Cold plate & FSW: the answer to the challenges of thermal management
Nowadays, many industries are looking for the most accurate if not perfect thermal management. This is the case in the aeronautics, space, military, wind and solar energy sectors and many others. Their solution for optimal thermal management: liquid cold plates. The challenge is to integrate these cold plates into their devices while reducing the overall weight. Our answer: chill aluminium plates welded by FSW.
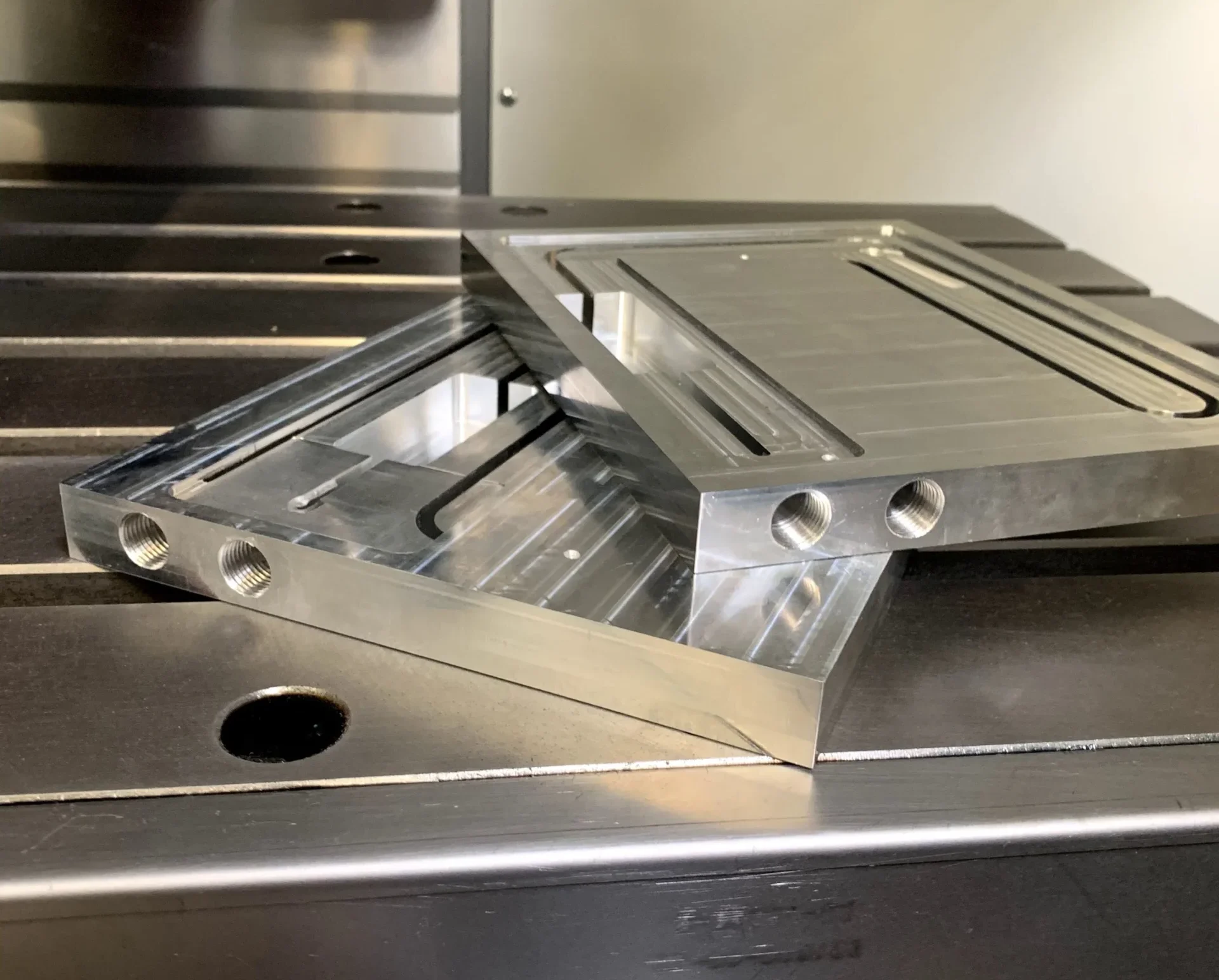
Which cold plates for which industries?
There are several families of cold plates:

Cold plate in aluminium foundry

Cold plate for e-mobility (die casting)
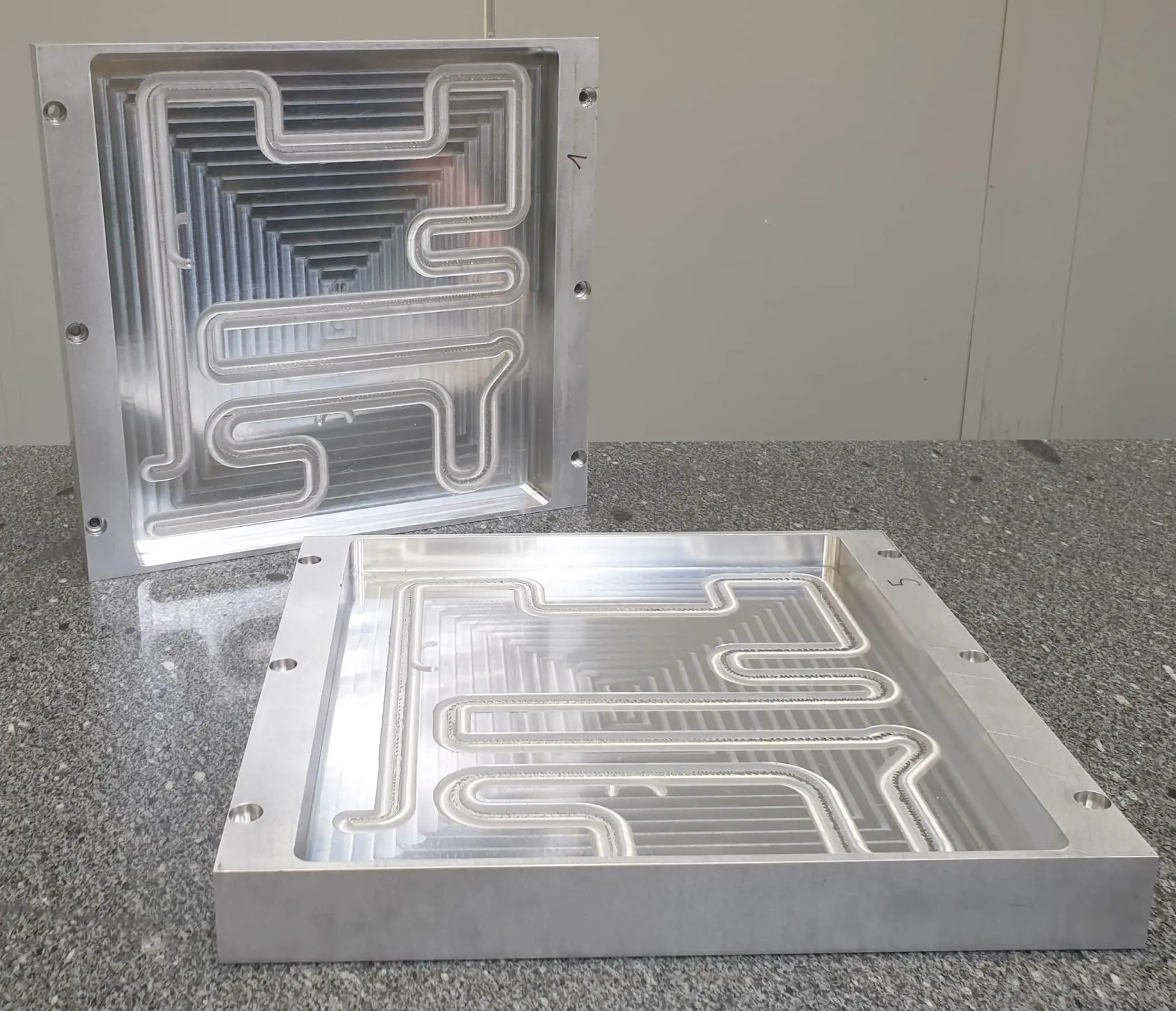
Liquid cold plate in aluminium
These cold plates do not have the same number of parts per batch. Indeed, cold plates dedicated to e-mobility are produced in larger series, whereas machined cold plates, dedicated to sectors such as aeronautics, defence or wind energy, are produced in smaller series, around 50 parts.
Chill plates are used in various industries. The main sectors are railways, wind and solar energy, space, aeronautics, data centres and the defence sector; sectors in which the issue of thermal management is essential.
Chill plates: The challenge of thermal management
In 90% of energy systems, cold plates are required for devices’ temperature management. Thermal management of equipment faces several challenges:
Let’s take the example of thermal management in aeronautics. In this sector, electronics cooling will represent the largest market size between 2021 and 2026 due to the increasing demand for automation (Source : Temisth).
The challenge: more electronics need to be housed in a smaller and tighter space.

In the aerospace and defence industry, chill plates are used to cool embedded (weightless and compact) systems such as radars or control and power electronics. These liquid cold plates are very specific: they have a transient cycle, i.e. they are used both to cool and to heat the parts.
The challenge: low volume production due to the very restrictive market type, which is subject to national regulations.

Thus, the market of liquid cold plates has been growing rapidly for the last decade, especially in the field of power electronics, laser, medical equipment and automotive as shown in the graph below.
In 2020, the number of chill plates welded by FSW was 250,000 units, or 13% of the market.

Source : Temisth
Why use aluminium for chill plates?
For an efficient liquid cold plate, the material used must be thermally conductive and as light as possible. In addition, once assembled, the cold plate must be 100% waterproof. The material that meets these requirements is aluminium. It has very good mechanical properties:
However, there is one issue: the weldability of aluminium. As a material with excellent thermal conductivity, the welding process can be complex with conventional fusion welding techniques. So let’s take a look at how to weld your aluminium cold plate using a new process: friction stir welding.

How to weld a liquid cold plate?
As mentioned above, aluminium is a material with low density, good corrosion resistance and high thermal and electrical conductivity. However, due to its specific properties, welding aluminium can be more complicated. Due to its high thermal conductivity, high welding energies are required. Other points to consider are the tendency of aluminium to deform during welding and possible defects (cracking, blowing, alteration of mechanical properties, material degradation).
There are several options for welding aluminium cold plate: vacuum brazing, electron beam welding or friction stir welding. To understand the best process for welding liquid cold plates we need to take into account the operating cost – investment cost and cost of the cover – as well as the cost of quality control.
Operating cost of liquid cold plate manufacturing
The operating cost therefore includes the investment cost in terms of the machine and the cost of the cover. These costs vary according to the welding technique used:
Machine cost | Cover cost | |
Vacuum Brazing | Vacuum furnace: € 1 million | Laser-cut cover: 5 € per part |
Laser Welding | LBW machine: € 1 million | Machined cover: 100 € per part |
FSW | FSW head for CNC machine: 98 000 € | Laser-cut cover: 5 € per part |
The difference in the cost of the cover between vacuum brazing and FSW and LBW welding is due to the fact that in LBW the design of the cover has to be extremely precise, which leads to additional costs.
Cost of quality control of liquid cold plate manufacturing
As the operating cost, the cost of quality control will depend on the assembly technique used:
Control of new part | Risk in service | |
Vacuum Brazing | X-ray for sticking or collapse of the brazing joint into the water channel | Brazing failure due to no-detected intial sticking defect & fatigue stress du to cycle pressure |
Laser Beam Welding (LBW) | Need to machine and then liquid penetrant testing for porosities | Leak due to no-detected porosity (liquid penetrant can only detect through porosities) & crack propagation due to cycle pressure |
FSW | No risk of sticking Solid state welding process: no porosity | None |
After this analysis of the different joining techniques – vacuum brazing, LBW, FSW – we can see that FSW has a real advantage in terms of both operating cost and quality control cost. But FSW is not only cost effective. We will see that it also has many other advantages, particularly in terms of the quality and mechanical performance of the part.
Looking for a solution to weld your liquid aluminium cold plates?
Here is the recommended welding technique: Friction Stir Welding. Welding a liquid cold plate by FSW has several advantages:
In order for the welding to be effective and efficient, several points must be taken into account:
Four parameters must be taken into account when welding a cold plate machined by FSW:
If you want to know everything about FSW welding parameters, please read our article “4 essential elements for a very high quality FSW weld“.

Final step: qualification of your FSW weld
Once your liquid cold plate has been welded, it is essential to qualify it. The standard to follow is ISO 25239.
First quality control: the visual test. This will allow us to check that there is no porosity on the surface or through the exit hole, that there is little or no flash and that the shoulder of the tool has pressed well on the surface.
Second quality control: the metallographic cut. This will allow us to check in depth that there is no porosity and to confirm that the tool shoulder has pressed against the surface of the machined cold plate.
Third quality control: the bend test. If the weld is faulty, the cover of the cold plate will break in a fragile manner. On the other hand, if the weld has been done correctly, the cover will be plastically deformed up to 90°.
The fourth and final quality control is the leak test. This test is essential for a machined cold plate, as a leaky cold plate is unthinkable.
Friction stir welding is the solution for joining your liquid cold plates: 100% waterproof, excellent thermal conductivity and a low cost process. To help you go further in your process, our FSW experts will support you. Mechanical calculations, material fatigue resistance, recommendations on the thickness and width of the cover, on the tool to be used… Nothing resists them, so do not hesitate to contact us, we will be there to answer your questions.
Want to know more?
Get our white paper on liquid cold plates welded by FSW.