Liquid cold plate: FSW assembly for more performance and cost savings
The performance of vacuum brazing at a lower price than deep drilling!
With the development of Friction Stir Welding (FSW), new FSW liquid cold plate technologies are changing the manufacturing process. Reliability of conductivity, flexibility and cost are three of the main advantages of FSW liquid cold plate welding over alternative techniques.
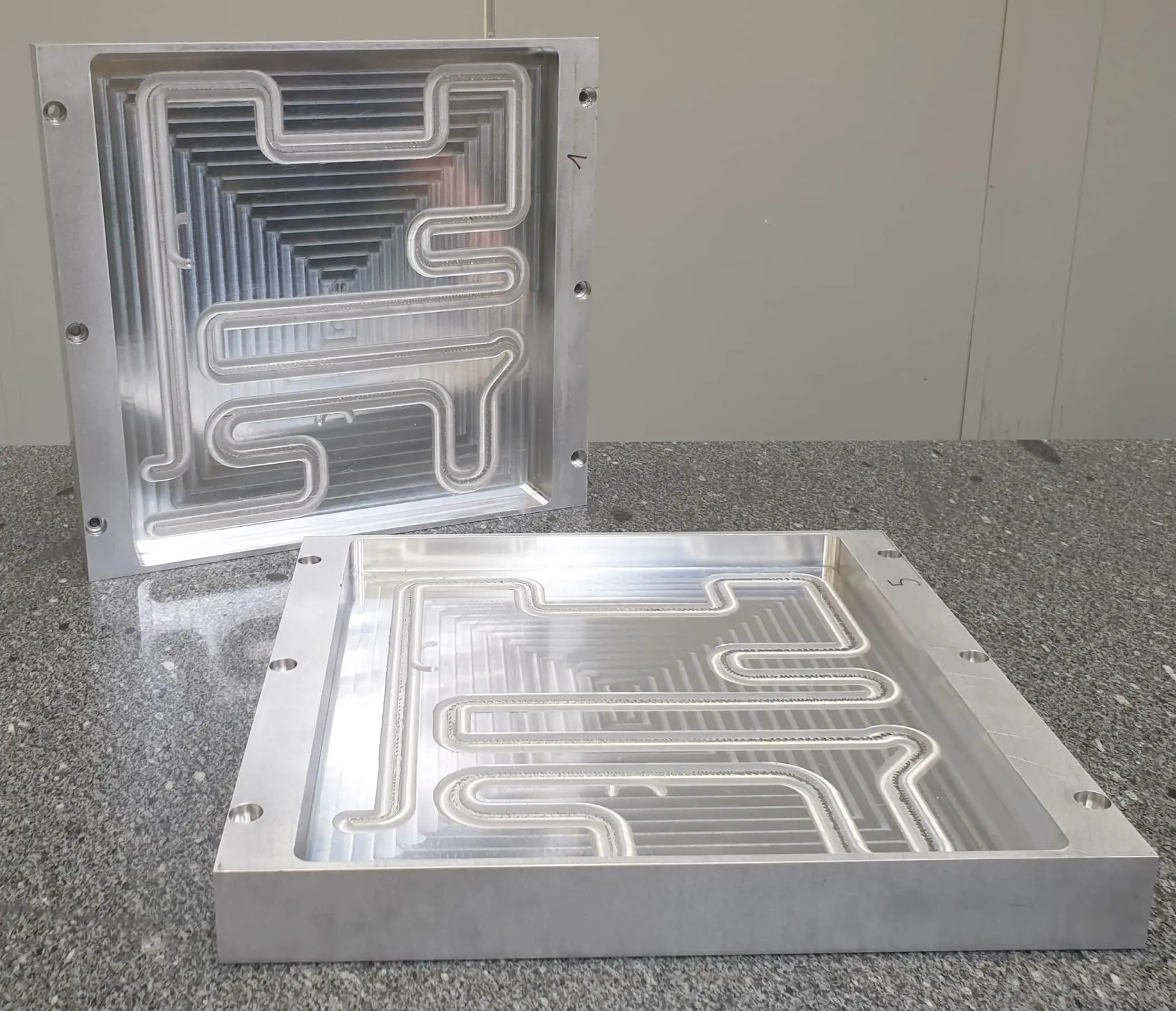
Heat dissipation by liquid cold plate: what does that mean?
Liquid cold plates are a heat dissipation device for electronic equipment cooling. This equipment allows the heat generated by high power electronic equipment to be dissipated to the surface of the cold plate via several fluid channels. The dissipation is achieved by conduction between the coolant in the channels and the cold plate.
Aluminium liquid cold plates contribute to the efficient design of new devices with high power electronics. One reason for this: the use of increasingly powerful electronic components in ever more compact housings. These compact packages force designers to think of new and efficient cooling devices.
The technical performance of these components is positively impacted by liquid cold plates which provide better cooling performance to high heat flux applications compared to more traditional cooling systems such as convective air cooling.
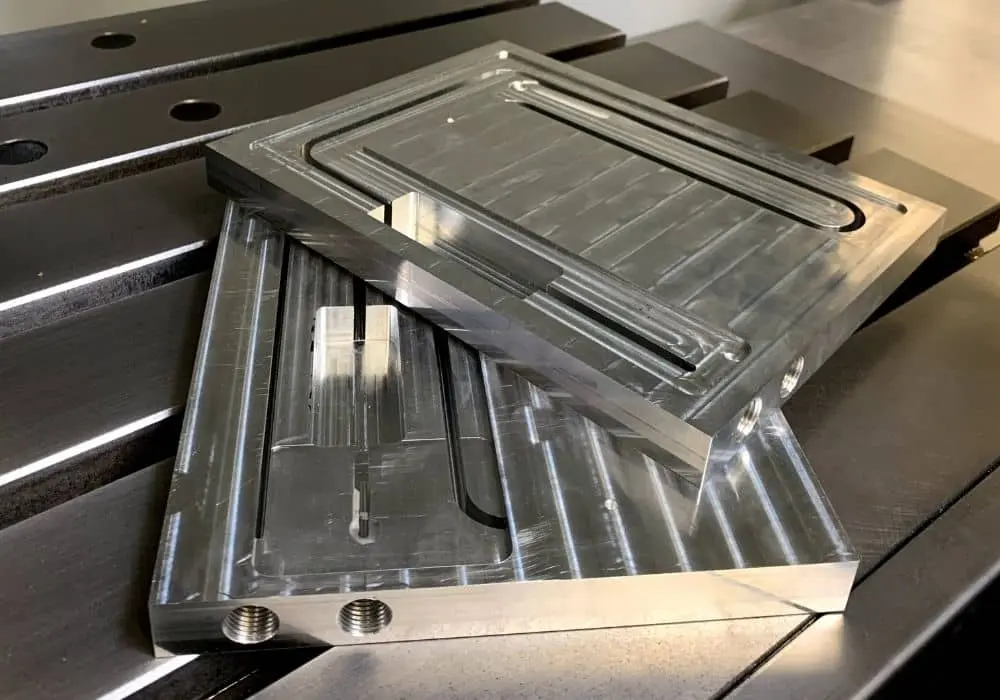
Which applications for liquid cold plates ?
There are many areas where perfect heat flow management is required. Here are the areas in which liquid cold plates are used:
What are the different types of liquid cold plates?
There are different types of liquid cold plates, namely:
Liquid cold plate: presentation and comparison of manufacturing methods
Tube liquid cold plate
This is perhaps the simplest form of liquid cold plate that exists today. It consists of a liquid cold plate with a seamless tube embedded in it.
Depending on the desired heat flow and coolant to be passed through the application, the tubes can be made of different materials, but most commonly the tubes are of copper. These are inserted in two ways; either mechanically (dry) or with a thermal epoxy seal to eliminate microporosities and maximise thermal performance.
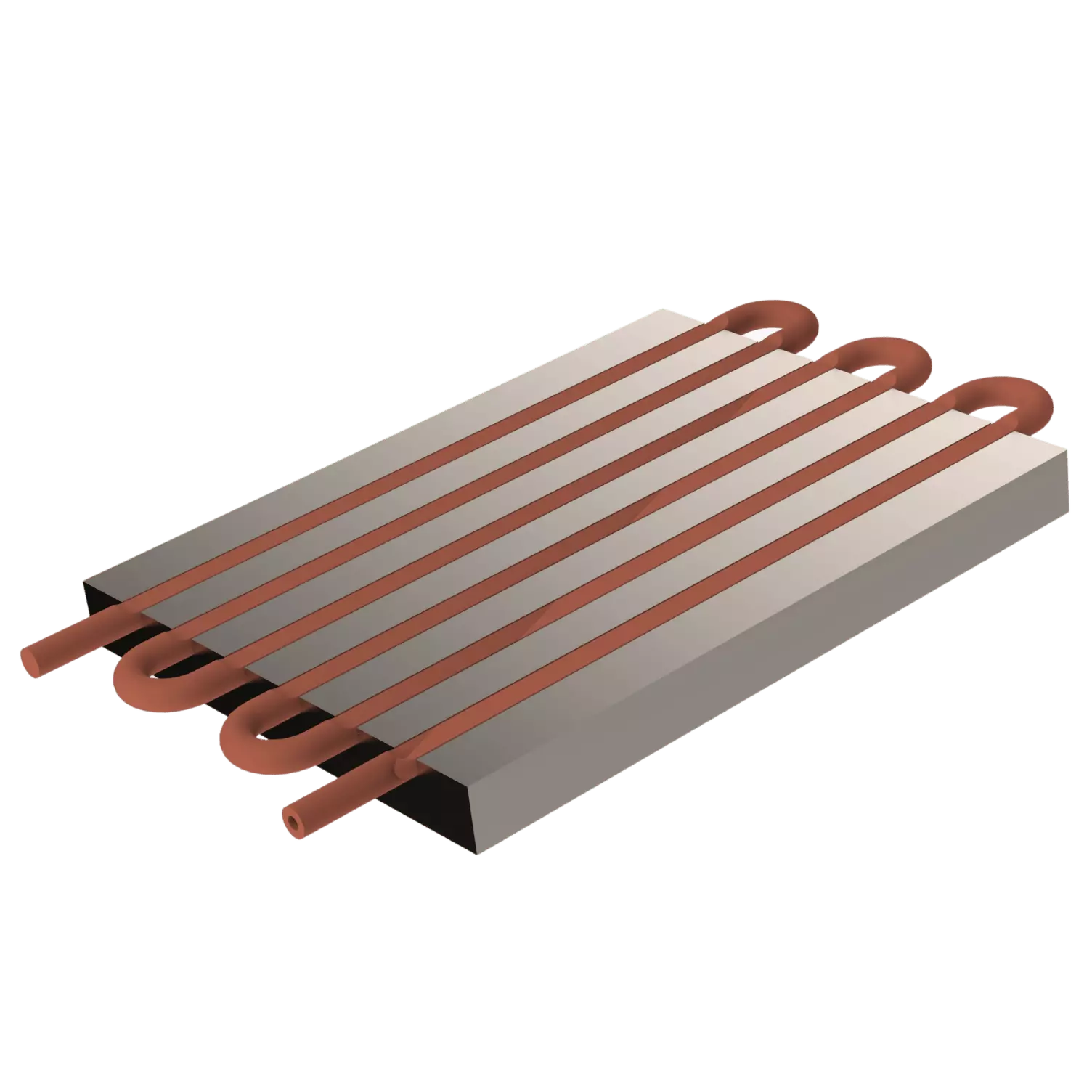
The disadvantages of the liquid cold plate with tube
The limitations of this configuration are the cooling performance (it is not possible to have a high channel density with this method) and the reliability of the tube conductivity due to the critical manufacturing steps, namely :
- Bending required to take the shape required in the plate
- Operation to ensure good thermal conductivity:
– Either application of a thermal paste which represents a significant cost,
– Or hydroforming to deform the tube in its housing but it is not possible to control whether a gap between the tube and the plate is still present.
Since 2020, the cost of copper has increased by a factor of 5, which is also an obstacle to the use of this liquid cold plate solution.
Gun drilling liquid cold plate
The liquid cold plate by gun drilling are designed with a series of deep holes along the length of the aluminium plate to create different flow channels. Each hole is drilled perpendicularly to the main coolant path and then partially plugged to create a continuous liquid path across the plate. Then taps are used to return the fluid to the plate.
The advantage of this liquid cold plate process is that there is no thermal barrier between the cooling medium and the aluminium plate. In addition, the aluminium plate is manufactured without thermal stress, making it easier to achieve its final flatness.

The disadvantages of liquid cold plate by deep drilling
- Deep-drilled liquid cold plates do not allow much design freedom in terms of the cooling surface, as the liquid paths are only straight lines.
- For cold plates longer than 500 mm, deep drilling becomes very difficult in aluminium plates.
- Seams are very sensitive areas for leakage.
Liquid cold plates in die-casting
The die-cast liquid cold plate consists of two parts: the housing and the cover. This type of heat sink is used for complex applications and/or large production volumes.
After moulding, the two parts can be sealed with an O-ring or by FSW.
Disadvantages of liquid cold plate in die-casting
Liquid cold plate in die casting use a particular technology that consists of moulding the aluminium part over the coolant pipe. Although the expected result is a perfectly sealed part, pouring the liquid aluminium around the tube is a delicate process that requires the tube to be held still to avoid any movement that could impact on the sealing of the plate. This technology greatly increases the cost of the cold plate due to the complexity of the tube and its holding.

Liquid cold plates assembled by brazing
Brazing technology in liquid cold plate assembly is typically used for high performance designs requiring lower thermal resistance but perfect sealing. For designers, using brazing for cold plate assembly offers many possibilities and flexibility to control the design:
- Thermal resistance,
- Heat flow,
- Pressure drop,
- Fluid path,
- Size,
- Shape,
- Material hardness,
- Surface geometry and the possibility of mounting components on both sides of the plate.
The cooling channel is created by machining baffles and fins into the plate or by directly inserting high performance corrugated aluminium fins. Although the use of this type of cold plate offers great flexibility, it is also a very expensive process.

The disadvantages of liquid cold plates by brazing
- Brazing equipment is very expensive (with vacuum equipment costing over €1M)
- High annual material maintenance costs.
- Heat treatment of parts is required after brazing to restore acceptable mechanical properties to the parts.
- Very long brazing cycles (about 8 hours)
- Impossibility of stirring very large cold plates due to the size of the brazing furnaces.
Liquid cold plates assembled by friction stir welding (FSW)
The FSW (friction stir welding) liquid cold plate assembly is a two-part construction.
The liquid flow path is machined into the cold plate housing. This cooling channel can be complex and even incorporate fins to improve the heat transfer surface.
The cover is then placed on the channel above the flow area and welded by FSW.
What are the advantages of FSW welded liquid cold plates?
The major advantage of using FSW for cold plate assembly for power electronics is its cost:
- All-in-one tool: hybrid welding and machining equipment
- Fast manufacturing process for large plates (approx. 10 min per plate) or small plates (approx. 1 min)
- Low energy consumption (similar to a machining operation)
- Fast training: 1 day to train a CNC operator into an FSW operator
Compared to the alternative methods mentioned above, FSW has a number of technical advantages:
- Pressure resistance of 300 bar (at 10 bar for the liquid cold plate by screwing).
- All aluminium alloys as well as high-strength and cast aluminium can be welded.
- All copper alloys can be welded.
- Aluminium can be welded with copper.
- Free choice of cooling geometry to cool specific areas of an application (unlike drilling where the channels are straight lines).
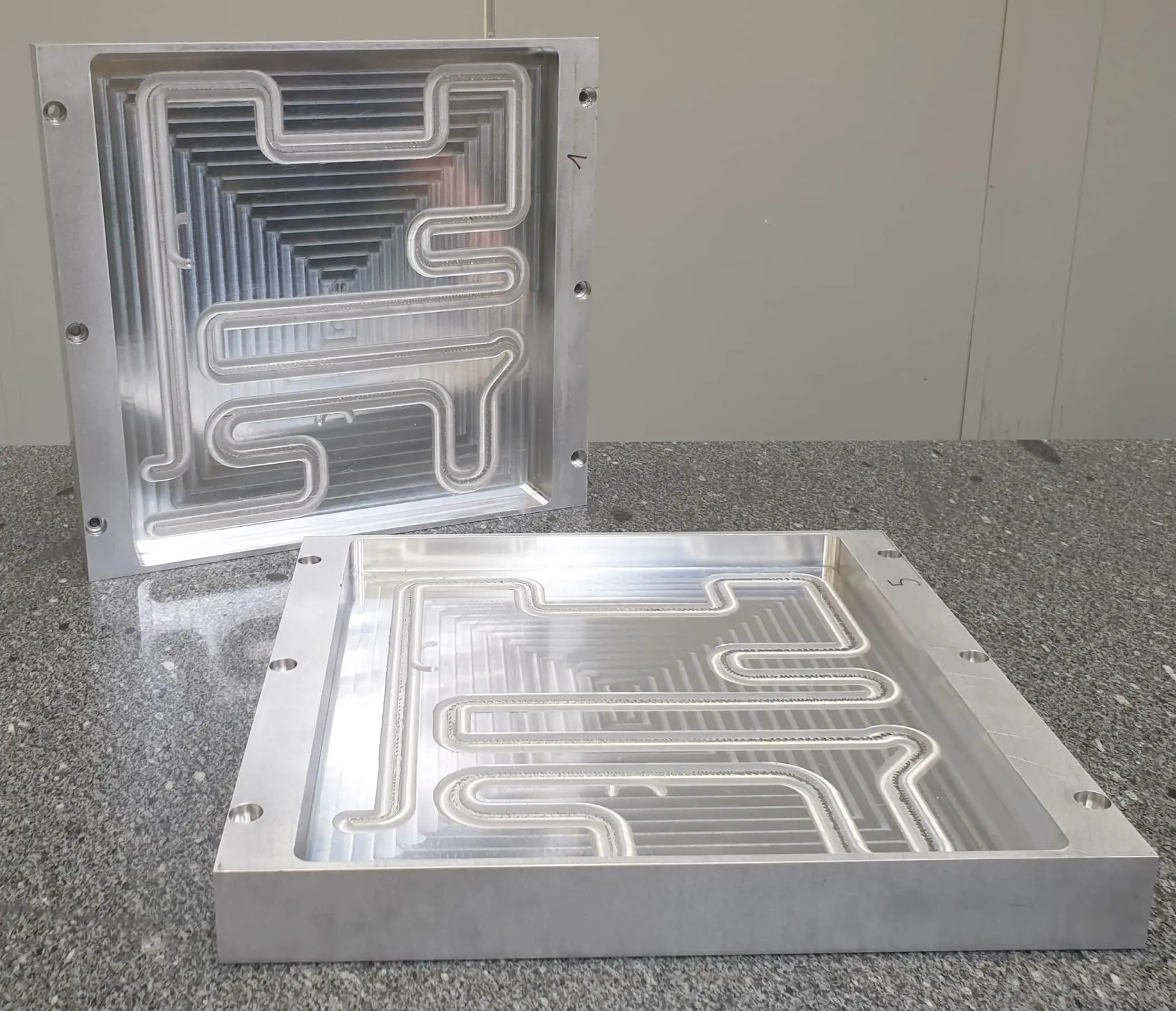
Want to know more?
Download for free our white paper on overcoming the challenges of cold plate manufacturing.