Friction Stir Welding: a key technology for the future of e-mobility
In an ever-evolving world, where the pursuit of sustainable solutions has become the cornerstone of innovation, Friction Stir Welding (FSW) is increasingly establishing itself within the e-mobility industry. This technology, both revolutionary and subtle, is reshaping the manufacturing and assembly paradigms of electric vehicles, offering tangible solutions to the challenges of our time. FSW, a technique where heat generated by friction and mechanical stirring joins metals without melting them, opens up new paths for the production of components that are lighter, stronger, and more eco-friendly. It is not just a welding method; it’s a technological breakthrough that enables the creation of electric vehicles that are more efficient, safer, and environmentally friendly.
But why is this so crucial today? And how does this technique fit into the grand journey of e-mobility? This article takes you through the intricacies of Friction Stir Welding, exploring its transformative impact on electric vehicle industry and revealing why this technology could very well be the missing link to a more sustainable future.
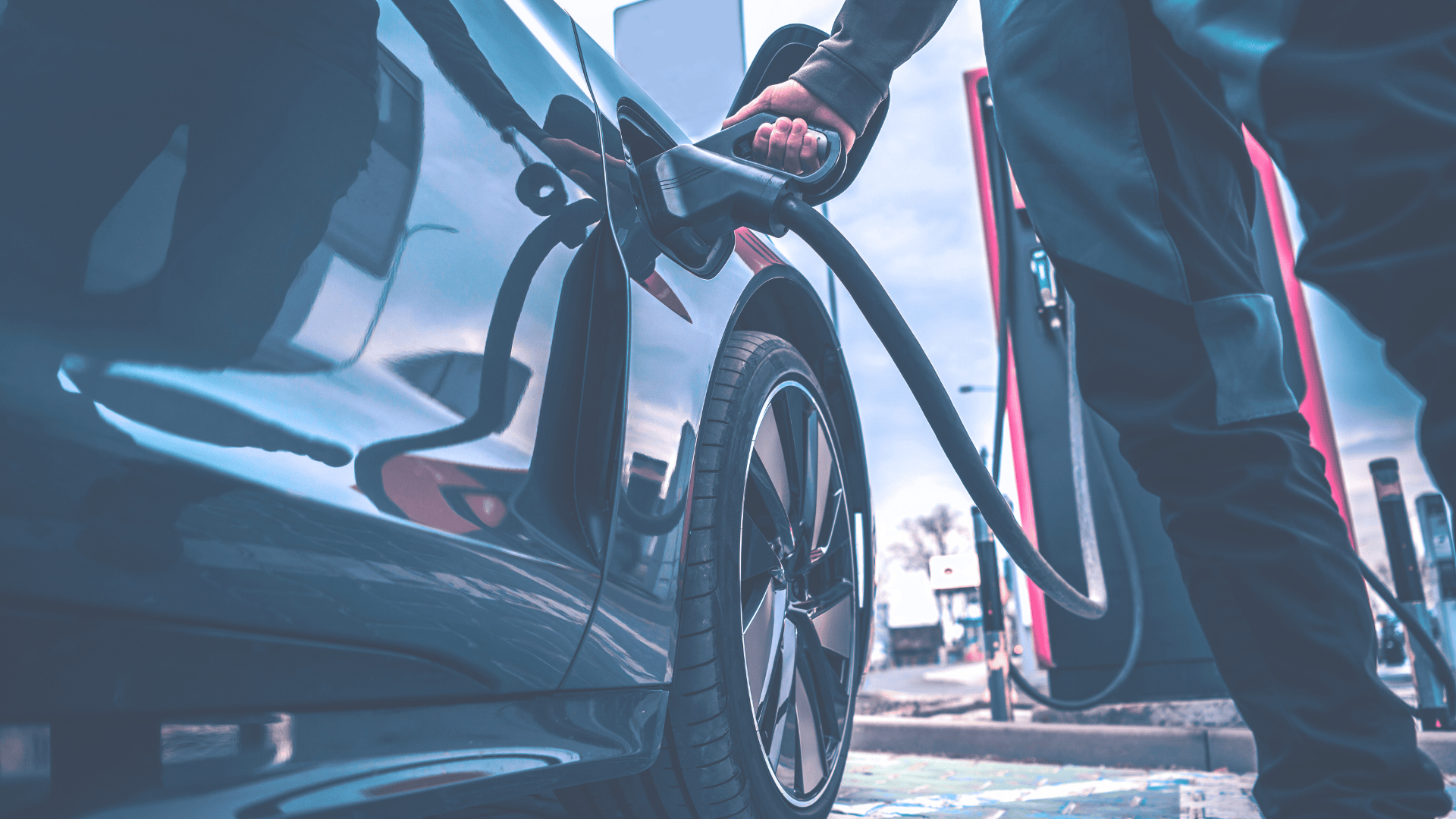
E-mobility and its current challenges
E-mobility, or electric mobility, refers to the use of vehicles powered by electric engines, primarily fueled by rechargeable batteries, as an alternative to traditional internal combustion vehicles. The main goal of e-mobility is to cut down on greenhouse gas emissions, reduce air pollution in urban areas, and lessen our dependence on fossil fuels.
The current state of the e-mobility market
The e-mobility market has seen exponential growth over the past decade, driven by significant technological advancements, decreasing battery costs, and increased government support through subsidies, tax incentives, and regulations favoring low-emission vehicles. Major markets, such as Europe, China, and the United States, have experienced a rapid increase in the number of electric vehicles on the road, alongside the development of charging infrastructure and a growing consumer awareness of environmental issues. The range of available electric vehicles has significantly expanded, with every major automobile manufacturer now having at least one electric model in their lineup.
Future Outlook
The future outlook for e-mobility appears promising and is characterized by several key trends: accelerated adoption of electric vehicles, expansion of charging infrastructure, technological innovations (improved battery capacity, increased range), and environmental regulations.
Manufacturing and assembly challenges in e-mobility
The manufacturing and assembly challenges in e-mobility are crucial for the successful development and marketing of electric vehicles (EVs) that meet the growing expectations for performance, durability, and environmental impact. Here are the main challenges:

Vehicle lightweighting

Material durability
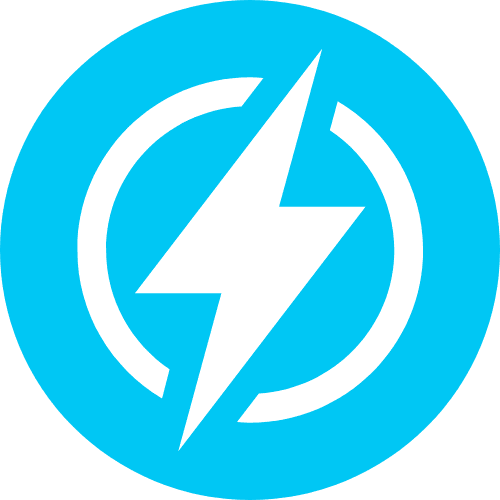
Energy efficiency
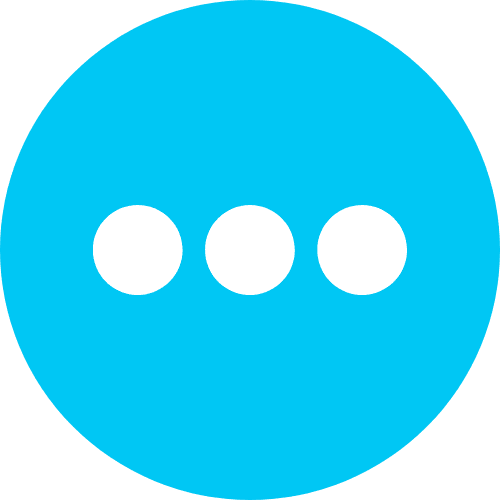
Other challenges
To meet these challenges, the e-mobility industry is investing in research and development of new manufacturing technologies, advanced materials, and innovative assembly processes. Friction Stir Welding offers significant advantage lightweight and heterogeneous materials, contributing to both lightness and strength of electric vehicles.
The impact of Friction Stir Welding on e-mobility
How does Friction Stir Welding (FSW) meet the challenges of e-mobility?
Friction Stir Welding (FSW) is an innovative welding technology that is particularly well-suited to the e-mobility industry, offering solutions to several key challenges related to the manufacturing and assembly of electric vehicles (EVs). Here is how FSW specifically addresses these challenges:
Vehicle weight reduction
Enhancing energy efficiency
Increased safety and durability of components
In summary, Friction Stir Welding effectively meets the challenges of e-mobility by facilitating the production of vehicles that are lighter, more energy-efficient, safer, and more durable. This technology represents a significant advancement in the field of electric vehicles, offering substantial benefits for component manufacturing.
Concrete examples of FSW application in e-mobility
Stiffened panels
Stiffened panels play a crucial rôle in the construction of vehicle floors and battery compartment structures. Given that they are subject to significant mechanical stresses, it’s viral that their assembly is both robust and durable. Friction Stir Welding (FSW) stands out particularly in the assembly of large panels. This technique allows overcoming size constraints, especially for aluminium profiles that must be less than 400 mm in width. With FSW, these profiles can be efficiently welded end to end, thus breaking traditional limitations.
Beyond overcoming these dimensional limits, FSW gives the panels increased lightness since this process does not require the addition of extra material to achieve the weld. This characteristic is particularly beneficial for electric and hybrid vehicles, whose reduced weight results in lower energy consumption.

Heat exchangers in cast aluminium
Heat exchangers, crucial for cooling electronic components in electric and hybrid vehicles, are made from cast aluminium parts. Their assembly requires special attention to ensure perfect sealing, optimal mechanical strength, and low manufacturing costs. FSW stands out for its excellent ability to create hermetic and resistant joints, successfully passing leak tests. Thanks to the superior quality of the welds produced by FSW, the need for screws in the assembly of components is reduced, thus offering significant time and cost savings for manufacturers during the production process.
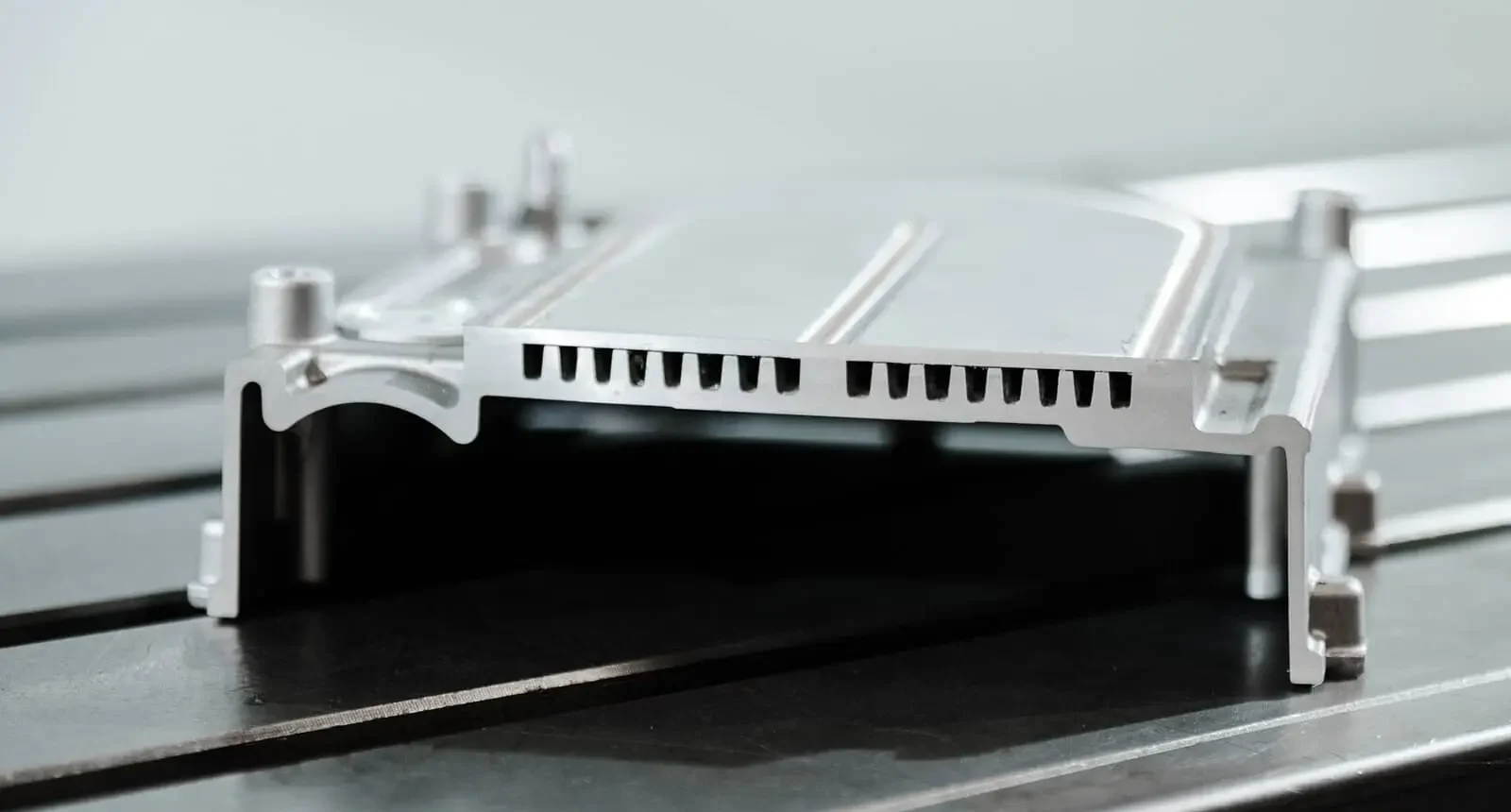
Battery trays
Battery trays, crucial elements for holding and securing the batteries in electric vehicles, require optimal electric conductivity. FSW is particularly suited to preserving this essential characteristic during the assembly of battery trays; This efficiency is due to the high quality of the welded joints and the fact that the melting point of the material is not reached. Moreover, as a cold-welding technique, FSW avoids damaging electrical components during the process, thus preserving their integrity and functionality.

Engine blocks
FSW is also used in the production of engine blocks for electric vehicles. Like battery trays, these are made from aluminium and steel alloys. FSW proves to be the most suitable technique for efficiently assembling these materials. Another advantageous feature of FSW is its versatility, allowing for welding in various configurations. This makes it particularly suitable for creating components with complex geometry, like engine blocks, which often need to adopt unique shapes to integrate different elements.
Chargers for electric vehicles
The production of chargers is a critical issue for vehicle manufacturers. Friction Stir Welding offers the ability to precisely adjust every aspect of the welding process. This allows operators to refine and closely examine the quality of the welded joints, thus ensuring the reliability and efficiency of the manufactured chargers.
Future prospects of FSW in e-mobility
Innovations in the field of FSW
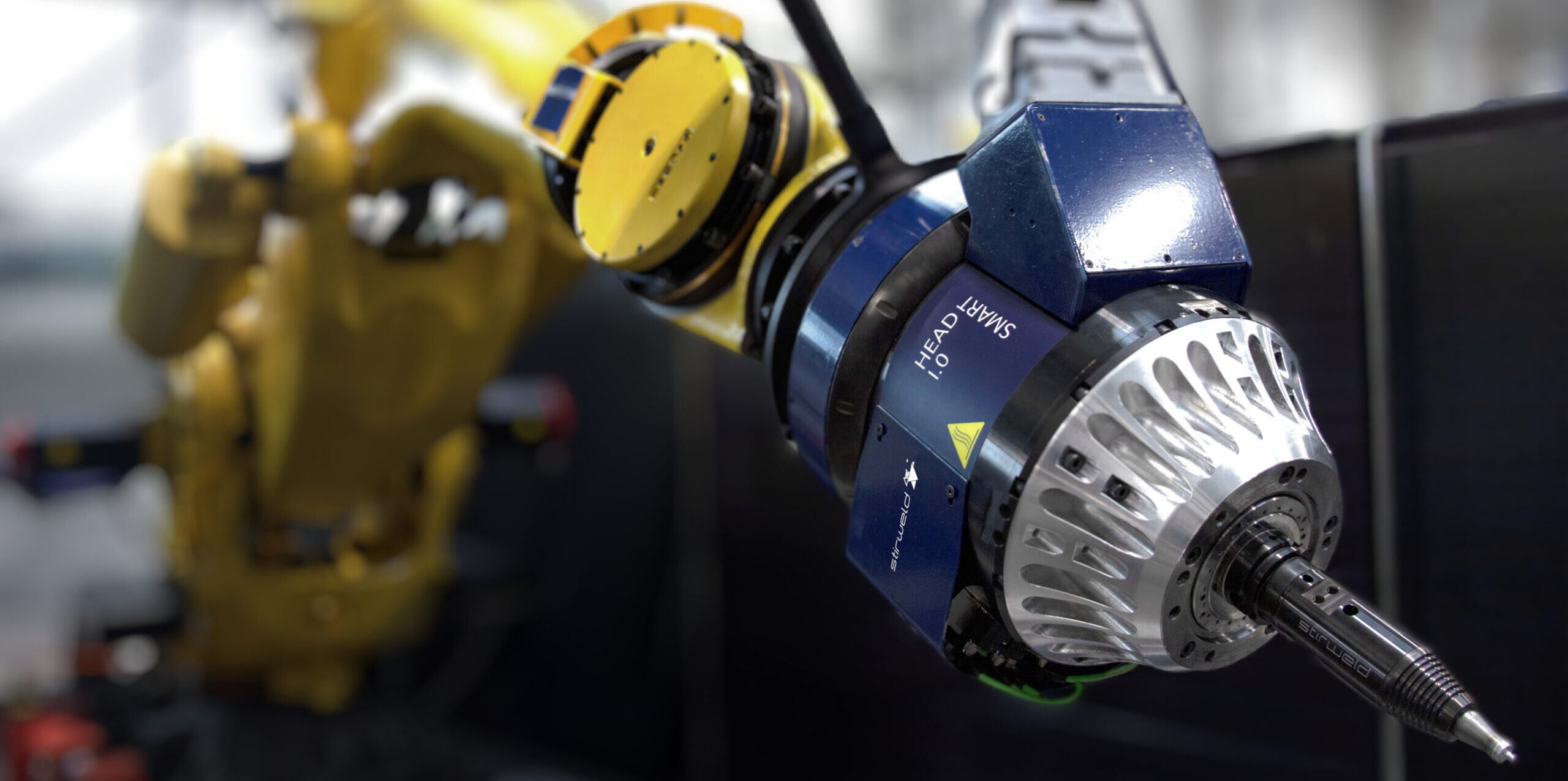
FSW spindle for robots
The integration of FSW spindles for robots in the FSW process opens up the way for greater flexibility and precision in welding. This allows for complex welds on three-dimensional shapes, ideal for electric vehicle components with specific geometries, such as battery trays or vehicle frames.
Controlled temperature FSW
The development of controlled temperature FSW techniques, such as our Smart Head equipped with an intelligent tool holder, enables better management of joint quality by precisely adjusting the temperature during welding. This proves especially beneficial for heat-sensitive materials, thus ensuring the reliability and performance of EV components.
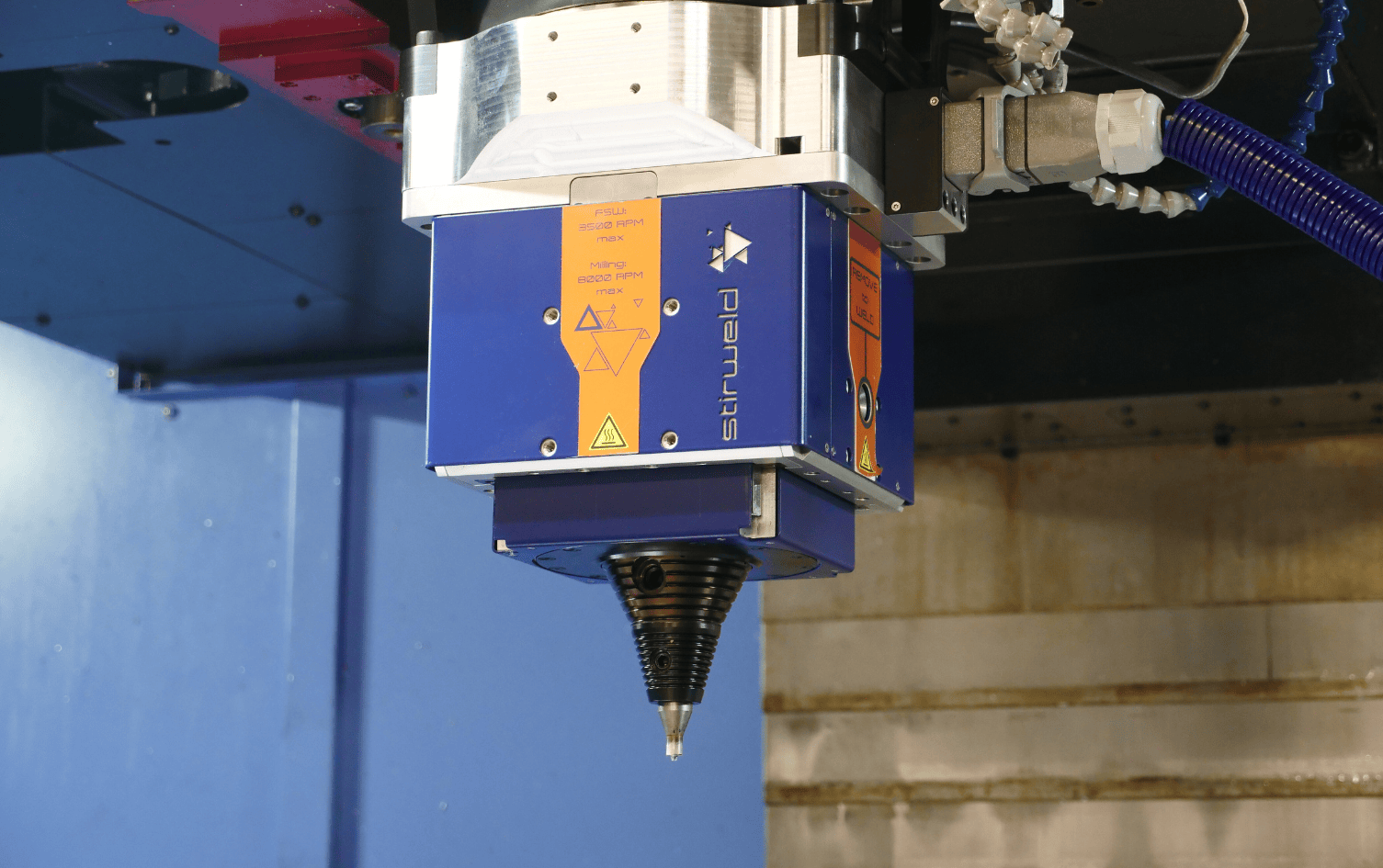
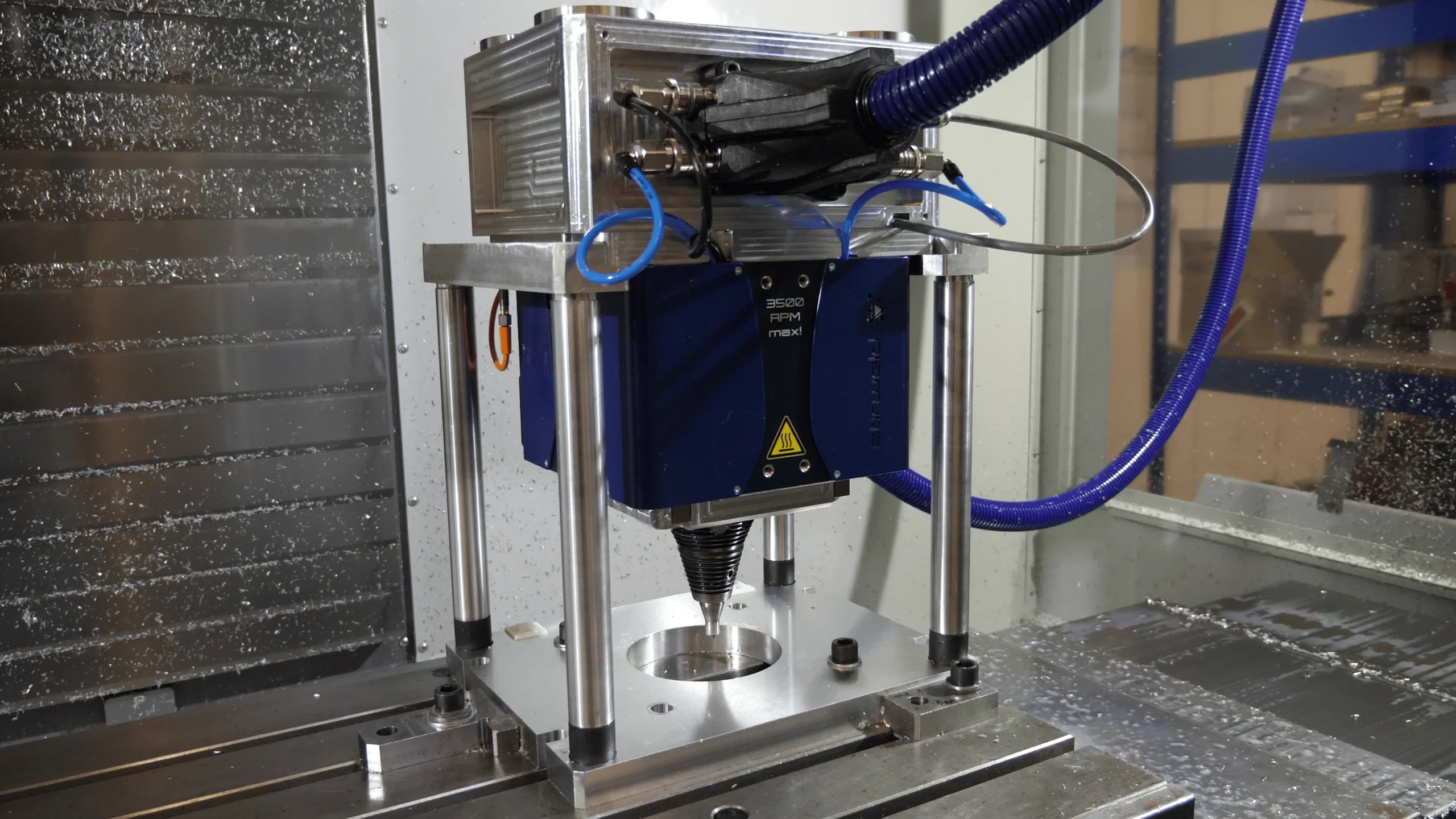
Automatic FSW welding operations
Thanks to equipment like the automatic FSW head changer, a machining center transforms into a true hybrid machine that integrates both welding and machining operations. This will significantly boost the productivity of the machine through quick and seamless transitions between these two operations, considerably reducing downtime.
Multi-material FSW welding
The advancement in FSW techniques for joining different material combinations (for example, aluminium to steel) without compromising the joint quality opens new possibilities for using optimized materials in EV manufacturing, thereby contributing to the lightness and the energy efficiency of vehicles.

Growth potential of FSW in the e-mobility sector
The growth potential of FSW in the e-mobility sector is significant and looks promising for several reasons. This technology provides unique advantages that directly address the needs and challenges of manufacturing electric and hybrid vehicles. Here are the key factors contributing to its growth potential:
FSW is well-positioned to play a role in the future development of the e-mobility sector, offering innovative solutions for the manufacturing of lighter, more efficient, and more durable vehicles. Its growth potential is closely linked to the evolving market needs and the continuation of innovation in manufacturing processes.
In summary, Friction Stir Welding (FSW) emerges as a revolutionary technology, ready to meet the unique challenges posed by the rapidly expanding e-mobility sector. Thanks to its ability to produce high-quality joints, its versatility in processing various materials, and its significant contribution as a key pillar in the quest for more sustainable mobility.
Beyond its technical and economic advantages, the adoption of FSW demonstrates the commitment of manufacturers to innovation and sustainability, aligning their production processes with the increasing expectations of consumers and global ecological imperatives. As the e-mobility sector continues to grow, FSW is not only ready to meet this demand but also drive the industry towards new horizons of efficiency and environmental respect.
Lead with Innovation in E-Mobility
Take the first step towards the future, today. Contact us to explore together the infinite possibilities offered by FSW. Your leadership in e-mobility starts here and now.