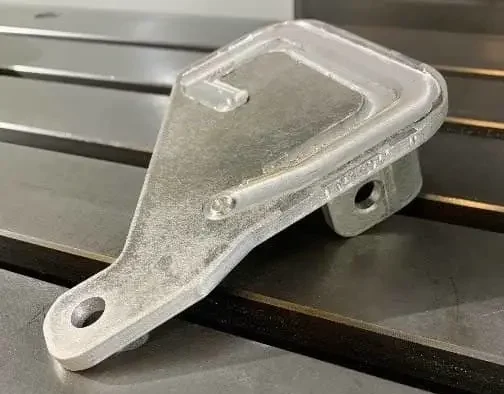
Mounting bracket welded by FSW

Breakdown of the FSW welding steps of a bracket mounting
The double mortise and tenon joint is combined with friction stir welding, providing high mechanical strength and a perfect seal.
FSW assembly of mounting brackets: T-weld configuration
In friction stir welding, there are different welding configurations: butt, lap and t welding.
To weld brackets using FSW, the parts are positioned in a T-weld configuration. In this case, and after a mechanical mortise and tenon joint, the two aluminium parts are welded together (vertically) on top of each other (horizontally), forming a T.

FSW welded mounting brackets: a stronger and more economical process
Friction stir welding is a welding process without any melting and material input. The welding operation is carried out in a solid state by mechanical deformation generated by the rotation of the FSW tool in the workpiece.
FSW for perfect mechanical strength
Compared to arc welding techniques, an FSW welded mounting bracket has twice the mechanical strength. This increased strength is the result of the double mortise and tenon joint combined with friction stir welding.
FSW according to Stirweld as a way to counteract the shortage of welders in the world
Like many jobs in the industrial and metal sector, the number of welders is in total decline. It is estimated that within the next 5 years there will be a shortage of 400,000 welders in Europe, as well as in the USA.
The Stirweld FSW heads allow the assembly of mounting brackets by friction stir welding (FSW) in a fully automated way. In addition to offering much better-quality welds with excellent mechanical strength compared to TIG/MIG processes, Stirweld’s FSW process is a perfect way to fill the welder shortage. Indeed, only two days of training are required to train your operators in friction stir welding.
By way of comparison, a Stirweld FSW hybrid head adaptable to a machining center represents the cost of a welder over 1.5 years.
Please note that we also offer our Stirweld Friction Stir Welding (FSW) heads for rental for less than 2000€/month.
To find out more about buying or renting a Stirweld friction stir welding head, contact us.

FSW for flawless welding
Unlike arc welding, FSW has no welding defects. It is common to find porosity or cracking defects on applications welded by arc welding processes (TIG/MIG). These defects affect two essential points in welding: the mechanical strength and the sealing of your parts.
Defects such as porosity or cracks in a weld will impact the mechanical strength and fatigue resistance of your mounting bracket. In FSW, once welded, your mounting brackets benefit from a high mechanical strength (twice higher than arc welding) and a perfectly tight weld (compared to 30% of non-tight welds in MIG welding).
These defects are not found in friction stir welding, because this technology complies with a set of welding parameters in order to determine the ideal temperature. Our FSW temperature measurement equipment will help to define the optimal parameters for a perfect and defect-free weld.

FSW for cost savings
The comparison here is very simple: friction stir welding to assemble a mounting bracket is considerably cheaper than MIG welding:
FSW: an ecological process
Conventional processes, such as MIG welding, require the use of gas. In addition, the high temperatures required to melt materials in arc welding result in high energy consumption, emission of harmful fumes (ozone O3), heat loss and light radiation which have an impact on the environment.
In contrast to these processes, friction stir welding does not use any material and consumes half the energy of arc welding. In FSW, only the tool is in action, and it rotates with an electrical efficiency close to 100%. The fact that FSW requires no heat, gas or material input and no surface preparation makes FSW a more environmentally friendly and safer welding process for operators.
Friction Stir Welding: an eco-friendly joining technology
Friction stir welding can be used to weld any aluminium alloy, unlike conventional welding processes such as MIG or TIG. High-strength aluminum alloys (2000 and 7000 series) are difficult to weld by arc welding. While in FSW, the welding operation is the same as for other 5000 or 6000 type alloys. These high strength alloys are used mainly in the aeronautical sector or certain applications such as mounting brackets which must have a tensile strength of more than 500 MPa (MegaPascal).
In MIG welding, only aluminium alloys 5000 and 6000 can be welded. These alloys have a maximum tensile strength of 250 MPa, which is half that of 7000 aluminium. Therefore, these mounting brackets can only be welded by FSW, a process that does not reach the melting point and allows the mechanical properties of the base material to be retained after welding.
Good to know: before FSW, it was necessary to weld together two 8mm thick aluminium sheets with a strength of 250 MPa, in order to obtain a tensile strength equivalent to a 4mm thick sheet with an Rm of 500 MPa. Today this is no longer necessary as 2000 or 7000 aluminium can be welded using FSW.

FSW Stirweld expertise on mounting bracket applications
Certified friction stir welding processes
At Stirweld, all our certifications of mounting brackets are controlled by the welding standard FSW ISO 25239. This standard allows us to meet certified quality and control requirements.
We perform three quality control tests on all our applications:

Bending Test
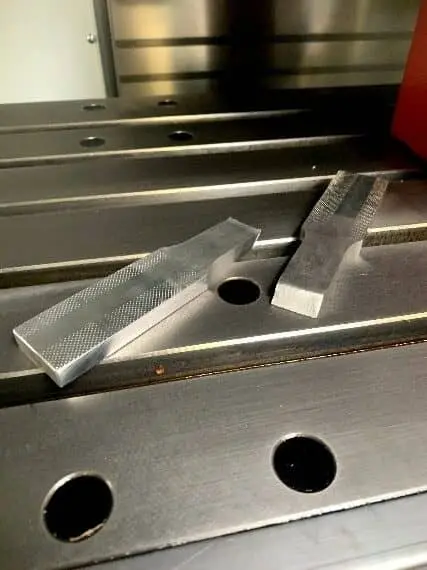
Bending Test

Metallographic cut
Demanding references for FSW Stirweld mounting brackets
Today, the FSW technologies developed within Stirweld are used in the railway and military sectors. These technologies allow the assembly of mounting brackets by FSW welding. If you would like to know more about our friction stir welding processes and applications, our FSW specialist teams are available to answer your questions, please contact us.