FSW APPLICATION
Bus Bar Welded by FSW
Enhancing reliability and efficiency in bus bar assemblies with Friction Stir Welding.
Why Choose Friction Stir Welding for Your Bus Bar Assembly?
Friction Stir Welding (FSW) offers a transformative solution for bus bar assembly, providing numerous advantages over traditional methods. From enhanced performance to significant cost savings, FSW stands out as the optimal choice for modern electrical systems.

No risk of unscrewing
Offers superior fatigue resistance, doubling the durability compared to traditional screwing methods.
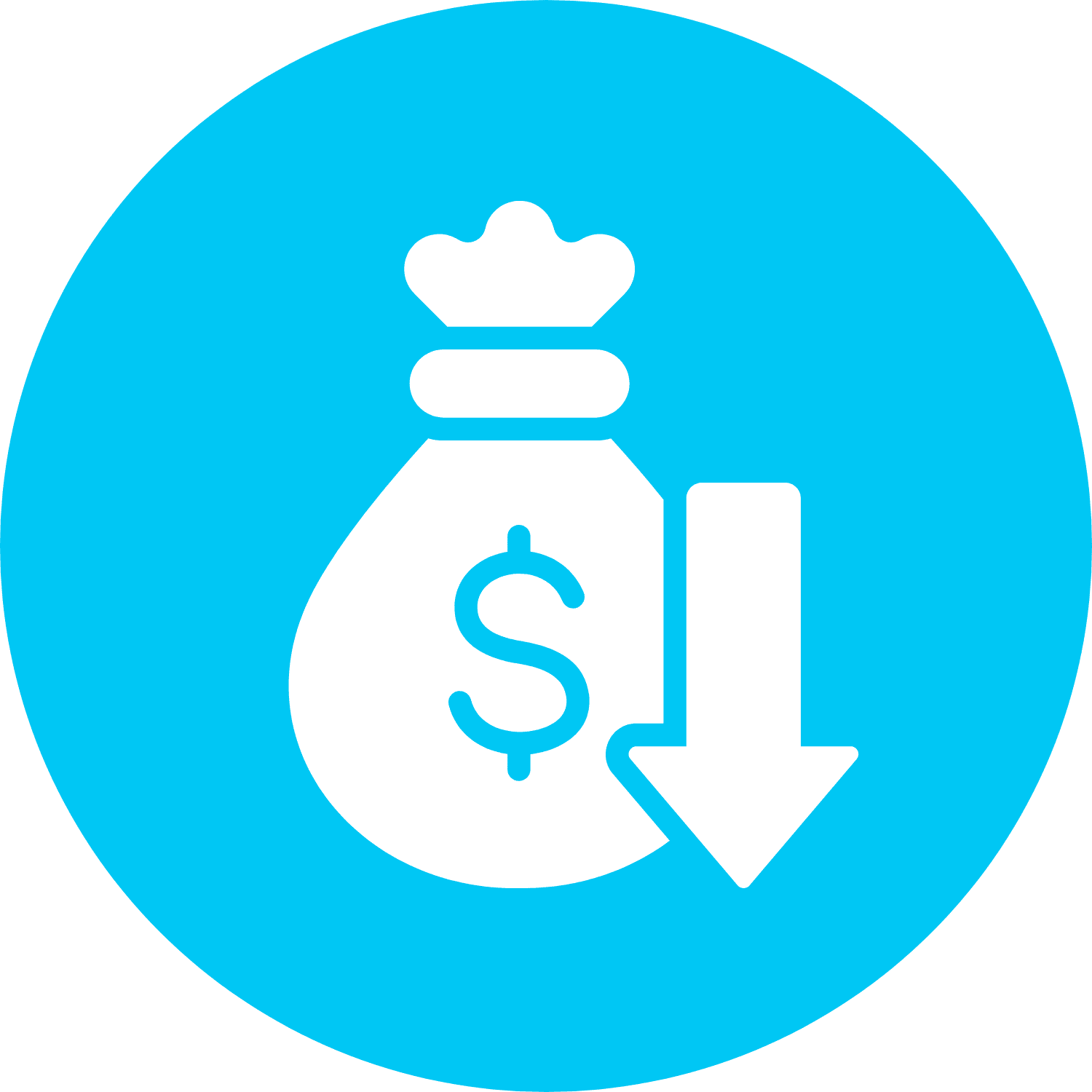
Cost divided by 3
Reduces welding costs by up to 3x compared to conventional screwing techniques.

Solution for copper shortage
Enables the use of aluminium as a viable alternative, making copper-aluminium welding feasible.
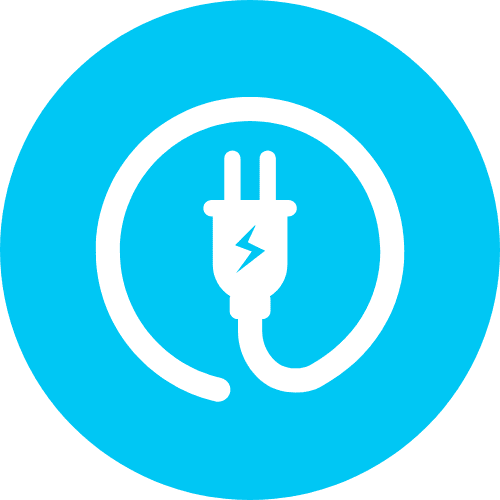
Perfect conductivity
Achieves weld conductivity that is twice as efficient as traditional screw connections.
Technical Specifications of FSW-Welded Bus Bars
See Friction Stir Welding Applied to Bus Bars in Real-Time
Comparing FSW to Leading Bus Bars Assembly Techniques
Friction Stir Welding vs. Screwing and Brazing
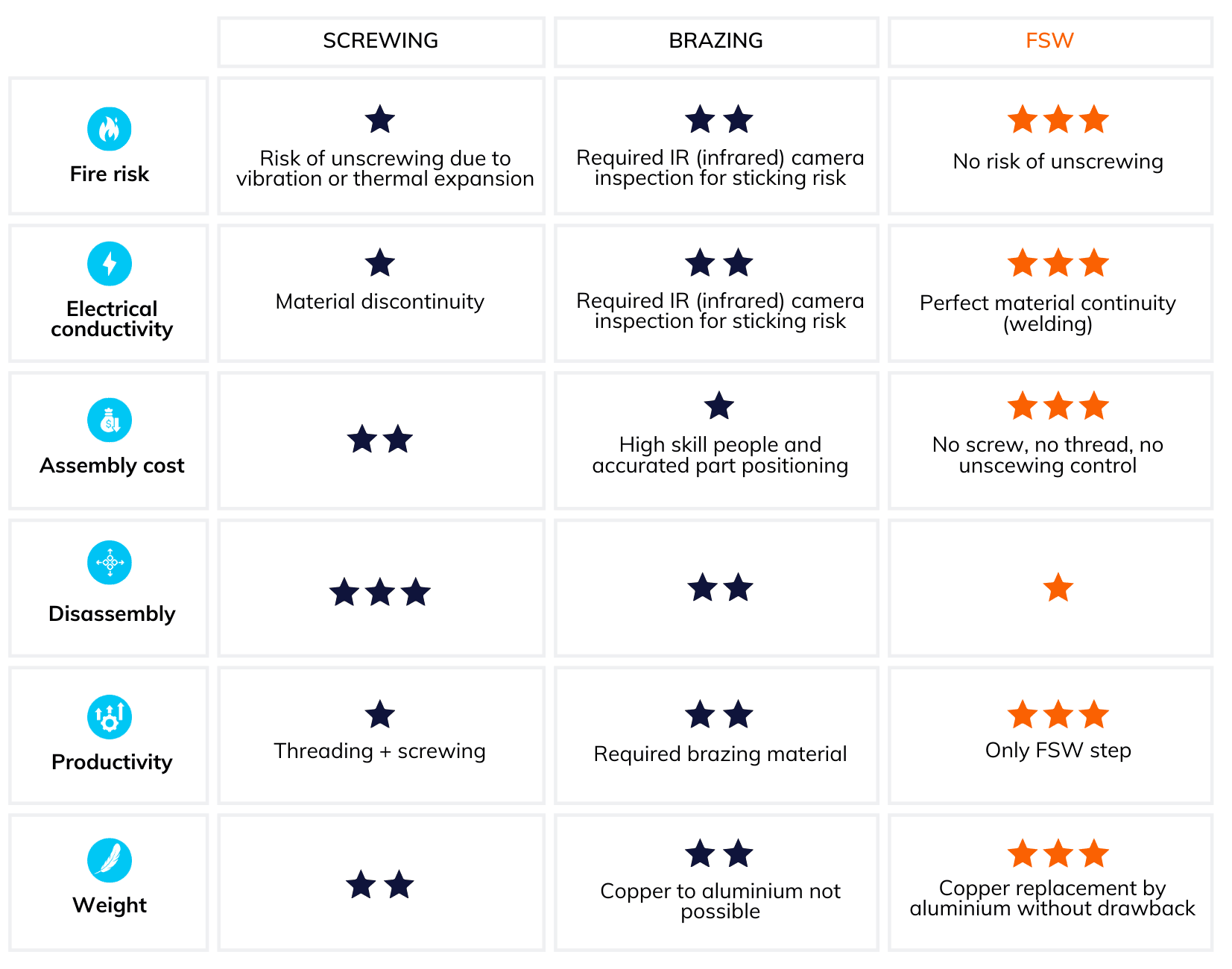

Friction Stir Welding vs. Laser and Ultrasonic Welding
Bus Bars: Essential Components Across Key Industries
Bus bars are fundamental components in electrical power distribution, providing efficient, reliable and scalable solutions that are critical to the operation of various high-demand industries. Their ability to handle large currents, reduce system complexity and enhance safety makes them a preferred choice for modern engineering applications. As technology advances and the demand for robust electrical infrastructures grows, the role of bus bars becomes even more crucial.
Whether in aerospace systems, automotive applications, railway networks, defense technology, energy production, or shipbuilding, bus bars ensure the seamless integration and operation of complex electrical systems, supporting everything from day-to-day functionality to mission-critical operations.

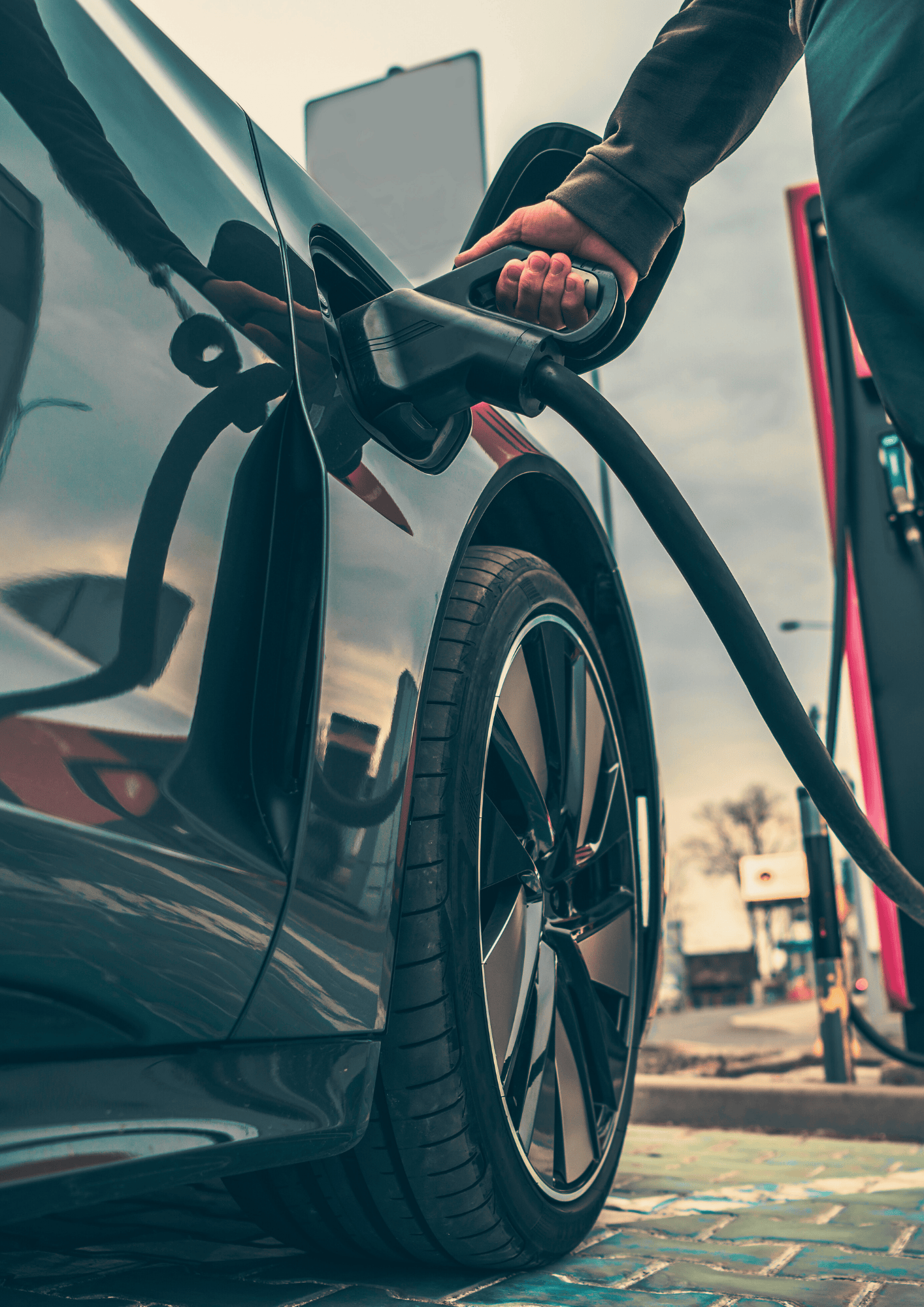



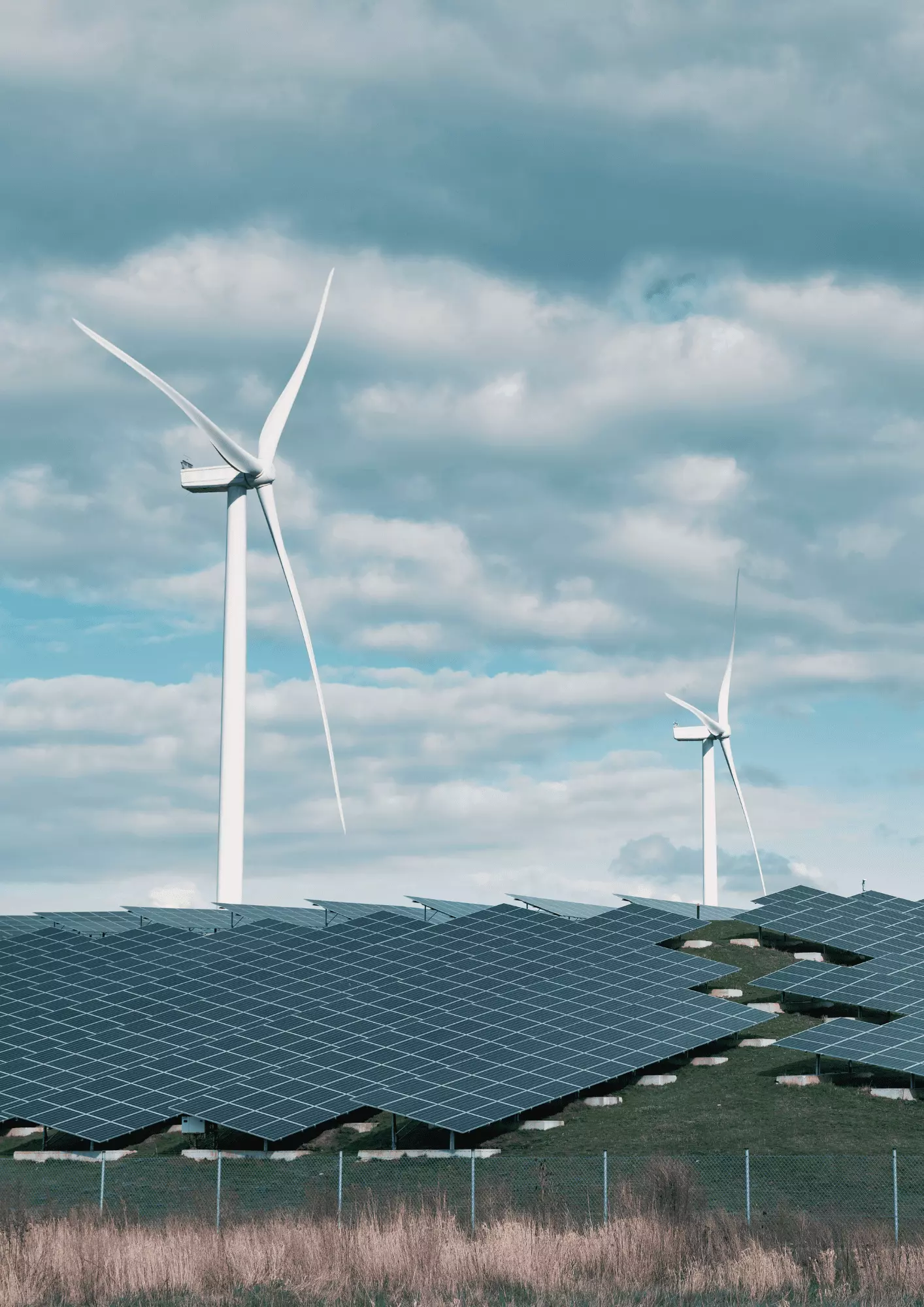
Energy
Empowering Sustainable Power Solutions
Dive Deeper: Comprehensive FSW Resources
Dive into the realm of Friction Stir Welding technology with engaging webinars, insightful blog posts, and in-depth whitepapers.
Webinar – 40 min – Replay on demand
Friction Stir Welding unveiled
Unlock the potential of Friction Stir Welding with our detailed webinar replay. Gain valuable insights into the process, its applications, and how to optimize it for your needs. Ideal for those looking to elevate their expertise in welding technology.
Blog articles – 5 min
Why FSW of aluminium is the future of industrial manufacturing?
How much will it cost you to weld your part by FSW?
Practical guide – 20 min
5 essential steps to master Friction Stir Welding
Master Friction Stir Welding with our step-by-step guide. From setup to certification, learn to improve your welds and enhance efficiency!

White paper – 20 min
Friction Stir Welding for dummies
Explore the fundamentals and advantages of Friction Stir Welding through our detailed beginner’s white paper to understand this innovative technology.
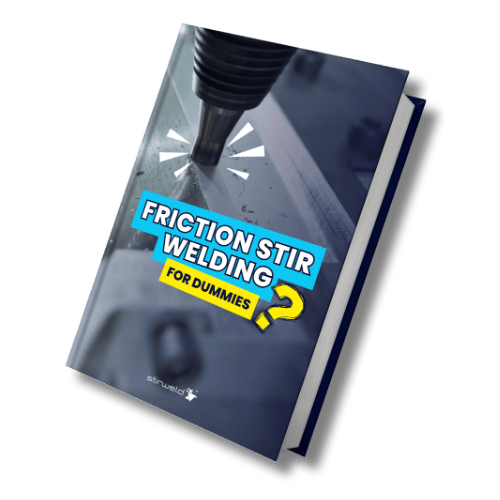
Ready to Revolutionize Your Bus Bar Manufacturing?
Discover how Stirweld’s innovative Friction Stir Welding solutions can revolutionize your bus bar assemblies and more. Let’s discuss how we can meet your specific industry needs.