How to choose my FSW tool for my application?
Since the emergence of friction stir welding, many innovations have been made to improve the quality of FSW tools. These improvements result in better quality, more stable welds, and a certified lifetime. Today, many people are asking how to choose their FSW tool and how this choice will influence the quality of their weld. We propose to answer this legitimate question throughout this article. To start with, it is important to detail the composition of an FSW tool.
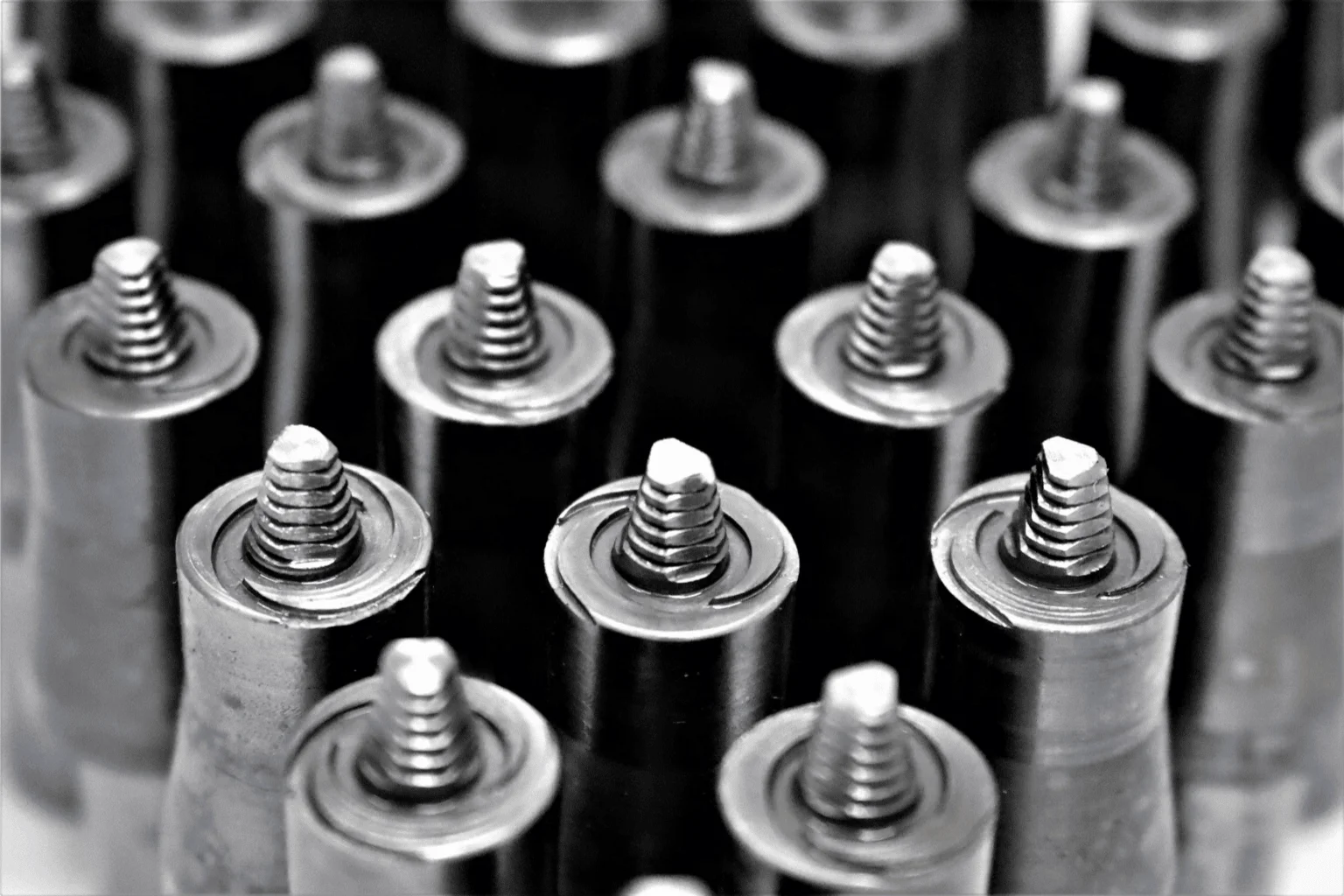
The different components of a FSW tool: what is a shoulder and what is a pin?
A FSW tool consists of three parts: the body, the shoulder and the pin.
The shoulder is the part that heats the material by friction in order to soften the workpieces and thus enable the welding operation. This is its primary function. The larger the diameter of the shoulder, the larger the contact area, which increases the frictional capacity of the tool. However, too large a shoulder will cause the workpiece to heat up too much and reduce the strength of the weld. The size of the shoulder will therefore depend on the thickness to be welded.
In addition, the shoulder with its counter-cyclical spiral shape allows the material flow to be pushed back towards the centre to prevent it from leaving the welding area. This second feature will improve the surface finish of the weld and the quality of the weld. With this feature, there is no need to tilt the tool during the welding operation. This is because the spirals pull the material towards the axis, which prevents the material from slipping (see infographic below: “No more tilt angle required on the FSW tool”).

In addition, the spiral shape improves tolerance to weld seam offset, reduces burrs and makes variable thickness welds possible.

Second part: the pin – the extremity of the tool.
The pin is the part of the tool that will penetrate the material by mixing it through a shearing effect: this is the stirring. Indeed, due to its conical shape and its grooves, the pin heats the material and softens it in order to ensure the mixing of the materials and the quality of the weld. The flat tip of the pin allows better penetration of the tool and therefore reduces the risk of lack of penetration. The pin and its flutes allow stirring in the direction of tool rotation as well as vertical mixing of the material.
Heat is generated by the friction between the workpiece and the tool, which produces plastic deformation of the workpiece and welds the two parts together.
How does the quality of my FSW tool contribute to the quality of my weld?
The quality of the weld depends directly on the quality of the tool and the choice of the tool. We will see later how to choose the right tool for your specific application.
But first, let’s see how the quality of the tool affects the quality of your FSW weld. To understand this, it is important to keep in mind how a FSW welding operation works.
Friction Stir Welding in 4 steps
Clamping of the parts to be welded: side by side in a butt welding configuration, one on top of the other in a lap welding configuration. The tool does not depend on the welding configuration. The same tool is used for butt and lap welding.
The tool penetrates the material: the shoulder heats the material by friction and the pin seals the parts together.
Welding operation: the tool advances along the weld seam and mixes the parts together.
End of welding: the tool moves up vertically, leaving a hole.

As you can see, the tool geometry has an impact on the weld quality. The tool will directly contribute to the mechanical strength of the weld. How? By the strong mixing of the material by the pin and by the heat generated by the shoulder. These two phenomena will cause a recrystallisation of the aluminium which will result in the precipitation of fine grains and thus contribute to the very good mechanical strength of FSW welds.
However, at the end of the weld, the tool will leave an exit hole as you can see in step 4 of the infographic above. This is not a quality issue, but for some applications it is better to remove it. The solution: the retractable pin tool. Where a conventional FSW tool leaves an exit hole at the end of the weld, a retractable pin tool seals the hole directly at the end of the weld, without any further intervention.
Finally, a last improvement has been made to the FSW tools: temperature measurement of the weld in real time. The temperature measurement tool allows you to control your FSW weld in real time: it is a quality tool.
Smart tool holder – the temperature measuring tool: precision for successful welding
In addition to the functionality of a standard tool, the temperature measurement tool allows you to precisely measure the temperature of the weld in order to adjust your welding parameters finely and check 100% of the parts.
How does the temperature measurement tool work?
The FSW temperature measurement has two holders, one fixed and one rotating, each containing an electronic card. These electronic boards receive and send the signal from the probe in the tool to the software. Thanks to this system, it is possible to control the temperature of the weld in order to optimise all the welding parameters (rotation speed, feed speed, Z force).
The benefits of the Stirweld temperature measurement tool are:
As an example, the temperature measurement tool is very useful for the assembly of aerospace components according to EN 9100.

How to choose my FSW tool according to my application?
To choose your FSW tool, you need to take into account 4 parameters:

Stirweld has developed a range of standard tools for different markets and materials to be welded. To give you an idea of which FSW tool is best suited to your application, here are some examples of FSW tool choices depending on the application sector, the material used and the thickness to be welded.
FSW tool for your application

For example, for the aerospace sector, the FSW tool will be made of a high-strength alloy to suit the more demanding aluminium parts (2xxx and 7xxx series).
Another example is the automotive sector, where most parts are produced in aluminium casting. These alloys contain silicon, which is inherently abrasive. For this type of aluminium, we use tools made of ceramic, a material that is highly resistant to abrasion.
Stirweld supports you with a complete range of high quality FSW tools. One of our main references, the Ariane company, leader in the aerospace field.
What is the lifetime of an FSW tool?
There are two factors that influence the lifetime of an FSW tool:
The life of the tool will also depend on the materials being welded: aluminium/aluminium, aluminium/copper, copper/copper, aluminium/steel.
FSW Stirweld tools have an average life of 2000 metres of weld in a “classic” Al/Al welding configuration with a thickness of less than 8mm. In order to guarantee the quality of its tools, Stirweld uses a test bench.
Stirweld’s role in choosing your tool
Stirweld experts are here to help you choose your tool according to your requirements (distance and depth to be welded, tool geometry and material of the parts to be welded).
Stirweld offers you a whole range of tools according to the material of your parts:
All Stirweld tools are available in fixed pin and retractable pin versions with the possibility to add temperature measurement.
Please feel free to download our catalogue to learn more about our FSW tools.
Thanks to our engineering department, we are also able to develop specific tools for your applications and requirements.
The advantages of Stirweld tools
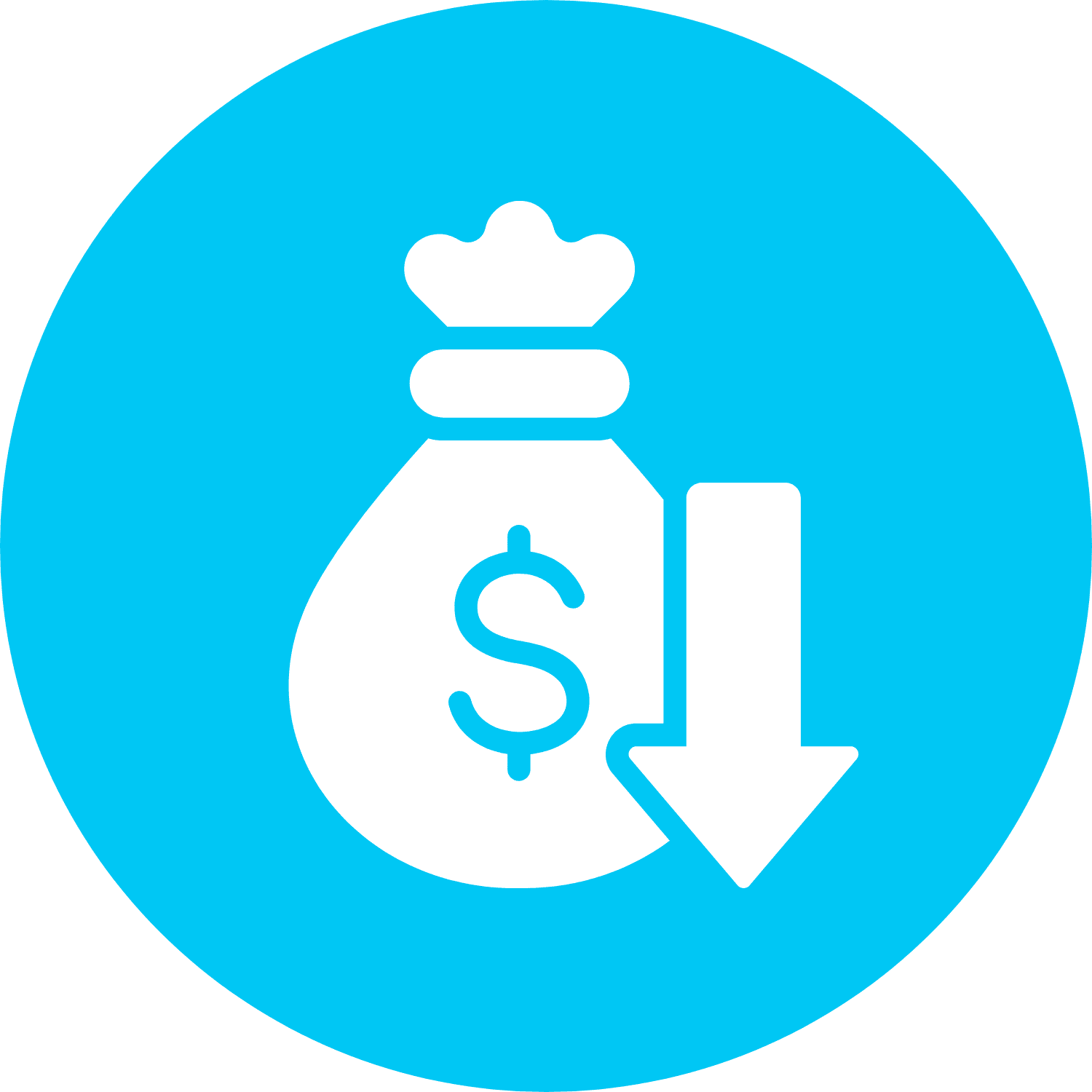
Manufactured in large series to reduce unit cost.

Quality with control of material, heat treatment and tool geometry – Ariane supplier

Ease of use thanks to Whistle Notch fastening.

Traceability thanks to the unique identification of each tool.
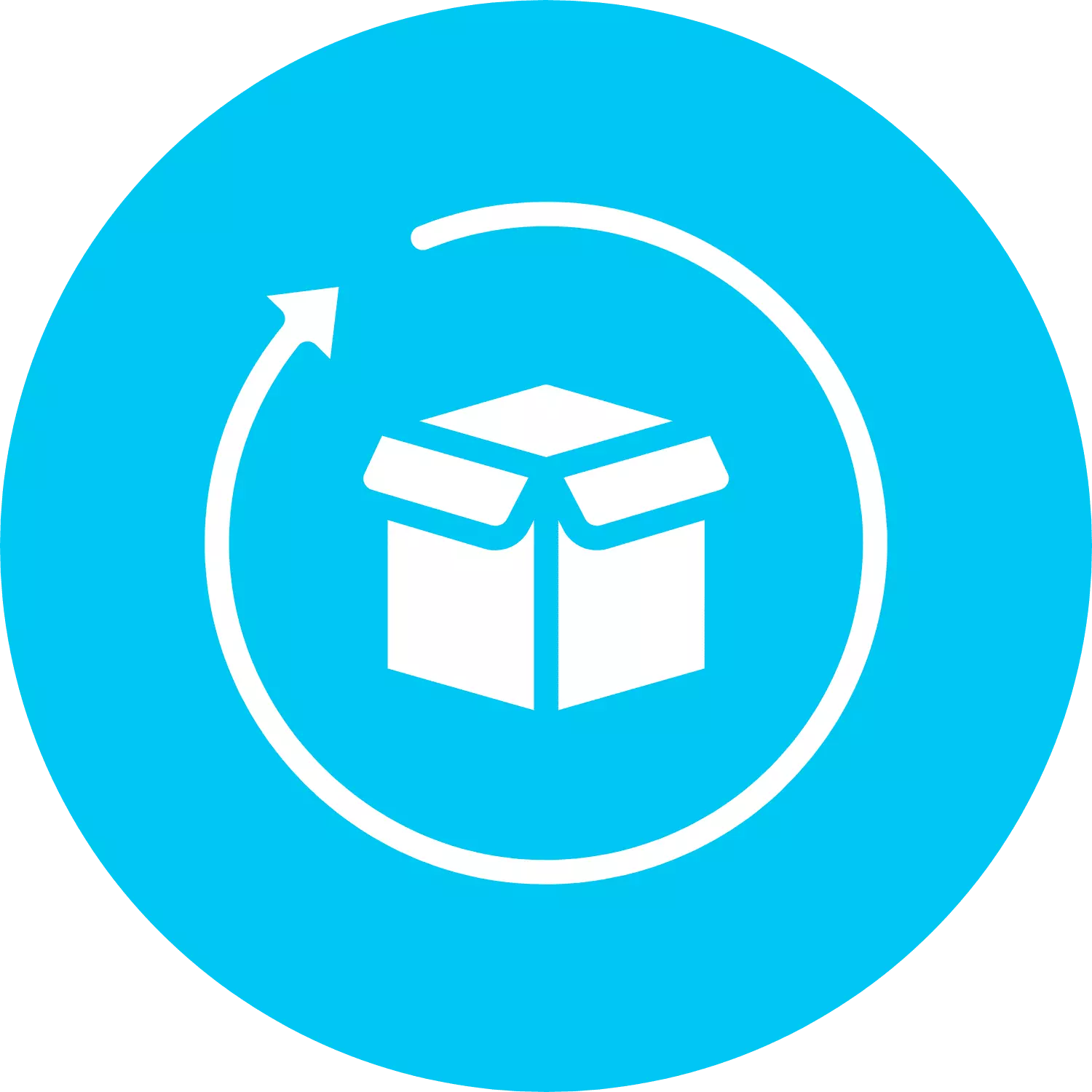
Delivery within 48 hours thanks to our stock of the most common tools.
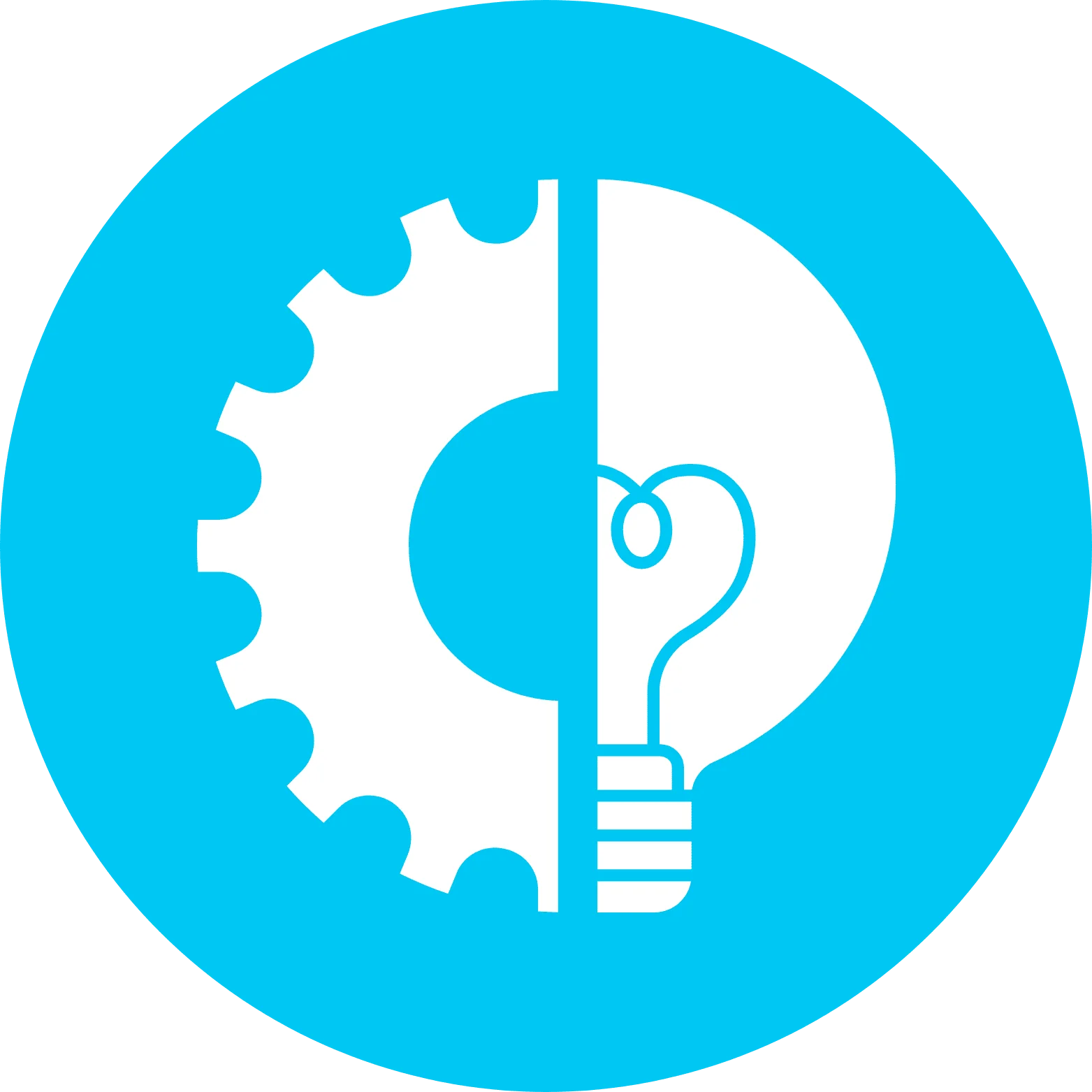
Performance with optimised geometry: minimise defects and maximise productivity and tool life – wear bench tested.

Qualification with pre-production to qualify the tool and process for your application.
Questions about our tools? About FSW?
We will assist you in the choice of your tool. Contact us without commitment.