Friction Stir Welding x Rheocasting
Unveiling the synergy of advanced manufacturing techniques.

In recent years, industry has undergone a deep transformation. Indeed, with the massive arrival of new technologies, industry standards are being shaken up. Environmental pressures and global warming are largely the causes.
As a consequence, it is necessary to adapt production processes and innovate by finding new processes that are just as efficient but reduce environmental costs. Today. we will take a closer look at two of these new technologies: friction stir welding and rheocasting.
What these two technologies have in common is that they work the metal in a specific state. Indeed, unlike conventional casting, rheocasting uses the metal in a pasty state. Similarly, unlike conventional soldering processes, FSW does not reach the melting point of the material and therefore welds the metal in its pasty state.
Rheocasting: what is this technology
Rheocasting is a process that originated in the 1970s. It came as a response to the problems faced with high pressure die casting, which was no longer able to meet the demands of designers. In fact, the casting world is evolving at a very fast pace with ever-increasing customer demand and requirements. Thus, the casting industry must rely on its latest innovations to bounce back. Given the increasing use of aluminium, rheocasting is one of the technologies to be acquired.
In which sectors is rheocasting used?
Rheocasting is a new process for producing aluminium parts. Nowadays it is a material used more and more because of its lightness, its affordable price and its perfect thermal conductivity. This is why some industries have turned to it to improve the technical characteristics of their parts.
Thus, rheocasting can be found in the telecom sector where thermal conductivity is very important, in the truck sector where the aim is to make vehicles lighter, and in the automotive sector where waterproof and other characteristics (lightness, lower CO2 emissions, development of the electric car, etc.) are paramount.
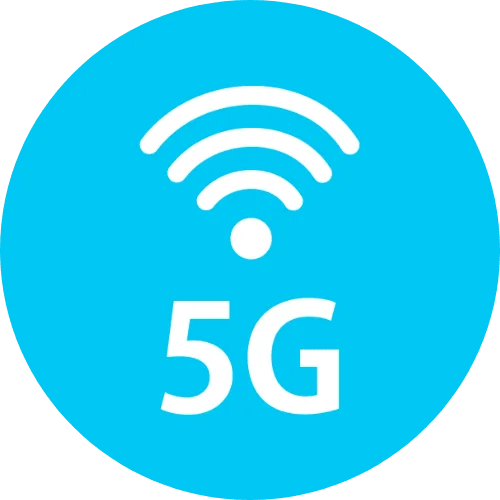
Telecommunication
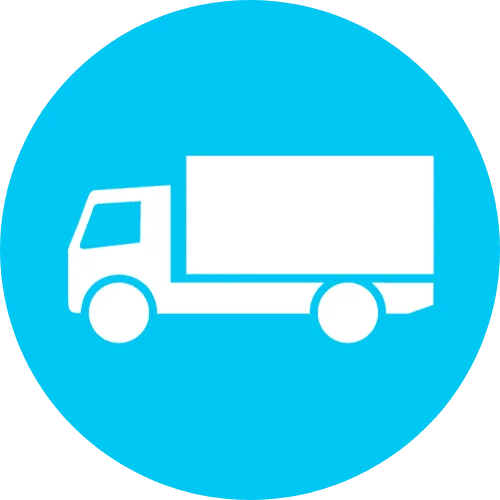
Truck
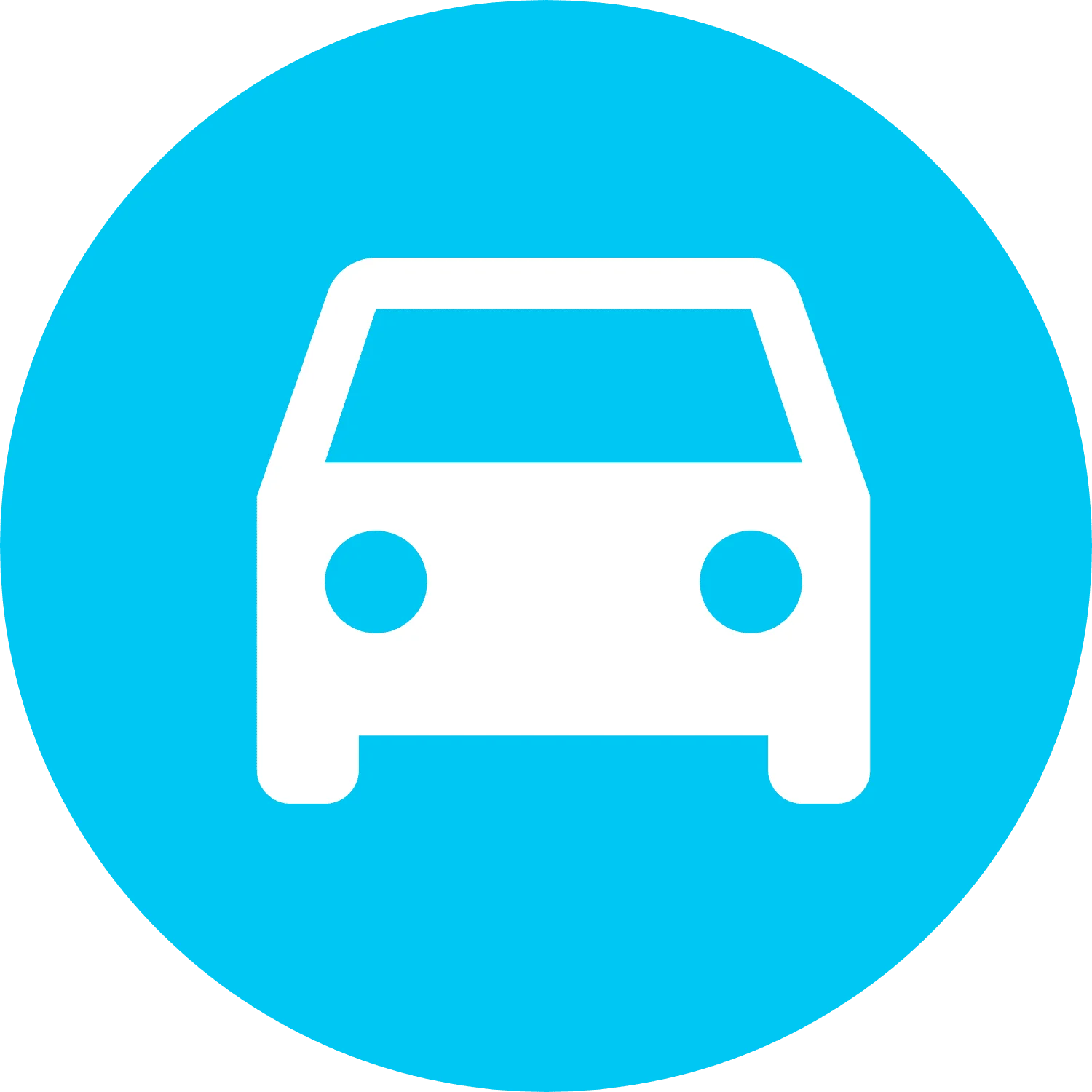
Automotive
What are the benefits of rheocasting?
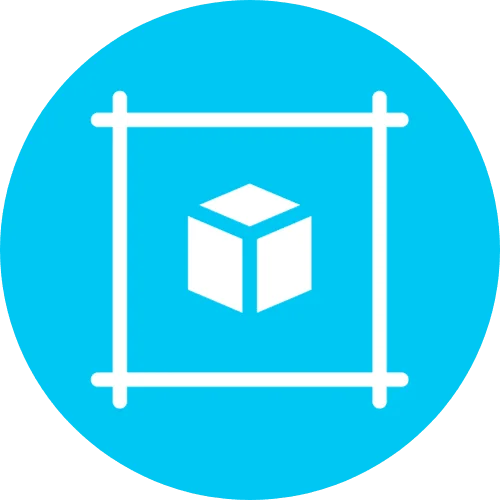
Design of highly complex parts in all possible forms.
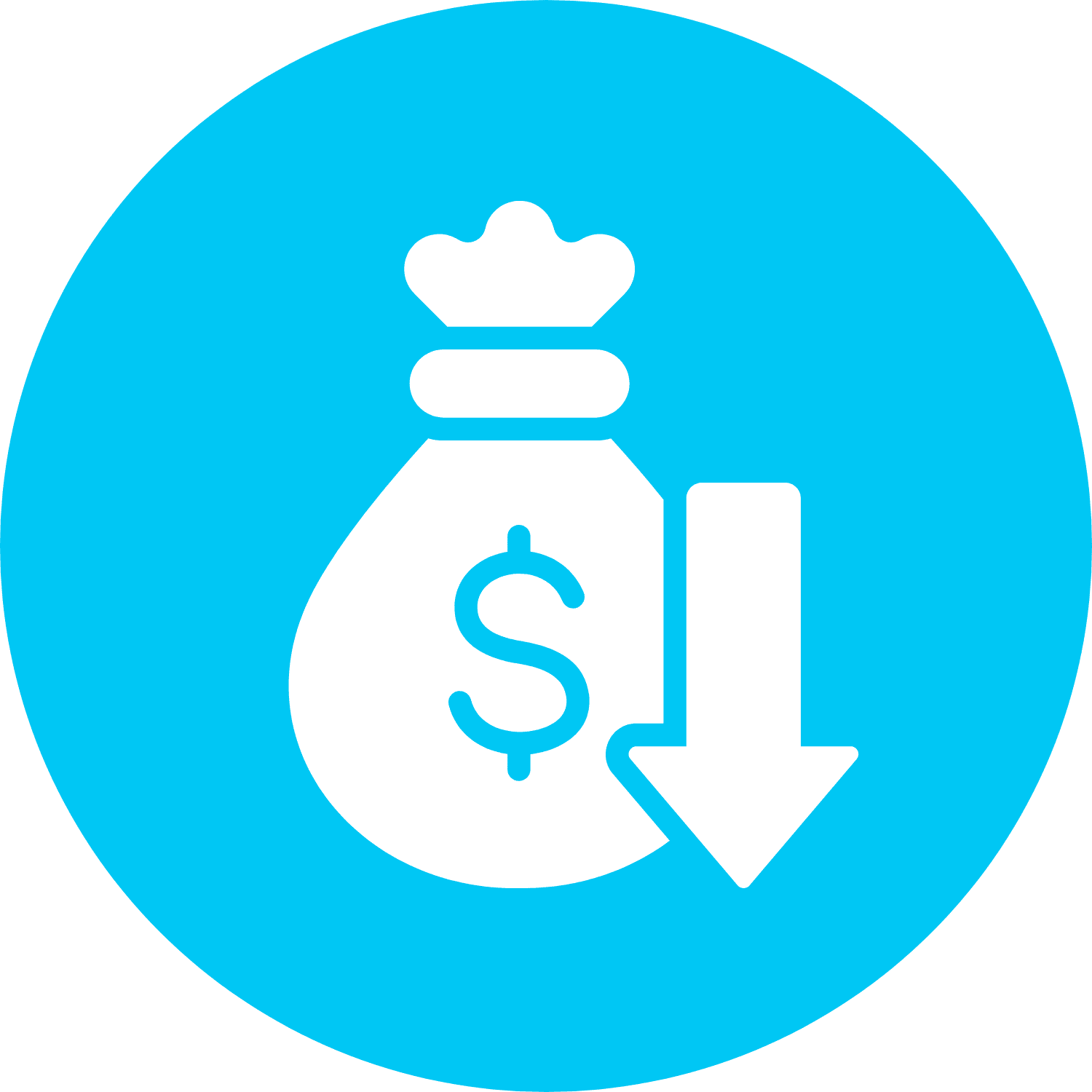
The mechanical post-treatment stage is no longer necessary, which reduces costs and therefore makes production as profitable as possible.

Aluminium is lighter than steel and offers similar mechanical resistance properties.

Easily weldable parts.
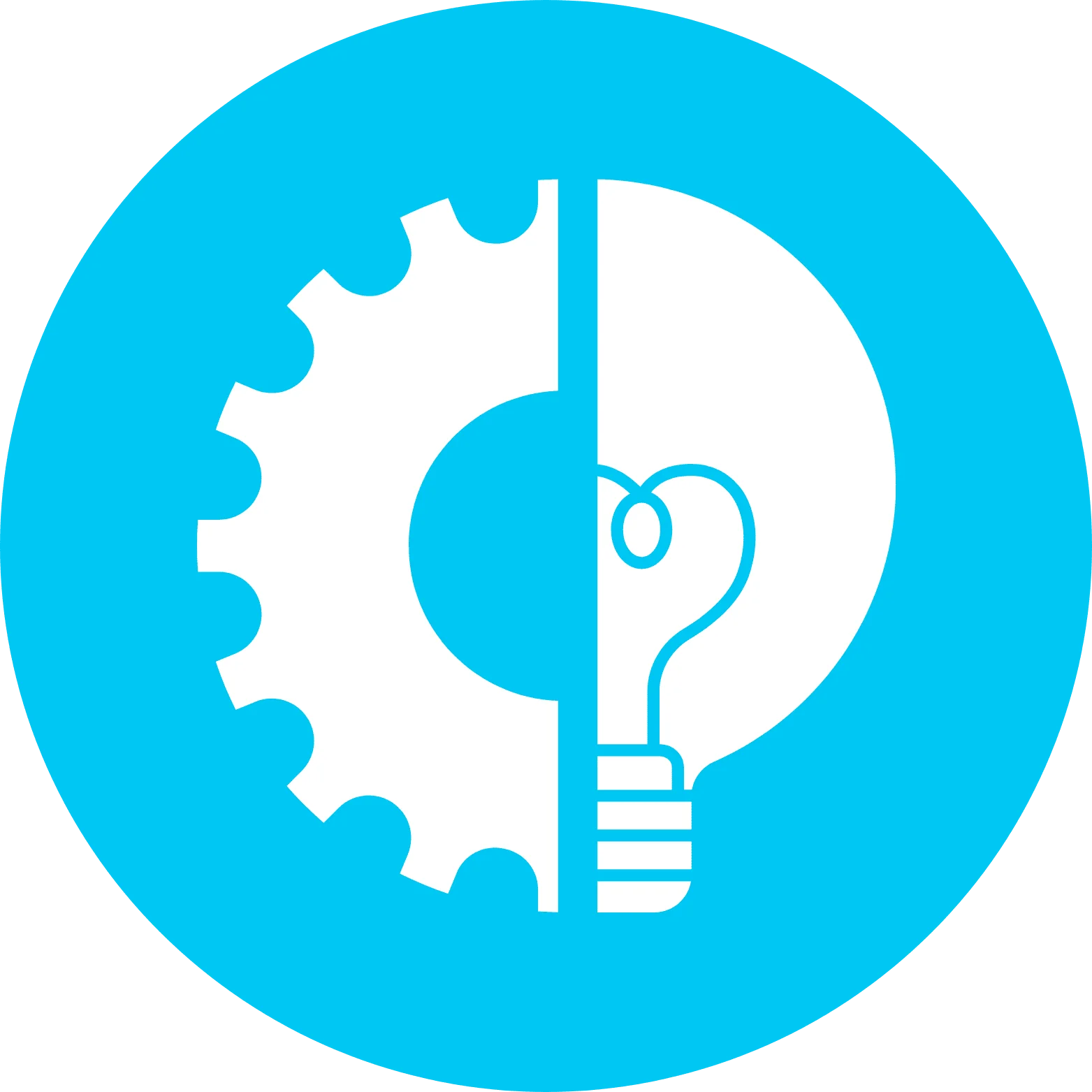
Wider range of secondary and primary alloys that can be cast.

Very low porosity levels: no leakage with high resistance.
What does rheocasting consist in?
Rheocasting is a special casting process in which aluminium, in its liquid state, is cooled and stirred until it reaches a semi-solid state. Rheocasting is based on two main factors:

Rheocasting is a new process to work the material in a pasty state. As you have seen, working this way offers many advantages for every industry sector. Let’s now move on to another technique that uses unconventional state for manufacturing: the friction stir welding technology.
FSW: the new and green welding technology
Friction stir welding, also known as FSW, is one of the most advanced trends in welding technology. It is a weld carried out in a pasty state, the so-called solid state of the joining process. The weld is created solely by mechanical friction deformation. Several technological parameters have to be taken into account:
In which sectors is FSW used?
The parts welded by FSW have a high mechanical strength with a static reduction of about 10-20% and a fatigue strength close to the base material. With no leakage (water, acid, or air), this process is used in many industries:

E-mobility
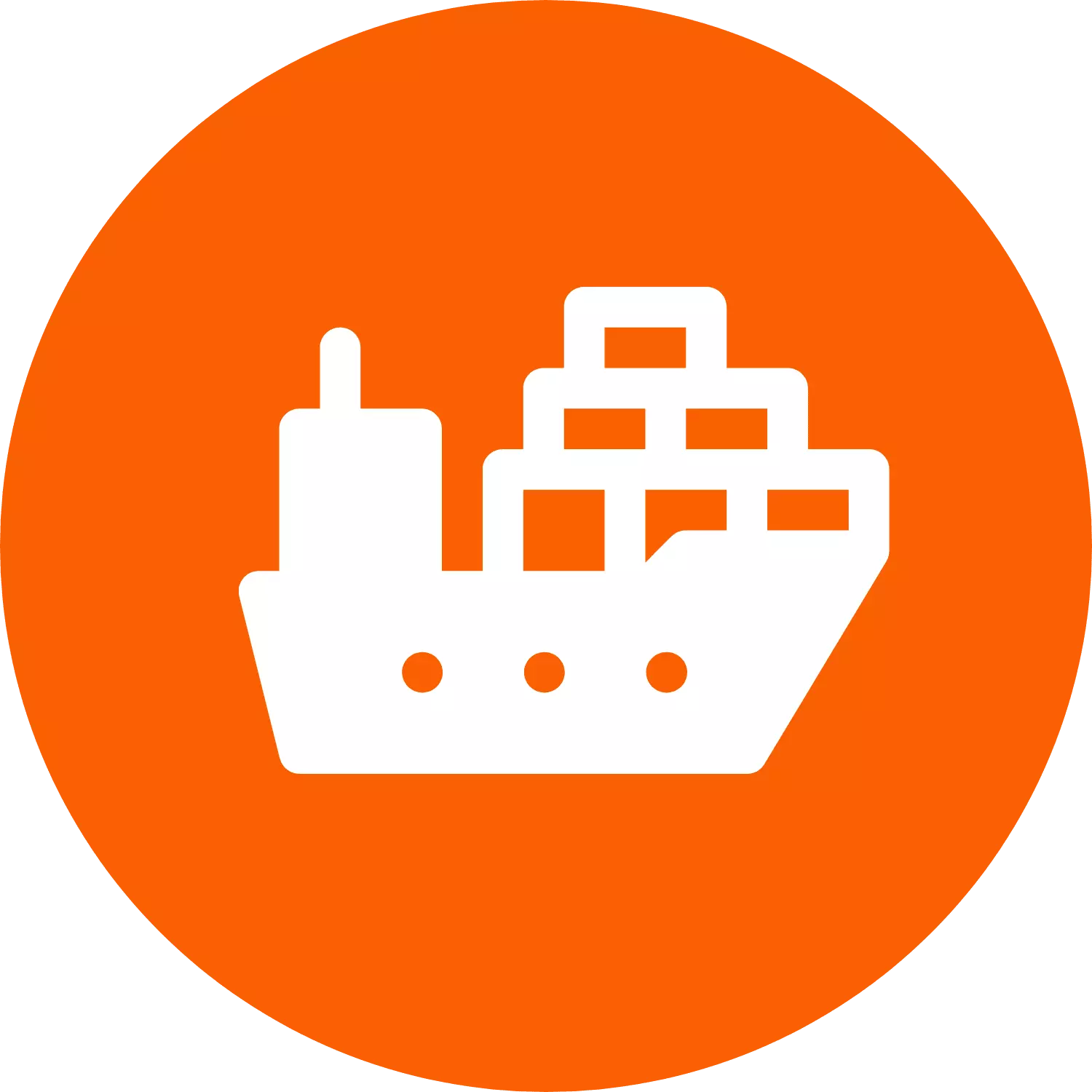
Shipbuilding
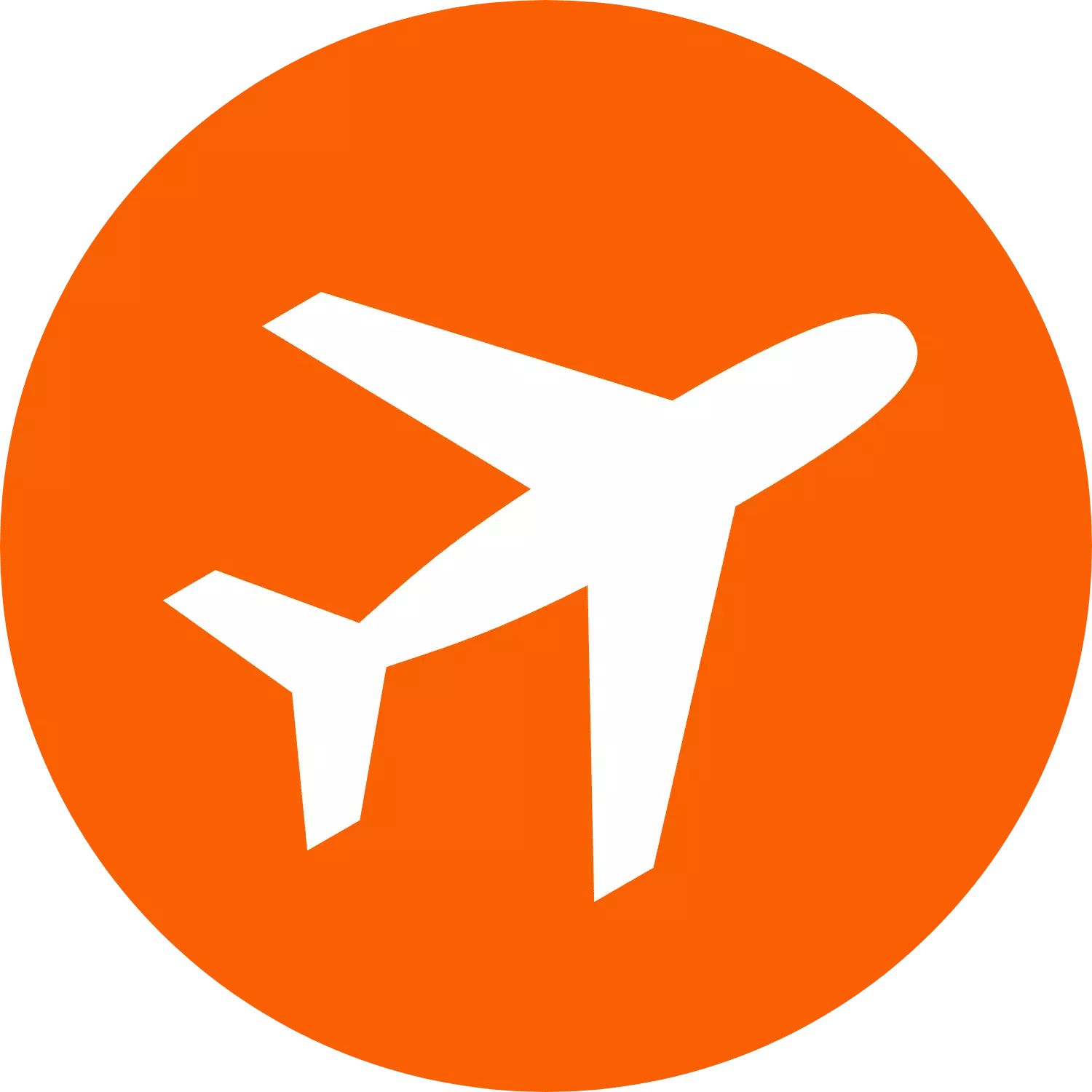
Aeronautics

Aerospace
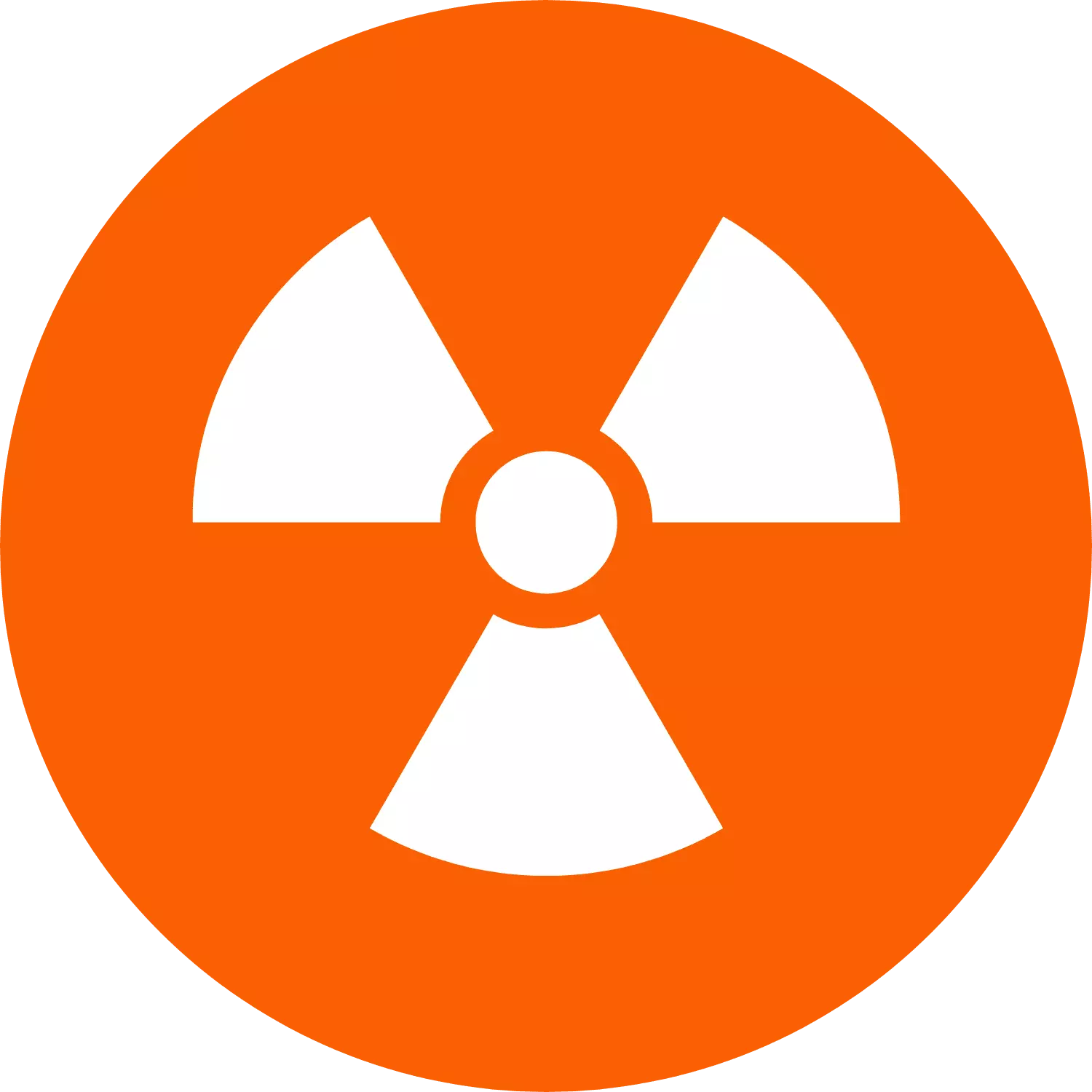
Nuclear
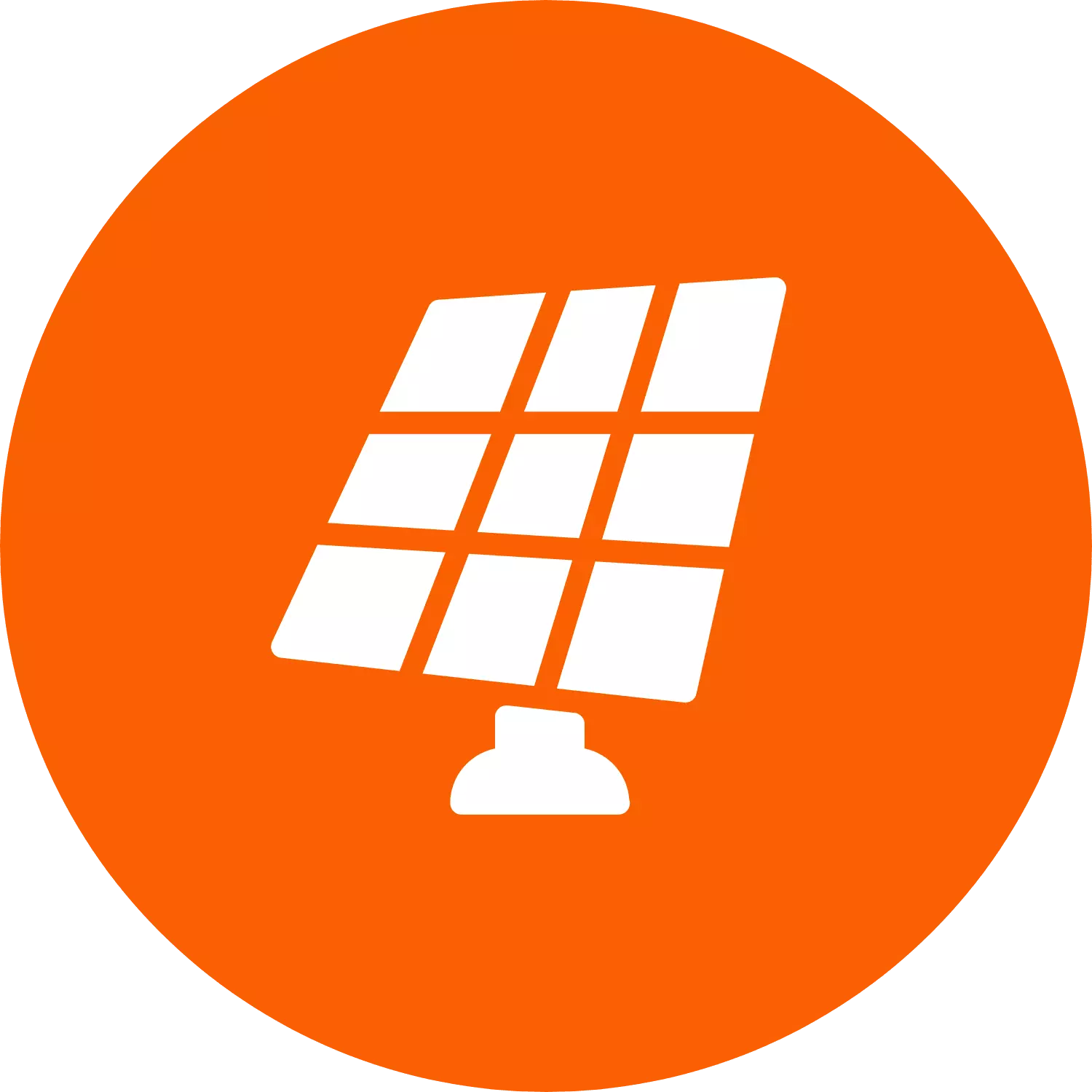
Solar panel
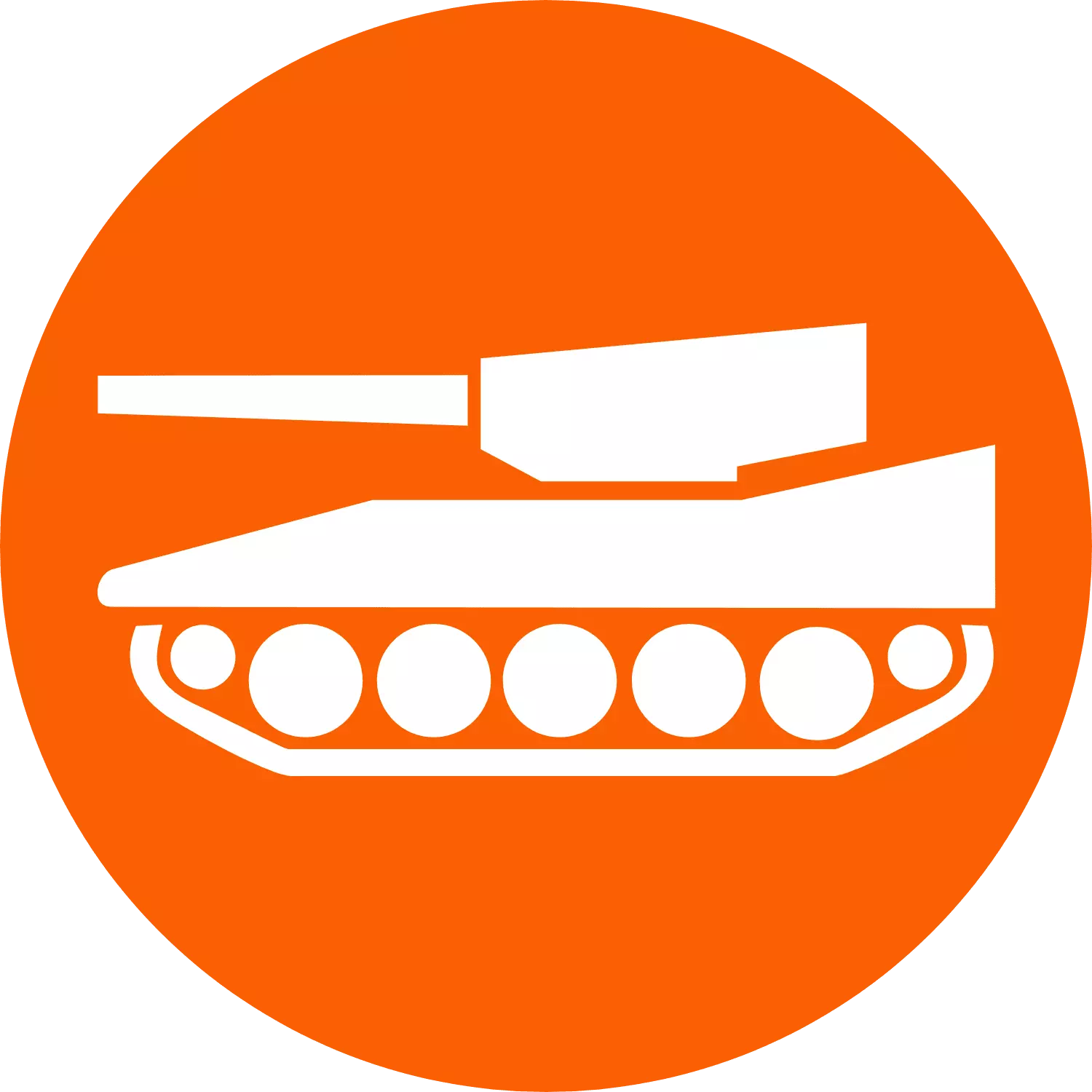
Military
What are the advantages of FSW?
Friction Stir Welding is a mature technology for the assembly of aluminium but also copper. This process makes it possible to maintain mechanical properties close to those of the base material.
Now, with FSW we can weld high-strength aluminium alloys (2000, 6000 and 7000 series), something that could not be done before. Welding of dissimilar materials has also become possible with FSW. Thus, aluminium and copper, aluminium foundries and aluminium and steel can be easily welded.
The table below illustrates the mechanical reductions according to the type of welding and shows the improvements related to the use of friction stir welding as far as joint efficiency is concerned.
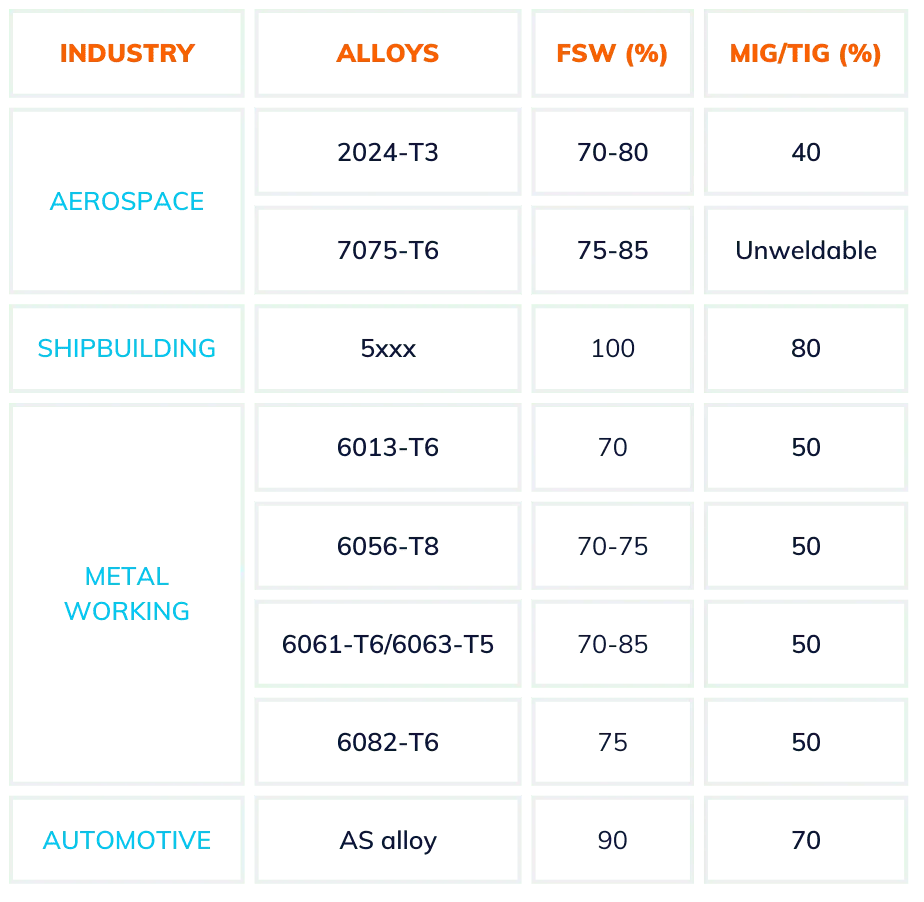
We were talking about environmental protection and taking into account the impact of industry on the environment. With the FSW, there is no surface preparation, no grinding or cleaning is required. No spar, no smoke, no noise. It is a “green” process.
Finally, the main advantage of the Friction Stir Welding is that it is a “cold” welding, more exactly in a pasty state, therefore without melting and without any addition of material.
How does Friction Stir Welding work?
The Welding Institute (TWI), invented friction stir welding in 1991. Once the TWI patent fell into the public domain at the beginning of 2015, great development prospects opened for FSW technology.
In the infographic below, follow the process of friction stir welding in its different steps:

As you have understood, FSW is a revolutionary process in the world of welding. Working the material in a pasty state is a great evolution in the industry.
Imagine now how mixing rheocasting and FSW will help you improving your parts!
Rheocasting & FSW: the best of two worlds
In the casting world, many innovations have emerged, including rheocasting and Friction Stir Welding: one has revolutionized the world of welding and the other has solved casting problems related to HPDC.
As a result, tests were carried out to find out whether rheocasting parts could be welded by friction stir welding. One of the main characteristics of rheocasting parts is that they are easily weldable.
In addition, rheocasting parts are extremely thermally conductive and once welded by FSW they remain so.
Another advantage of combining these two technologies is the ability to perform complex parts. Indeed, with rheocasting it is possible to make all imaginable shapes. With friction stir welding it is then possible to weld these complex parts. The FSW technology allows the welding of several complex non-castable components into a single part.
An additional benefit of combining rheocasting and FSW is the possibility to make large parts. Indeed, in rheocasting, the size of the parts is limited. Therefore, with Friction Stir Welding, it is possible to assemble several parts of the rheocasting part to make one large part. An example of this is shown below:

FSW of two rheocasted part: zoom on the weld
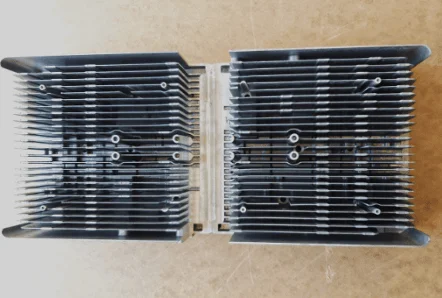
FSW of two rheocasted part
Why combine FSW and Rheocasting?
The combined use of FSW and rheocasting is gradually emerging and should take place in the coming years. Indeed, with the awareness of the urgency in which we are on the environmental side, it will be necessary to change our production methods which are energy consuming and not renewable.
Thus, sectors such as automotive or telecommunications have to redesign their products. Yes, electric vehicles are better for the environment and yes, 5G will allow us to go faster and further, but under what conditions? With these new products, the demand for efficient heating and cooling systems is exploding. As a result, we had to find new techniques, more respectful of the environment. The rheocasting x FSW combo will address this niche.
Zoom on telecom industry: the 5G Boom
If we take the example of 5G, thousands or even millions of antennas will be installed all over the world. These antennas are to be cooled to guarantee battery life (maintenance of batteries, interiors, and residual heat from electric motors) to optimize the working area. In addition, 5G is a field where high thermal conductivity is essential as losses are high due to high radio frequencies. Thus, 5G antennas are in great demand for heat sinks to cool their batteries.
The design of these heat sinks is overly complex and therefore difficult to achieve with conventional techniques. Rheocasting appears to be the most suitable technological option to produce these parts.
However, the size of the heat sinks for the 5G is also a problem. Indeed, rheocasting is the solution for a perfect thermal conductivity. Nonetheless, this technique limits the design of the parts in terms of size. This is where the FSW comes in.
Friction Stir Welding helps solving this size problem since it allows to weld the different parts of the heat sink into a single one. Moreover, the FSW is the optimal technique for assembling the heat sinks of 5G antennas since the welded parts keep excellent mechanical properties close to those of the base material. Thus, rheocasting heat sinks welded by FSW have high thermal conductivity, high tightness and their production will be highly repeatable since it is automated.
Other sectors and not the least use Rheocasting
Today, all sectors of the industry are paying attention to their environmental impact. Changing its production methods, improving its production line, using one environmentally friendly material over another and innovating on its products are essential actions that all players in the industry will have to adopt.
Thus, rheocasting combined with FSW opens up ecologically efficient futures to several sectors such as the military, naval, space, aeronautics and especially automotive as seen previously.
Indeed, the European Union has put out the figures: greenhouse gas emissions from new passenger cars will have to be reduced to 37.5% by 2030 and to 31% for commercial vehicles. A huge challenge for the automotive industry.
The automotive industry will have to focus its efforts on protecting the environment by drastically reducing the average fuel consumption of all vehicles. This will be achieved by reducing the weight of the vehicle completely. Indeed, less weight means less greenhouse gas emissions. The materials used are constantly being challenged. Steel will gradually give way to aluminium.
This is where rheocasting and FSW will come into play, as these two technologies enable the production of parts that are perfectly thermally conductive and 100% waterproof.
As we have seen, rheocasting and friction stir welding are two techniques that work the material in a semi-solid state, a great advance for every industry sector. Moreover, these two techniques have the advantage of retaining practically all the technical properties of the base materials. The parts are therefore highly thermally conductive.
Thus, combining these two technologies means producing very high-performance parts with complex designs and sizes while having optimal mechanical properties.
Comptech x Stirweld
Comptech is an innovative Swedish company in the field of rheocasting. Its goal is to become the leader in rheocasting. With strong environmental values, Comptech seeks to be ever more effective in improving the functionality of its customers’ products.
Thus, a partnership has been established between Stirweld and Comptech to go ever further in innovation. The two companies therefore asked themselves the question: How would it look if we combined FSW and rheocasting?
From this partnership came out various conclusions seen throughout the article with prototypes and tests. The interest being to provoke the technology, to go to the end of their ideas and thus combine these two technologies was obvious: rheocasting and FSW are two very innovative techniques so joining them is a real breakthrough for the industry.
Visit the website of our partner Comptech : http://comptech.se/
Interested in finding out more?
Download the white paper about Friction Stir Welding and Rheocasting.