Which materials are weldable by Friction Stir Welding?
Friction Stir Welding represents a revolutionary advancement in the field of metal joining techniques. This innovative process, developed in 1995 by The Welding Institute (TWI) in the United Kingdom, is distinguised by its ability to weld materials that are difficult to assemble using traditional methods while offering exceptional mechanical performance. FSW is now prevalent in various sectors such as aerospace, automotive, rail and electronics, thanks to its numerous advantages. It is particularly favored for joining metals like aluminium, copper and magnesium, as well as for dissimilar assemblies, paving the way for innovative and versatile applications.
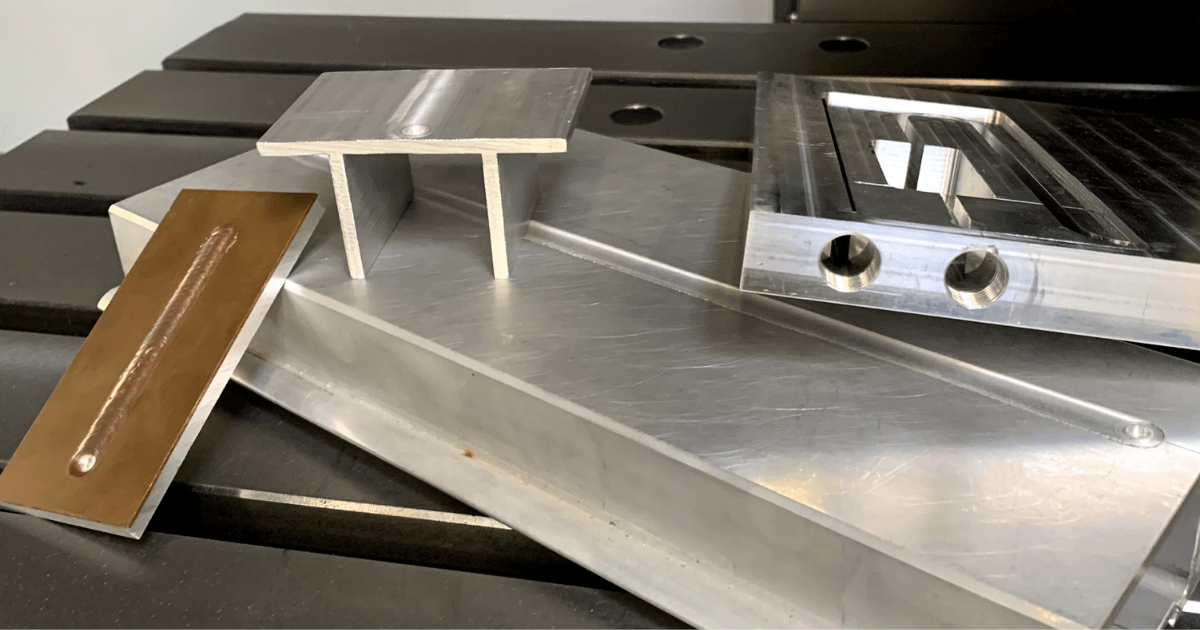
Weldable materials by Friction Stir Welding: applications and advantages
Aluminium is widely used in many industries due to its light weight, corrosion resistance, and good mechanical, thermal and electrical properties. However, its weldability can be complicated by oxide formation and high thermal conductivity.
Why use FSW for aluminium?
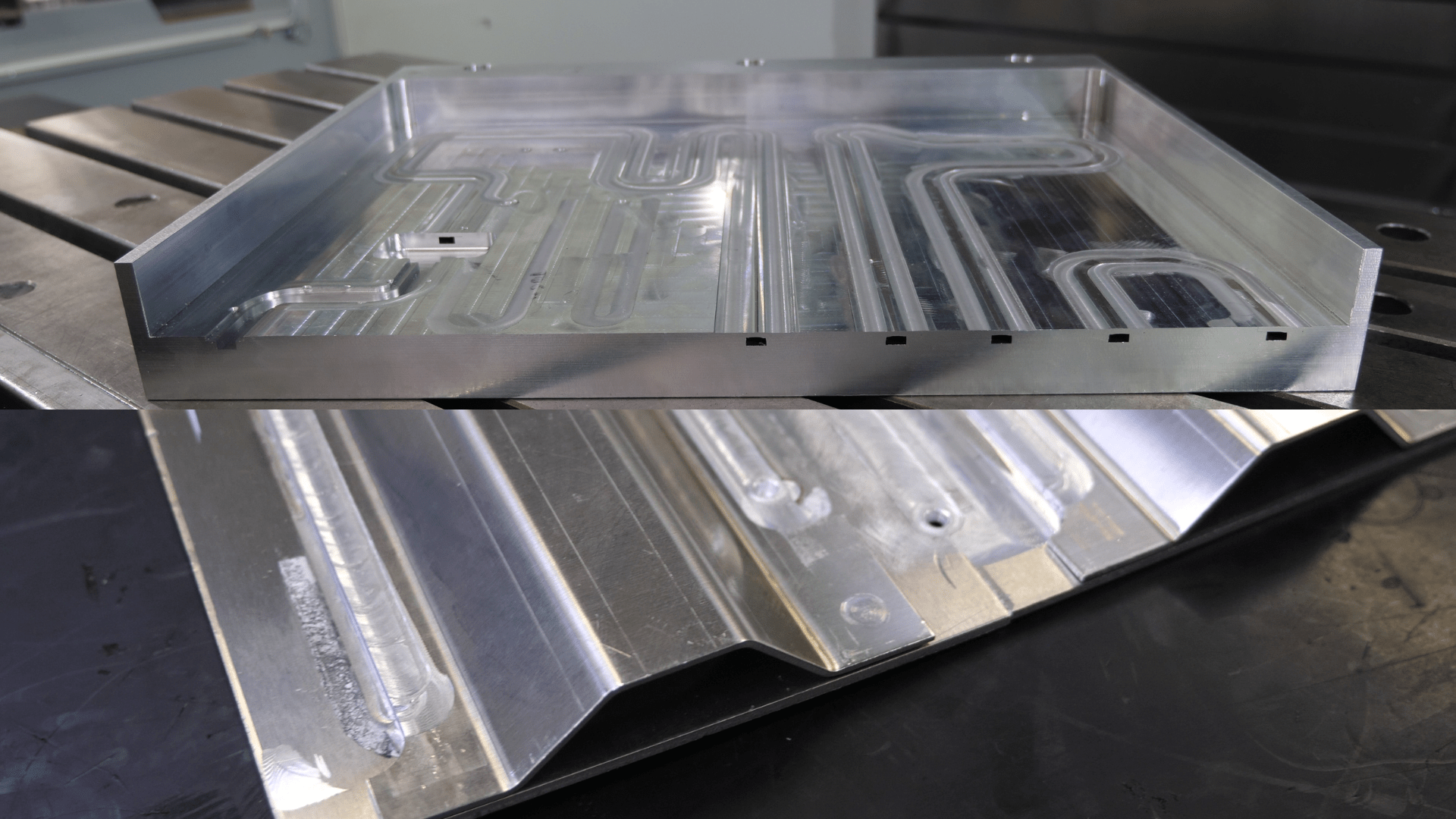
FSW is particularly suitable for aluminium as it reduces the risks of porosity and cracking associated with fusion welding methods. The FSW process produces homogeneous joints with high structural integrity, while minimizing distorsions and residual stresses. Consequently, FSW enables the welding of aluminium alloys that are traditionally considered non-weldable, such as high-strenght aluminium alloys (2000, 7000 series).
Applications in automotive, aerospace and beyond
In the automotive field, FSW is used to assemble lightweight aluminium structures such as car bodies, chassis and battery trays. In aerospace, it welds fuselage panels and structural elements, contribution to weight reduction and improved energy performance of aircraft. Additionally, FSW is employed in boat construction (floors, cold plates) and trains (sides, floors, cold plates) where light weight and corrosion resistance are essential criteria.
Comparison with traditional techniques
Traditional welding techniques for aluminium, such as MIG and TIG welding, face challenges like oxide formation and hot cracking. FSW avoids these issues by keeping materials below their melting point, ensuring more reliable and durable welds without the common defects of fusion methods.
Copper is valued for its excellent electrical and thermal conductivity, as well as its corrosion resistance. However, traditional copper welding poses challenges due to its high thermal conductivity, which requires significant energy input to reacj melting temperatures.
Advantages of FSW for copper
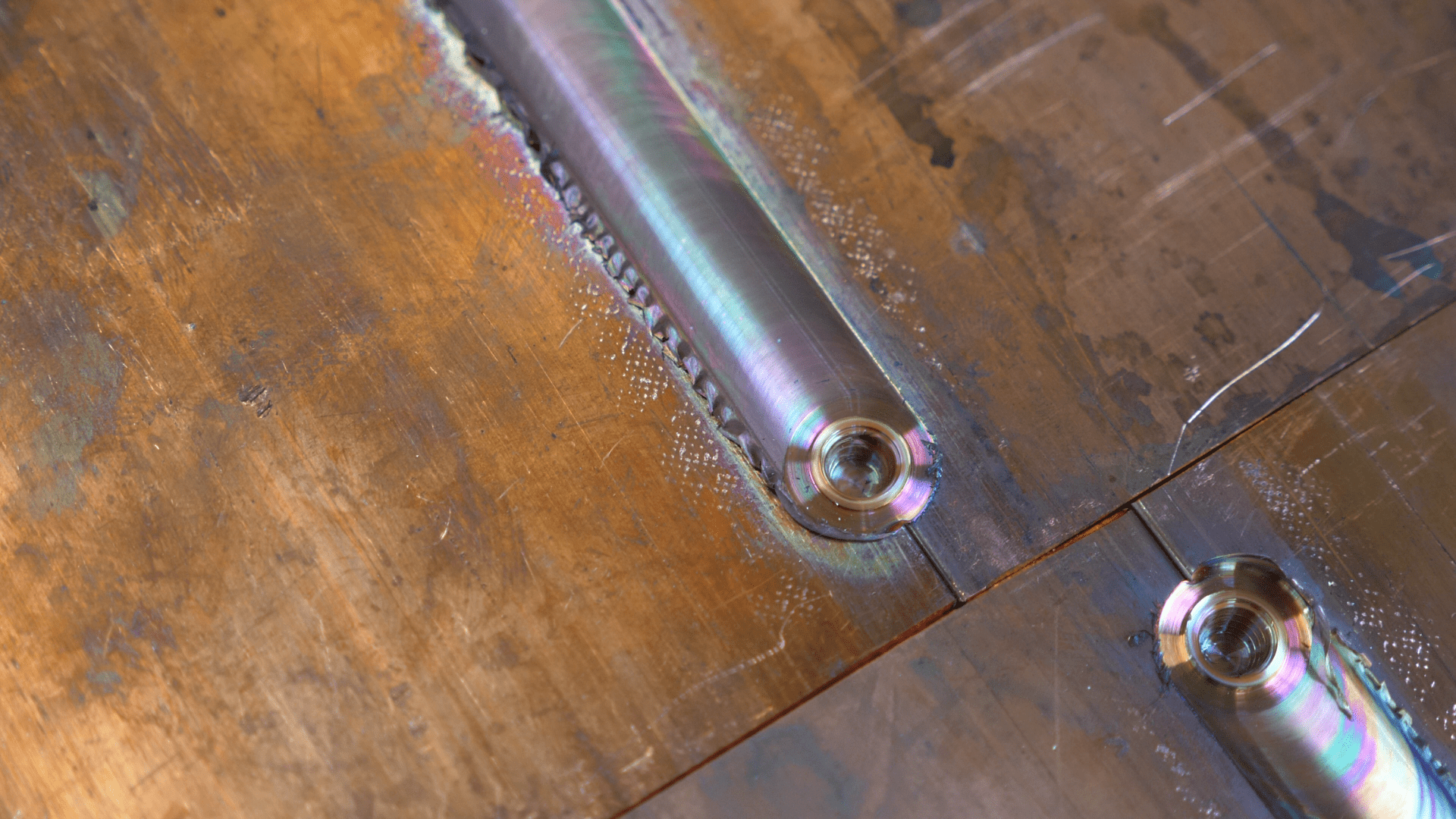
Friction Stir Welding offers an efficient solution for joining copper without reaching melting temperatures, thus avoiding thermal distorsions and common metallurgical defects found in traditional processes. Additionally, FSW allows for high-quality welds with excellent mechanical properties, comparable or superior to the bas metal.
Specific applications in electronics and electrical conductors
The applications of FSW of copper are numerous and varied. In electronics, it is used to manufacture electrical components, radiators, and heat exchangers. FSW also creates robust and reliable electrical connections essential for energy infrastructures and electrical distribution systems such as bus bars.
Comparison with traditional techniques
Traditional copper welding techniques, such as arc welding and brazing, involve high temperatures that can cause distorsions and quality issues in welds. FSW, on the other hand, operates at temperatures below the melting point, minimizing deformation risks and producing homogeneous and strong joints.
Magnesium is known for its light weight and good mechanical properties but welding it can be complex due to its reactivity and relatively low melting point.
Advantages of FSW for magnesium
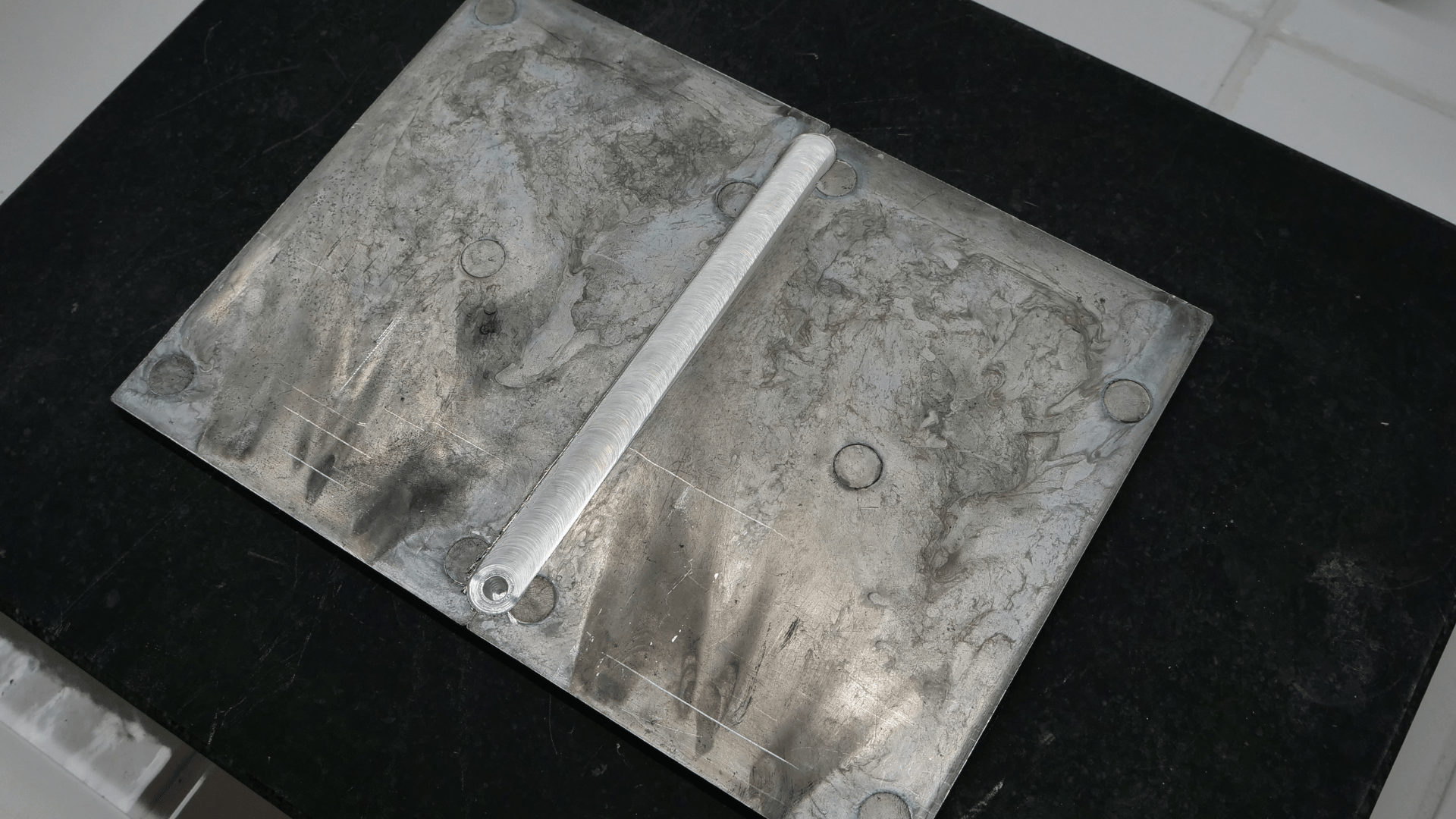
Friction Stir Welding is particularly effective for magnesium as it allows welding without melting the metal, this reducing the risks for cracks and imperfections. The process produces welds with excellent mechanical properties and good structural integrity.
Applications in aerospace, automotive and electronics
Magnesium welded by FSW is used in applications where light weight is crucial, such as in aerospace for structural components and cockpit elements. In the automotive industry, it is used to manufacture lightweight parts like engine mounts and chassis elements, contributing to improved vehicle energy efficiency. Magnesium is also used in portable equipment and electronic products, where reduced weight is a significant advantage.
Comparison with traditional techniques
Traditional welding techniques for magnesium, such as TIG welding and arc welding, can lead to issues like cracking and porosity. FSW minimizes theses risks by operating below the melting point, ensuring stronger joints with fewer defects.
Dissimilar assembly: the innovative solution of Friction Stir Welding
Challenges and opportunities of dissimilar assembly
Assembling dissimilar metals presents unique challenges due to differences in physical and chemical properties, such as thermal expansion coefficients, melting points, and the formation of brittle intermetallic phases. These differences can lead to internal stresses, cracks, and accelerated joint degradation.
Friction Stir Welding stands out as a cutting-edge solution to overcome these challenges. By using a solid-state welding process, FSW minimizes melting and solidification issues, creating strong and durable joints between dissimilar metals.
Techniques and advantages of FSW for dissimilar assemblies
FSW used a rotating tool to generate frictional heat, welding metals without melting them. This technique effectively mixes the materials, creating homogeneous welds with superior mechanical properties and without defects. Employing this technique offers numerous benefits for your production.
Applications and examples of dissimilar assemblies
FSW opens news possibilites for dissimilar assemblies, enabling combinations of materials that were once difficult to weld. Here are some concrete examples of applications.
Aluminium – copper: ideal for heat exchangers or bus bar

Assembling aluminium and copper presents specific challenges due to their distinct chemical and physical properties. FSW overcomes these challenges by creating strong and durable joints.
Using FSW to weld aluminium and copper improves thermal conductivity. Indeed, FSW creates a metallurgical continuity between the two materials. The ability of FSW to produce high-quality welds between aluminium and copper is particularly beneficial for industries requiring efficient thermal management, such as electronics (bus bars) or energy infrastructures (heat exchangers).

Aluminium – Steel: perfect for automotive applications
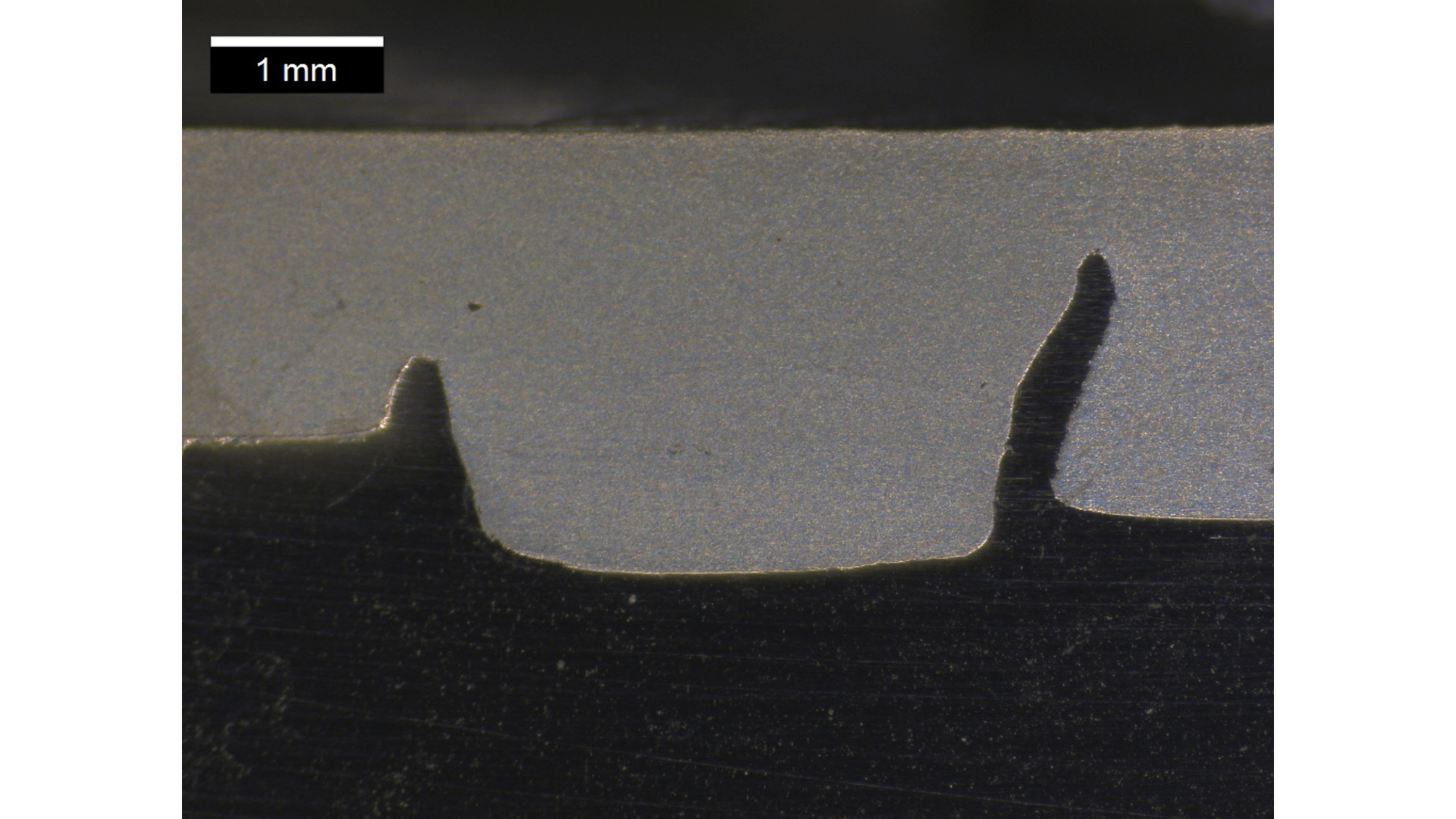
Assembling aluminium and steel combines the light weight of aluminium with the robustness of steel. However, differences in melting points and metallurgical behavior make this combination difficult with traditional welding methods.
FSW creates strong joints without melting, reducing cracking and porosity issues through robust welds that perfectly suit automotive structures. In the automotive industry, using FSW to assemble aluminium and steel contributes to vehicle weight reduction improving energy efficiency and performance. FSW can be used to assemble car bodies, chassis, and safety components.

Friction Stir Welding proves to be a revolutionary technology for metal assembly, offering significant advantages over traditional methods. By enabling the welding of materials without reaching their melting point, FSW minimizes thermal distorsions and metallurgical defects, producing high-quality joints with superior mechanical properties.
Thus, Friction Stir Welding positions itself as a key technology for the future of metal assembly, offering effective and innovative solutions to meet the growing demands of modern industries. Whether for welding homogeneous of dissimilar metals, FSW promises to transform manufacturing processes and contribute significant advancements in various fields.
Interested
in trying FSW?
Download our white paper “FSW for dummies” now to kickstart your learning of friction stir welding (FSW).