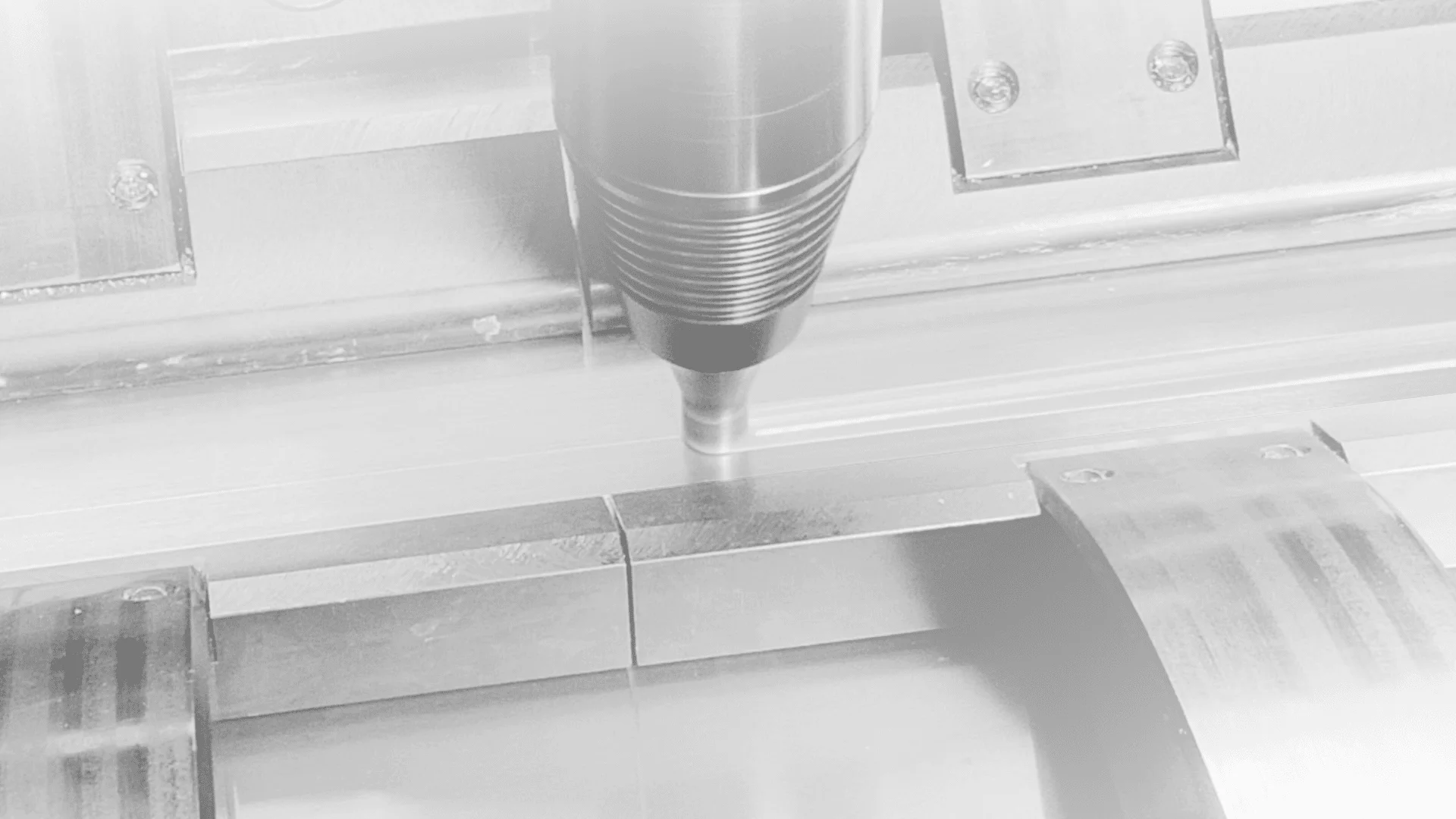
Friction Stir Welding Process
A technical overview: how FSW transforms traditional welding paradigms
Why Opt for FSW in Sustainable Industrial Welding?
In the realm of advanced welding technologies, Friction Stir Welding (FSW) stands out for its versatility, eco-friendliness and precision. The process offers a myriad of advantages, making it an ideal choice for industries striving for peak efficiency and environmental responsibility.
Here’s why FSW is a game-changer in sustainable welding:

High TRL
Rated at level 9 on the Technology Readiness Level (TRL) scale, FSW is a trusted and highly advanced method for joining materials, predominantly aluminum and copper, while retaining near-original mechanical properties.

Versatile Aluminium Welds
Friction Stir Welding offers the unique capability to weld high-strength aluminum series such as 2000, 6000 and 7000. Additionally, it facilitates mixed joins with materials like copper, aluminum castings or steel.

Eco-Conscious Process
FSW stands at the forefront of eco-friendly welding. By sidestepping pre-weld cleaning, wire feeding and shielding gases, it guarantees a cleaner process, completely free from harmful emissions and noxious fumes.
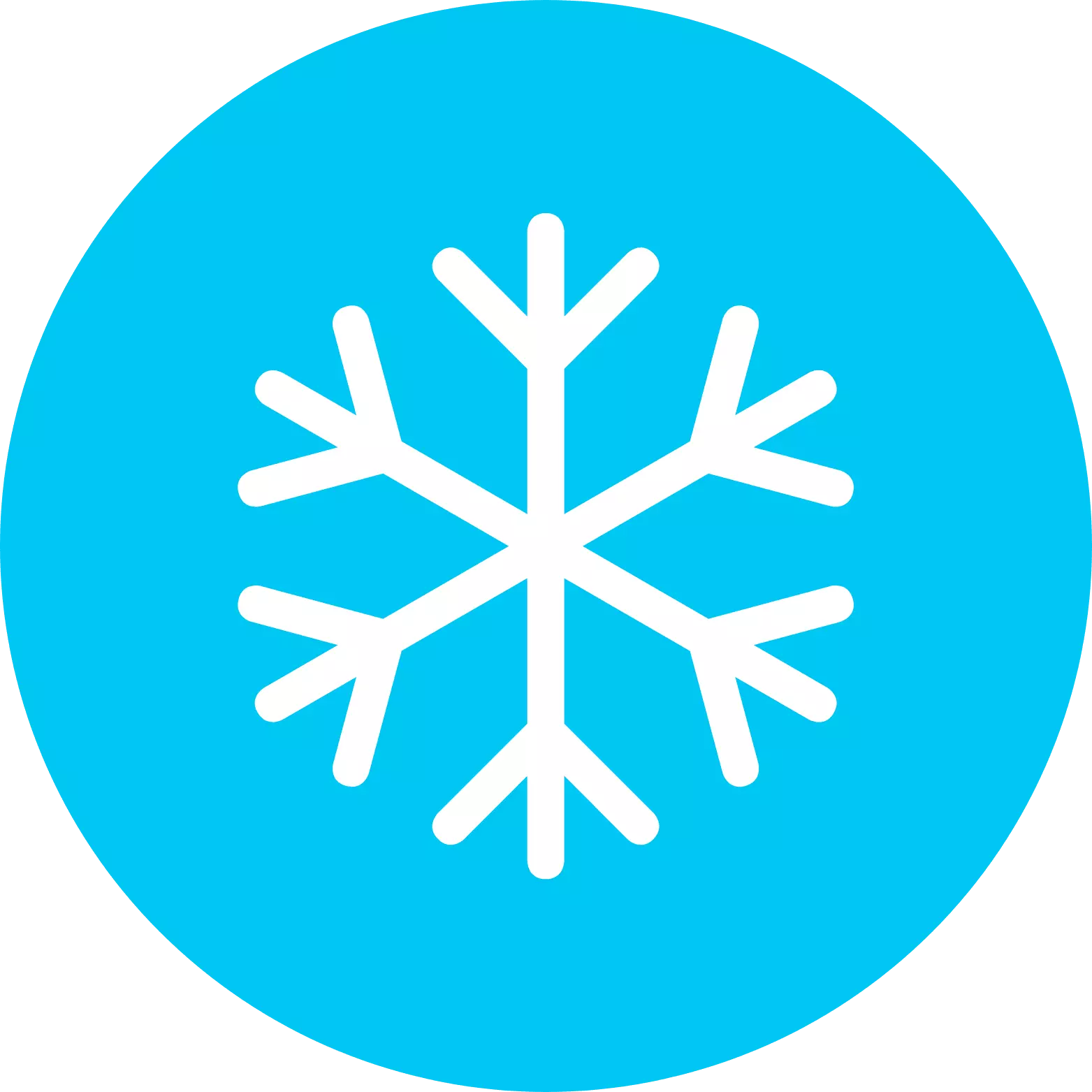
Cold Welding
Friction Stir Welding revolutionizes the very concept of “cold welding”. By leveraging mechanical deformation without resorting to melting or using external additives, it effectively negates risks associated with porosity.
Unlocking Friction Stir Welding: 4 Steps for High-Quality Welds
Friction Stir Welding is a unique and intricate process that demands precision at every step. By understanding each phase of the procedure, one can ensure the highest quality of welds, which are both robust and immaculate. Let’s dive into the nuanced stages of this groundbreaking welding method:
Before anything else, the parts to be welded are clamped. They can be positioned either edge to edge, commonly referred to as “butt welding”, or by overlapping them, which is termed as “lap welding”.
The central player in FSW is the tool, which boasts a shoulder and a pin. The shoulder generates heat via friction, while the pin is designed for stirring. As it rotates at speeds fluctuating between 400 and 6000 RPM, the tool is then inserted vertically into the material, ensuring a secure engagement.
After an essential thermal stabilization period lasting 1 to 5 seconds, the tool begins its journey, moving at a steady pace. The speed varies between 700 and 3000 mm/min, contingent on the material type and thickness. The friction-induced heat softens the material, rendering it malleable. This state allows the stirring pin to seamlessly blend the pieces together, ensuring a robust joint.
Once the welding journey concludes, the tool is carefully elevated in a vertical motion, leaving behind an exit hole. While this might initially seem like an imperfection, there are different techniques available to rectify this minor setback, ensuring a defect-free weld.
FSW Mastery: Key Parameters and Welding Configurations
Mastering the FSW Parameters for Optimal Welds
In the world of Friction Stir Welding, achieving the highest quality welds demands more than just the right equipment—it requires an understanding and mastery of the key welding parameters. These specific FSW parameters, when dialed in accurately, form the bedrock upon which the integrity, strength and longevity of the weld are built, ensuring not only optimal performance but also extended durability in real-world applications.
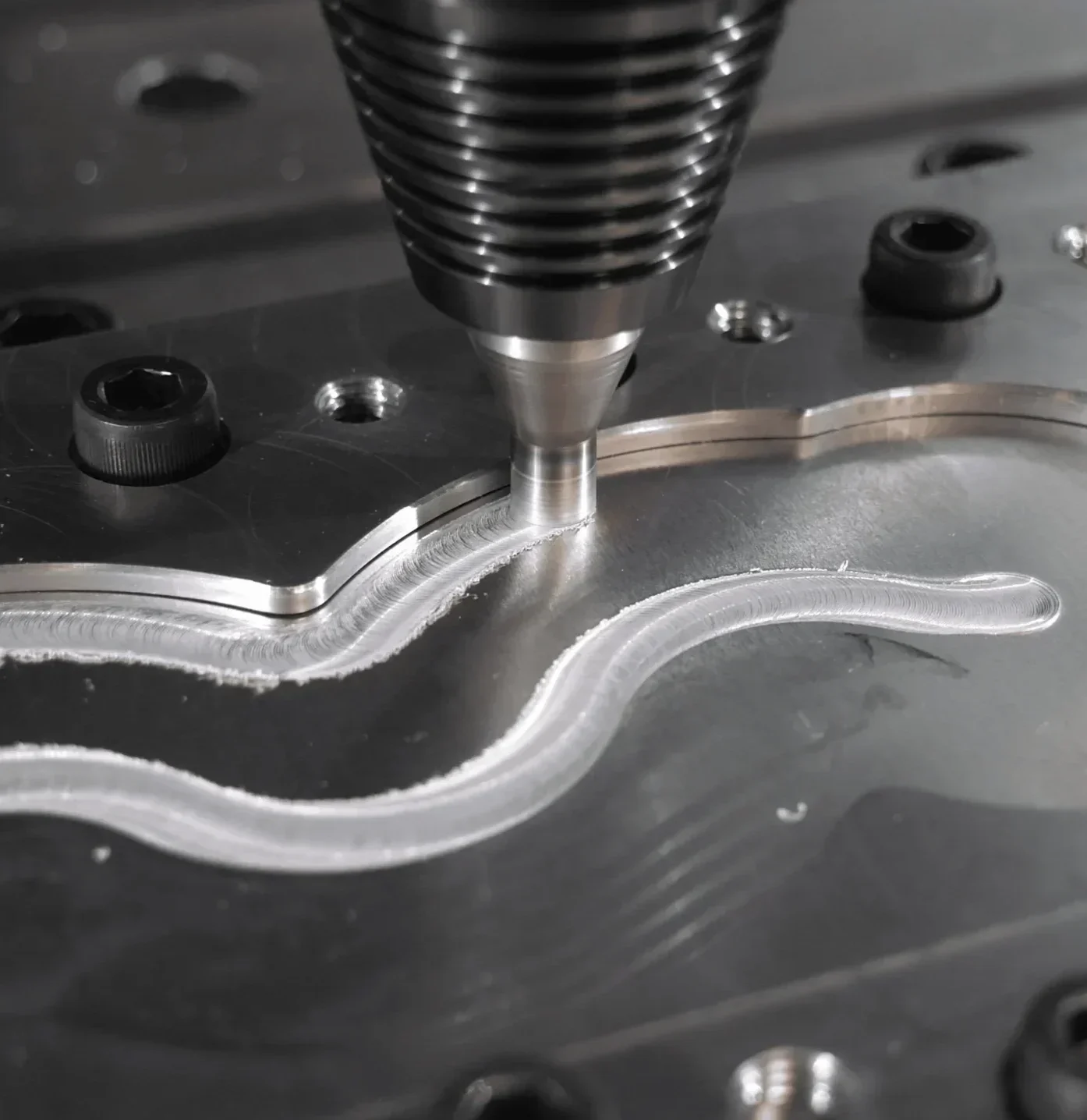

FSW tool geometry
The shape and design of the FSW tool play a pivotal role in determining the quality of the weld. Its design is intricately linked to the nature of the materials being welded and the desired outcome of the process.

Vertical force (in kN)
Applying the right amount of vertical force is vital. Insufficient force may not achieve the required stirring, while excessive force can cause a fast wear of the tool or deformation of the workpieces.
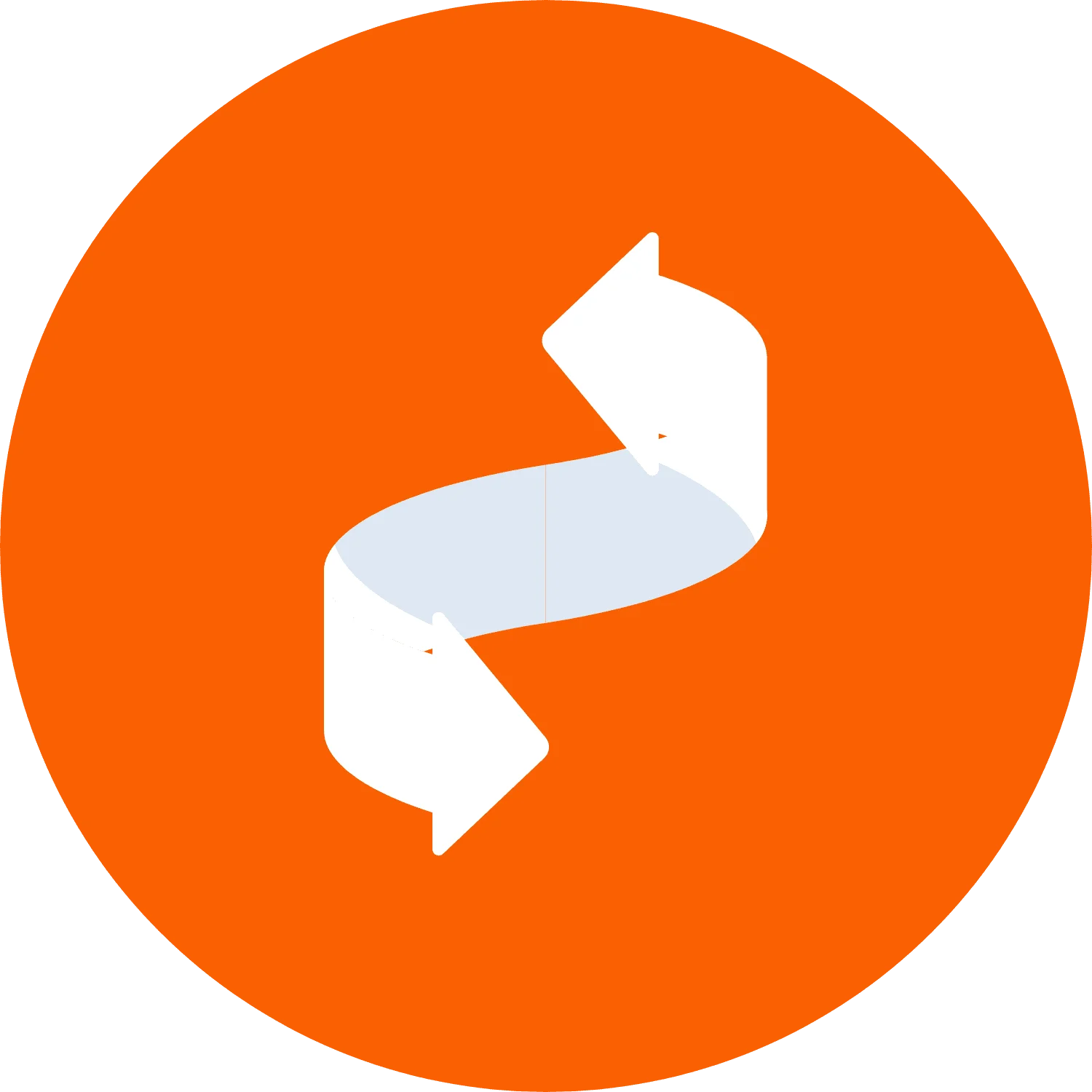
Rotation speed (in RPM)
The speed at which the FSW tool rotates can influence the heat generated during the process. An optimal speed ensures uniform heating and optimized material mixing.
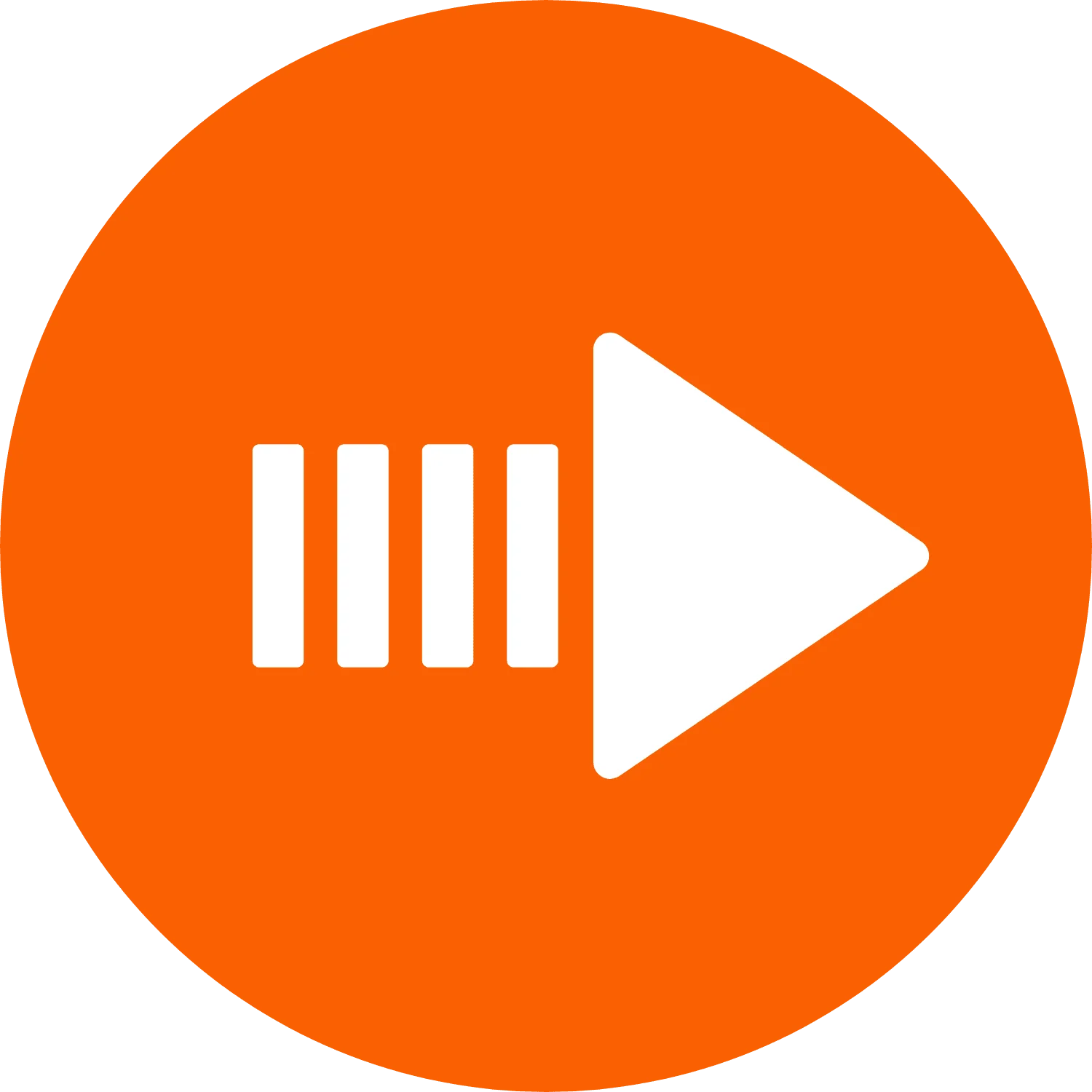
Feed rate (in mm/min)
The rate at which the tool traverses along the weld line determines the time the material spends under the influence of the tool. This affects the consistency and quality of the weld.
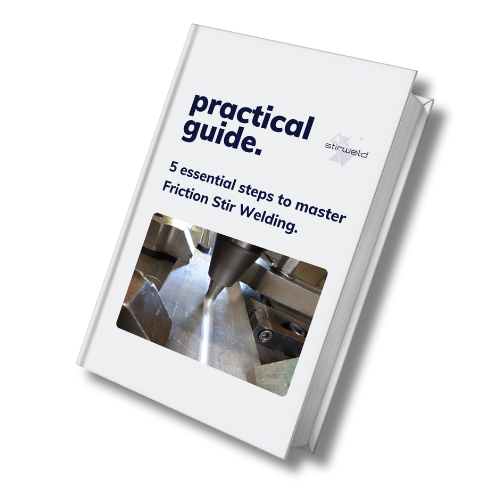
FSW RESOURCE
5 essential steps to master Friction Stir Welding
Explore our expert guide on Friction Stir Welding. Gain insights into each stage, from initial planning to expert certification, to elevate your welding projects!
Configurations Tailored to Your Needs
In the evolving realm of welding technologies, Friction Stir Welding stands out as a method that seamlessly marries precision with adaptability. FSW not only offers the advantage of a cleaner and more efficient welding process but also the flexibility in the ways materials can be connected, ensuring that each weld is tailored to its specific purpose and application. With this adaptability, it becomes paramount to understand the different FSW configurations available:

Butt welding: This configuration is distinguished by its precision in aligning parts edge to edge. Ideal for applications where a continuous and undisturbed joint appearance is desired, butt welding offers a seamless connection between materials. It ensures a homogeneous, high-quality fusion, which is vital for projects where both aesthetics and structural integrity are paramount. By preventing any overlap or offset, this method achieves an optimally smooth and consistent weld bead, ideal for scenarios requiring uncompromised material uniformity.

Lap welding: When the design calls for one material to be overlapped by another, lap welding proves invaluable. This configuration is especially suitable for situations where different materials or thicknesses need to be joined, as it provides a robust bond at the overlapping juncture. The lap joint is inherently designed to distribute stress over a larger area, enhancing the durability and resilience of the joint. Especially pivotal in applications where load-bearing capacities or thermal properties play a significant role, lap welding ensures a sturdy connection that stands up to rigorous demands.
Material Specifications: Which Are Weldable by Friction Stir Welding Process?
FSW is a cold-welding technique that relies on the mechanical deformation of materials, eliminating the need for melting or filler materials. This allows for a different range of metals to be welded with this approach:
To learn more about the materials compatible with FSW, check out our detailed article: Which materials are weldable by Friction Stir Welding?
Comparing FSW to Traditional Welding Techniques
Friction Stir Welding vs. TIG
FSW offers distinct advantages over traditional TIG welding. Unlike TIG, Friction Stir Welding doesn’t require melting, thus minimizing common defects like porosity and cracking. This method is especially beneficial for aluminum alloys as it better retains their mechanical properties. In essence, FSW stands out as an eco-friendly and efficient alternative, particularly for applications requiring higher reliability and consistency.
Friction Stir Welding vs. MIG
Friction Stir Welding process emerges as a groundbreaking alternative to traditional MIG welding. Unlike MIG, Friction Stir Welding operates without melting the material, dramatically reducing defects like porosity and cracks. This solid-state technique excels in preserving the mechanical properties of metals, especially for heat-sensitive alloys. Further benefits of FSW include the absence of protective gas and filler materials, leading to economic and environmental advantages. Additionally, FSW ensures minimal thermal distortion and consistently high-quality welds. Particularly effective for challenging alloys, FSW offers a reliable and advanced welding solution for modern industrial needs.

Friction Stir Welding vs. Brazing
Friction Stir Welding stands as a robust alternative to traditional brazing methods. While brazing relies on heating metals near their melting points, Friction Stir Welding offers solid-state welding that minimizes thermal distortion and stress. The mechanical blending of base materials in FSW results in notably stronger joints compared to brazed connections.
Additionally, the FSW process eliminates the need for filler materials or flux, leading to purer, more reliable joints. With its capability to weld challenging alloys and the added benefits of cost and environmental efficiencies due to the lack of consumables, Friction Stir Welding presents a cutting-edge solution for diverse industrial joining needs.
Friction Stir Welding vs. EBW
Compared to Electron Beam Welding (EBW), FSW process presents distinct advantages. While EBW requires a vacuum environment, FSW effortlessly operates in open air, streamlining the process. Whereas EBW has constraints due to material thickness, FSW surmounts such challenges, adeptly joining thicker sections. FSW boasts extensive material versatility, accommodating a diverse array of metals and alloys.
In terms of safety, FSW stands out as it doesn’t emit X-rays, a concern with EBW. Economically speaking, FSW setups generally come with a friendlier price tag than the intricate systems associated with EBW. Additionally, with pristine weld zones and reduced heat-affected areas, FSW guarantees efficient and top-quality joins, marking its dominance as a premier industrial welding technique.
Friction Stir Welding vs. Laser
FSW of aluminium alloys is easier and more cost effective than laser welding. It requires less expensive machines (100k€ versus 1 m€), less electrical power (20 times less) and no consumables apart from the wear resistant FSW tools (no gas, no wire).
If the shiny surface of aluminium reflects the laser light, the keyhole of the laser welding process becomes unstable and generates blowholes and sputters. Maintaining good laser welding quality is always challenging and requires substantial process know-how, while laser cutting is relatively simple, and is typically outsourced to a job shop.
FSW is a particularly easy and repeatable process as milling operation because it operates below the melting point (no molten pool, no gravity impact, no shielding gas). FSW is beneficial for high-strength aluminium alloys, for joining extrusions to extrusions and for mixed material combinations.
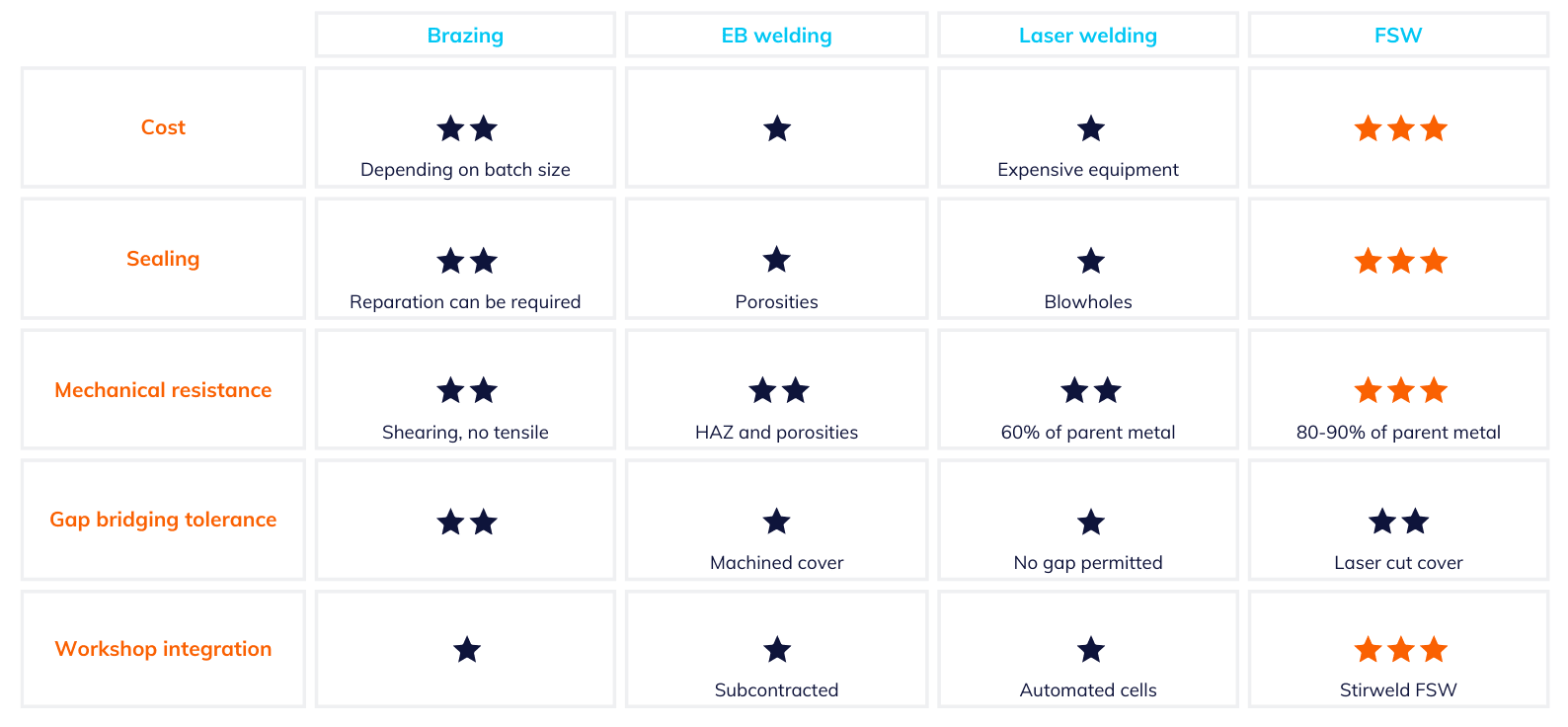
Exploring FSW applications
The capacity of Friction Stir Welding process to produce robust and consistent welds in materials traditionally difficult to join sets it apart, making it a favored choice for diverse industrial uses:
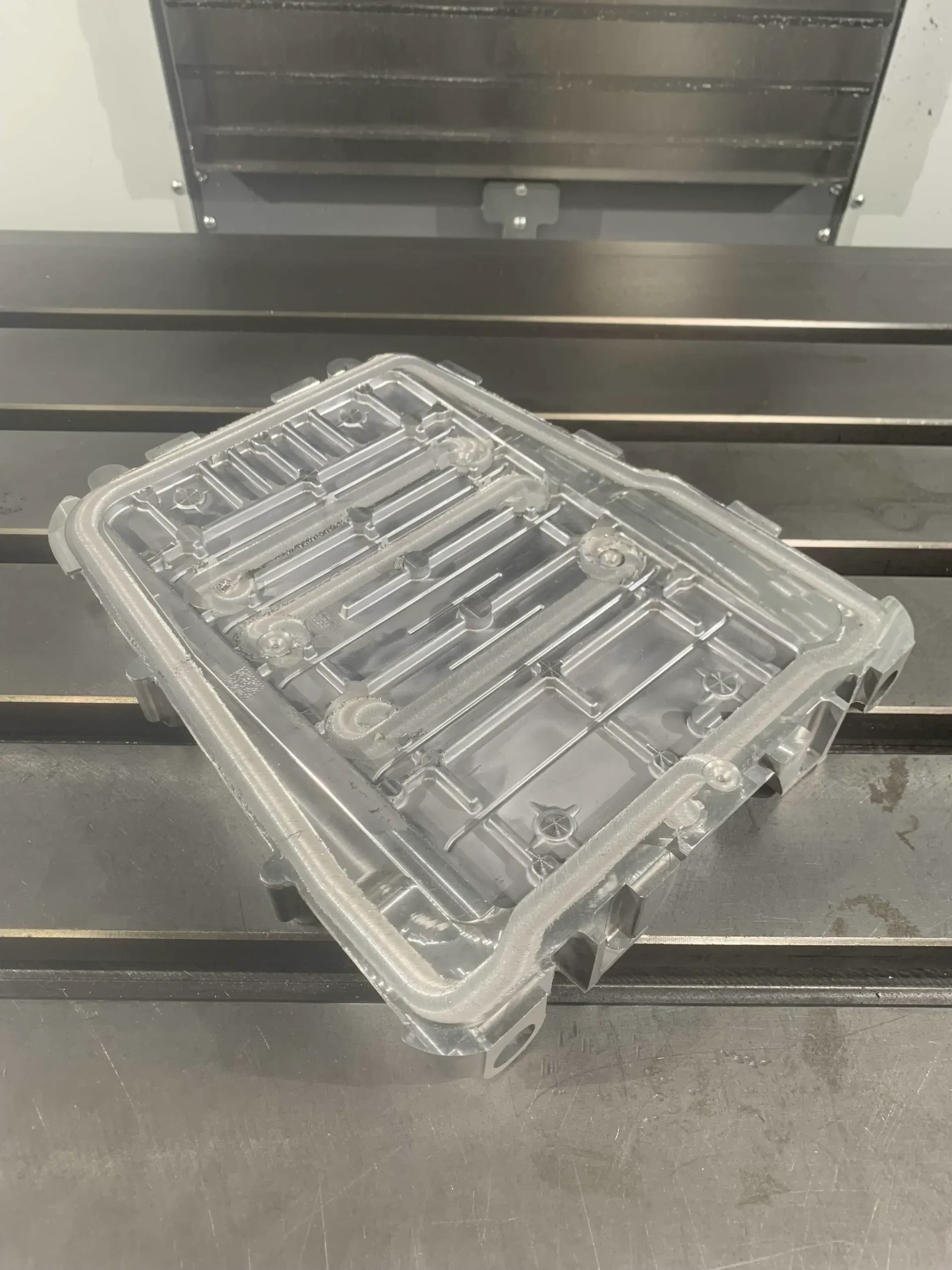
Heat sinks
Optimal performance and extended lifespan of high-performance systems.
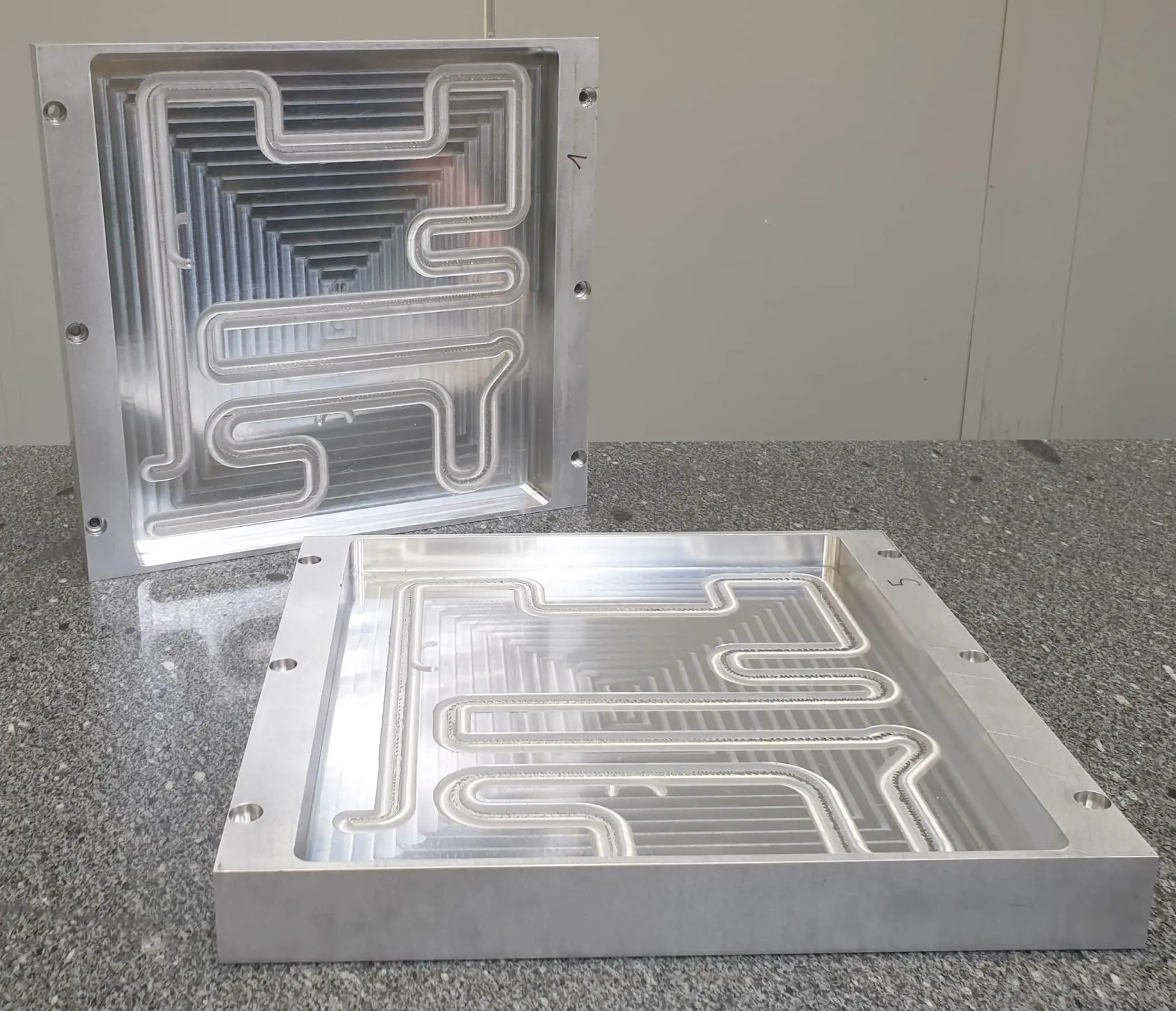
Cold plates
High quality thermal management devices thanks to Friction Stir Welding.

Stiffened panels
Aluminium panels enhanced for increased rigidity, extended length, and reduced weight.

Tanks
Leakproof, superior mechanical strength and and increased lifetime thanks to FSW.
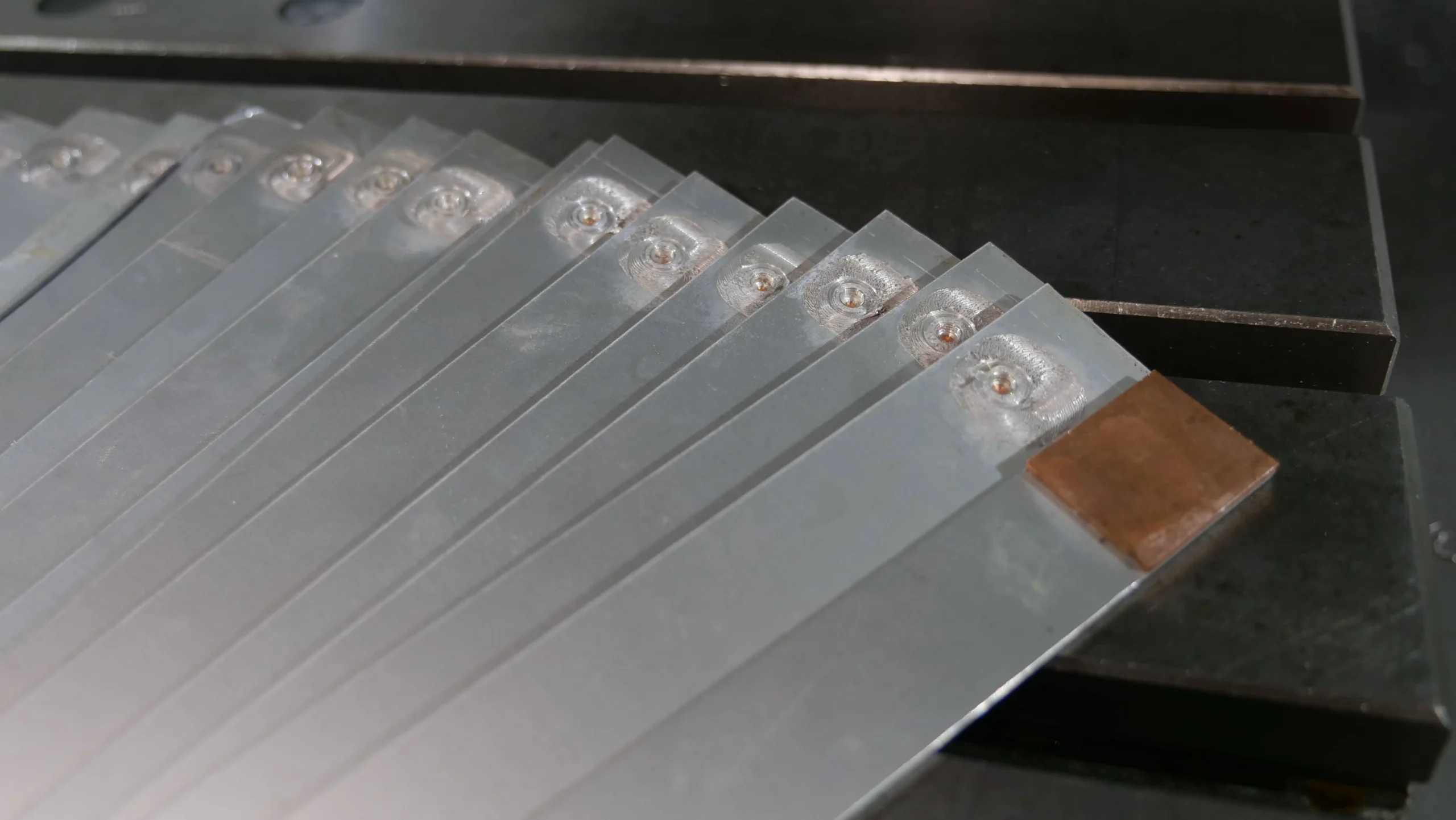
Bus bars
Highly conductive, seamless and durable, ideal for efficient power distribution.
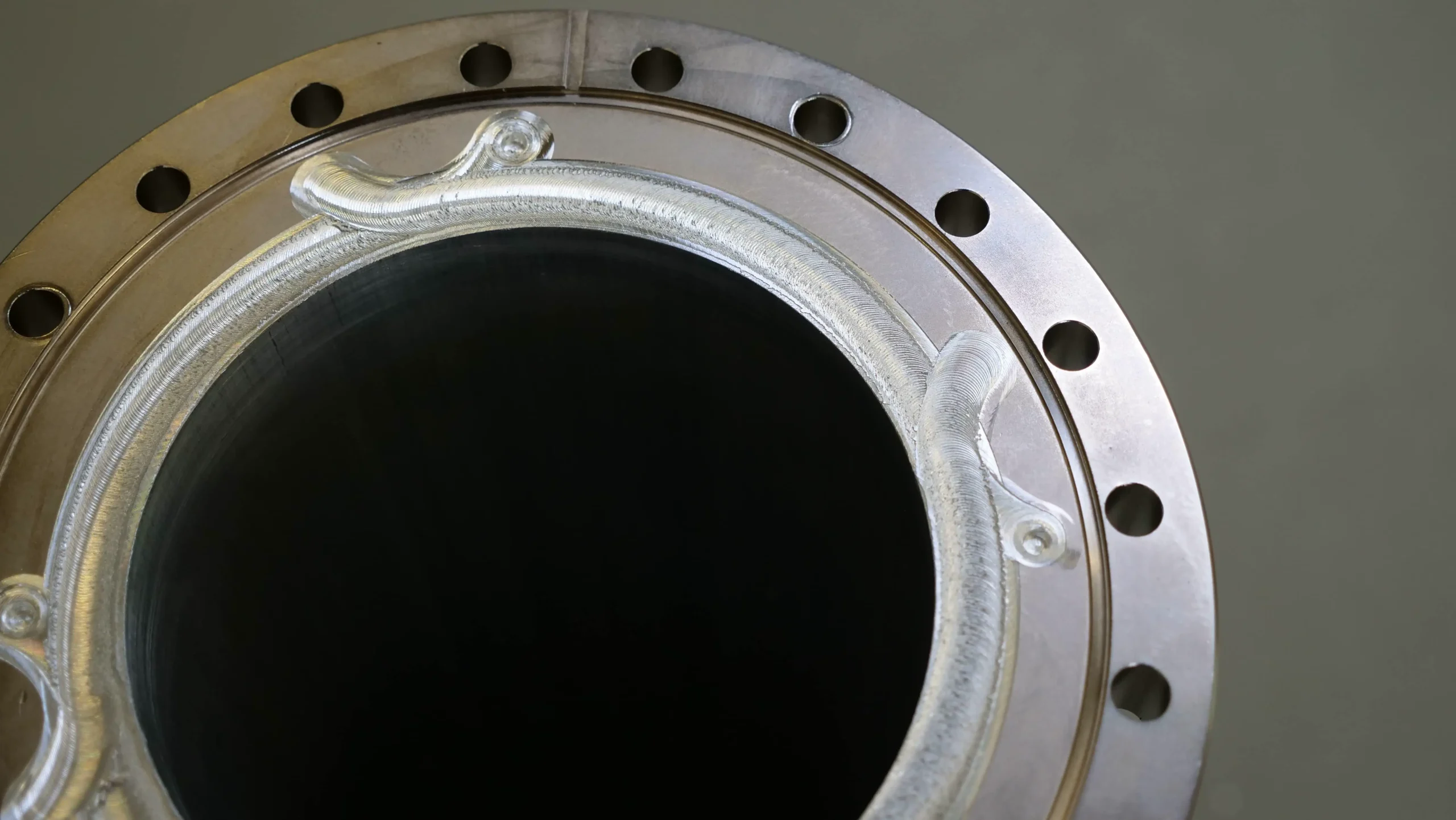
Flange builders
Lightweight, corrosion-resistant, with excellent thermal conductivity and strength.
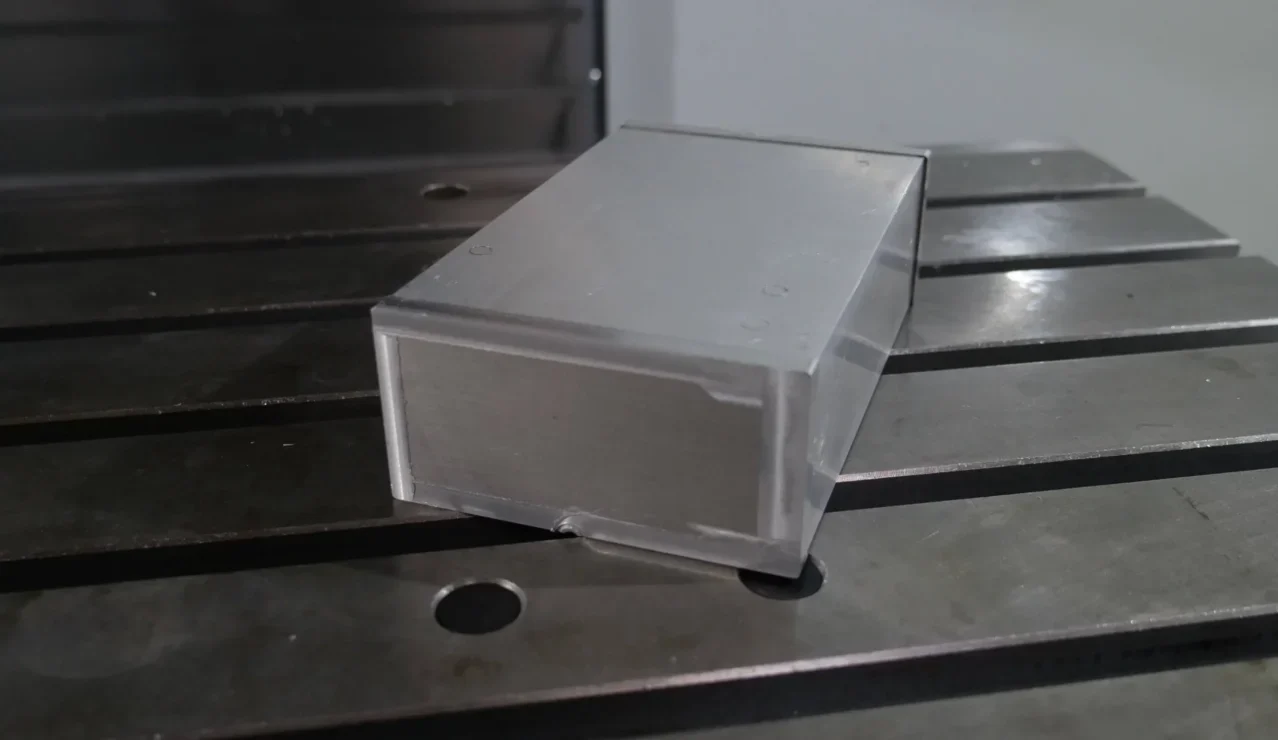
Vacuum chambers
Corrosion-resistant, lightweight and thermally conductive, ideal for vacuum applications.
Dive Deeper: Comprehensive Friction Stir Welding Resources
Interested in exploring Friction Stir Welding process further? We provide an array of resources tailored for you, such as informative webinars, articles and comprehensive whitepapers. Click below to discover a wealth of information we’ve curated just for you.
Webinar – 45 min – Replay on demand
Friction Stir Welding: all you need to know
Discover the intricacies of the innovative welding process. Dive deep into the Friction Stir Welding process, understand its workings, explore its advantages and limitations, identify applications best suited for FSW and learn ways to optimize your technological processes today. Join us for an insightful session.
Blog articles – 5 min
How much will it cost you to weld your part by FSW?
4 essential elements for high quality FSW
Practical guide – 20 min
5 essential steps to master Friction Stir Welding
Explore our expert guide on Friction Stir Welding. Gain insights into each stage, from initial planning to expert certification, to elevate your welding projects!
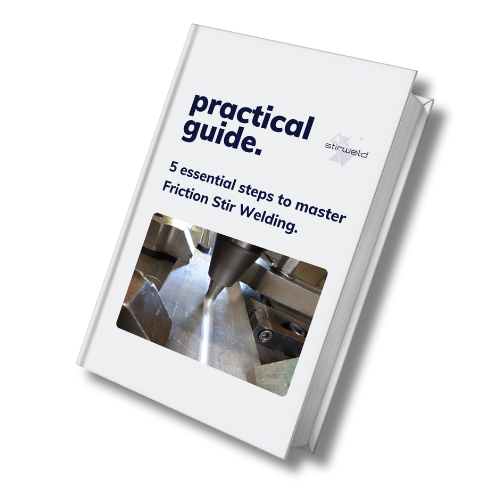
White paper – 20 min
Friction Stir Welding for dummies
This white paper simplifies the complexities of FSW, offering readers straightforward explanations and practical applications, ideal for quick and effective learning.
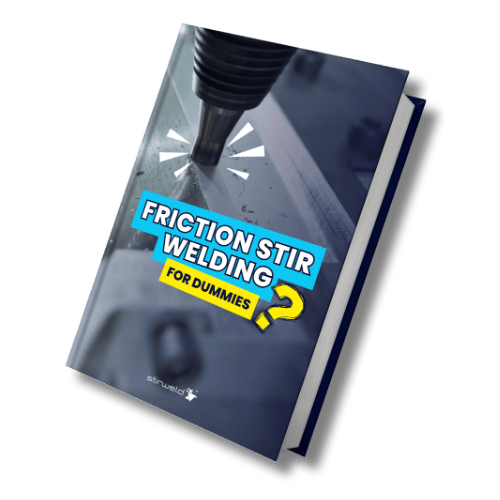
White paper – 20 min
11 rules for perfect compatibility with FSW
Discover 11 essential design rules for seamless Friction Stir Welding. Optimize quality, reduce costs and ensure durable assemblies with this free guide!
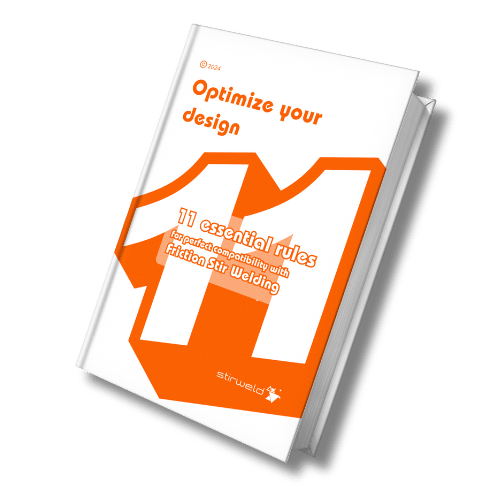
Catalogue – 20 min
Friction Stir Welding equipments
Access the catalogue of equipments for Friction Stir Welding and find out which of them are best suited to your project.
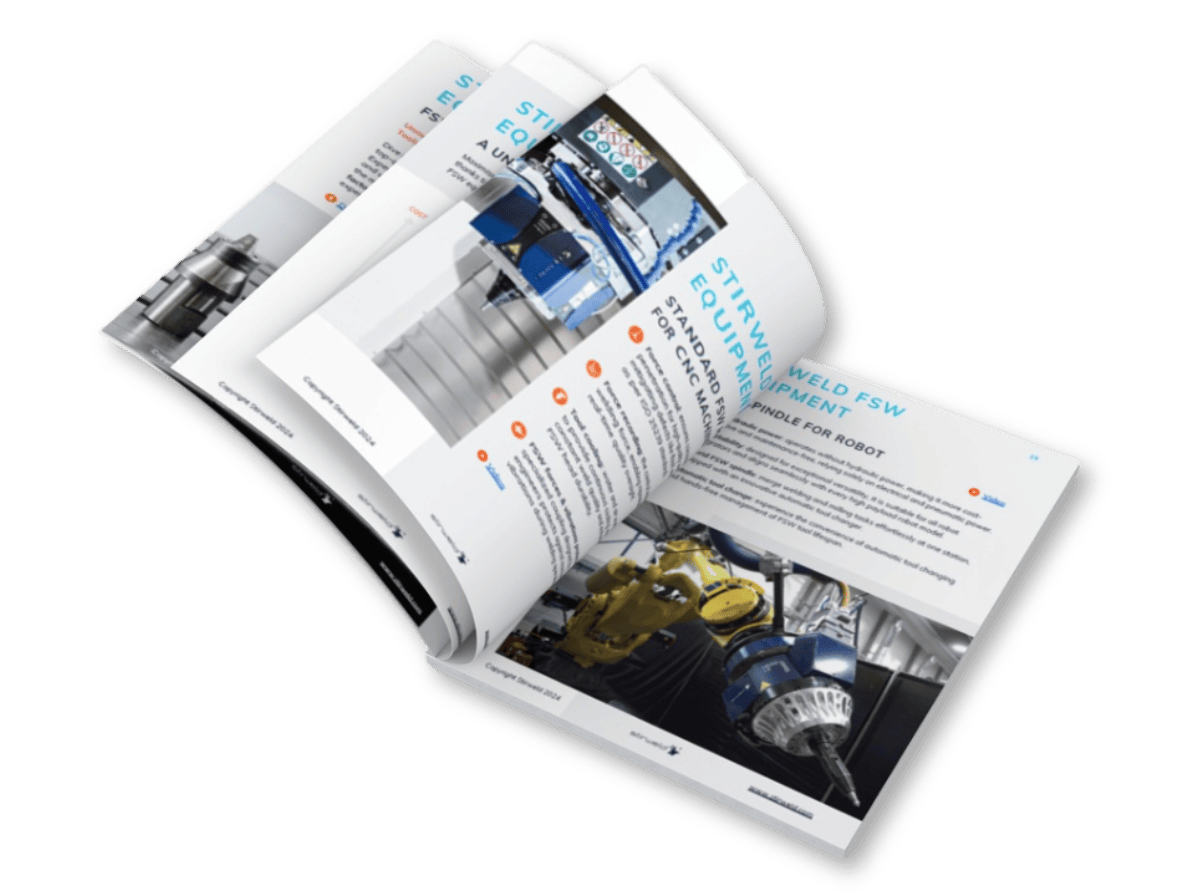
Unlock the Power of FSW with the Experts
Discover how our team can guide you through the nuances of Friction Stir Welding, ensuring optimal results for your projects.