How much will it cost you to weld your part by FSW?
Friction Stir Welding costs compared with other processes
FSW is a leading way of achieving better and more efficient manufacturing solutions, than traditional welding methods. As the industries continue to search for ways of cutting down on the production costs while at the same time achieving high quality standards, there is the need to consider new welding techniques. FSW has certain advantages over conventional methods like TIG, MIG, brazing, and Electron Beam Welding (EBW). This article aims to explain how FSW does not only enhance the quality of the welds but also cuts down on the costs that are associated with the welding of difficult alloys and intricate configurations. Thus, the direct and indirect cost benefits of FSW can be analyzed to explain the increasing adoption of this technology in industrial settings where efficiency and cost competitiveness are critical.
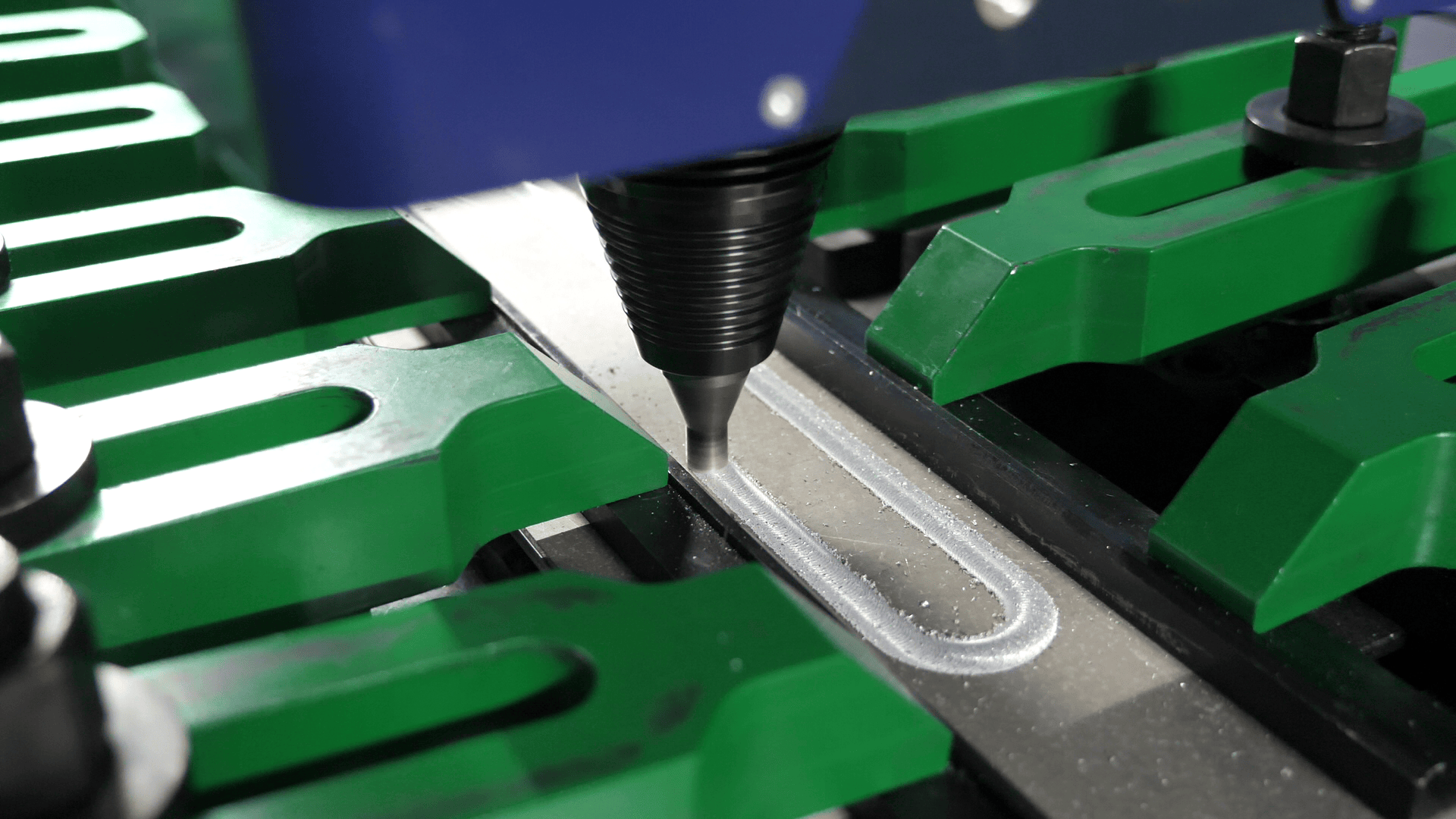
FSW process: how does it work?
Friction Stir Welding (FSW) is a solid state joining method which has changed the face of welding by welders and engineers. Unlike other forms of welding like fusion welding, FSW does not involve the melting of the base metal hence making it strong, ductile and having a good weld interface. Friction Stir Welding was first discovered by The Welding Institute (TWI) in the United Kingdom in 1991 and has since been used in aerospace, automotive and shipbuilding industries, among others.
The process of Friction stir Welding (FSW)
Friction Stir welding employs a non-consumable rotating tool to join materials without melting them. The rotation of the tool generates heat through friction, softening the material into a plastic-like state that allows it to be mixed at the joint. As the tool moves along the joint line, it stirs the material, facilitating a solid-state bond as the material cools and re-solidifies behind the tool.
Advantages of Friction Stir Welding
Comparred to conventional welding or laser welding, FSW offers several advantages. It creates joints with high mechanical strength and compressive force, with minimum distortion due to no melting. Additionallyit enables the joining of dissimilar metals, e.g., copper and aluminium alloys.
It also eliminates the need for a filler metal, flux, or shielding gas, thereby making the process more environmentally friendly. Furthermore, FSW technique minimizes typical fusion welding defects such as porosity or cracking. FSW can be fully automated and integrated into existing CNC machines, providing a cost-effective and flexible solution for industrial production.
Applications of Friction Stir Welding in aluminium and metal structures
This innovative welding technique is widely used in industries where material integrity is crucial, such as aerospace for joining aluminium in aircraft structures, and automotive for assembling lightweight alloy components. The ability of the FSW to maintain the properties of the base materials while providing a strong joint makes it valuable for manufacturing light and efficient structures: die cast, cold plate, stiffened panel, aluminium tank, flange builder, vacuum chamber, mounting bracket, battery tray, etc.
Comparing Friction Welding to traditional welding techniques
Friction Stir Welding vs. TIG welding
Friction Stir Welding (FSW) significantly surpasses TIG welding, particularly when working with aluminium alloys or other challenging material combinations. Unlike TIG welding, FSW does not involve the melting of the material, thus preventing the common defects associated with the fusion welding molten pool, such as porosity, burn-off, and thermal distortion. This feature helps in preserving the intrinsic mechanical properties and microstructure of aluminium alloys, ensuring the integrity and strength of the weld interface.
Furthermore, FSW is a more ecological option since it does not require filler material, welding flux, or emit harmful gases, and generates heat through mechanical friction instead of electrical arcs. This combination of advantages makes FSW a more reliable and suitable choice for high-strength applications where precision, tensile strength, and durability are crucial.
Friction Stir Welding vs. MIG welding
FSW offers a superior alternative to MIG welding by eliminating the need to melt the material during the joining process. This characteristic not only minimizes common welding defects like porosities and cracking but also preserves the original properties of the alloys being joined. As a result, FSW provides a more economical and eco-friendly solution, reducing waste and avoiding the use of additional gases and materials. This makes FSW particularly advantageous for modern industrial challenges, where cost-efficiency and environmental sustainability are increasingly important alongside reliable and robust welding performance.
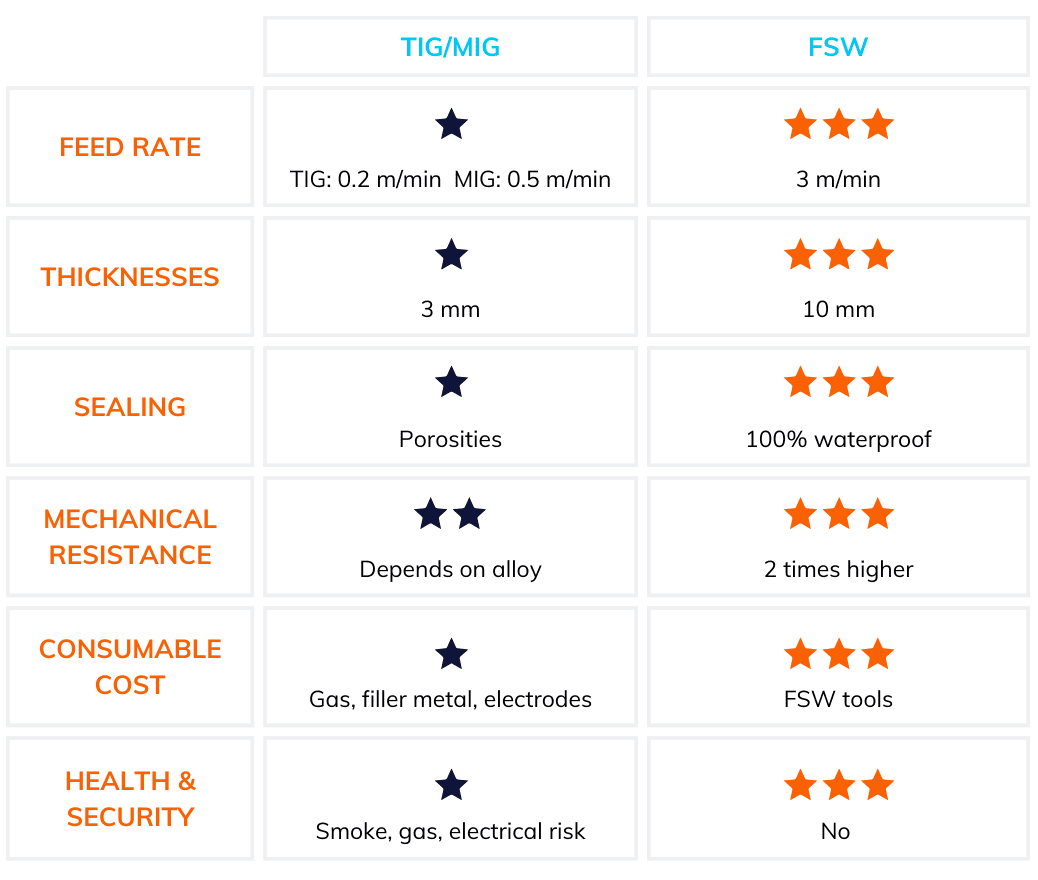
Friction Stir Welding vs. Brazing
Friction Stir Welding significantly outshines brazing in many aspects of industrial applications, especially when dealing with challenging alloys. FSW minimizes thermal distortion and stress, typically associated with the high temperature of brazing. This process creates stronger and purer joints by mixing the materials directly without melting them and without the need for any consumables such as filler metals or fluxes. As a result, FSW emerges as a cost-effective and eco-friendly choice, eliminating the environmental load and reducing material costs, making it highly suitable for high precision and high-strength welding in industrial settings.
Friction Stir Welding vs. EBW
FSW offers distinct advantages over Electron Beam Welding (EBW) across several key areas of industrial fabrication. Unlike EBW, FSW does not require vacuum conditions and can be performed in open air, making it simpler and less costly in terms of equipment and operation. FSW facilitates the joining of thicker materials more easily and is inherently safer, as it does not involve X-ray emissions, a notable concern with EBW. Additionally, FSW supports a wider range of materials and ensures clean, high-quality welds without the risk of contamination. These attributes establish FSW as a superior choice in industrial welding, where versatility, safety, and cost-effectiveness are paramount.
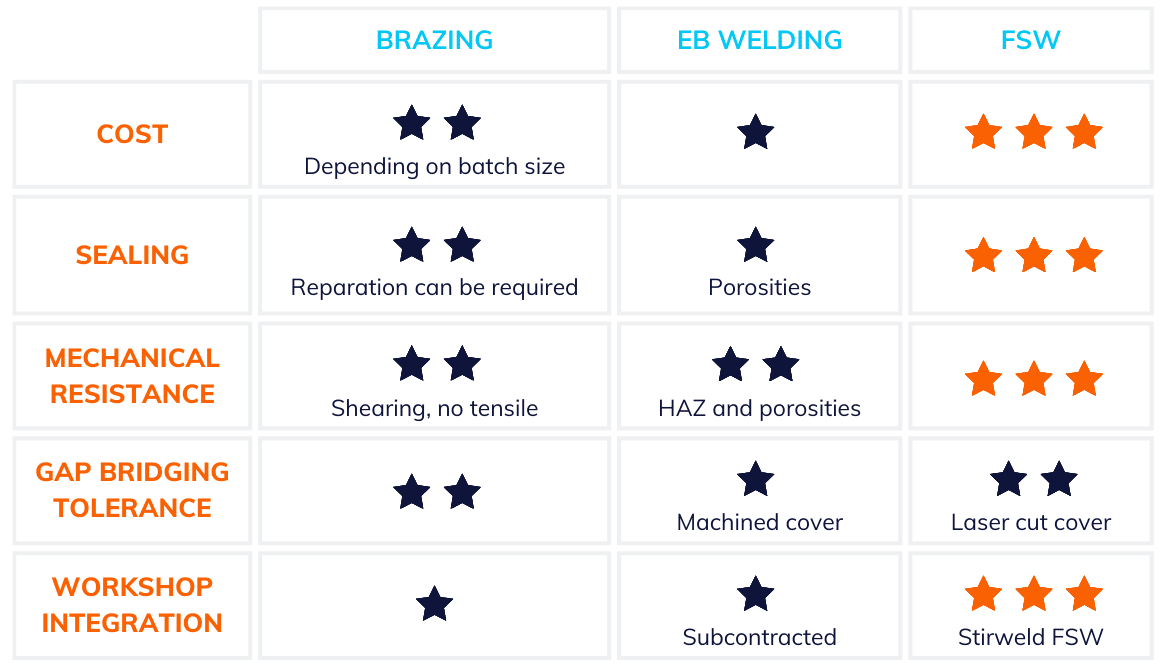
Economic insights: how much does welding cost?
Investment cost: FSW vs. MIG, TIG, EBW and vacuum brazing
FSW head for CNC machine | Incorporating a FSW head into CNC cost less than €100,000; significantly cutting costs versus dedicated machines, with FSW tools as the sole consumable and guaranteed quality eliminating non-conformity expenses. |
TIG/MIG equipment | Prices range from €2,500 to over €15,000, with higher consumable costs and defect risks, leading to significant non-quality expenses. |
Electron Beam Welding (EBW) | Small to medium EBW systems cost €300,000 to €500,000 for research or limited production, with high-volume industrial setups exceeding €1 million. |
Vacuum brazing furnace | The purchase of a vacuum brazing furnace can range from €200,000 for simpler, smaller models to over €1,000,000 for large-capacity or specialized equipment. |
Operational costs: FSW vs. MIG, TIG, EBW and vacuum brazing
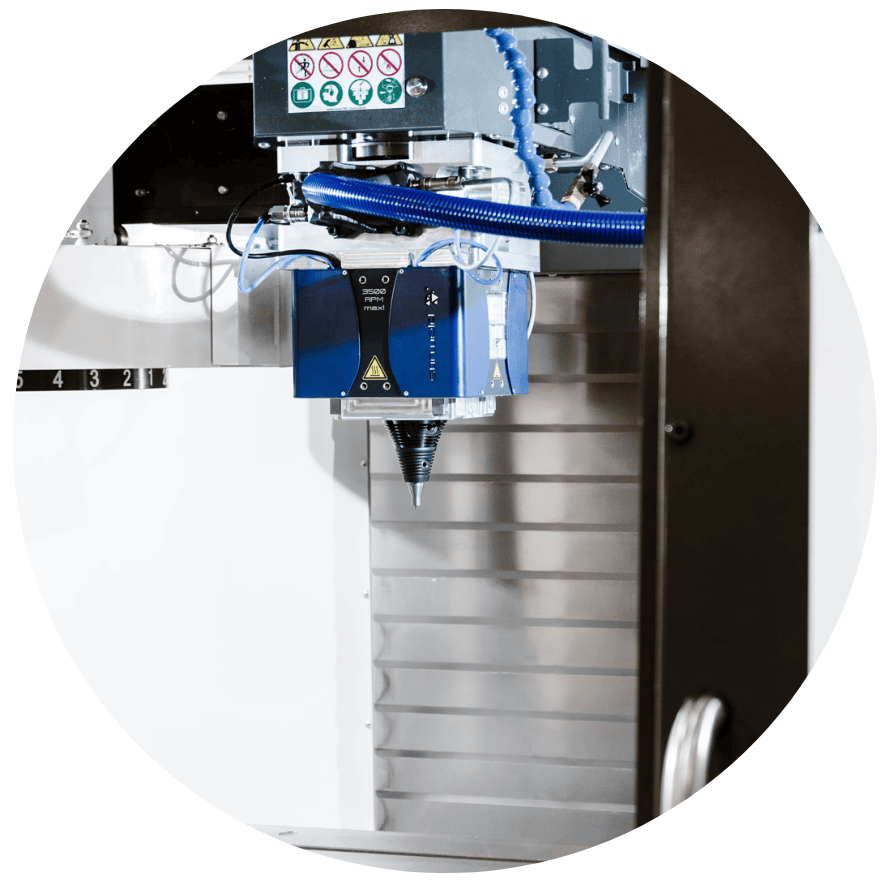
Operational costs of Friction Stir Welding
Friction Stir Welding (FSW) offers several operational cost advantages that make it a compelling choice for efficient manufacturing processes:
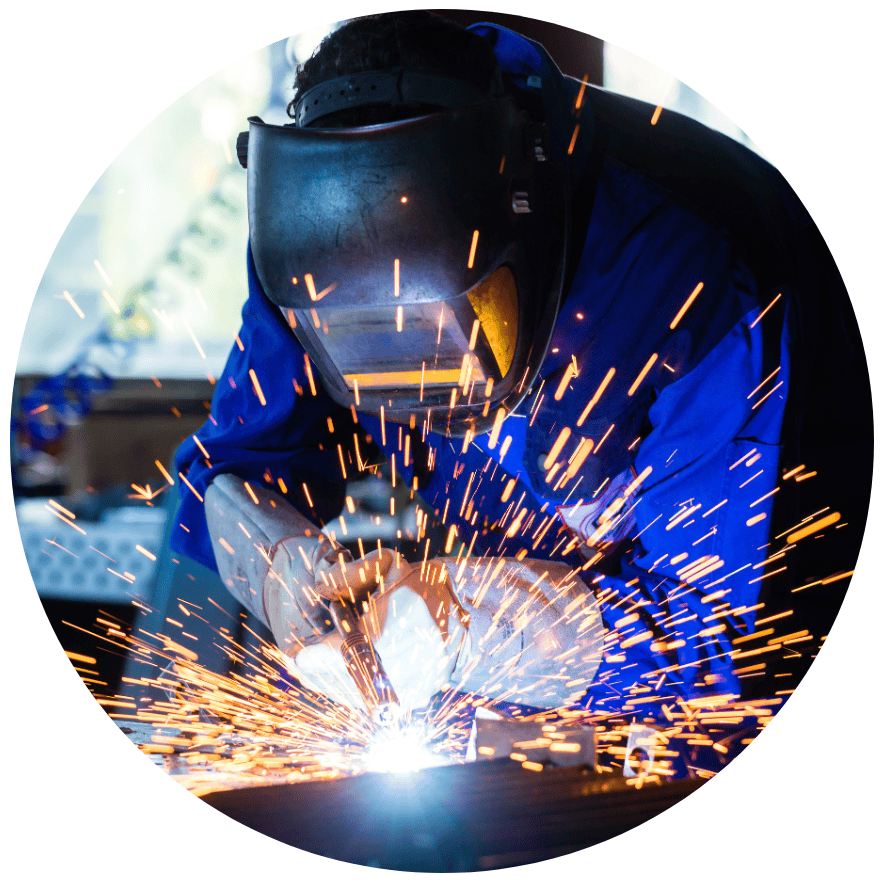
Operational MIG and TIG welding costs
TIG and MIG welding are popular manufacturing process, each with its own set of operational costs that impact overall efficiency:
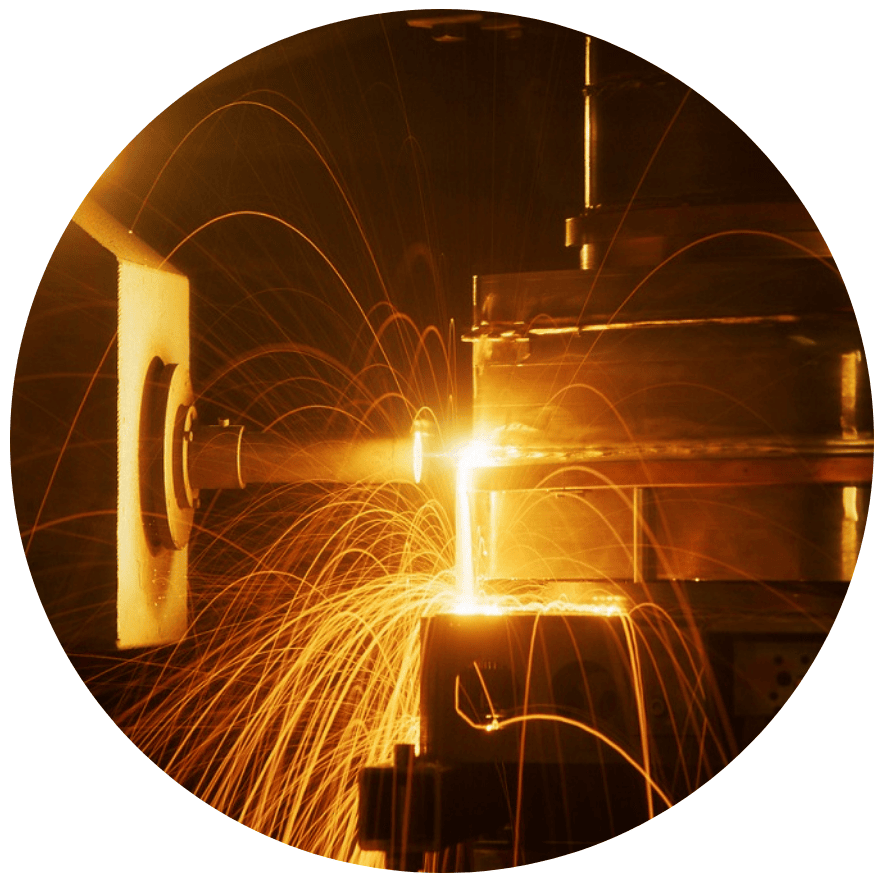
Operational costs of EBW – Electron Beam Welding
Electron Beam Welding (EBW) is a sophisticated process that, while effective, incurs specific operational costs crucial for its performance:
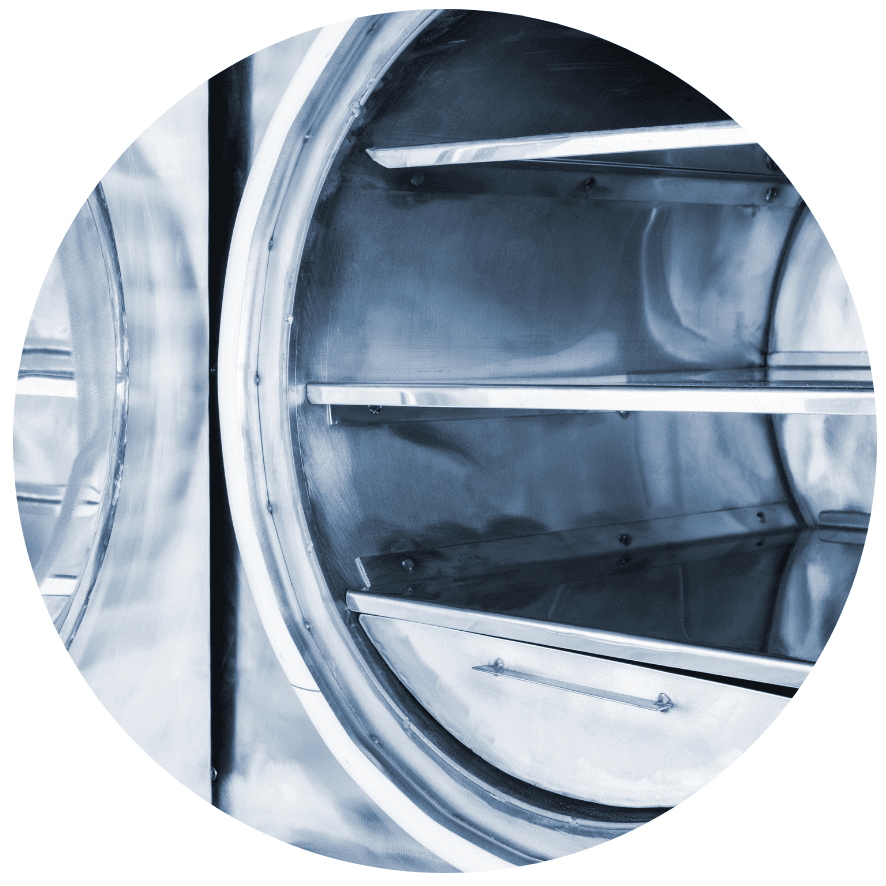
Vacuum brazing: operational costs
Vacuum brazing is controlled and precise joining technique that, while offering high-quality results, involves several operational costs that must be carefully managed:
Clamping system cost: FSW vs. MIG, TIG, EBW and vacuum brazing
FSW head for CNC machine | It highly depends on part complexity and can go from standard elements to fully automated dedicated clamping device. It must include backing if the part is not self-supported, to take over Z load, and mechanical stops to prevent it from moving. |
TIG/MIG | Very simple clamping system with standard elements, as no mechanical loads involved. Dedicated clamping system can sometimes be involved. |
Electron Beam Welding (EBW) | The gap requirement is very tight. Then apart from the part preparation process, it needs an effective clamping system to keep the gap bridging low. |
Vacuum brazing | The gap requirement is very tight. Then apart from the part preparation process, it needs an effective clamping system to keep the gap bridging low. |
Case study: cold plate in aerospace sector
Cold plate manufacturing for one plane (12 units) – Financial analysis:
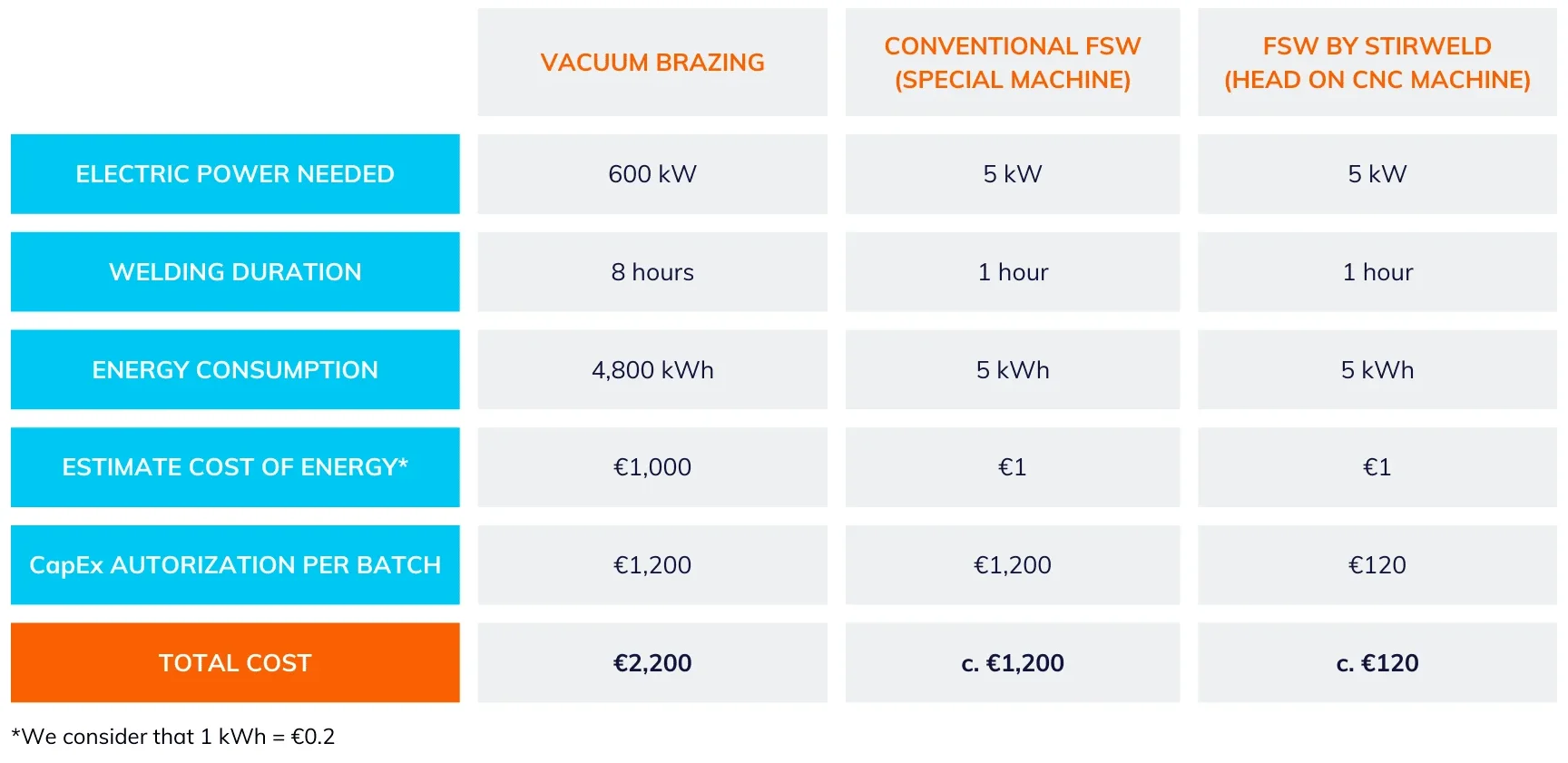
Stirweld is ~10x less expensive compared to conventional techniques.
Cold plate manufacturing for one plane (12 units) – Environmental analysis:
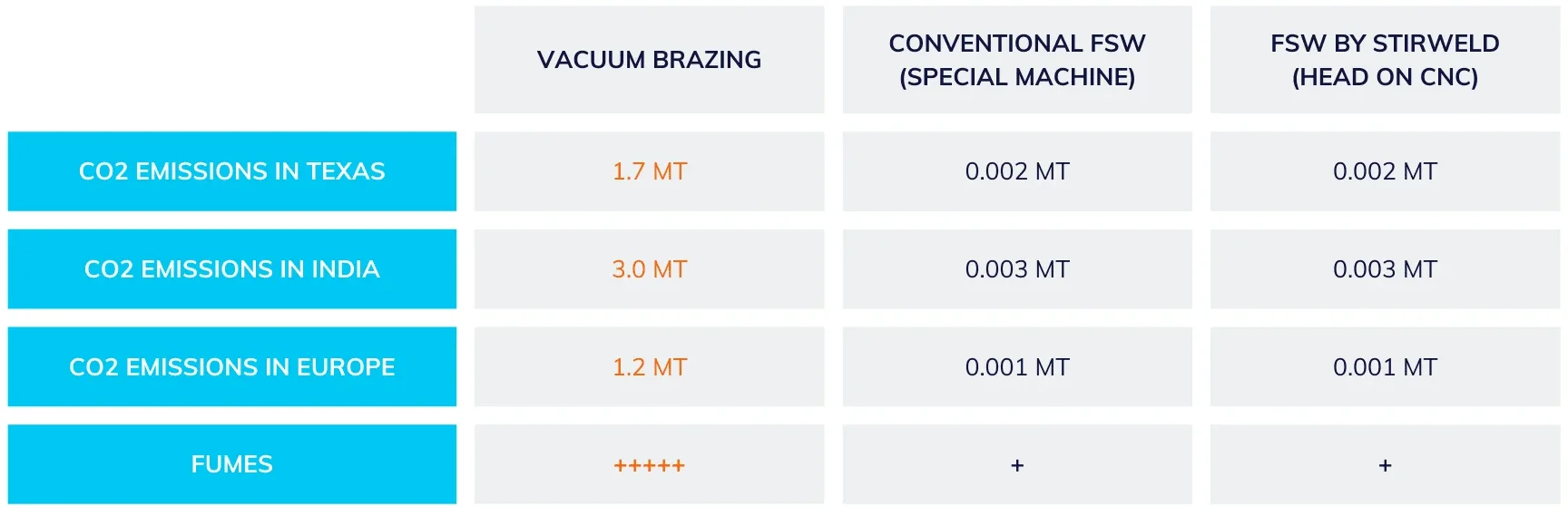
FSW reduces carbon footprint by 1,000x compared to vacuum brazing. Stirweld solution generates less CO2 emissions and emits no fume or toxic gas than traditional welding methods, contributing to a more environmentally friendly welding process.
While each welding and brazing technique presents its own set of advantages and applications, the operational costs associated with these methods can significantly influence their suitability and efficiency in industrial applications. Friction Stir Welding (FSW) emerges as a particularly cost-effective option due to its minimal consumable use and low energy requirements. In contrast, techniques like TIG, MIG, and Electron Bean Welding, although widely used, tend to incur higher operational costs due to their need for expensive consumables, high energy consumption, and intensive maintenance. Vacuum brazing also shows a high-cost factor, especially in terms of energy use and part preparation. Ultimately, the choice of welding or brazing technology should be guided by a comprehensive understanding of both the technical requirements and the cost implications, ensuring that the selected method aligns with the overall goals of quality, efficiency, and cost-effectiveness in manufacturing processes.
Welding process cost comparison
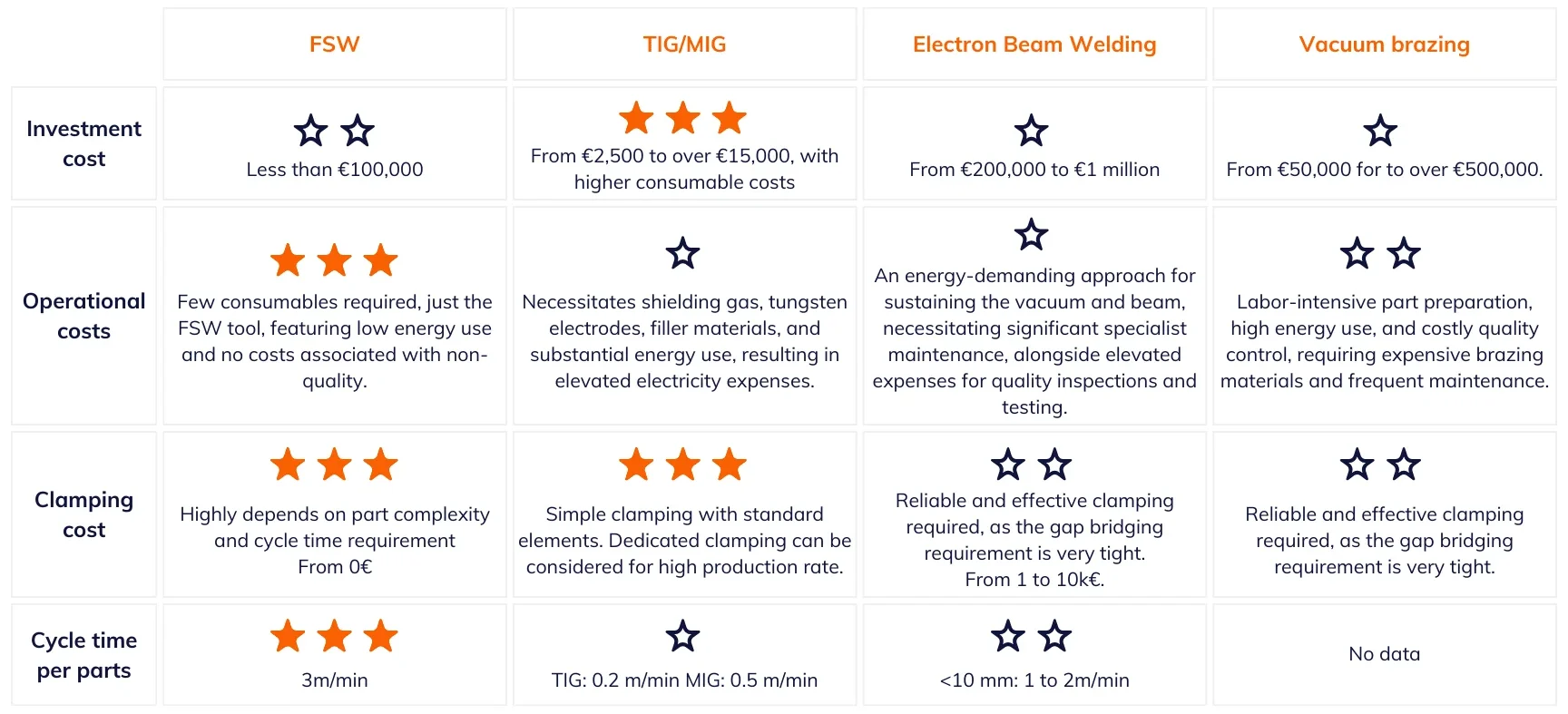
Gain Deeper Insights into Friction Stir Welding Costs
Interested in a deeper dive into the costs associated with Friction Stir Welding compared to other welding techniques? Watch our comprehensive webinar titled “How much will it cost you to weld your part by FSW? Comparing to other welding techniques” for expert insights and detailed cost analysis.