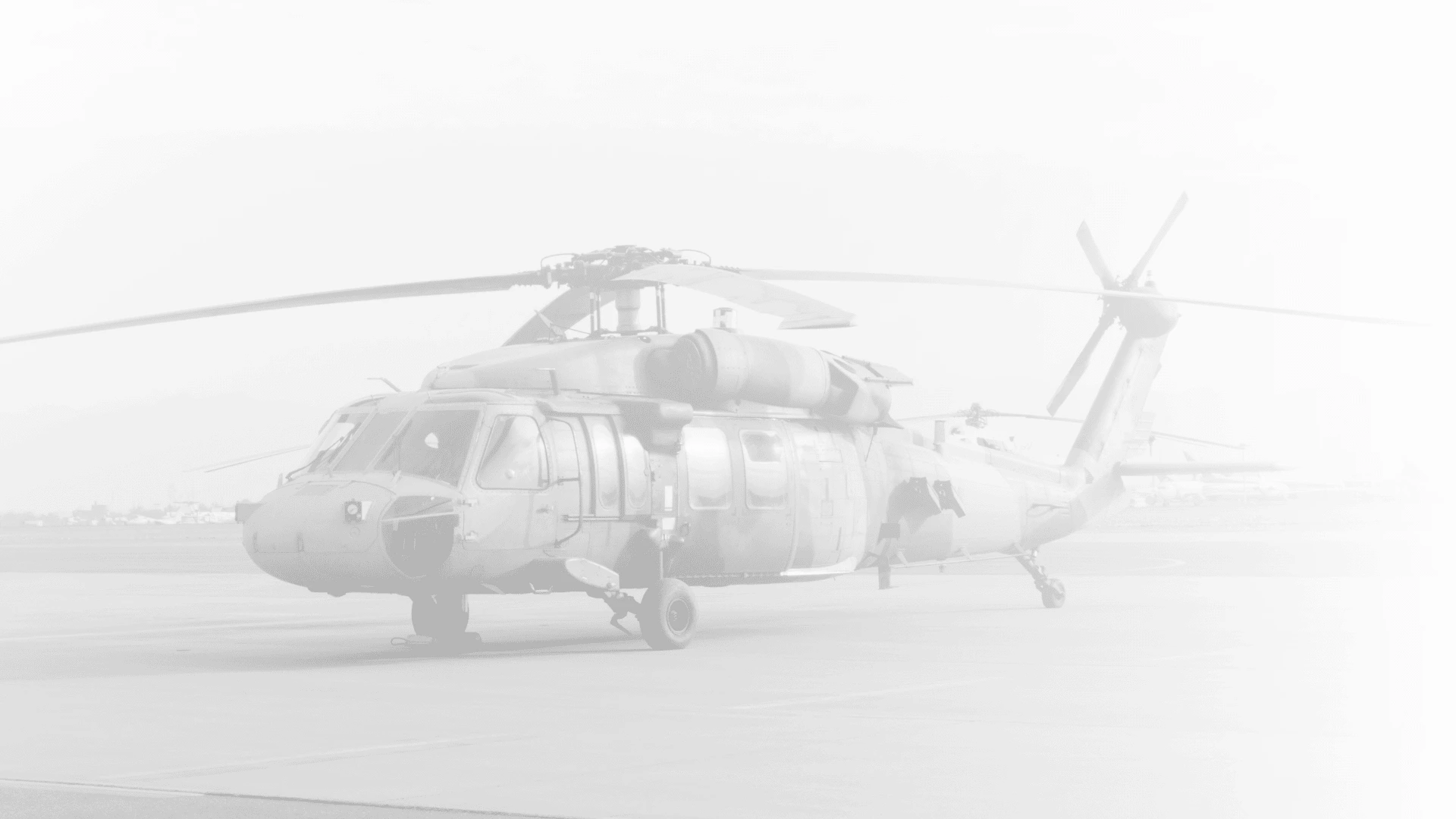
WHERE FSW TECHNOLOGY MAKES A DIFFERENCE
Friction Stir Welding in Defense
FSW technology fortifies defense with durable, resilient and advanced materials.
Unlocking Defense Potential with Advanced FSW Techniques
The defense sector confronts a host of challenges, spanning from the persistent pressures of R&D advancements to the stringent demands of cost-efficiency and supply chain reliability. In a domain where superior materials, sustainable practices and technological innovation are paramount, Friction Stir Welding emerges as a transformative solution. Offering a fusion of quality, economic efficiency and environmental responsibility, FSW introduces a paradigm shift, revolutionizing defense manufacturing processes. By consistently delivering components of unmatched resilience and durability, FSW technology is poised to redefine the benchmarks of military equipment excellence.
Exploring FSW Applications in the Defense Sector
In the stringent defense sector, ensuring equipment robustness, adaptability to extreme conditions and longevity, while maintaining operational efficiency, is paramount. Friction Stir Welding steps up to these challenges, offering unparalleled welding solutions tailored to the unique needs and high standards of military applications.

Stiffened panels
Stiffened panels are integral in the construction of armored vehicles and military structures. FSW has emerged as the preferred technology for welding these critical defense components.
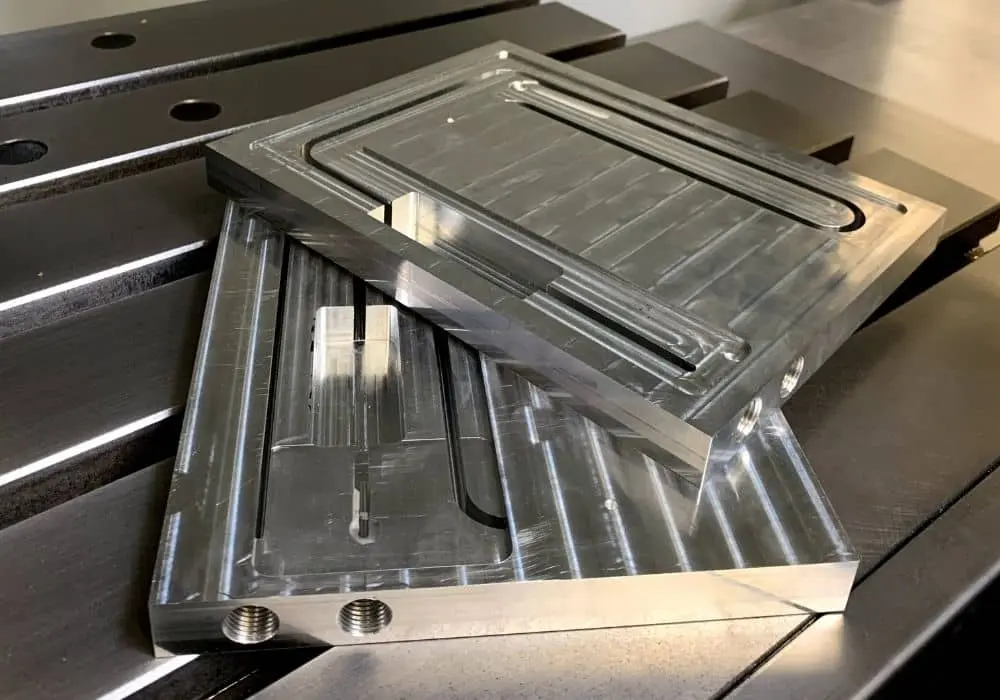
Cold plates
Crucial for regulating the temperature of electronic components in defense equipment, liquid cold plates safeguard the optimal functioning and lifespan of sophisticated military systems.
Recommended FSW Equipment for Defense Applications
Our FSW equipment offers a trio of benefits: quality, affordability and eco-friendliness, meeting the rigorous standards of the defense sector. Explore the devices our FSW experts recommend, tailored to your defense-related requirements.

Standard FSW head for CNC
This FSW equipment can weld from existing 3-, 4- or 5-axis CNC machine tools. It delivers precision in force control, immediate force feedback, effective tool cooling and top-tier defense against mechanical wear and vibrations—crucial for premium FSW welds.
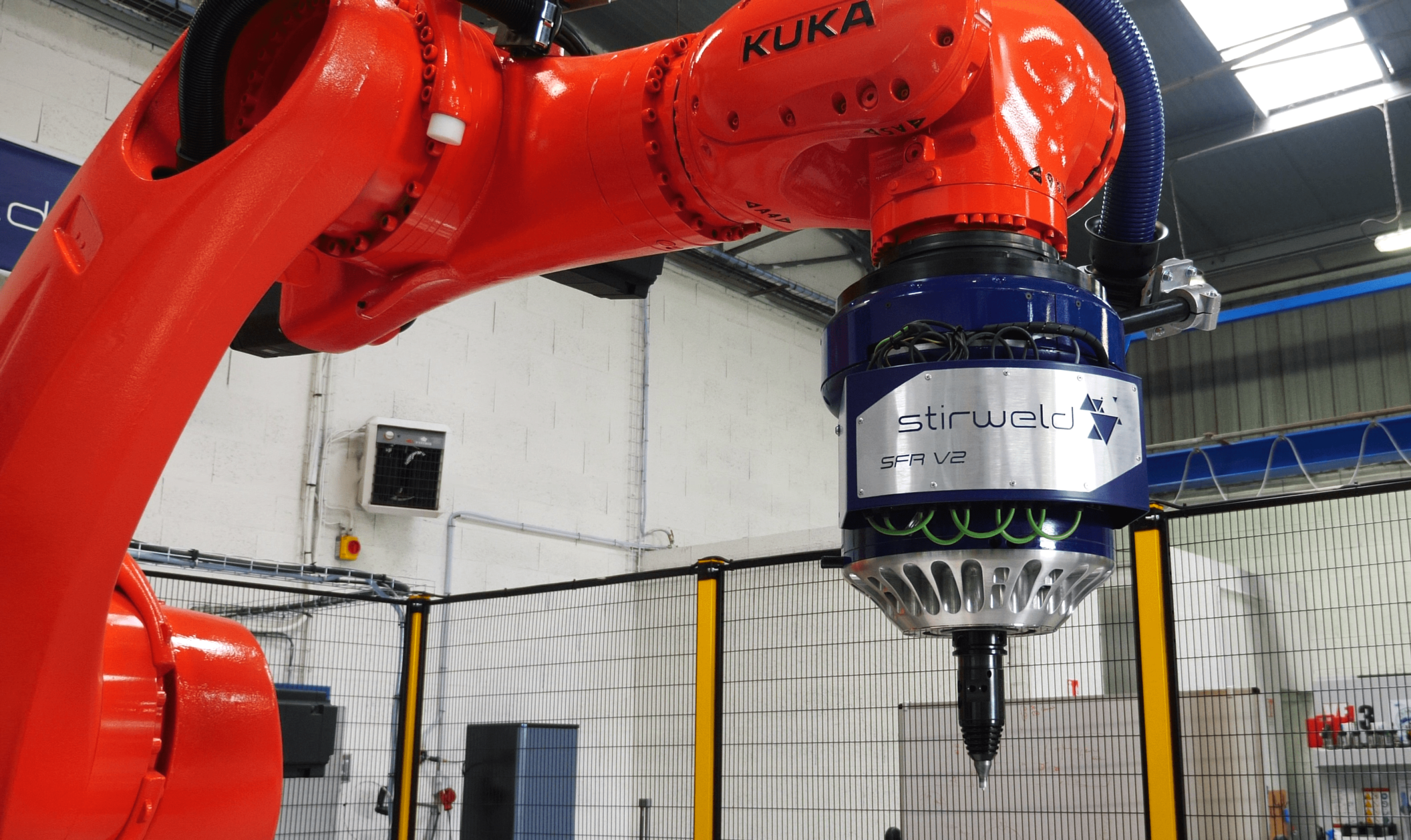
FSW spindle for robot
Suited for high-capacity robots, our robotic FSW system equips standard industrial robots with Friction Stir Welding functions, transforming them into versatile units that meld welding and machining, enhanced with auto tool-switching capabilities.
Dive Deeper: Comprehensive FSW Defense Applications Resources
Want to explore FSW Defense Applications further? We’ve gathered a set of valuable resources tailored for you, featuring engaging webinars, informative articles, and comprehensive whitepapers. Dive in below to tap into the knowledge we’ve curated specially for you.
Webinar – 45 min – Replay on demand
Thermal management: why choose FSW for the assembly of your liquid cold plates?
Choosing Friction Stir Welding as the joining technique for your cold plates has several significant advantages, including no risk of leakage, improved thermal management by 2 and costs that are reduced by ten.
Do you want to know how to reach these results? Register for this free replay webinar on FSW liquid cold plate.
Blog articles – 5 min
Mounting Bracket and FSW: Friction Stir Welding performance in response to the welder shortage
Stiffened panels assembled by friction stir welding
White paper – 20 min
Overcoming cold plate manufacturing challenges
Delve into the prowess of friction stir welding in crafting liquid cold plates in our enlightening white paper. Transform production challenges into advancements with insights from this guide.

White paper – 20 min
Aluminium stiffened panels welded by FSW
Discover the superior manufacturing of FSW-welded aluminium stiffened panels in our succinct white paper. Navigate assembly hurdles using methods that prioritize strength and longevity.

Elevate Defense Standards with FSW
Ready to elevate the capabilities of your military equipment? Discover how Friction Stir Welding can be your strategic advantage. Connect with our experts to discuss tailored solutions for your projects.