Why Friction Stir Welding of Aluminum is the Future of Industrial Manufacturing?
In the world of modern manufacturing, the welding of aluminum represents a constant challenge due to the specific nature of this light but robust material. Traditionally, conventional welding methods can lead to defects, low strength, and high costs in terms of time and resources. However, an innovative technology is emerging as a revolutionary solution: friction stir welding (FSW). This method, which involves using the heat generated by friction to create welds without melting the material, offers a multitude of advantages that are transforming the industry.
Friction stir welding of aluminum stands out not only for its ability to produce high-quality welds with fewer defects but also for its energy efficiency and compatibility with various industrial applications.
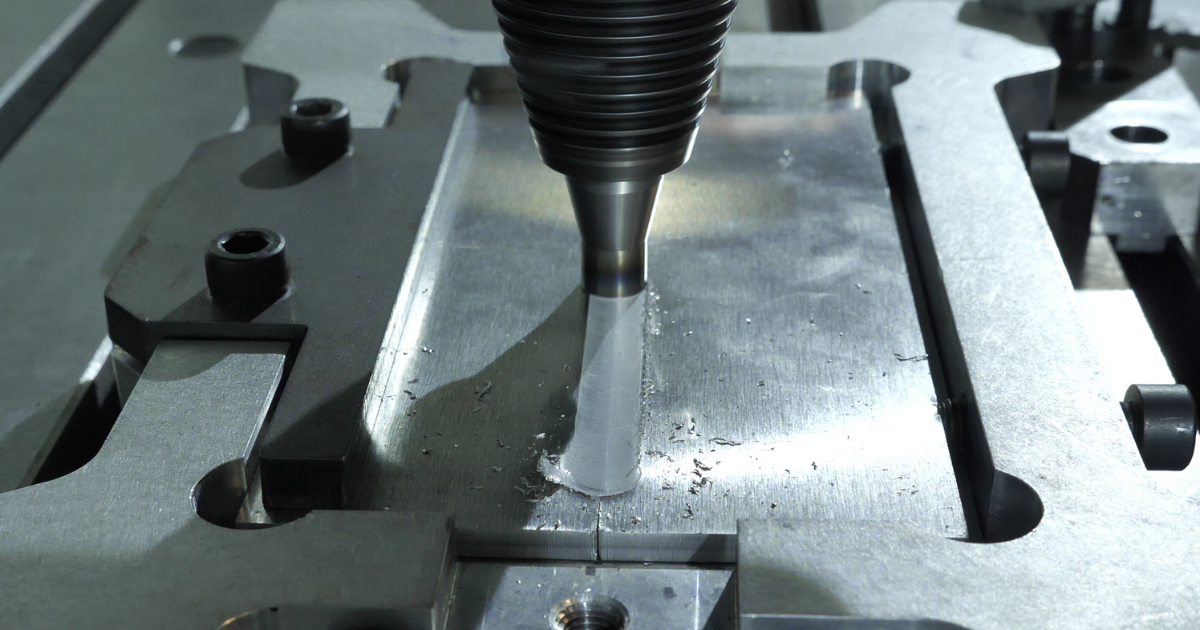
Aluminum Welding: The Basics of FSW
What is Friction Stir Welding?
Friction Stir Welding, also known as FSW, is an innovative welding technique developed in 1995 in the United Kingdom by TWI. Unlike conventional welding methods, which involve melting the materials at high temperatures, FSW uses friction generated by a rotating tool to soften and stir the metals without melting them. The tool, consisting of a shoulder and a pin, rotates at moderate speeds (from 600 to 4000 RPM) while moving along the weld seam (from 0.4 to 4 m/min depending on the welding configurations). The heat produced by the friction makes the material around the tool malleable, allowing for the creation of a solid and homogeneous weld when the metal cools and solidifies.
Why Choose FSW for the Welding of Aluminum?
Aluminum is widely used in many industries due to its light weight, corrosion resistance, and electrical and thermal conductivity. However, it presents particular challenges for welding, including high thermal conductivity that makes heat control difficult, and a tendency to crack and become porous when welded using traditional methods.
FSW offers several distinct advantages for the welding of aluminum:
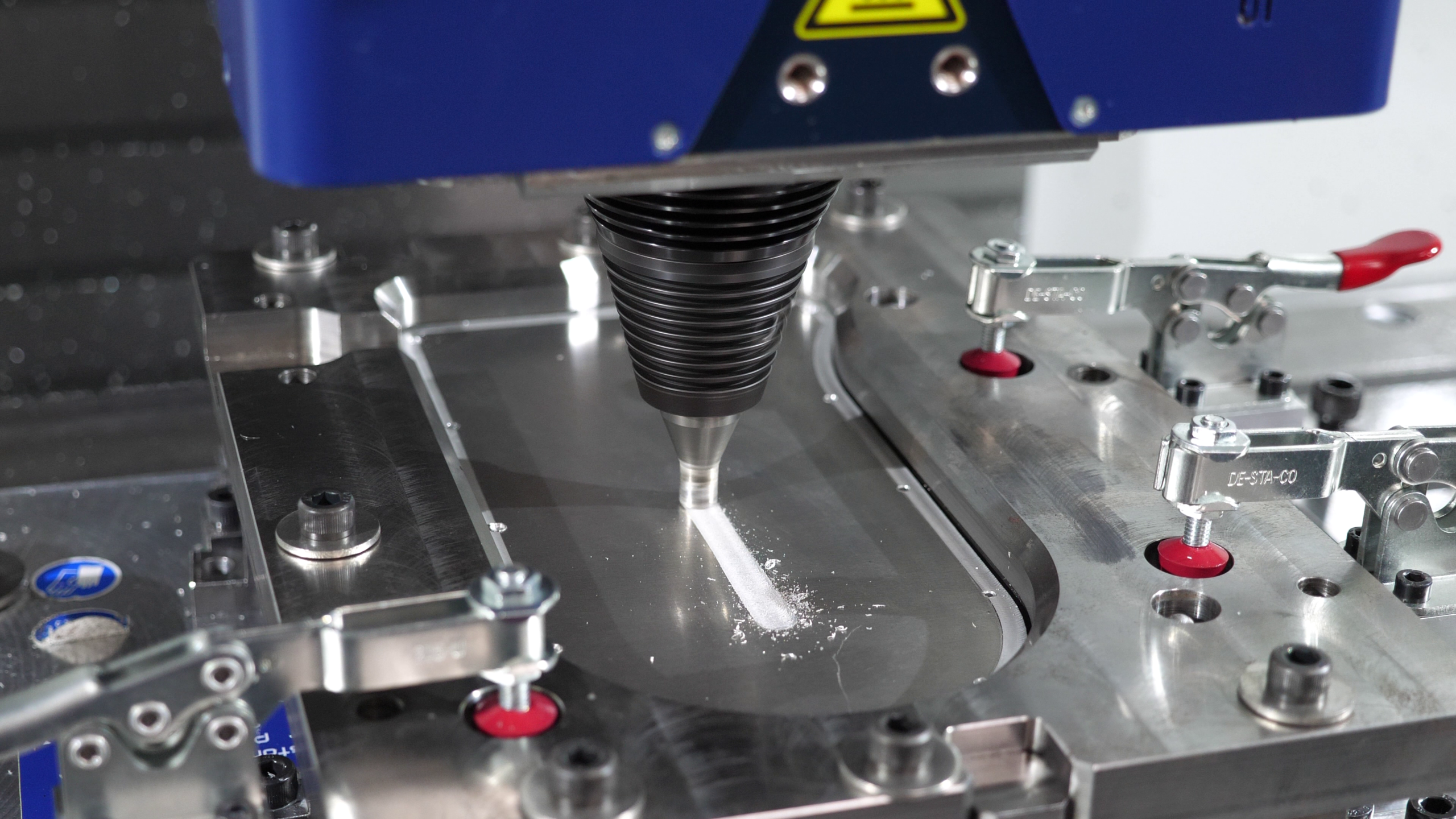
Comparison between FSW and Traditional Aluminium Welding Methods
FSW offers several advantages over traditional aluminum welding methods, such as arc welding (TIG/MIG) and resistance welding. Unlike these methods, FSW does not involve melting the materials, which greatly reduces the risks of defects like porosity and cracks, as well as deformations due to high temperatures. Read our article on comparing FSW to conventional welding techniques now to learn more.
The Challenges of the Welding of Aluminum and How FSW Overcomes Them
Common Problems in Aluminum Welding
The welding of aluminum presents several unique challenges that complicate the achievement of high-quality welds. Here are some of the main problems encountered with traditional welding methods:
Porosity: Aluminum has a strong affinity for hydrogen, which can be absorbed during welding. When cooling, the hydrogen escapes, creating pores and bubbles in the weld, affecting its strength and integrity.
Hot Cracking: Hot cracking occurs when the metal solidifies after melting, creating internal stresses that lead to cracks. High-performance aluminum alloys (2000, 6000, and 7000 series) are particularly prone to this defect due to their wide solidification range.
Rapid Oxidation: Aluminum reacts quickly with oxygen in the air to form a very stable and hard-to-remove aluminum oxide layer (Al2O3). This layer must be removed before welding, otherwise it can lead to poor fusion and brittle welds.
High Thermal Conductivity: Aluminum conducts heat very efficiently, meaning a lot of heat is dissipated quickly from the weld area. This makes temperature control and heat management more difficult, potentially leading to incomplete fusion or distortions.
High Coefficient of Thermal Expansion: Aluminum has a high coefficient of thermal expansion, meaning it expands and contracts more than most other metals during welding. This can cause deformations and residual stresses, affecting the precision and quality of the weld.
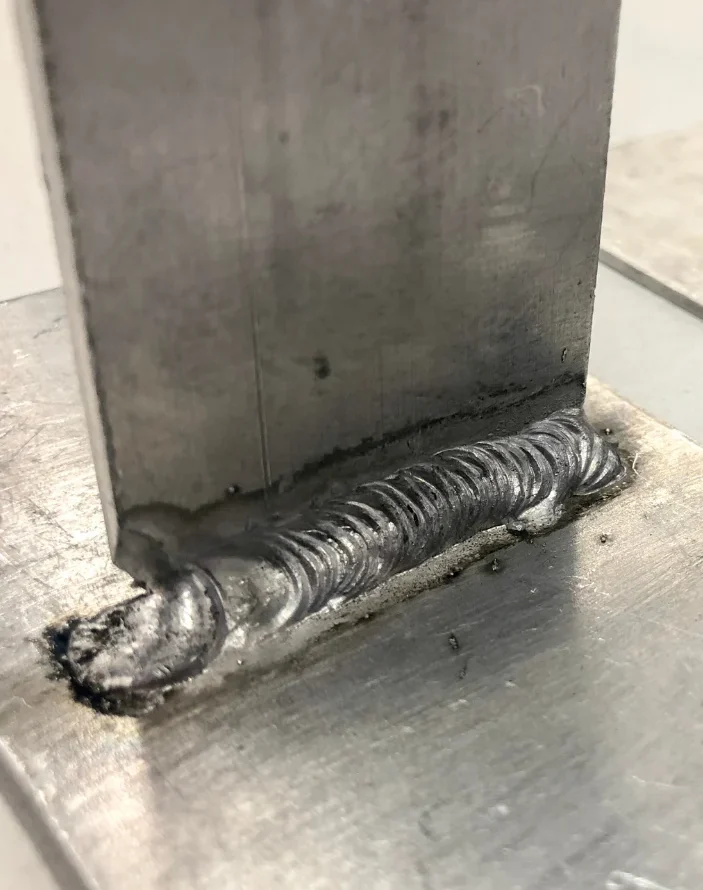
How FSW Solves These Inherent Aluminum Welding Problems
Friction stir welding overcomes these challenges effectively through its unique solid-state welding approach, where the material never reaches its melting point. Here’s how FSW addresses common aluminum welding issues:
Absence of Porosity: FSW uses friction to heat and soften the material without melting it, eliminating the liquid phase where gas absorption could occur. This removes the risk of porosity in the weld.
Elimination of Hot Cracking: Since FSW operates at temperatures well below the melting point of aluminum, the risk of hot cracking is nonexistent. The plasticity of the material during FSW allows for a homogeneous, crack-free weld.
Oxidation Management: As FSW does not require melting, there is no formation of a high-temperature oxide layer that could compromise the weld. The rotating tool mechanically cleans the surfaces to be welded, improving weld quality.
Improved Thermal Control: Heat dissipation by conduction is better controlled in FSW, as the welding temperature is lower and more stable. It is also possible to control the temperature during the welding operation. This reduces distortions and allows for better control over the heat-affected zone.
Reduction of Deformations: Due to a lower welding temperature and better management of thermal stresses, FSW minimizes distortions and residual stresses. The high coefficient of thermal expansion of aluminum is less problematic, leading to more precise welds.

Practical Guide: 5 Essential Steps to Successful Friction Stir Welding
Integrating friction stir welding into your production line requires careful planning and a thorough understanding of the technology.
Here are the key steps to successfully transition:
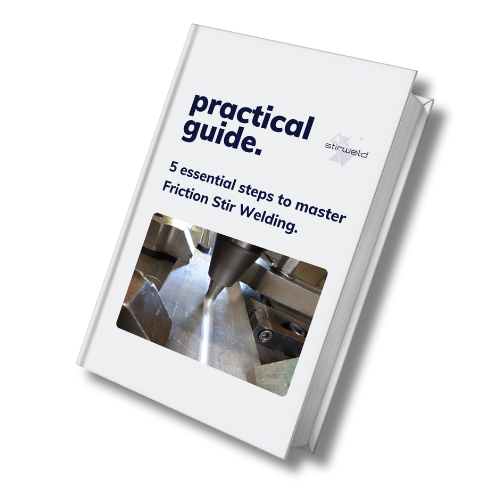
Want to know more?
Are you ready to revolutionize your manufacturing processes with friction stir welding? Don’t miss our comprehensive guide to learn all about this innovative technology. Discover how FSW can transform your weld quality, reduce costs, and increase operational efficiency.