Robotic Friction Stir Welding: the new hybrid FSW industrial tool for robots
After the industrialized FSW head for machining centers, we are now very proud to make official the arrival of our new industrial tool: the FSW spindle for robot. Its use as a welding tool offers the same characteristics as the special FSW machines and is perfectly adapted to all brands of high payload robots, at a much lower cost. Both, FSW tool and machining tool, the Stirweld’s FSW spindle for robot becomes the new most performing hybrid industrial tool on the market. This innovation is clearly in line with Industry 4.0 and offers companies the possibility to optimize their robot park by taking advantage of the Friction Stir Welding technology (FSW).
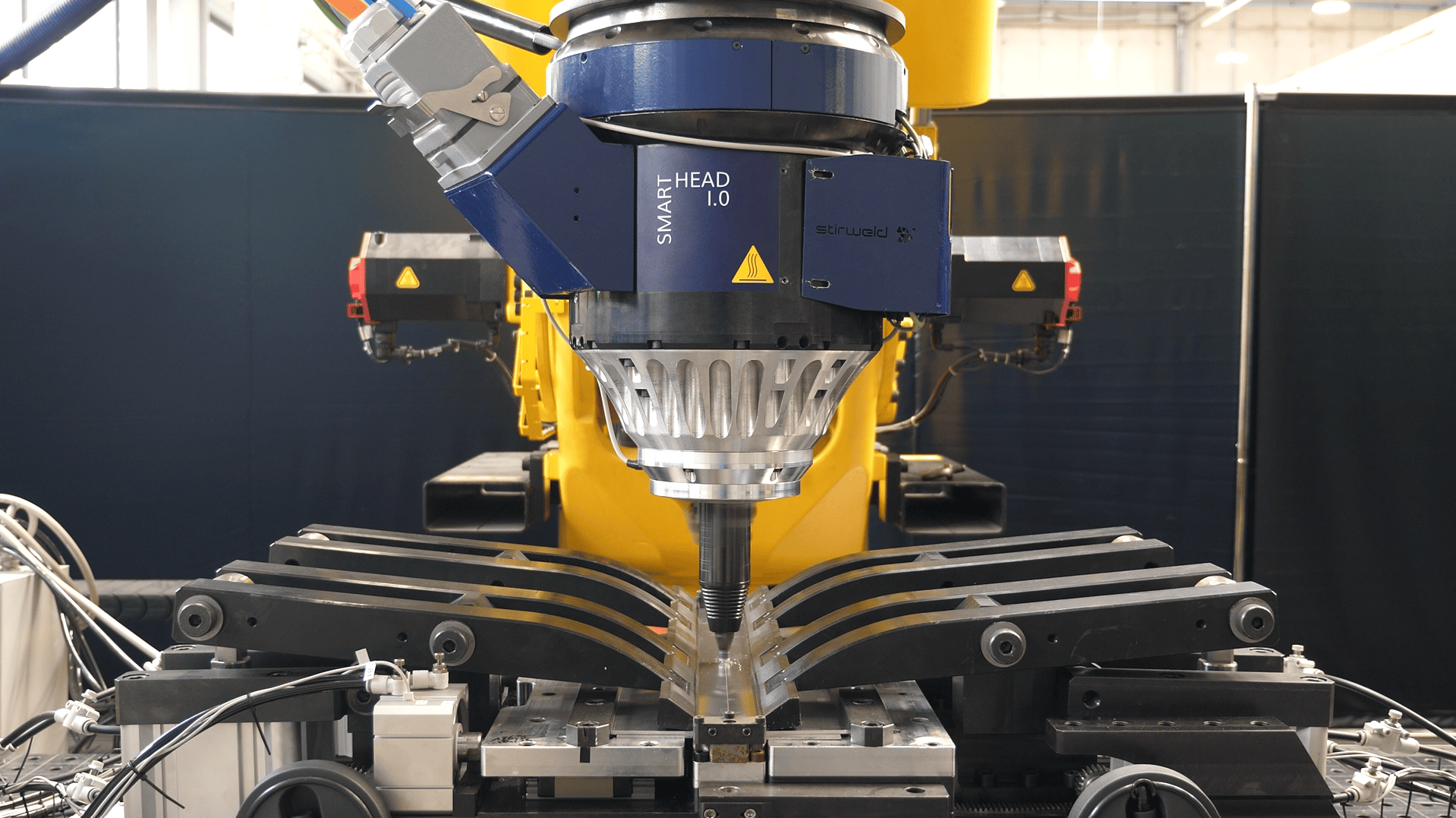
Friction stir welding on robot: presentation and advantages
Friction Stir Welding, a process finally accessible to companies thanks to Stirweld’s FSW spindle for robot
Friction Stir Welding (FSW) was previously a process reserved for high value-added applications, due to its relatively high cost.
However, this welding process, without any melting, offers many advantages, both economically and ecologically.
Friction Stir Welding (also called FSW) allows the assembly of non-ferrous metals with low melting point such as aluminum, copper or magnesium. An assembly made without adding material and therefore without fusion. Each FSW assembly maintains the high mechanical properties of the materials, doesn’t require seam preparation, and causes very little deformation. The result is a high-quality assembly with perfectly sealed welds.
The key advantages of friction stir welding
At Stirweld, we developed a FSW spindle for robot, adaptable to all brands of high payload robots. This FSW head makes friction stir welding accessible by transforming an existing robot into a real friction stir welding robot. This robot will combine FSW welding actions as well as machining actions thanks to its automatic tool changer.
Thanks to this new tool, companies can optimize their robot park with a FSW robot, to take the advantage of all the benefits of friction stir welding.
Advantages of robotic friction stir welding

Equipping a robotic cell with a motorized FSW spindle combines all the advantages of friction stir welding with the advantages of using a robotic cell (robot workstation) as an industrial tool.
These are significant benefits in terms of high performance, in addition to a significantly lower investment cost.
The assembly of 3 dimensional (3D) joints for large parts
Unlike a machining center that only works flat, a robotic cell (or workstation robot) with an articulated arm equipped with an FSW spindle, is capable of a wide range of movements. A range of motion that allows working on 3-dimensional parts.
By working on complex 3D joint assemblies, FSW welding cells represent a real opportunity for sectors such as aeronautics, aerospace, railway, automotive…
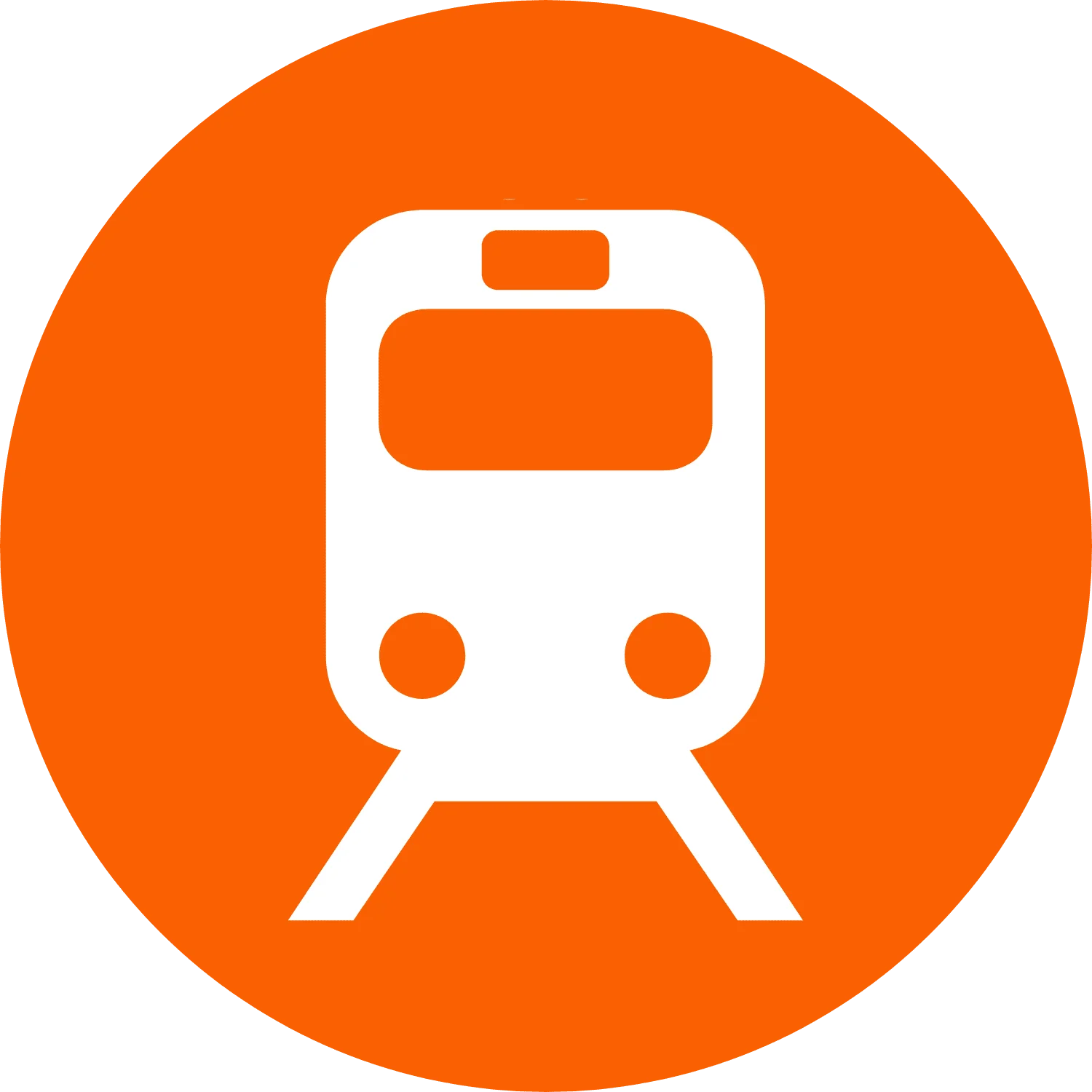
Railway
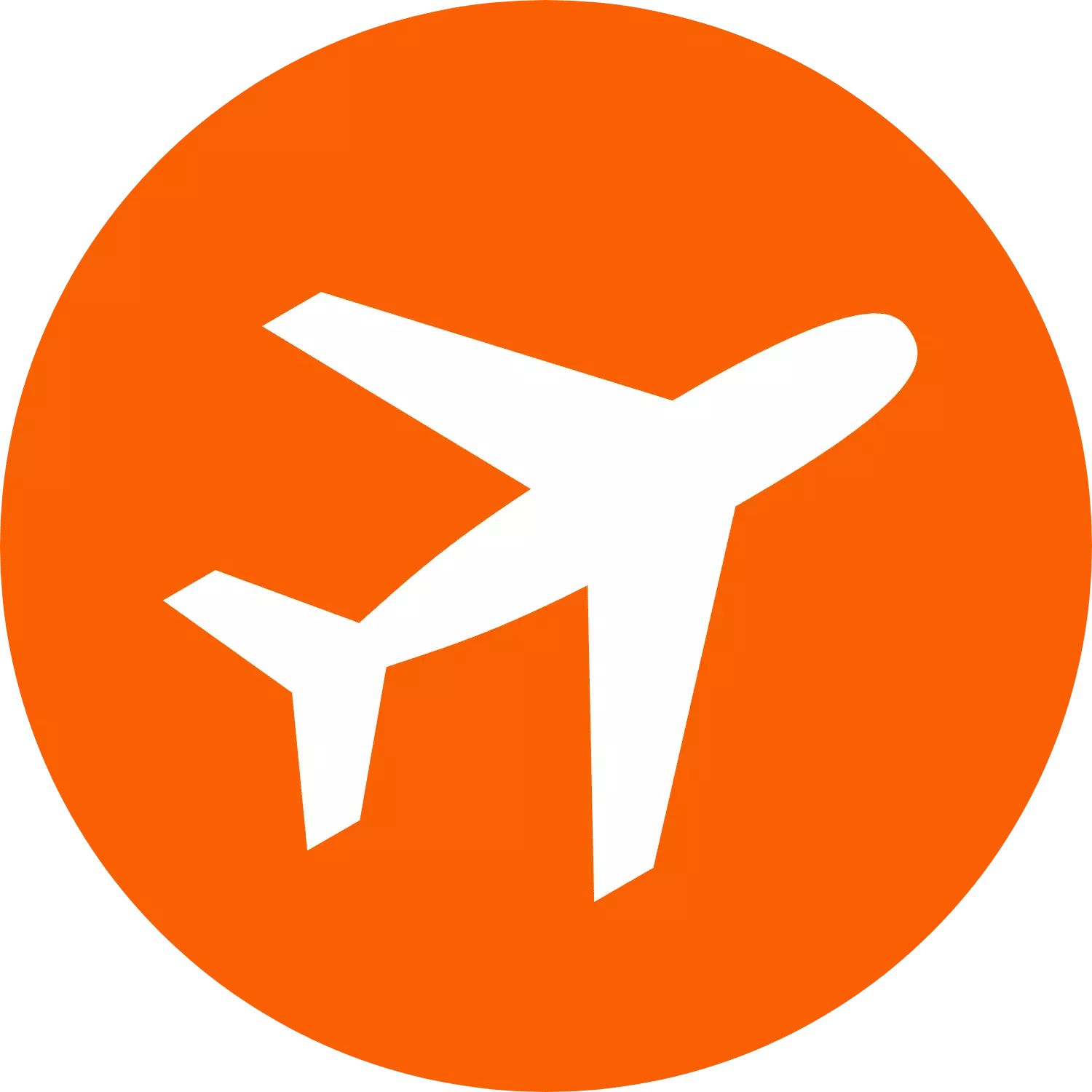
Aeronautics

Space

Automotive
With a Friction Stir Welding solution for robot, parts can be assembled on 7 axes (as opposed to 3 or 5 on a machining center machine), allowing the entire surface of large parts to be covered and welded in 3 dimensions.
FSW robot cell for ever larger assemblies
Equipping a robotic cell with a FSW spindle for robot means being able to carry out large-scale welding operations. With an original height of 3 meters, the articulated arm can already work over a total amplitude of 2 meters.
For even larger workpieces, the performance of an FSW robot station will not be limited, as it will be possible to mount the cell on rails up to 20 meters long. This means that even larger workpiece areas can be covered.
This possibility of equipping a FSW robotic station on standard elements such as rails, is a real gain in economy of scale. Considerable production and cost savings for welding and machining of large parts.
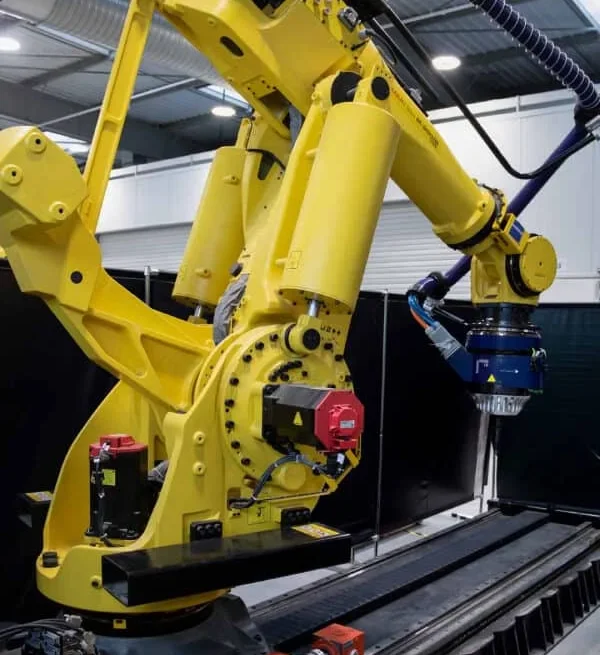
FSW robot spindle and increased productivity
With its 360° rotation, the robotic cell equipped with the FSW spindle can work simultaneously on several workstations. Once a first part has been welded, the articulated arm can easily start welding on a second work surface, while loading/unloading of the first part (pendular loading or in masked time). A considerable gain in productivity for large series of parts to be welded.
The new FSW hybrid spindle for high payload robots: between performance and innovation
With this FSW hybrid spindle for robots, we wanted to improve and increase the productivity of companies in the metal assembly industry. A FSW hybrid tool that combines innovative and high-performance industrial features.
What are the innovations of the FSW spindle for robot?
FSW spindle adaptable to all robot brands
Today, some robot brands offer their own Friction Stir Welding head, compatible only with their robot. The Stirweld’s FSW spindle for robot is adaptable on all brands of high payload robots.
With this innovation of compatibility via an adapter (Robot Flange), Stirweld becomes the first FSW spindle for robot in the world to fit on all brands of high payload robots. Robots ranging from 600 kilograms to 2,000 kilograms of load such as: Fanuc, Kuka, Stäubli, Yaskawa, or ABB.
As robot cells are standardized to facilitate and limit maintenance costs, we offer with this spindle a considerable cost saving by adapting the FSW technology on all these robot brands. A tool offering to robot cell integrators a solution completely independent of a robot brand.
Note: only the spindle is delivered, which offers the possibility to freely compose FSW welding environments. A solution that meets all industrial demands.

The FSW spindle for robot, the hybrid industrial tool for welding and machining
Friction Stir Welding can lead to flash on different applications, in other words, burrs on the edges of the weld. Using the FSW spindle for robot also means benefiting from a hybrid head that can be equipped with both, an FSW welding tool and a machining tool. Thanks to the human-machine interface that we developed, the robot can easily and quickly change tools, in complete autonomy.
Automatic tool changer
With its HSK 63 automatic tool changer, the Stirweld spindle can automatically adapt its manufacturing cycles to manage several FSW or machining tools. Moreover, the robot can replace its FSW tool at the end of its life without human intervention.
Industry 4.0: a robotic cell equipped with an intelligent FSW spindle
By equipping a robotized cell with a FSW spindle, we equip the robot with a real intelligence system on 2 axes:
FSW connected spindle for predictive maintenance: the spindle permits the feedback of potential future maintenance on the man-machine interface delivered with the head. The computer permits smooth and easy communication between the user and the robot spindle via visual and audio alerts. Despite the low maintenance requirements of this new tool, it’s still useful to have feedback on the wear and tear of the FSW tools used (for example, when the tool reaches the end of its service life).
Note: All our tools and parts for the FSW spindle for robot have been extensively tested to ensure that they are reliable and robust and require as little maintenance as possible. When an FSW tool reaches the end of its use, we change it in a standard exchange.
Intelligent information feedback: Thanks to the complete instrumentality of the FSW spindle for robot, the human-machine interface is able to feedback a large amount of information in full monitoring. Information such as torque measurement, welding torque, vibrations, inclinations, cooling control… Information which allows to gain in quality and efficiency on the different series of Friction Stir Welding, but which also permits to ensure the good course of the welding bead on the different assemblies.
Note: All our tools and parts for the FSW spindle for robot have been extensively tested to ensure that they are reliable and robust and require as little maintenance as possible. When an FSW tool reaches the end of its use, we change it in a standard exchange.
Technical characteristics of the FSW spindle for robot
Our Stirweld’s FSW Spindle for robot has superior characteristics to special Friction Stir Welding (FSW) machines, although it’s considerably less expensive:

Robotic FSW welding process: a project developed by 3 main actors
As the carrier of this FSW spindle for robot project, we have, with the help of two local actors and the support of BPI France, developed this Industry 4.0 tool.
Would you like to know more about the FSW spindle for robot?
Contact our experts.