Friction Stir Welding: Why a headless CNC approach doesn’t work?
Exploring the intricacies and fundamental flaws of pursuing friction stir welding without a FSW head: an in-depth analysis of the technical hurdles, operational limitations and the compromised outcome quality, highlighting the essential role of advanced FSW heads in ensuring optimal efficiency and superior weld quality.
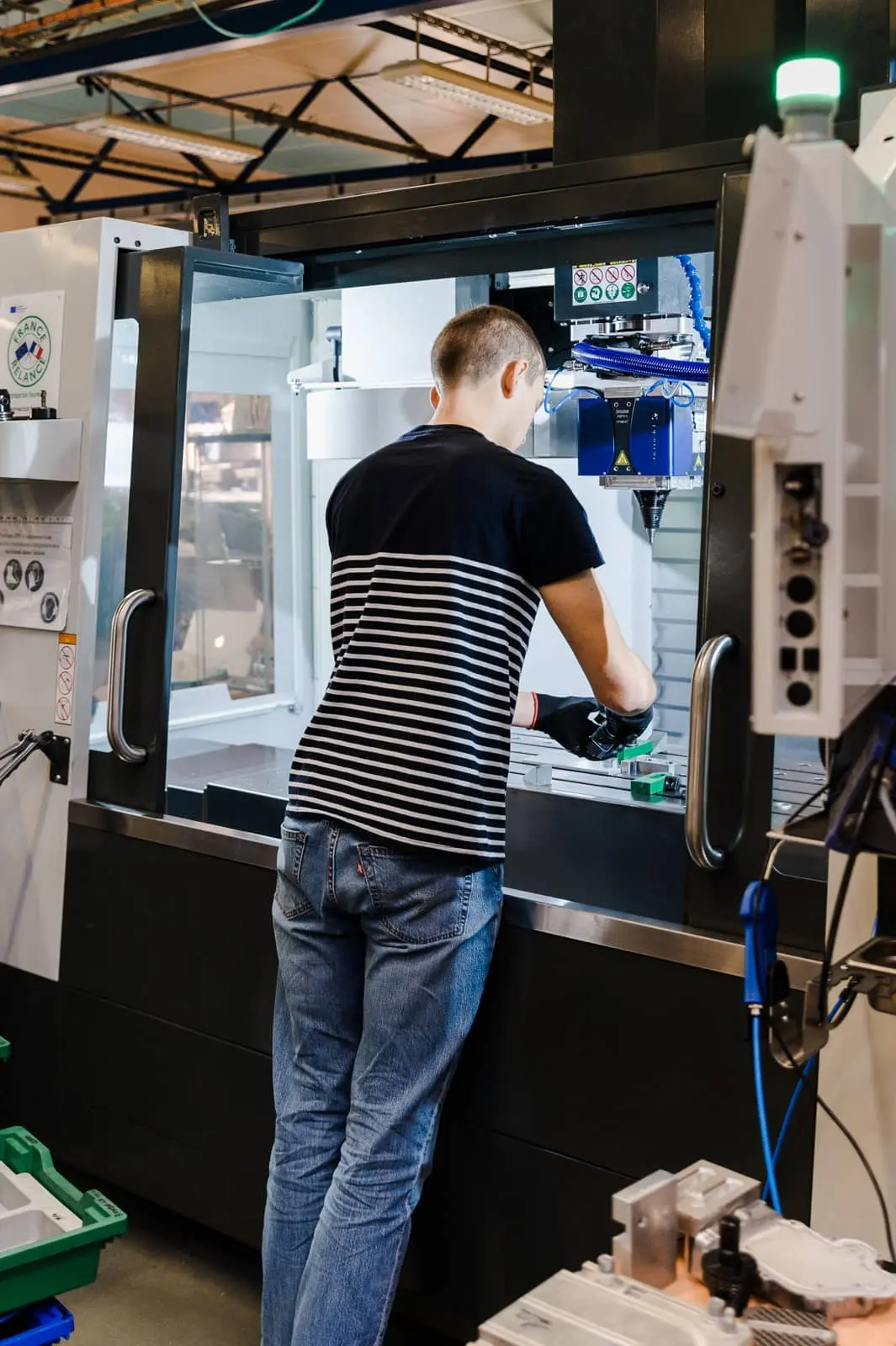
FSW on CNC without head: Numerous issues for uncertain outcomes
When considering the integration of friction stir welding (FSW) directly into your machining center for the fabrication of parts, it’s imperative to acknowledge the significant limitations and challenges inherent in this method. This approach, while apparently convenient, falls short in several critical areas, impacting both the quality of the welds and the efficiency of the production process. Below, we detail these key concerns to illustrate why a dedicated CNC FSW welding head is not just beneficial but essential for achieving industrial-grade welding outcomes.
Firstly, FSW on CNC without head requires a perfect piece flatness (lower than 0,02 mm), limiting the versatility of the materials and shapes that can be effectively welded. This constraint significantly narrows the scope of projects suitable for FSW without specialized equipment or without force control.
Secondly, FSW on CNC without head requires a workpiece with a sufficient thickness (> 70 mm thick) or without local strong clamping jig (as a roller) to withstand deformation challenges, highlighting the inadequacy of force control in standard CNC setups. Without precise control of the welding force, the risk of damaging the workpiece increases, compromising the structural integrity of the weld.
Thirdly, without head, the inability to manage excessive tool temperature limits the weld length due to the shortfall in tool cooling capabilities. This restriction not only affects the weld quality but also its length, thereby impacting the scalability of production.
Finally, for entities involved in serial production, the lack of vibration and force protection in the CNC spindle necessitates frequent replacements of the expensive CNC spindle. This requirement for constant maintenance introduces substantial downtime and escalates costs, undermining the viability of using a machining center for FSW on a larger scale.
Collectively, these constraints underscore the lack of repeatability and scalability in the welding process when attempting to utilize a machining center devoid of a dedicated FSW head. Such challenges starkly demonstrate the infeasibility of this approach, reinforcing the necessity of investing in a specialized CNC FSW welding head. With the right equipment, businesses can achieve consistent, high-quality welds that meet industrial standards, ensuring both productivity and profitability in their welding operations.
FSW on CNC: the indispensable 4 functions of our advanced welding head
To get past the problems, save time, and avoid extra costs of FSW on CNC machines, our friction stir welding head for CNC has four key features: force control, tool cooling, machine protecting and force recording.
Force control in FSW: key to overcoming flatness and thermal distortion
In real-world manufacturing and welding scenarios, the ideal of perfectly flat part remains illusory. Two primary phenomena impact part flatness: manufacturing variances such as inaccuracies from rolling, extrusion or casting, and the welding process itself, which introduces thermal distortion and in accuracies from piece locating. These challenges necessitate a nuanced approach to ensure the integrity and quality of the weld, which is where the specialized functionality of dedicated friction stir welding head becomes indispensable.
The ”force control” feature of a FSW head addresses these challenges head-on. In the absence of force control, the unavoidable irregularities in part flatness results in intermittent contact between the FSW tool shoulder and the workpiece surface. This intermittent contact leads to porosities into the weld, compromising its strength and integrity. Conversely, with force control, the FSW tool shoulder can adaptively follow the part surface along the weld joint, maintaining constant contact and thereby ensuring a high-quality weld devoid of porosity.
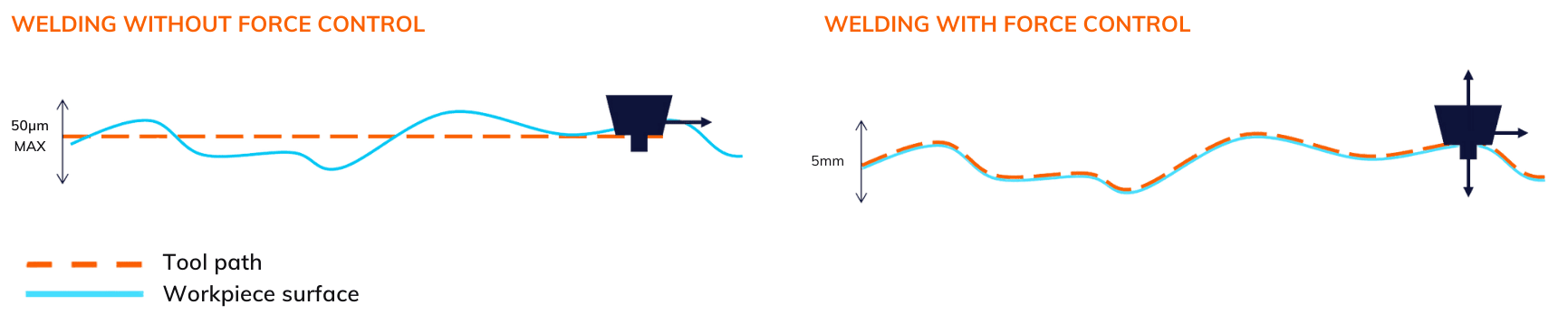
The necessity of force control extends further when considering the deformations that occur during the welding process:
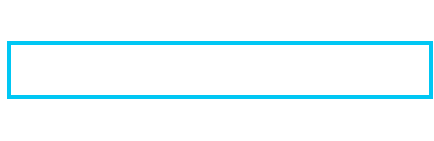
Before the welding process starts, the part retains whatever level of flatness it achieved post-manufacture.
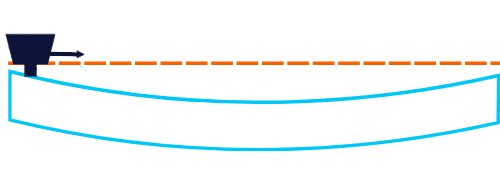
During the welding process without force control, the heat generated by the friction between the FSW tool and the component leads to thermal distortion. This distortion, even if minor, can significantly compromise the quality of the weld by altering the intended path of the tool or by creating gaps between the tool shoulder and the workpiece.
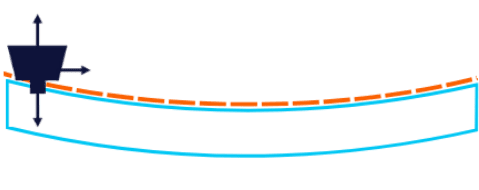
During the welding process with force control, the tool dynamically adjusts to the thermal distortions, maintaining constant contact with the workpiece. This adaptability ensures the tool shoulder remains in continuous contact with the surface, countering the thermal distortion and preserving the quality of the weld.
The importance of managing these deformations cannot be overestimated, and force control is pivotal in this regard. Consider the case of a 1-mm flatness defect:
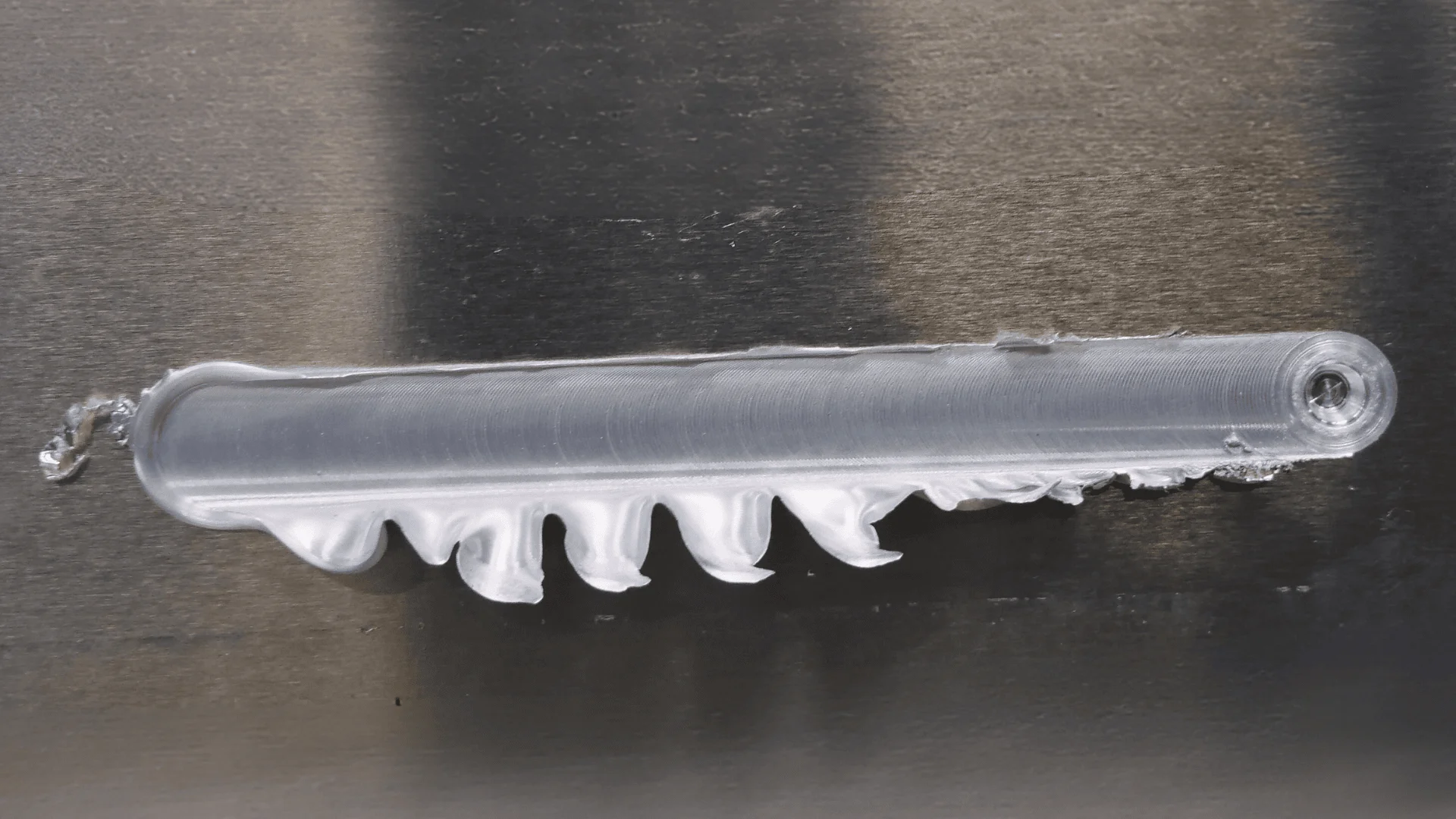
Welding without force control and with a positive plunge leads to the tool penetrating too deeply into the surface of the part, causing excessive flash, thinning of the workpiece, and a consequent reduction in mechanical strength.
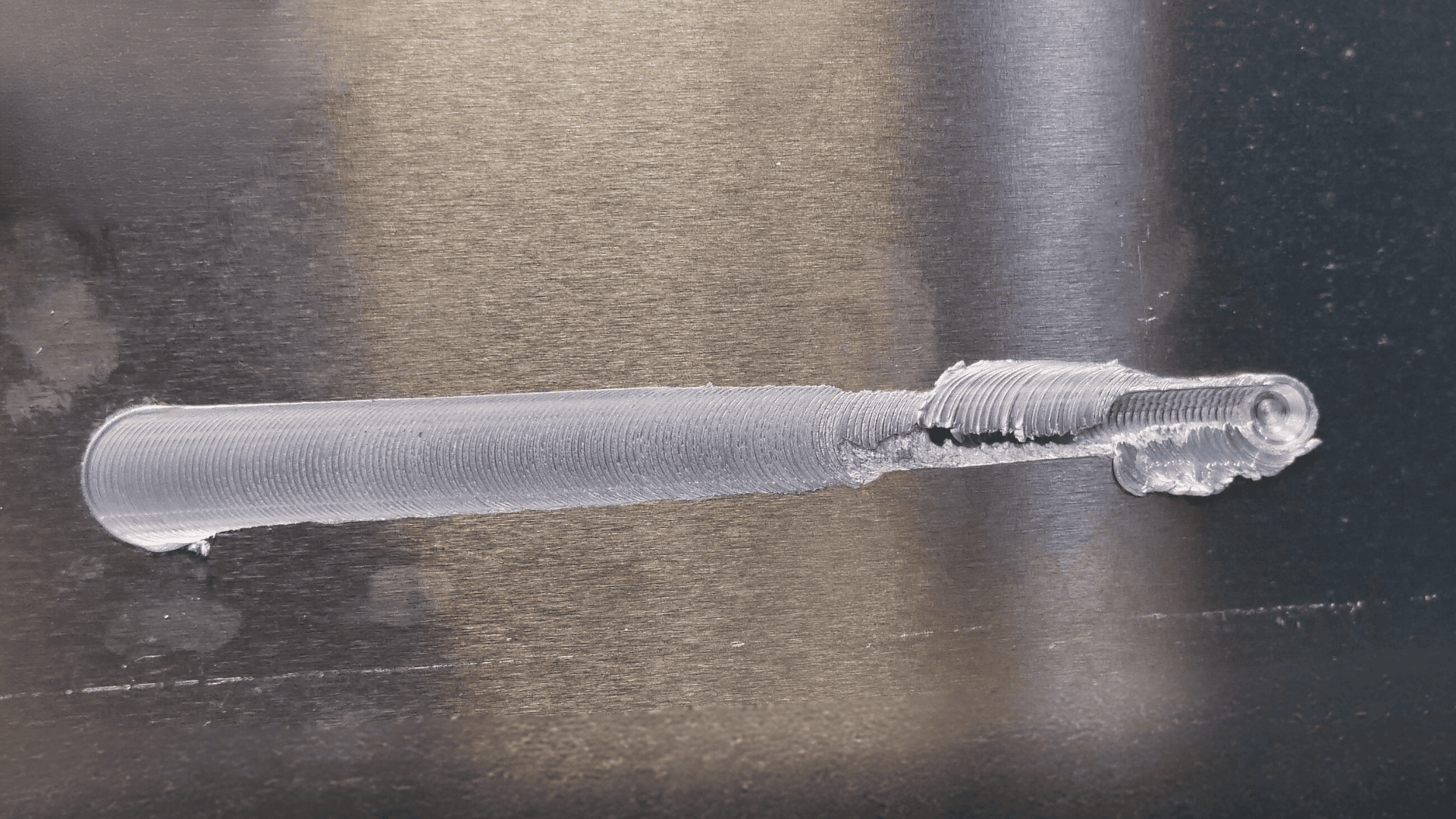
Welding without force control and with a negative plunge results in the tool losing contact with the part surface, introducing porosities or wormholes due to insufficient compactness.
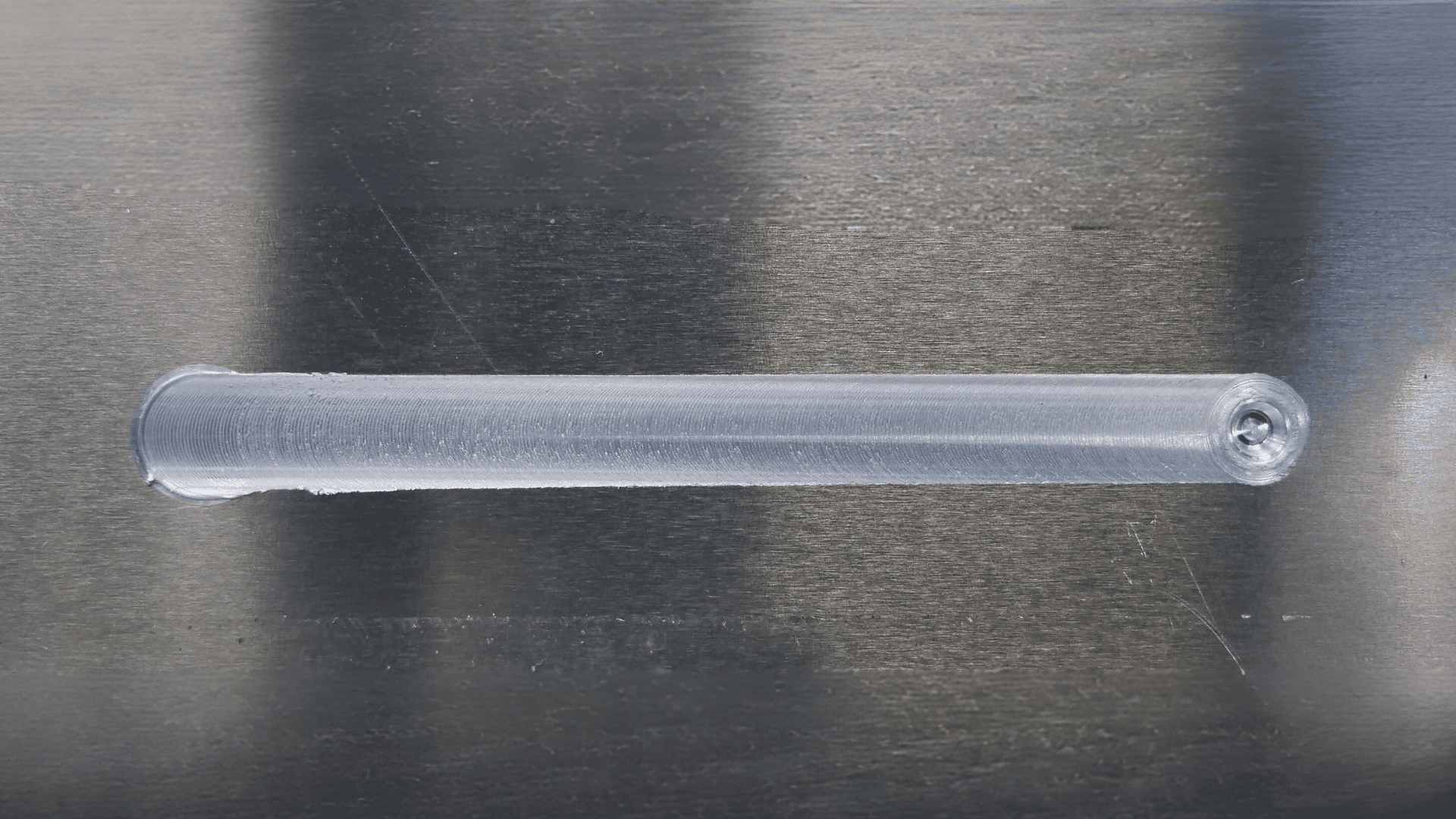
With force control, the constant contact between the FSW tool and the part surface is maintained despite a flatness defect of 1 mm, resulting in a defect-free and high-quality weld.
This detailed exploration underscores the critical role of force control in overcoming the challenges posed by part flatness and thermal distortion in FSW. By ensuring consistent contact between the tool and the workpiece, force control facilitates a process capable of producing high-quality welds, demonstrating the indispensable value of a dedicated FSW welding head equipped with this functionality.
Precision tool cooling: the path to superior FSW quality
In the field of friction stir welding (FSW), managing the temperature of the welding process is essential for securing high-quality welds. The ideal temperature range for welding varies by material, with each requiring precise control to ensure the integrity of the weld. For aluminium, the temperature must be maintained between 480°C (896°F) and 520°C (968°F), staying below its melting point of 600°C (1112°F). Straying outside these specific ranges results in significant issues.
Exceeding the optimal temperature range results in the FSW tool overheating, pushing the weld temperature beyond the melting point of the material. This creates porosities within the weld, leading to welds that fail to meet quality standards. Moreover, such overheating can also damage the CNC spindle, leading to costly repairs and downtime.
Therefore, tool cooling in FSW is not just beneficial but essential. It prevents the tool from overheating, thus avoiding damage to the CNC machine and ensuring the weld remains within the desired temperature range. To achieve a defect-free weld, the temperature must reach at least 70% of the melting point of the alloys being welded. This enables welding in the pasty state, facilitating solid-state joining that is free from defects.
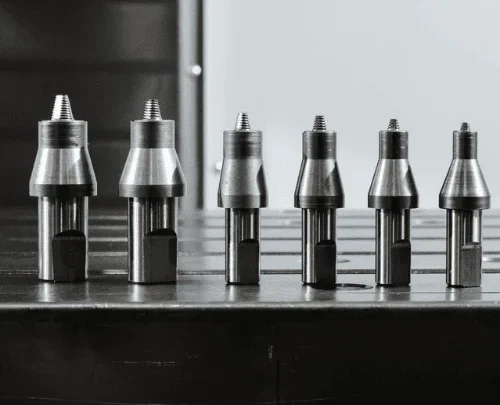
Traditional cooling methods, such as liquid spraying, are not viable during FSW since they reduce too much the temperature of the parts being welded, unfavorably affecting the temperature of the workpiece, thereby ensuring optimal conditions for welding. By maintaining the correct temperature, our equipment enables the production of high-quality, defect-free welds, underscoring the importance of tool cooling in achieving superior FSW results.
Thus, with our solution, we address this challenge with a closed-loop system inside our equipment. This system cools the tool efficiently without impacting the workpiece temperature, ensuring optimal welding conditions.
CNC protection: ensuring durability in FSW operations
Our solution is engineered to safeguard your CNC machine with four layers of protection: against welding temperatures, against excessive force during Friction Stir Welding (FSW), against overload conditions in FSW, and against vibrations induced by FSW.
Against welding temperature
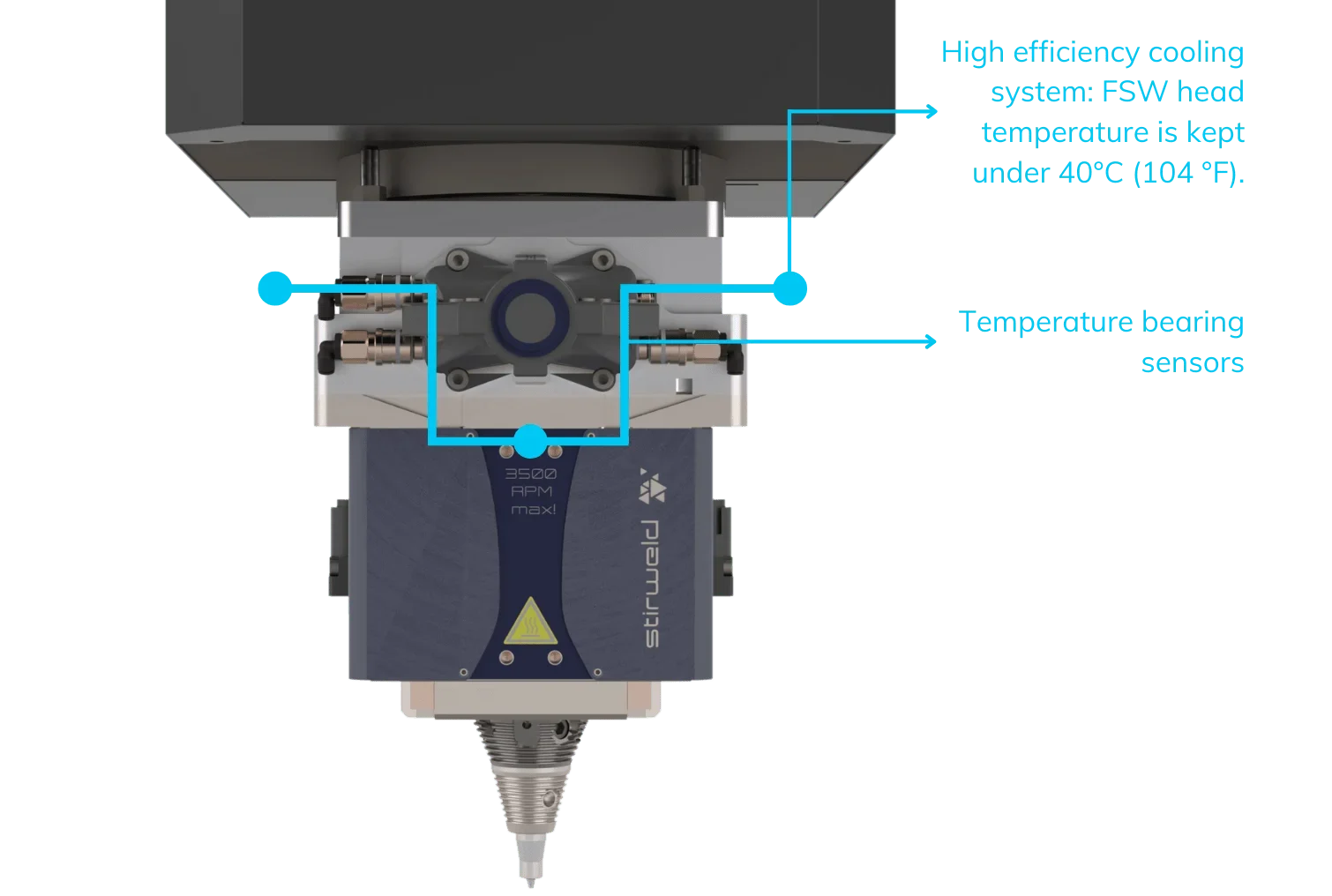
Against FSW excessive force
Why not modify the machine?
Modifying a CNC to include force control is highly challenging due to the need for significant mechanical changes and restrictions from proprietary controllers. This process is impossible in most of CNC.
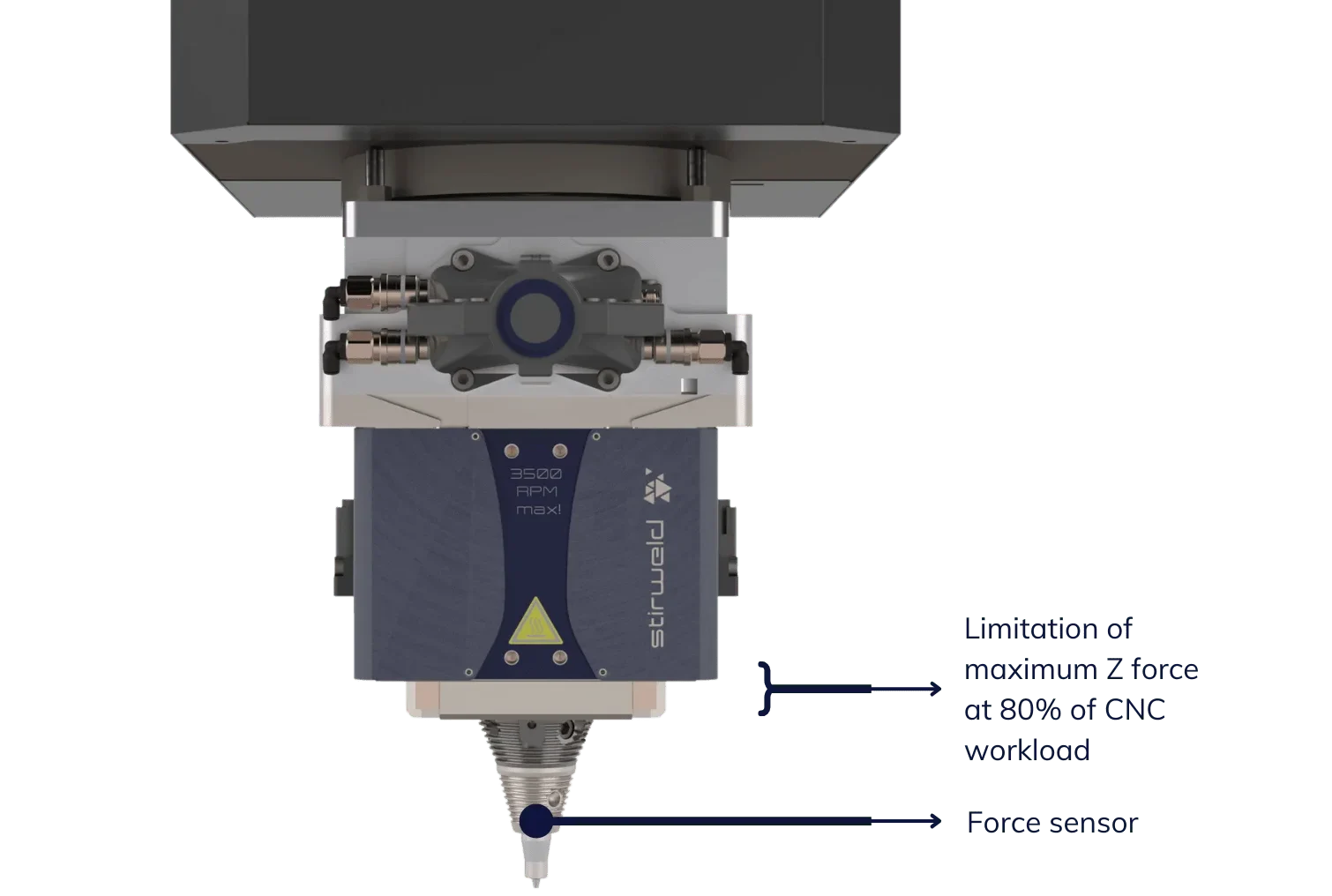
Against FSW load
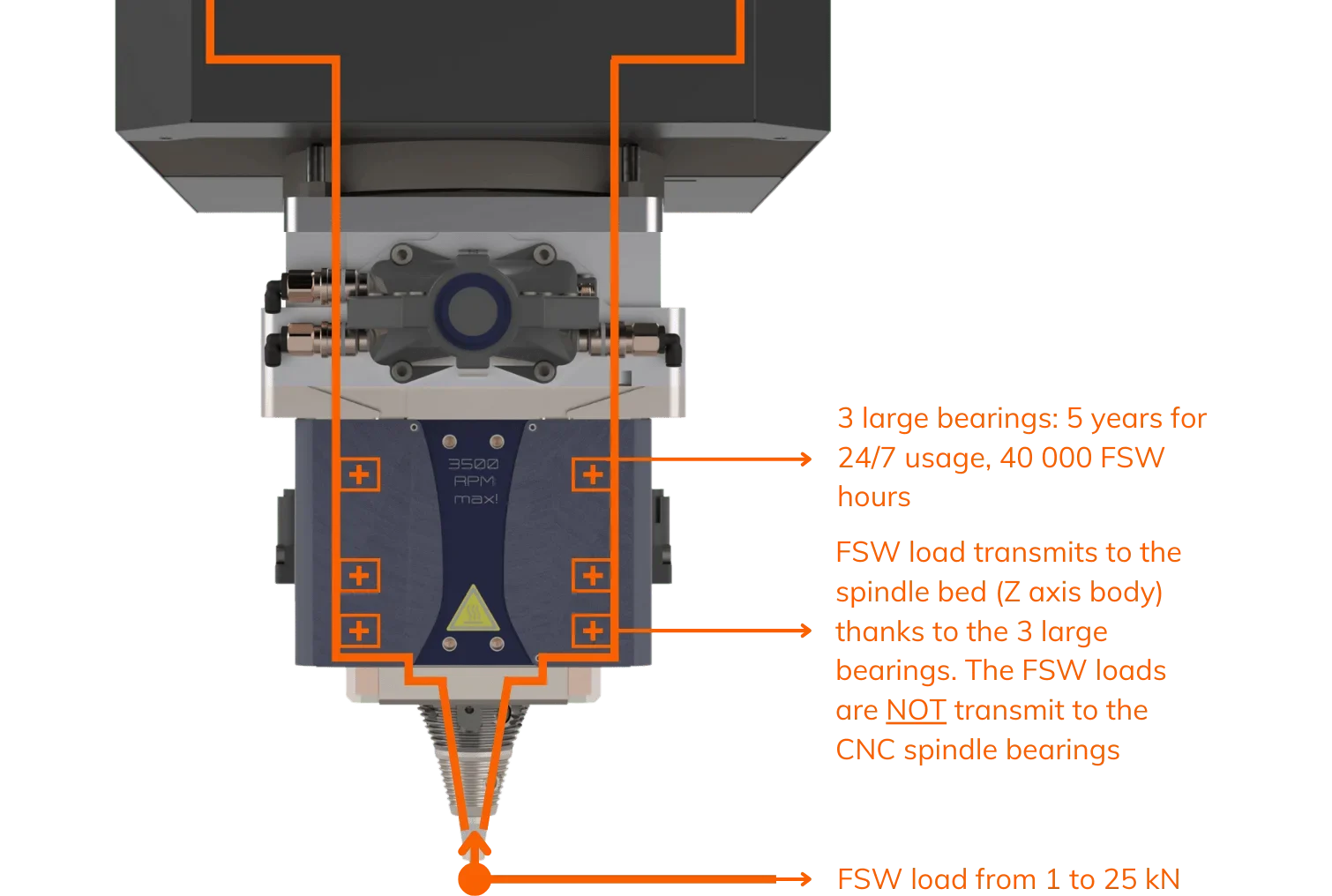
Against FSW vibrations
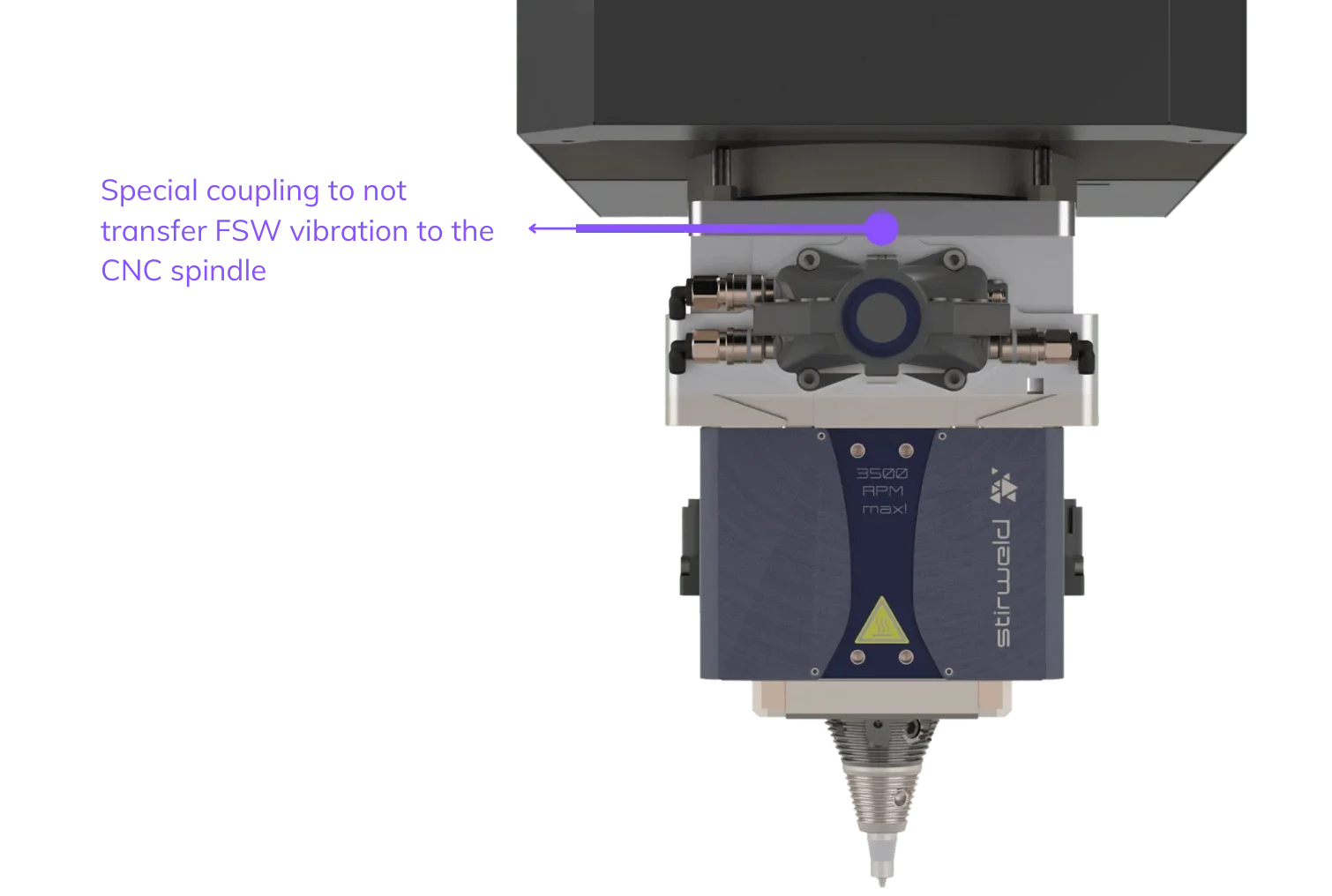
Force recording: revolutionizing FSW quality assurance
Force recording stands as a pivotal innovation in enhancing the quality of welds through precise force management. This technique plays a crucial role in achieving defect-free and superior-quality welds, a benchmark that Stirweld commits to by incorporating advanced sensor technology. Here’s how this approach elevates the welding process:
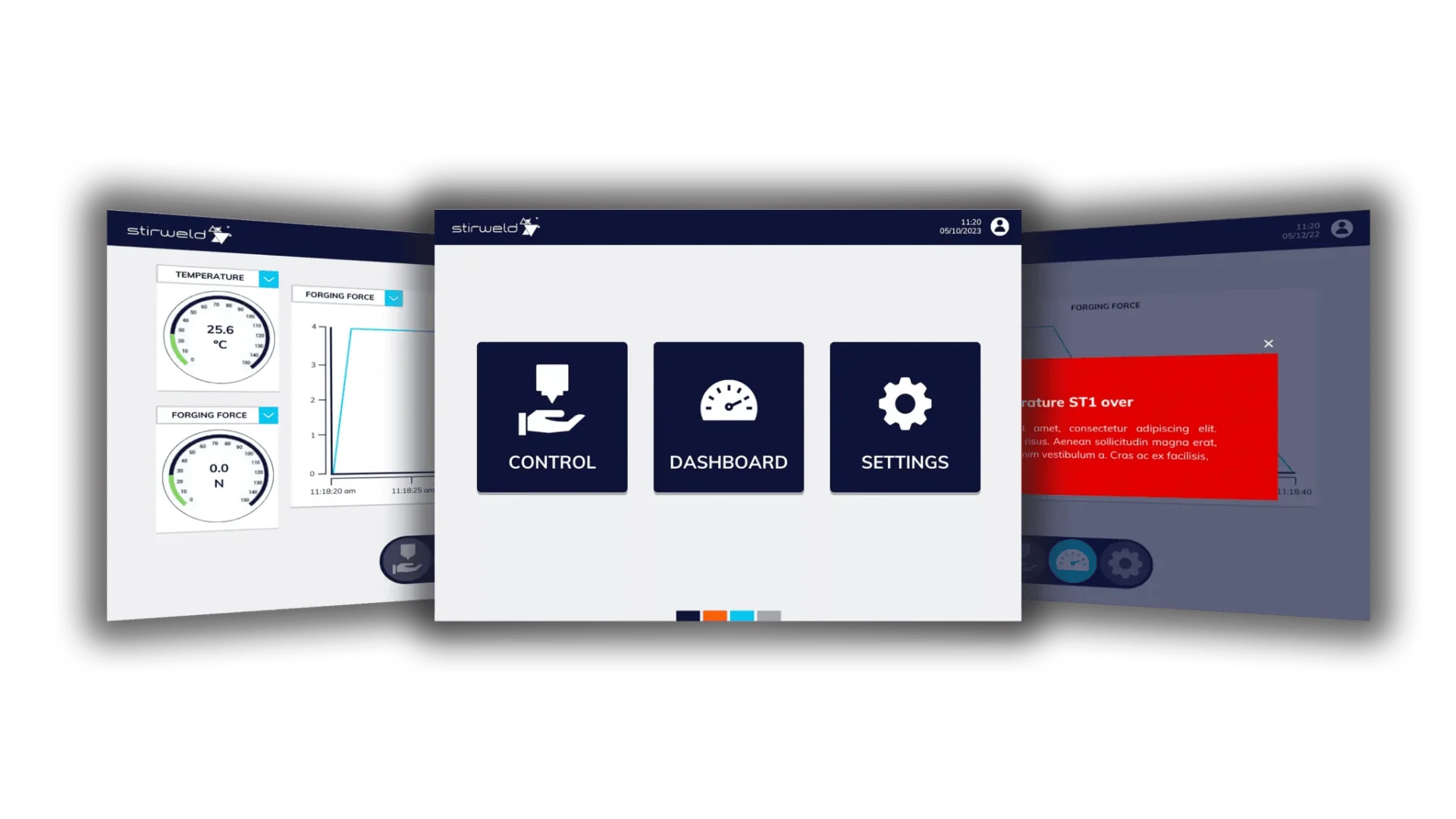
FSW head for CNC machine installations
In conclusion, the direct use of a CNC machining center for friction stir welding (FSW) without a dedicated head presents numerous limitations, from the requirement of perfect workpiece flatness to the inadequacy of force control, tool cooling, and the lack of protection against FSW forces. These challenges significantly impact the quality of the welds and the overall efficiency of production, underscoring the necessity of a specialized CNC FSW welding head.
Our advanced FSW head addresses these issues with indispensable features: force control, tool cooling, machine protection, and force recording. Each function is designed to overcome specific obstacles inherent in FSW, ensuring high-quality, defect-free welds, and prolonging the lifespan of your CNC equipment. From managing part flatness and thermal distortion with force control, maintaining optimal welding temperatures with tool cooling, to safeguarding your CNC machine against excessive force, load, and vibrations, our solution is engineered for excellence.
Furthermore, the integration of force recording technology enhances weld quality through real-time monitoring and analysis, offering a pathway to continuous improvement in your FSW processes.
Invest in the right tools to transform your CNC machining center into a versatile, high-performance welding station. Embrace the future of manufacturing with our dedicated FSW head, designed for precision, efficiency, and reliability.
Contact FSW experts
Take your welding operations to the next level – Contact us today to learn more about our innovative FSW solutions and how they can benefit your business.